Introduction: Hardening a Door Frame
About a month ago, I was talking with a friend of mine who's a police officer. We were talking about a number of things in regards to home security, and he mentioned that in most burglaries, the thief just kicks in the door - no problem - because door frames tend to be pretty wimpy. He also mentioned that door frames that were reinforced with a strip of metal were immensely harder to kick in ... and I immediately starting thinking about making my own.
Most residential doors are pretty "soft" - i.e. easy to get through. There are a number of videos on YouTube where you can see someone almost casually kick in a door - and when you understand the actual support structure around most locks and deadbolts, it's pretty obvious why this is the case. While you might have an awesome deadbolt that resists picking and lock-bumping, the only thing REALLY keeping your door closed is a relatively thin strip of wood (probably pine) and maybe some trim - i.e. the relatively thin door jamb.
This instructable covers one possible technique for making a door frame nearly impervious to being kicked in. I want to admit right off the bat that this design is overkill - lol. I have a tendency to over-engineer things and this project was no exception. If I were to do it again, I'd be looking at using 16GA or thinner metal (1/16") as opposed to the 10GA (1/8") metal I used - it would be easier to work with and still very strong.
I also want to mention that there are commercial products out there that do the same thing - but why BUY what you can MAKE when you can make it better? :) I was also able to make the door reinforcement for about half what a much thinner commercial product would have cost (not including time, of course) - total cost was around $22.
What you'll need:
Supplies:
Metal strip - I used a 2" x 48" strip of 10GA 304 stainless steel. I'd recommend 16 GA (which should be even cheaper)
Heavy-duty screws - 4" long (I used hardened decking screws with Torx heads)
Tools:
Assorted metal files, hammer, cold-chisel, drill, bits, countersink, sander, sanding belts or sandpaper, measuring tape and/or rule, center punch, scribe, welder, metal saw (reciprocating, abrasive, whatever works) and it would be nice to have Dykem and/or permanent markers.
Step 1: Dimensions and Layout
The first thing to do is check how much of a gap you have on the "knob-side" of the door. If you've got the room, you might be able to install the strip on top of the wood, but if the gap is a little tighter (around 1/8") you're probably going to have to inlet the surface of the jamb. I had plenty of room, so I opted to go with a surface-mounted installation.
Next, check how wide of a strip you need. I used a 2" wide strip, but you'll want to make sure that you won't have too much overhang if you go with that dimension. The 2" wide strip was *just* about the right size - I could mash it back against the weatherstrip and get the front edge just flush with the face of the door frame. The commercial units run around 1 1/2", which doesn't seem wide enough to me (another reason to build your own)
Once you have your material, it's time to transfer the locations of your lock and deadbolt catches. Since these catches are usually kind of "tuned" during install, and mine were set up pretty much exactly where I'd want them, I decided that the best technique to get the dimensions would be to scrub-trace them, and save myself a lot of hassle trying to measure it all out. If you use this technique, be *sure* to get the edge of the door frame as a reference since it's the distance between the front of the frame and the front edge of the catch-plate that determine how tightly your door closes (or doesn't close).
Step 2: Fabrication
The first thing I did was to bend the end of the strip over to 90 degrees with a roughly 1/2" radius. It did surprise me that this required a torch - which is one more reason I'd suggest going with thinner material. I fabricated the two "catch ramps" by cutting just where the arc started, at the middle of the arc, and just where it ended - giving me two pieces to weld on. These cuts were made with a hacksaw ... and a good amount of effort - lol.
Next on the agenda were the holes. These were cut in the time-tested tradition of drilling a bunch of holes and beating the center out. Hey, it works :) A little time spent with a file cleaned the holes up nicely. The process took maybe 20 minutes.
At this point, the catch ramps were tacked in place, adjusted to make sure they were aligned, and welded on. After the piece cooled (I didn't quench the metal because I didn't want to take a chance at hardening it) I used a file and an angle grinder to smooth down the welds and give some shape to the edges of the catch ramps. Once everything was smooth, I sanded the surface with an orbital sander to unify the surface texture and smooth out any dips. I marked two lines down the strip - the first 1/2" from the back edge, the second 1-1/8" from the back edge. I then marked the position of screw holes about every 6" on alternating lines along the length of the strip. The holes need to be alternating so that you avoid creating a stress line (that might cause a split) in the wood you'll be anchoring to.
Drilling holes and countersinking the holes is self-explanatory - but a good tip is to use cutting oil when doing so. Steel is SO much easier to drill and work with cutting oil - your bits will cut faster, cleaner, cooler and stay sharp longer. I usually have a little plastic scoop where I put about half a teaspoon of oil and dip the drill bit two or three times during the drilling/countersinking process. This seems a lot cleaner and less wasteful than dribbling oil on the surface and having 90% of it end up in the wrong place.
Final finish was done with a belt sander with a 180-grit belt. I found that moving quickly from one end to the other worked the best as slower movement gave an uneven finish. When I say moving quickly, I was probably covering the whole length of the strip in 4 or 5 seconds.
Step 3: Installation and Additional Suggestions
Installation was surprisingly quick - but then I wasn't insetting the plate so that helped. First, leaving the original catch plates in place, I positioned the new strip to make sure the front edges of the holes aligned with the edges of the original catch plates. Once in position, I sunk a temporary screw to hold it in position, and closed the door to make sure that everything lined up and operated smoothly. Once operation was confirmed, I removed the original catch plates and re-installed the strip. I worked from the center of the strip out to the ends. I used a Vix bit to make sure I was drilling the center of the hole, and followed up with a 3" deep pilot hole. You want to drill pilot holes even with "self-tapping" screws to avoid creating any kind of splitting stress in the wood you're anchoring to. I also drilled the holes just slightly canted toward the center of the frame just to make sure that the screws were going into the "meat" of the frame member. It's not necessary to crank down on these screws - just get them to go flush with the plate and you're done - any more than that and you can bow the door jamb.
Other thoughts:
So now that you've fixed the first glaring weakness of your door, it's time to look at the next weak link in the chain which is going to be the hinge-side of the door. Fortunately, the hinge-side is pretty easy to reinforce. All you need to do is take one screw out of each leaf of the hinges - both on the frame side and door side and replace the relatively short screws with something beefier and longer - 4" screws are great for the frame-side, and 2" for the door-side. You only need to replace one screw per leaf - any more than that is really overkill and you're increasing the risk of splitting the door (and remember: drill pilot holes!)
If you have a wooden door, you might also want to consider installing a deadbolt shroud. This will keep your door from splitting open around the lock when subjected to ... uh.... "unnatural" forces.
Thanks for reading :) ... and if you think it fits the description, vote for this instructable in the INDESTRUCTIBLES contest :)
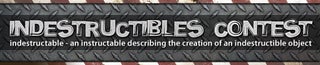
Participated in the
Indestructibles Contest