Introduction: How to Make the Mini Metal Foundry
How to make a simple backyard foundry for less than $20, for melting pop cans, and casting aluminum.
Step 1: Watch the Video
WARNING: Charcoal foundries can reach temperatures in excess of 1,000ºC, which is well above the melting point of hobbyists. This project should only be attempted with adequate knowledge and training, proper protective safety gear, and in a fire resistant area with adequate ventilation. The sparks flying from the foundry can ignite fires, and the fumes from burning dross can be toxic. Use caution and common sense. Use of this video content is at your own risk.
Step 2: The Mini Metal Foundry
In this project you’ll see how to use equal parts of sand and plaster, to make a simple backyard foundry, that’s powerful enough to melt scrap metal in seconds, but still pleasant enough keep around for decoration.
Step 3: Things You'll Need
Start this project with a big bag of play sand, and some plaster of paris. Both of which you can find at your local hardware store, for under $20.
You’ll also need a 10 quart steel bucket, and a tablecloth to cover anything important, because chances are this is going to get a bit messy.
A 2.5 quart bucket can be used for measuring the ingredients, but it also serves a more important purpose that you’ll see in just a second.
The recipe for this makeshift refractory lining, is 1-3/4 buckets full (21 cups) of plaster of paris, 1-3/4 buckets full (21 cups) of sand. And 1-1/4 buckets, filled (15 cups) with water.
Step 4: Refractory Mix
The moment the water touches the dry mix, the clock starts ticking. You’ve only got about 15 minutes before it all hardens up. So get busy mixing everything together.
It’s really important to get all the dry powder wet, and work out any lumps as quickly as possible.
After mixing for a couple of minutes, it should be fairly runny, and roughly all the same color. When you’re convinced there aren’t any clumps of powder left in the bucket, the refractory mix is ready for pouring.
Carefully transfer it to the steel bucket as slowly as practical, to minimize the splattering. There should be just enough fluid to fill the bucket about 3” from the top. Now bring back the plastic measuring bucket, and use it to form the center of the foundry.
Fill the bucket with water, to give it a bit of weight, but anything like sand or rocks will work as well. As you push the bucket into the center, the mixture rises upward, but it won’t spill out.
Before the mix is starts to firm up, try working the bucket up and down a few times, to help level it before it sets. Now hold still for 2 to 3 minutes. This will give the plaster just enough time to harden, so the bucket stays in place, even when you let go.
Time for a little cleanup.
Step 5: Clean Up
Everything will still need about an hour to really harden up, but the plaster’s still soft enough that you can clean and shape it to look really good. And while you’re here we may as well wipe the bucket down as well.
Dampen a rag and gently drag it around the top, the surface cleans up pretty nicely, and gets a cool texture in the process. When it looks the way you want it too, simply leave it for about an hour.
While you’re waiting, turn an old steel fire extinguisher, into a custom crucible.
Step 6: Making the Crucible
You can tell it’s made from steel because a magnet sticks to it. And magnets won’t do that to aluminum.
Depressurize the tank and unscrew the valve from the top, to make it safe and easy to cut in half with a hacksaw. Which should happen in less than a minute.
The bottom part of the extinguisher is what you want for the crucible, because it’s basically a steel cup 3” in diameter, and 5” tall. That’s going to be perfect for your custom backyard foundry.
Step 7: Making It Professional
At this point, the plaster should be pretty well set, so dump the water from the bucket, then use something like a pair of channel locks, to grip one edge of the pail, and pull gently toward the center.
Grip it with both hands and give it a bit of a twist, you can see the whole bucket pops loose, and pulls right out. This just created an amazingly smooth surface, which gives this makeshift foundry, a surprisingly professional look.
The only features you are missing now, are an air supply port, and a lid, so make those next.
Step 8: Lid & Supply Port
A 1-3/8” (35mm) hole saw is the perfect size for accommodating this 1” steel tubing, and if you center the metal cutting blade with the top line on the bucket, you can carefully begin cutting through the metal wall.
Once through the metal, it’s easy to burrow down at about a 30º angle because the plaster hasn’t fully cured, and cuts away like butter.
Now you have a tight, downward sloping hole, that the blower tube fits perfectly into, and it’s strategically placed, a few inches up from the bottom. This way, if a crucible fails, and dumps molten metal into the foundry, it will stay in the foundry, instead of dangerously flowing out of the pipe.
The blower tube is really easy to make. Start with a 1” steel pipe. This is the “business end” that will sit next to the hot coals in the foundry. You’re also going to need a 1" PVC coupling (Slip x FIPT), as well as some 1” PVC pipe.
You can see the threads on one half the coupling screw onto the steel pipe, and the slip adaptor on the other end, simply pushes onto the PVC tube. It’s that easy.
Now go one step further and make a lid to help retain the heat.
Get a couple of 4” U-bolts from the hardware store and stand them upright in a 5 quart, bigmouth bucket, filled with a half-measure of our insulating mix. (10 cups plaster, 10 cups sand ,7 cups water).
After an hour, the plaster should have set, and the whole thing pops free from the bucket, giving you a nice little custom lid for the foundry.
It still needs a vent hole for relieving pressure buildup, and you could just form one when you’re casting it, or you could try drilling one with a 3” hole cutting saw like this.
With the hole in the center, you can see you end up with a nice thick lid, that kind of looks like a giant white donut. This design works great for venting pressure, and gives you the option to melt metal as well, without even having to take the lid off the furnace.
Step 9: Finishing Touches and First Firing
Pick up a can of “Burnished Amber” spray paint, and give the foundry a couple of coatings to make it look a little more attractive.
When you get it fired up, the mini foundry gets so hot on the inside, that it will melt soda cans within seconds and fill a crucible with liquid aluminum. Look for how to do that, in another project video.
With this homemade furnace, you have the power to liquify aluminum in the backyard, and cast just about any object you can think of.
The best part is, when you’re not melting scrap metals, rather than taking up space and looking terrible, you can drop in a plant, and instantly transform it, into fashionable home decor.
Step 10: How to Melt Soda Cans
With this transforming “Flowerpot Foundry”, there’s certainly “more than meets the eye”. And by the way, if you run out of soda cans to melt, you could try using it as a blacksmithing forge, or even a bbq, for summertime grilling. After all, it is fueled by charcoal briquettes.
Well now you know, how to use commonly available materials, to build the mini metal foundry. Powerful enough to melt metal in seconds, but still pleasant enough keep around for decoration.
Well that’s it for now. If you liked this project, perhaps you’ll like some of my others. Check them out at www.thekingofrandom.com.
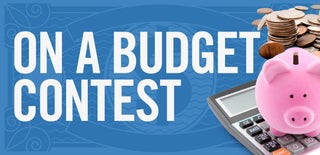
First Prize in the
On a Budget Contest
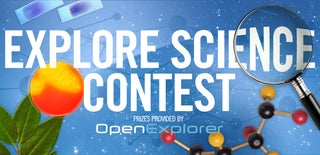
Participated in the
Explore Science Contest