Introduction: Homemade Electric Kiln
I was frustrated with the price of electric burnout kilns for ceramics, metal annealing, glass enameling, and melting precious metals etc,. so I decided to build my own. Most kilns that run at these temperatures cost between $600 and $1200. With a little help from a guy at a ceramics store, I built one for about $120 (not including the power controller and pyrometer). This little electric kiln can get up to 2000 degrees F and is easy to make without any special tools besides a handheld router. I also wanted one that I could take apart and replace the element, since these are inexpensive.
Materials:
1. 8 x 10" bolts with nuts- 1/4" diameter
2. 7 x soft insulating fire bricks (4 1/2" x 9" x 2 1/2"- make sure they are soft)
3. About 7 feet of angle iron from Home Depot (this is the frame) (4 x 14" legs/corners, 2 x 9" floor supports)
4. One sheet of thin aluminum (for the door). At least a 9" by 9" square
5. One 3/8 inch x 18” coiled heating element (stretched to about 28") out of 16 gauge Kanthal wire. I had this wound for me at the local ceramics store. I recommend you wind your own or as a ceramic supplier in your area to wind one for you. In my other instructable, Electric Kiln -Top Loader, I give directions on how to wind your own.
6. One small hinge with screws
7. Fire proof pins (should come with element) or you can make these out of the Kanthal wire.
8. Short outdoor extension cord rated to at least 10 amps (cut down to about 6 feet)
9. Stand alone ICS kiln controller. Sundanceglass.com has one for $84.
10. 1" thick Kaowool- about 1 foot square
Tools:
1. Hand held router with 3/8 inch bit
2. Wrench
3. Needlenose pliers
4. Hacksaw
5. Wire cutters/stripper
6. Drill
7. Tin snips
Step 1: Cutting the Channels
1. Pencil the channels in as a u-shape 3/8 inch wide. I left about an inch, to an inch and a half from the edge and the top of the "U" so the elements are not too close to the opening of the kiln.
2. Route out the channels with your router using a 3/8 inch bit.
3. You will need to cut one of your fire bricks down to a square 4 1/2" by 4 1/2" for the back and route out two straight channels. This will be the back wall.
Step 2: Putting in the Element
1. You'll need two bricks for the floor, as pictured.
2. The dimensions of the fire bricks are 4 1/2" x 9" x 2 1/2" - when you construct the firebrick box, the kiln will be too wide across (2 outside walls at 2 1/2" and your back wall is 4 1/2", for a total of 9 1/2"). To make the walls flush with the roof and floor (9") you will need to take out a 1/2". In the first pic you can see I shaved off a1/2" from the right side. Any saw can cut these bricks, they are very soft.
3. The element I started with was 18” inches long. Separate the coils of the element so that they aren't touching. If you are unsure of how to do this, then you can always ask the people at the ceramic store. This stretched my element out to 28 inches not including the pigtails. My element cost me about $25. If you make your own don’t forget to make 5 or 6 inch pigtails to stick through the back holes for your power hookup!
4. You'll need to drill two holes out the back of the kiln so you can run the ends of the element out the back. These are drilled inside the top channel about 1" apart. Pick a drill bit slightly bigger than your element wire.
5. Thread the element into the channels as shown.
6. If the ceramics store gives you pins, I found it was better to use pliers and make little u-shaped pins out of them. You can push these into the fire brick about an inch apart to keep the elements in the channels. It doesn't seem important now, but when you start firing, the element will want to flex and move around. The pins will keep it fixed in the channels.
**update - There have been many questions about the element I used and where I purchased it. I had hoped people would ask questions from their local ceramics store and get answers there. That is where I had my element wound for me. I have learned a few things since then. The element is a type of NiCr wire called Kanthal. Most Kanthal is rated to about 2450 F. There are other element types if you need higher temperatures. Kanthal is used in low-fire/ceramic applications. Either find a ceramic supplier to help (as I did) or you can contact a place like Joppaglass.com and have an element made to your specifications. They will usually want to know the voltage of the power source, max amperage (my garage is 10 amp breaker) and the gauge of wire (I think mine is 16 gauge). The arbor (inside and outside diameter of the element) can be requested and you can get the element you want. I have started to wind my own and you can find those instructions in my instructable about my top loader kiln.
Step 3: Making the Frame.
1. The frame I designed, squeezes it all together. Cut four 14" lengths of the angle iron with your hacksaw for the corners.
2. Cut two 9" lengths for the bottom. These two pieces hold the floor and rest on two 10" bolts on the bottom.
3. Thread the bolts as shown--4 on top,4 on the bottom. Two of the bottom bolts hold up the floor, the rest just squeeze the whole project together to hold the bricks in place.
4. Remember to place two bricks on top for your roof. Also, you can see that I have the whole project off the floor by about 3 inches.
*Safety tip--never use this or any other kiln on a surface that isn't fireproof. I always have this on my concrete floor in the garage.
Step 4: Making the Door
1. With your tin snips, cut your aluminum sheet into the shape shown in the picture. You can use steel plate if you want. I believe mine was 22 or 24 gauge. It won’t get too hot to melt because you will insert insulating Kaowool inside! The dimensions I used make a 6 inch door. The central square is 6" and the tabs are 1 1/2". (So start with square 9" by 9" and cut out the corners)
2. I used a sophisticated metal break to bend the metal (called my fingers and a scrap of wood). Bend the tabs up so you have 1/2" on the inside and the door itself is 1" thick.
3. Cut a 6" x 6" square of the 1" thick Kaowool and squeeze inside the metal as shown.
4. Attach the door with a small hinge. I pre-drilled some holes in the frame and used metal screws to screw it to the frame. I didn't put a latch on this. As an option you could by-pass this step and use another fire brick over the entrance.
Step 5: Connecting the Power
1. Cut an outdoor electrical cord(10 amp) down to 6 feet and keep the plug end. You don't want it too long.
2. Strip the wires and connect to the element wires coming out the back of the kiln. My element came with metal connectors and ceramic sleeves. The sleeves are optional. I have since used small bolts to attach the power. This separates the terminal wires from the copper wires of your power cord and the nuts and bolts act as a heat sink to keep your wires from getting too hot
3. You need to ground this by attaching the green wire to the frame. I just found a small metal screw and attached it to the frame.
4.
**update 1/5/2017: A lot of people have asked me about my green controller. This was from an old Nova kiln and has no numbers or markings on it. I have done some research on the type of controller you will want. They are called stand alone ICS kiln controllers. I have found one at Sundanceglass.com (pic 2 and 3) and have ordered one for myself as a backup for my controller. This is an infinity switch which will turn the power off and on depending on the setting you use and will allow you to obtain an even temperature. Use a thermocouple and pyrometer to monitor your heat and then you will know what setting works for the temperature you are trying to reach. There are some people in the comments that have used PID controllers and they have Instructables on how to wire them up to your kiln. I think cost wise, it is about the same to order an ICS controller or a PID controller.
**Safety tip--Do Not plug this directly to a wall outlet. Also, do not touch the element wires when the kiln is on.
5. I ran a piece of flat iron across the back wall of the kiln so that the back wall has more stability. This is not essential. When I first made my kiln, the squeeze of the frame held the back wall in fine.
Step 6: Finished Kiln!
1. In the original incarnation of my kiln (1st pic) I drilled a hole in the top and mounted an old thermocouple/pyrometer on top of the kiln.
2. I have recently upgraded to a better thermocouple (Pic 2) and directly connected this to the analog temp. gauge on my controller. I was lucky and had one of these from an old kiln I broke. For accurate firing temperatures I recommend a K Type thermocouple with a digital pyrometer. Another option for ceramics or glass enameling would be to drill a viewing hole in the side and then buy a ceramic plug for it.
3. I have run this for many hours at various temperatures (3rd pic). I really have not experienced any problems except my element still wants to pop out of those channels. I"ll just have to keep an eye on them.
Please let me know what you think or questions you have.
**update Dec. 11 2014- I have run this kiln now for hundreds of hours (firing clay, PMC clay etc.) and found the max temperature to be 2300 F.
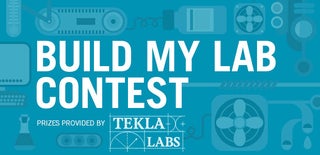
Fourth Prize in the
Build My Lab Contest
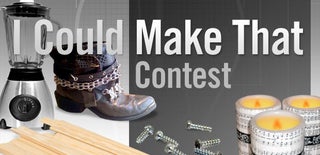
Runner Up in the
I Could Make That Contest