Introduction: INDEXER Rotary Table DIY Gearbox, Stepper Motor, and PLC Controller.
INDEXER Rotary table
One of difficult things in constructing things is cutting or making circles. Hopefully this will help some of you to invent some new ways of doing things. Adding circles, arcs, or curves to your next project may make it a winner.
This instructable shows you how to make your own indexing table to drill hole patterns, to cut out circles, and to cut many other things related to a circle. It allows you to set the index degrees by setting some push buttons. As an example setting it to four divides the circle in four 90 degree segments. This would allow you to drill a 4 bolt hole pattern or cut an arc 90 degrees in a piece of material.
If I won the Shopbot challenge I would use the machine and software start a small business making signs, templates, furniture, jigs, fixtures, engravings and parts out of wood and plastic. I have put together my own cnc mill drill but feel I need something bigger and more accurate like the shopbot to make it work. The autocad software completes the package for anyone to start a small business. Thank you to Instructables, Shopbot, and Autodesk for a great contest.
Features of index controller
Adjustable index degrees
Adjustable index speed
Single index by run button
Single index by proximity switch
Continuous run button
Brake output
Time lapse camera output
Index count indicator
Reset index to zero button
Index count increase button
Index count decrease button
Add 10 to index count button
Stop button
Self contained controller
Indexer can be connected to CNC computer control
Some Uses
Cutting holes
Cutting wheels
Cutting round slots
Cutting arcs
Drilling hole patterns on flat surfaces
Drilling hole patterns on round objects
Cutting slots on round objects
Triming pipe ends
Time lapse photography
Panoramic photography
Step 1: How to Set It
Set the index degrees by dividing 360 degrees by a number. The number is set by using the push buttons to increase or decrease by one or by pushing the increase by ten button.
To set it to 36 push the plus 10 button 3 times and then the increase button 6 times. Note you have to zero the count first by pushing the continuous button or holding the stop button on for 7 seconds. This will make the chuck index 10 degrees everytime the run button is pushed or the proximity sensor is triggered.
Check the count by counting the number of times the indicator light comes on in between pauses.
Run button is used to start the index to the next position or the proximity sensor can be used to trigger it to move to the next index position.
Increase button is used to increase the divide number by one.
Decrease button is used to decrease the divide number by one.
Continuous button allows stepper motor to run continuous full circle rotations. After the continuous button is pushed the run button is pushed to start the motion or the proximity sensor can be used. The stop button is used to stop the motion.
Time lapse mode button is held in for 5 seconds to enable that mode. First you need to set your index step amount. To set to 1 degree indexes first zero your count setting. When it is zero the count light will be turn on continuously. Then push the +10 button 36 times to set the count to 360. Then hold the time lapse mode button on for 5 seconds and the chuck will start to index in 1 degree increments. Push the stop button when you are done.
Step 2: Parts Needed to Make It
Materials
Programmable logic controller with pulse output ( Mitsubishi FX0-14MT-DSS Transistor Unit ) - Ebay
Programmable logic controller software for FX PLC - Ebay
Programmable logic controller cable - Ebay
Stepper module I used is an STMicroelectronics GS-200S in half step mode but I recommend geckodrives - Ebay or electronic supplier
5Vdc voltage regulator 7805 - Radio Shack #276-1770
24Vdc voltage regulator LM317T - Radio Shack #276-1778
(8) Momentary pushbutton switches - Radio Shack
bridge rectifier - Radio Shack
fuse - Radio Shack
fuse holder - Radio Shack
Multipurpose PC Board - Radio Shack # 276-150
1/2 inch romex connector - hardware store
Box to mount components - surplus
(1) 24 Vdc relay for time lapse output - Radio Shack
(3) On Off switches - Radio Shack
5/8 inch shaft to lathe chuck adapter - brother made it for me
Lathe chuck borrowed from small lathe
24 VAC wall transformer - surplus
Nema 34 Stepper motor - Ebay
Aluminum plates 8 X 4.5 X 3/4 and 8 X 5.625 X 3/4 inch - brother donated
Lovejoy coupling to fix gearbox shaft and motor shaft - Surplus
Gearbox with high gear reduction like 60 to 1 - Surplus
( I would like to upgrade to an actual milling rotary table)
Hardware for mounting everything together (10-32 threaded screws)
Spacers - I made them
Step 3: Buying Parts and Making It.
The PLC that I have used is still found on ebay so you can use the same program that I am currently running. I am still looking to improve the program so I was not going to upload it to instructables yet. But if someone wants to build this right now I will provide the program. If you want to use a different PLC just make sure it has a pulse output that can be used with stepper motors. Your PLC needs to have a solid state outputs to make this work correctly. Mechanical relay outputs will not work.
The gearbox on my indexer is surplus and so others will have to find one that fits their needs. Therefore it makes no sense for me to draw a drawing with all the sizes and bolt holes because yours is going to be different. The goal is to look at what I have shown and make something better that will fit your use. Actually I would recommend a milling machine indexing table to get the stiffness and accuracy needed cut nice parts.
My stepper module is also an older unit and so you will be selecting a different stepper driver for you project. I would recommend one of Gecko stepper drives. Remember most of the Gecko drives are 10 micro step drives. My drive is only 1/2 step drive. The PLC program will have to be changed to allow for this. This is a simple number change but it will slow the maximum high speed the motor can run. I will include a drawing showing a gecko drive being used. I removed the enable switch from the drawing because I do not feel it was needed.
The love joy coupling is ok for my light duty indexer but for accuracy I would use a solid flexible coupling.
The stepper motor on a index table does not have to be real big because if the high gear ratio of the gearbox. Also do not let that little stepper motor hurt you. That high gear ratio gives that little stepper motor a lot of power on the output shaft.
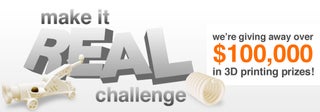
Participated in the
Make It Real Challenge
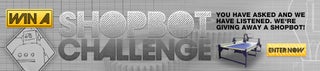
Participated in the
ShopBot Challenge