Introduction: How to Perfectly Clean Wires in Minutes!!!
Here is an old ham radio operators trick for cleaning wires for soldering that are old and corroded. It is hard to find this technique printed anywhere! I am a ham, NH7ZE, and learned it from my elmer (mentor). I am passing it on. I hope it helps people who need to clean wires:P Please vote!!!
Normally, if you strip a wire, and see it is corroded, there is not much you can do to restore it's shiny new conductive properties. There is scraping and scratching which comes to mind, but you'll never get it to the solderable slickness it once was long ago. After laboring and fretting over the corroded pieces of wire for a long, long time, you see that your sweat coming out of your palms and fingers are corroding the copper AGAIN!!!! Oh, dear. NOT TO WORRY!!!!! Give yourself a pat on the back, because what you will pull out of your bag of tricks now, will send all the corroded copper wires scurrying and scampering away in fear!!!! Here is how to clean any corroded wire without even touching it, in 30 seconds!! And what's more, you can even solder it!!!
This process uses two solutions, one is regular table salt and vinegar. Any kind of vinegar will work, from balsamic, to rice, to white vinegars. Its the acidity and corrosiveness of the salt and vinegar together that you want. The other solution is Sodium Bicarbonate, or baking soda, and water. This is used to neutralize the corrosive properties of the other solution, and to further clean the wires.
Step 1: Strip the wires to be cleaned.
Step 2: Get 2 containers, one for each solution. They can be paper cups, plastic, glass, bowls, whatever you can find. I have vials, because I am a professional electronics installer and I use these solutions out in the field.
Step 3: Get 1 tablespoon of raw salt, and put it in one of the containers. Fill up the rest of the container with vinegar, and stir the both together. As a general rule of thumb, put as much salt in the vinegar as will dissolve.
Step 4: Get 1 tablespoon of Sodium Bicarbonate, (baking soda) and add it to the other container. Fill up the rest with water, and stir well. Add more baking soda to make it cloudy. The amount is not important, as long as it is alkaline to cancel the acid of the vinegar solution.
Step 5: Put the stripped end of the wire in the vinegar solution, and stir the solution with the wire. any wire you want cleaned needs to be under the solution. Movement of the wire in the liquid speeds up the process.
Step 6: After 2 minutes or so, the wire will look very shiny and new in the vinegar solution. The acid and salt in the solution is etching away the oxides, exposing the bare metal. Make sure the metal is uniformly shiny. Leave it in longer if it is not perfectly clean throughout.
Step 7: Once the wire is satisfactorily clean, remove the wire from the vinegar, and plunge it into the baking soda solution to neutralize the acid's corrosive properties. If the wire was exposed to the air, without neutralizing the acid first, it would quickly corrode again. The baking soda keeps it clean and shiny. Swish the wire around in the baking soda water for about 10 seconds, and then you are done!! Shiny new wire ready for soldering, and conducting once again!!
Please vote on this instructable!!
Thanks for reading.
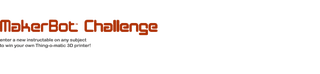
Participated in the
MakerBot Challenge