Introduction: How to Build Your Own Deadmau5 Mouse Head Helmet!
So you're a HUGE Deadmau5 fan and have been aching to get your hands on one of those sweet Mau5 heads - but NOT one like some of those epic fail's you've seen some people wear... you want a legit head that will be envied by all. Well, I'm here to help. The process is long, it takes a huge amount of determination and patience, but I promise you, in the end, you will have the sikkest Mau5head of any you've ever seen!
Alright, LET'S GO!!!!
Materials:
14” acrylic lamp post globe with 5.5” neckless opening – any color www.superiorlighting.com
6” acrylic lamp globe – white www.superiorlighting.com
4’x8’ Dow blue extruded polystyrene Styrofoam sheet 1/2” thickness
12” fully threaded rods 8/32” diameter (4pcs)
1 ¼” fender washers (4pcs)
8/32” wing nuts
Professional grade ratcheting hard hat
Lighting for eyes, can use LED’s – I use EL wire from www.coolneon.com
2yds fabric – 4 way stretch is best
Hot glue gun and glue sticks
Liquid Nails for foam adhesive and applicator gun
Stitch witchery
Clothes steamer
Ball end sewing pins
Dremel with bits for cutting, sanding, and drilling
Jigsaw or open ended hacksaw
Fabric measuring tape
Scissors
Single-edge razor blades
Small jaw clamps
Metal Mesh Food Cover Dome
Nylon tights or sheer chiffon for mouth
Electrical or duct tape
Poster board
Sharpie marker
Safety Glasses
Protective Gloves
Wire cutters
Rubbing Alcohol
Black Spray Paint
Getting Started:
Before you begin building your own Mau5head, there is one thing I cannot stress enough, take a great deal of time in the beginning to PLAN. Not only are the collective materials needed an investment, but to create your head properly, it will also take a lot of time – you want your final product to be worthy of all the blood, sweat, and tears that go into its creation! Find a few reference pictures to work from for inspiration and keep those at your work desk, it will help you to visualize along the way, as the head won’t look like much until it all comes together in the end.
For the most accurate replica, a 14” acrylic globe should be used, however if you are very petite a 13” could be used, or if you’re of a larger build you may consider a 16” globe, but in most cases the 14” will be ideal. My measurements are based off of a 14” diameter globe, if you should use a different size, please keep this in mind and adjust your measurements accordingly.
Step 1: Marking Your Globe
The first step is to mark grid lines on your sphere dividing it into quadrants. DO NOT rely on the little “nipple” opposite the neck opening to determine center, these are often off by a half an inch or more and can throw off your entire layout if used as the midline. Measure 19.25” from the edge of the opening at several places to find the center opposite the neck. Divide your globe into vertical quadrants intersecting at this point. Make a ring of poster board 44” in circumference that will fit perfectly around the globe at its widest point, and use this ring as your guide in drawing the lines. It will help you create a very accurate, crisp line easily. After both lines are drawn completely around the globe, measure from the center point down 11” on all 4 lines to locate the equator midline of your globe. The old phrase, “measure twice, cut once,” applies here as much as it ever could! Before proceeding to the next step, recheck your measurements one last time to make sure they are all equal.
The neck opening should be angled toward the back to both look the best and have the most natural angle when worn. The easiest way to map out the circle for the opening is to create a ring out of your poster board that measures 9” in diameter and place it on the existing opening front. The remainder of the circle will extend slightly up the back of the globe – be sure to check that the ring is equal on either side so that your opening will not be lopsided. Secure with tape, trace around ring with a sharpie, and remove poster board ring.
The mouth opening will rise slightly above the equator line in the center. Mark a dot 5/8” above the equator on the front center line to determine the high point on the mouth. Measure 6 ½” down from this dot to find the lowest point of the bottom lip and mark this point. Now place a dot on the equator line ½” in front of the side line on each side, this will be the outer edges of the mouth. Again, strips of poster board will be incredibly helpful to create even, straight lines. Use tape strips to secure the poster board across the globe starting with the center top point to outer edge points, draw your line with a sharpie. Then, using the same poster board strip, repeat this on the bottom edge from the lower point up to the outer edges. This will create a perfectly curved lower lip, and perfectly straight upper lip.
Don’t worry about marking the ear position yet, we will do that once the ears are built.
Step 2: Cutting Neck & Mouth Openings and Eye Globes
Now let’s move on to cutting the neck and mouth openings. The acrylic globes are thicker near the neck opening, and are tougher to cut, so this is the first thing you need to cut out. ALWAYS WEAR EYE PROTECTION WHEN CUTTING. Acrylic is extremely chippy and sharp when cut, protect your eyes! I use a jigsaw with a medium wood cutting blade on the thickest area near the front of the neck opening, and about ¼ of the way around, switch to a fine wood cutting blade as the acrylic becomes much thinner at this point. Keep a close eye on the acrylic so that you are using a blade right for the thickness you are cutting, too coarse and you risk chipping, too fine and it will do nothing but melt the acrylic. A little trial and error and a lot of patience go a long way here. You can also use an open ended hacksaw for this, or even a Dremel with a cutting blade (but be prepared for a lot of time if you go the Dremel route).
The mouth opening can now be cut, but be very careful not to rest your arm or place unnecessary pressure on the globe. Cutting out these areas weakens the structure, and you want to avoid cracking or otherwise damaging the acrylic during this phase of construction. ** do NOT cut the mouth out with the jigsaw, the acrylic is very thin here and it will break! ** A Dremel with cutting blade works great for the mouth, and the acrylic is MUCH thinner in this area. Be patient and make 2-3 passes over the entire area to cut through. You can also use an open ended hacksaw to cut the mouth, but again, be careful with the pressure you place on the globe and you’ll do just fine. Keep the cut out piece to use as reference as you form the metal mesh for the mouth later on.
At this point you can get your head inside, go ahead, try it on and make sure the neck hole is large enough and everything is looking even and properly placed so far. Keep in mind that the hard hat will elevate the globe up off your shoulders. You can even slip the hard hat through the neck opening at this point to try on if you would like. After everything looks good, sand any rough edges around the areas that were just cut out.
Since you’re likely covered in all kinds of acrylic bits and dust, this is a great time to cut the smaller white globe that will become the eyes. Mark out 5 1/4" circles on either side of the white globe and cut out with a Dremel. Smooth edges with a sanding bit or sandpaper on a wood block if you prefer. Remove any remaining sharpie marks with rubbing alcohol and a paper towel.
Step 3: Building the Lip
The foam sheet that is used for the ears and lip edge has a thin plastic sheet coating the outer edges. Remove this by gently peeling it off of both sides. Use your razor blade to cut ¾” strips of foam to use to create the lip. Hold your razor blade perfectly straight to cut a flat 90* edge for the lip. Before placing the foam inside the lip, gently bend it bit by bit along the length to create a gentle curve in the foam. Once it holds a nice C shape curve on its own, trim the length so that it is about 3” longer than the mouth opening and slip inside to check fit. Using the low temperature setting on your glue gun, attach the foam to the inside of the globe, making sure to align the foam perfectly to the cut edge of the acrylic and clamp with your small clamps until the hot glue cools and hardens. Work your way around the length of the lip until the entire length is attached. Repeat this process on the remaining lip, trimming the end to fit snugly up against the overlap at the corner of the first lip. Glue the corner area generously, as the junction of these two foam strips helps strengthen the mouth opening. After the glue has cooled, trim any areas that the glue squeezed out of, or sand smooth any areas where the acrylic overlaps too far being careful to keep very straight lines on the lip edge.
Step 4: Creating the Ears
You’ll notice that there are two basic ear shapes used: more round and more oval. I prefer the more oval ears, and my dimensions are based off of that shape, simply adjust the dimensions if you would like more round for your head. Create a template using poster board to ensure all ears pieces are identical. Create 2 cutouts inside to mark where your threaded rods will run through the foam. Using this template, trace 4 ears on the blue foam sheet. **keep this template for future use to create additional sets of ears** Cut outline with a jigsaw with coarse blade or hacksaw. Using the tip of your razor blade, cut two V shaped channels in TWO of the ears deep enough to accommodate the threaded rods. You will be sandwiching two pieces of foam to make one ear, and cutting this channel allows the pieces to fit together flush after the rods have been inserted. Test the channels for fit before moving on.
Also be aware that some fabrics are somewhat sheer, so keep that in mind when marking your foam sheets and assembling ears. Try to put the printed side on the inside of the ear foam sandwich to avoid any see-through when covering them with fabric later.
Once the channels are cut and fit checked, use low temp hot glue to secure the rods in the channels. The rods only need to extend ¾”-1” past the bottom edge of the ear. Draw a bead of foam safe liquid nails adhesive on the foam and then apply hot glue down the channels with the rods and around the perimeter of the ear. Quickly sandwich the other piece of foam on top and use strips of tape to hold the two pieces firmly together until the glue has set. Repeat process for other ear.
After the glue has set, remove the tape strips that were used to hold the sandwiched pieces together so that the entire edge of the foam is exposed all the way around. Now, take a piece of 300 grit sandpaper wrapped around a wood block to sand the edges of the ears perfectly smooth. You will want a nice flat edge with 90* angle all the way around to have a crisp, finished look to your ears after applying the fabric covering.
Now that your ears have taken shape you can decide where you want them to rest on the head. Again, there are two main positions for the ears: wider set, and higher perked-up ears. The spacing difference between the two is only about ¾”, so be careful when you mark your globe. Hold your ears up to the head to get a feel for where you would like them to sit – don’t place them on the side marker lines, the ear holes should be cut 1” back from the side midlines. Hold them up to determine height placement, mark, and check to make sure they are equally spaced down from the center point at the top of the head.
Now you can cut the holes for the rods to slip through. Your rods will be at an angle, so cut your holes oval to allow for slight adjustment as the rods slide into the head. You don’t want a super tight fit as this could cause the acrylic to crack as they move. Have you ever seen someone split the seat of their pants? Yeah… too tight of a fit.
After you’ve drilled your holes for the rods, attach them to the head with washers and wing nuts. Now it’s really starting to look like you’re getting somewhere!!
Step 5: Eye Placement and Lighting
With the ears attached, take the white acrylic domes and place them on the front of the head to figure out how you would like them spaced. Use a loop of tape on the inside of the domes to test out different placements and then step back and look at how it looks from the front and the side views on each side as well. Trace the outline of the eye domes onto the head.
Depending on the type of lighting you will be using in the eyes, you may wish to mark out any holes you need to drill or cut to accommodate the lighting source. I use electroluminescent cool neon wire from www.coolneon.com and only need to drill two small holes in each eye area to route the wires. At this point, do not yet install the lighting; this will be done after you have covered the head in fabric.
Step 6: Preparing and Installing Head Restraint
Next, cut sections out of the hardhat on either side to allow ease of access to the ear attachments once the hardhat is installed. The material hardhats are made of is very glue-resistant, so drill several holes through the hardhat in the area where it contacts the globe and also roughen up the area by sanding. Once you have done a test fit of the head with the hardhat in place, mark out where the contact areas area on the globe and secure the hardhat in place with a large amount of low temp hot glue. Make sure that there is enough glue to ooze through the holes you drilled in the hardhat, creating a mechanical bond between the acrylic and hardhat. Hold firmly in place until glue has completely cooled.
Step 7: Preparing Metal Mesh for Mouth Opening
Previously, in this section of the Instructable, you would have been beating a piece of flat 1/4" grid metal mesh into a curve with a rubber mallet, and probably would have been cursing my name because it is DEFINITELY an exercise in frustration... BUT, I've gone ahead and updated this section to give you a MUCH EASIER alternative that gives you a much, much better looking end result.
The solution: use a large (14" diameter) metal mesh screen food cover dome that is already in the proper spherical curve needed to form the mouth =) These are best found at your local Asian market, and should cost you around $5
Using the acrylic piece left over from cutting out the mouth, trace the outline of this piece onto the mesh dome and carefully cut the wire, making sure to be on the outside of the marked line. Always best to have a little more than you need, than not enough after you cut it out. Also, wear protective eyewear and heavy duty gloves to protect your hands - the cut edges are extremely sharp!
Once the piece has been cut from the mesh dome, go ahead and do a test fit inside the head, pressing against the foam lip on the inside to see how it lines up with the lip edge. When the fit is good, trim off any excessive overlap of wire (remember you will want at least ½” overhang on the inside to attach to lip). Wrap edges of metal mesh with electrical tape doubled over, or duct tape cut into 1” wide strips and doubled over. You should not have the tape go very far into the mesh area, just over the very edge to seal in the raw edge of the metal. This will protect you and your sheer fabric from the sharp edge of the mesh, as well as help you attach the mouth to the inside of the lip.
With the mouth mesh held in place, go into the head from the neck hole and mark dots where you will be placing the screws to hold the mouth in place. Remove mesh from the head and use a punch, thick nail, or other object to open the wire mesh in the places you will be inserting your screws. This will make installing the mesh much easier once it is covered with fabric.
Next, spray paint both sides of the mesh black. This will make the mesh disappear behind the fabric you will use to cover the mouth and because it won't interfere with your eyes from the inside, it will greatly increase your ability to see out of the Mau5head. A white or silver mesh will be very difficult to see out of and will make you very dizzy - do yourself a favor, spray it black!
Do not attach mouth yet, this will be the last step in creating your Mau5head.
Step 8: Covering Ears With Fabric
Start by laying your fabric face down on the table and then placing the ear on top of it. Pin around the perimeter of the ear with fabric pins while gently stretching the fabric so it fits nice and tight against the foam. Once you’ve pinned around the entire bottom edge of the ear, trim the fabric approximately an inch and a half out from the edge of the ear, making the fabric easier to handle as you secure with glue. Go around the ear approximately 4” at a time, securing along the top outer edge with hot glue. It doesn’t take a LOT of hot glue, so just make a thin bead of glue, stretch the fabric over, and rub with the other hand to smooth and cool the glue. Continue this around the entire perimeter of the ear. When the glue has cooled, trim off the excess fabric very closely to the foam and repeat process on other ear.
Now you’re ready to do the other side (front) of the ear. The process to pin the fabric will be virtually identical, except now you’ll run a strip of stitch witchery fusible web around the top edge of the ear. Pin the stitch witchery in a few places to hold until the fabric is stretched over it. Now, very carefully go around the perimeter of your ear stretching the fabric up the edge and over the back, and pin the fabric at the back of the ear. You are doing this to give a tight fit up against the stitch witchery, but not pin exactly to it. After you’ve gone around the entire ear and gotten a nice smooth fit all the way around, steam around the edge of the ear with your steamer to melt the stitch witchery and adhere your fabric edges together. Move slowly around the edge, allowing 10 seconds or so over each area to fully adhere the fusible web. Let the fabric cool completely, and then trim the edges. This will be your finished edge, so give a little teeny bit of stretch to the fabric as you trim it to get the smoothest even cut along the edge.
Secure the edges bottom near the rod ends with hot glue, making sure they are very smooth – this edge rests against your head and an even surface is very important!
Step 9: Covering the Head With Fabric
In this step, be extremely patient! You’ve put so much time into your Mau5head that you want the “icing” on this cake to be perfect!!! Some fabrics are somewhat see-through, so before you put the fabric on, remove all sharpie markings with rubbing alcohol.
Play with your fabric a bit to get a feel for how/where it stretches. Place it on the globe in several areas and stretch it to get an idea how it will mold to the area you are about to cover. I like to start with the bottom lip/back first. Use your C-clamps to hold the fabric in place after folding over the bottom lip, and stretch the fabric up and around, securing with clips or pins as you go. If you have a friend who sews, bribe them with free pizza and ask for help. A seamstress’ experience can be invaluable if you have one you can borrow for the afternoon.
If you need to, you can tack the fabric in place with a *tiny* dot of hot glue. Remember that the glue can seep through many fabrics, so test on an inconspicuous area first. After the fabric has been stretched into place, you can secure with hot glue, or with stitch witchery if you will be overlapping fabric to fabric (stitch witchery between fabric layers and steamed to adhere).
On the inside of the lips, use hot glue on the back side of the foam – not on the lip itself! You want the fabric taut over the foam lip edge and secured only on the back where the metal mesh will touch.
Repeat this process on the top half of the head, and at your seam you can either trim smooth or roll under for a finished seam like a sewn edge would look. Secure with hot glue or, my preference, steam edges together with stitch witchery.
Secure fabric on inside of neck with hot glue after rolling fabric over cut edge of neck opening.
Cut small slits with a razor blade through holes for ear rods and any holes cut for eye lighting.
Step 10: Installing Eyes
Now that your head is completely covered with fabric, reattach ears. This will help make sure the eyes get positioned properly. Go ahead and put in whatever lighting source you have chosen. If possible, try to put a reflective material such as foil as a background in the entire eye area to intensify the light output from the eyes. Secure the power source to the inside of the head with self adhesive Velcro strips.
Test fit your eye domes over the lighting and inspect for placement. When you are satisfied with placement, run a thin bead of hot glue around inner edge of the white acrylic dome, one at a time, and place over lighting source. Be careful to not drip any glue on the fabric of the head.
Step 11: Installing Mouth
Finally, the last piece of the puzzle is ready to go in! Cover the metal mesh mouthpiece with either a piece of nylon tights material, or sheer chiffon fabric and secure edges with either hot glue or tape. Place the mesh inside the head, holding edges tight against inner edge of lips. You will be securing the metal mesh in place with screws so that you can replace fabric if needed, or make other adjustments without having to battle a hot glue mess later down the road. When you have decided where you would like the screws to attach, pierce through the tape edge of the mesh to cut through the tape and fabric, and to start a path for the screw to go through into the foam lip edge. Screw through this slit into the foam, and repeat in several places around the mouth edge. Check from the front from time to time, and see where the mouth needs to be screwed in, giving the proper shape to the mesh.
Step 12: YOU DID IT!!!!!!
The last step is to ROCK THAT MAU5HEAD!!!
Switch on the lights and put on that amazing Mau5head you just created, and rock it like you mean it! You deserve it ;D
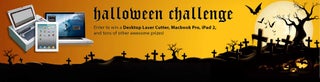
Finalist in the
Halloween Props Challenge

Participated in the
What Can You Do with a Dremel Tool?
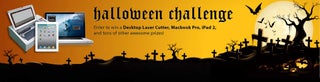
Participated in the
Halloween Epic Costumes Challenge