Introduction: How to Make a Chainmail Shirt
- 1-2 years of time
- A very strong will
- 1200-2000 feet of wire (6000-10000 links)
- 2 pairs of small blunt nose pliers
- A drill (with a chuck)
- ½ inch or ¼ inch metal rod
- A dremel or other cutting device
- A vice or strong clamp
- Some 2 by 4s
- 4 screws
For an interview with me about my chainmail click Here
Step 1: How to Make a Chainmail Shirt
The first step is to be able to make the links of the chainmail. If you have some money you can buy them at theringlord.com as well as other jewelry stores. If you plan on buying links you can skip this step and the next.
First with the 2by4s you need to build a rig to support the rod (fig 1) that the links will be made on. Attach the 3 pieces together with the screws. Drill a hole in both sides of the wood, big enough for your rod to pass through easily. Now drill a small hole through the rod that your wire can get through. For wire I used a multi-purpose galvanized 16-gauge wire from Lowes. It is sold in 200ft lengths for around $8.
When you have all this assembled put the rod and drill into the jig (which should be clamped on a table) insert the wire into the hole and start the drill turning slowly. The wire will wrap it's self around the rod making a nice little spring. Use pliers to pull the wire out of the hole and slide the spring off the rod.
Step 2: How to Make a Chainmail Shirt
Now that you have the spring, it needs to get cut into individual links. When I started I was using a hacksaw, which did not work very well and took a long time. Then I got a dremel, which is a rotary cutting tool, and it got the job done very quickly.
To cut the spring, slide it on to another rod of the same diameter and put both in the vice or other clamp. When you are cutting it with the dremel be sure to wear safety glasses and do it in an area with no combustible gasses.
Depending on the length of the spring it should take around 5 min to cut and then you will have roughly 40 links that you can start using.
Step 3: How to Make a Chainmail Shirt
Now that you have links to start working with you need to know the pattern to attach them in. It is a very simple pattern, called 4 in 1 European mail; basically it means that every link is connected to 4 others. This makes a very strong and, depending on the size of links, a very dense fabric. For my chainmail I used 3/8” links, which are really too big to be protective or historically correct, I would recommend using ¼” links instead.
You will need a pair of blunt nose pliers that preferably do not have teeth. First take 4 links and close them so they will lie flat on the table. Then take a fifth link and open it so that you can slide the 4 other links on to it, then close the fifth link. This is the building block of your chainmail. (Fig 1, 2, 3)
Now that you have the basic building block of the shirt you will need to make many more. To attach them together line the 4in1s up so that the pattern matches. Then take another link and connect the 4 rings that are in the center. This makes another 4in1 within the first 2.
Step 4: How to Make a Chainmail Shirt
Now we can finally start making our shirt. I warn you this is a very long step and will require the most time and patience. First you will need to make a strip that is one 4in1 wide and the length of you waist. Once it is finished find the middle and put a link there to mark it. Now measure about 4” over on both sides. This will be your head hole, so 8” may be to big or too small, a good way to find out is to measure a t-shirt; but remember chainmail doesn't stretch so bigger is always better. Mark both sides of the head hole with links and remove the center link. On either side of the head hole you will add rectangles that will be the shoulders. I would recommend that the head hole be around 20 links or 6” deep so that it will not slide around too much when you bend forwards. Now comes the longest part. You have the head hole and shoulders you need to make the front and back pieces. I found the best way to do this is to make strips of the correct length 7-11 rows wide. Just keep adding on rows until it is as long as you want it, probably just past you waist. When you are done it should look like a tunic that fits over your head but has no sleeves and is not connected at the sides. This step will take around 1-2 years (depending on the size of the links and length of the tunic.)
Step 5: How to Make a Chainmail Shirt
Now that you have your chainmail tunic you need sides and sleeves. I would recommend doing the sleeves first. I made my sleeves 7in wide to make sure that they would not be too tight. A good way to estimate your width is to measure a t-shirt the fits loosely and then add 2-3in on that. Now you have to decide how long you want your sleeves to be: 6-18”. I made mine t-shirt length of around 6in but it is completely your choice.
Once you have these 2 dimensions you need to double the width so it goes back and front. Now take a ruler and stretch out part of the mail and count how many rows are in 1” so that you will know how many rows you will need for the sleeves.
You are know ready to make to identical rectangles that will become the sleeves of your shirt, once you have them attach the center of the sleeve to the center of the head hole. Do not connect the sleeves at the bottom.
Step 6: How to Make a Chainmail Shirt
Now comes the final step; attaching the sides. This step varies for everyone so I will give just basic instructions. Put on your chainmail tunic and with the help of a friend measure the distance between the 2 sides, don't pull it too tight across your body or you won't be able to get it on (or off). Depending on how loose you want it to be you can add a few rows to the initial measurement.
Make 2 rectangles that are that wide and long enough to reach from the bottom of the sleeve to the edge. Go ahead and connect your sidepieces.
Finally you will need a small piece to connect the sleeves at the bottom if they do not already meet. Once again measure and add more if necessary.
When you have these pieces connected all you have to do is attach under the arms. Unfortunately the pattern does not match up here so just improvise: it is not too critical.
You’re done!!!!!!
Step 7: How to Make a Chainmail Shirt - You Are DONE!
Congratulations on finishing your chainmail shirt! I am sure that you are very happy now and have a new sense of achievement. This is a very long, and at times boring project, but it is rewarding like nothing else you have ever done.
For more information on Chainmail I would recommend these websites:
• http://en.wikipedia.org/wiki/Mail_(armour)
• http://www.middle-ages.org.uk/chainmail.htm
• https://www.instructables.com/id/European-4-in-1-maille-chainmail-speedweaving/
• https://www.youtube.com/watch?v=oBQjp_oZ0Z8
• https://www.youtube.com/watch?v=ZXz3aOz3HbM
Step 8: Make-to-Learn Youth Contest Questions
My name is Bronwyn Erb and I am in grade 9. I made a nearly historically correct chainmail shirt.
Over the course of 10 months (Nov 2011- Aug 2012) I, link by link, put it together by my-self in the way you have just read. I worked mainly in the basement of my house but also at my cottage during the summer. This project gave me something to work towards, I have a tendency to just sit in front of the computer all day but instead I would watch Netflix while putting together links. This impacted on my family and friends because if anyone came over to our house or asked what was up with me I would say that I was making a chainmail shirt and then explain what that was. My aunt is a teacher so recently I went to her school to tell the grade 4s and 5s about chainmail and show them how to do it.
I learned a lot from making the chainmail but the most important things would be patients and the meaning of silence. Patients is pretty self-explanatory because there are over 6000 links in my chainmail, all of which were connected by hand. The meaning of silence is more difficult to explain: what I mean by it is that in our society there is a constant flow of information and garbage being thrown at us from TV, billboards, and shopping mails. Basically I found that when I turned off my computer and just sat and did chainmail I rediscovered silence and it is a beautiful thing.
If I was ever going to do this again there are a few changes I would make. First I would use smaller links (¼”) so that it would more correct. Also I would have a better pattern of cutting a lot of links and then putting them all together. Finally I would use the dremel for all of the cutting instead of a hacksaw because it takes a lot less time.
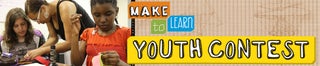
First Prize in the
Make-to-Learn Youth Contest
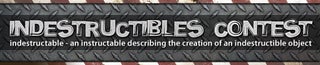
Second Prize in the
Indestructibles Contest