Introduction: How to Make a Spot Welder - for Cheap!!
Step 1: You Might Be Surprised How Cheap It Can Be
Have you seen the video above? If not, take a look now because it will help you as you go along in this instructable.
A typical resistance Spot-Welder can range in price from about $200-$800, but with a little resourcefulness, and a bit of free time, you can make one like this for about $10 or less.
Spot welders are used to fuse thin sheets of metal together. They are most likely used in the auto industry, as well as HVAC for welding metal ducting.
There are a couple of videos you should see before starting on this project, because you may want some background on how the device works.
Here is how to: Make The Metal Melter
Here is what it can do: The Metal Melter
Step 2: Take Some Measurements
Measuring the base of my Metal Melter, I found it was about 4-1/4".
I found a 6' length of 1x6 common board for about $4, which actually measures out at 5-1/2", so it will work just fine.
Two pieces of the board will need to be cut to 12" lengths (5-1/2" x 12"), but the rest can be pushed through a table saw to trim the width down to 4-1/2" (1/4" wider than the transformer base).
Step 3: Roughing the Case Together
The piece of common board that you just trimmed down to 4-1/2" wide can be cut into 3 pieces measuring;
4" x 4-1/2"
12" x 4-1/2"
24" x 4-1/2"
The other 2 pieces of the common board should measure;
12" x 5-1/2" (x 2 pieces)
You'll also need 4 pieces of 2x2 measuring;
2" x 2" x 13-1/2" (x 2 pieces)
2" x 2" x 4" (x 2 pieces)
This is all the wood you'll need for building the casing.
I used a 3/4" rounding bit and my router to smooth the edges and give it a cleaner look.
This is roughly how it will look when it's assembled.
Step 4: Prepping the Pieces
A notch needs to be cut on one of the 2x2 arms, and you'll see what this is for later on. I found a piece of scrap can be used as a template.
The notch can be cut out with a bandsaw, wood saw, or any other saw you can get creative with. I used a jig-saw, but wouldn't recommend it as the safest option.
The back panel (4" x 4-1/2") also gets holes cut that will accommodate an electrical light switch, and a notch for a power cable.
The pieces get sanded, primed, and painted. I chose to paint this black and yellow.
Step 5: Additional Materials
When I salvaged the Microwave Oven Transformer in this previous project , I saved some of the other components that can be used for our Spot Welder;
- The power cord
- The door handle
- Wires for the transformer terminals, with insulated spade connectors
- Power switch, with wires and insulated spade connectors
Aside from these, the only other items you'll need are;
- Simple light switch, with faceplate
- Copper offset terminal lugs that will hold ( x 2)
- 1/4" hex screws( x 2)
- Small nails ( x 2)
- Length of solid copper wire (4AWG is better, but I used 6AWG in this project)
The solid copper wire can be snipped into 1" lengths, that fit nicely into the terminal lugs.
The lugs have a mechanism that can be tightened with a screwdriver to secure the connection with the wire. The tighter the better.
Step 6: Start Assembly
Now that the wood is painted, finished, and dry (I gave it about 2 days), the unit can be assembled.
The back panel is for a light switch and a power cord.
Before screwing the panel into the base, make sure your cord goes in first. The thick piece at the end of the cord prevents it from pulling back though the hole.
This is also the time to add the 2 pieces of 2" x 2" x 4" support blocks to the base. Be sure of your measurements before you screw them down. You want them to end up flush with the side panels when it's done.
The Metal Melter can be placed inside now, and when a good position is found, can be screwed to the base with a couple of small screws.
Now it's time to wire up the electrical system.
Step 7: The Electrical System
Starting with the power cord coming into the casing, I stripped the black wire, and attached it to the bottom terminal of the light switch.
Next, I attached one of the wires I had salvaged, to the right terminal on the transformer, stripped the other end, and attached that to the top of the light switch.
The electrical could almost be finished here, but I wanted to add another switch, for safety and convenience, and that's where the salvaged switch from the microwave hack comes in.
The two wires attached to the switch can be wrapped with electrical tape to secure the connection and help insulate from electric shock.
The both ends of the wires are stripped so the copper wire is exposed.
One wire connects to the left terminal of the Metal Melter's primary coil, and the other wire connects to the white wire on the power cable that runs back to the house.
The electrical system is complete!
Step 8: Close It Up and Add the Arms
The sides can be screwed on with 6 wood screws on each side. I used 2" wood screws after drilling pilot holes to make sure the wood didn't split.
The trigger switch is attached near the tip of the top welder arm, and at a bit of an angle so it can be pressed easily. I found that 2 small nails held this in place perfectly.
Both arms can get inserted into the front of the casing, and with a bit of guesswork, a hole can be drilled through the side of the casing and into the end of the arms, so that when a nail is inserted, it will pivot.
Now you can see why we needed the notch in the arm.
To help the arm stay in an upright position, I added a couple of screws and rubber bands to keep the tension.
This also provides a little back pressure, and stabilization when using the welder.
Step 9: Adding the Electrodes
The copper lugs can be added to the tips of the arms.
I drilled pilot holes with a 3/16th drill bit, then secured the lugs by pushing the hex bolts first through the hole in the lugs, then through the lugs on the the Metal Melter terminals.
One in the top, and one in the bottom. It shouldn't matter which way they go, but I chose to make my top cable on the same side as the switch because it was easier to handle.
If the electrode tips don't line up perfectly, it's easy to bend them a little until they do.
When finished, it should look like this.
Step 10: The Finished Result
The Spot Welder is finished!
It will only work if the safety switch on the back is turned on, and even then, no power is delivered until the thumb operated switch is pressed.
To use, place thin sheets of metal between the electrode tips, then press the button with your thumb for about 3-4 seconds.
The massive electrical current pushing through the metal, heats it up to the point where it fuses with the other sheet.
You can release your thumb from the switch and wait until the weld cools enough to handle.
Welding these metal washers worked so well, I couldn't break them by hand. I had to use 2 pairs of pliers to get them to snap.
When the energized electrode tips touch each-other, you can see the high-amp sparks.
Note: Burning galvanized metals may release zinc-oxide fumes. Welding should be done in a well ventilated area.
Step 11: Additional Features
The electrode arms are only held in with nails, so if the nails are removed, the arms can be removed to extend the welders reach, and access difficult angles.
They go back together very easily, and the elastic can be conveniently replaced when necessary.
When the electrode tips are spent, it's easy to unscrew the bolt holding them in place, and add a fresh piece of copper wire.
Copper wire is relatively cheap. You can get a pice of 12" 4AWG wire for about a dollar. That means each tip is less than 10¢ each!
The power of the metal melter is still evident in the way this can bring iron metal to a boil! Be careful running the welder too long because there is a chance the wires will get so hot that the insulation on the cables will start smoking and melt.
Now you know how to make my version of a cheap Spot Welder.
If you haven't seen the step-by-step video, you can still see it here.
If you like this project, perhaps you'll like some of my others. Check them out at www.thekingofrandom.com
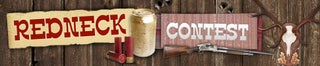
Runner Up in the
Redneck Contest
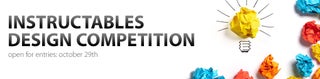
Participated in the
Instructables Design Competition