Introduction: Itty Bitty Mini Forge
Long time fans of blacksmithing, we delighted in having the Florida Artist Blacksmiths Association demo at our recent Gulf Coast MakerCon event in March. We were equally delighted to find a way to bring a little bit of the blacksmith arts into our suburban garage, when we came across this great video by NightHawkinLight, on how to make a Soup Can Forge. Intrigued, we looked around for some written step-by-step instructions and didn't see any, so we hope NightHawkinLight takes it as a compliment that we documented our little build and share it here, as perhaps a companion piece to his terrific how-to video, which we've included here and highly recommend you watch in its entirety first.
Our build time, start to finish: about an hour and a half, mostly 'cause we were klutzy with the fireproof lining mixture.
Step 1: Assemble Your Supplies
You'll need:
- A can - we used a 28 ounce crushed tomato can, sans the crushed tomatoes. We chose to leave the label on for a Warhol-esque effect.
- A block of wood
- A black iron pipe nipple - 1/2" x 2"
- Two L brackets
- A pair of wood screws to afix the brackets to the block of wood
- A pair of small metal screws with washers and nuts to afix the can to the L brackets
- A small bag of sand
- A box of plaster of Paris
- A gallon ziplock bag to mix the sand and plaster
- A standard propane torch with a spiral flame nozzle
- Some water
- Safety glasses
- Fire Extinguisher - just in case
Step 2: Prepare Can
Drill two holes, about a half inch in from either end of the can.
On the opposite side of the holes, about an inch from the back of the can, drill a 1/2 inch hole for the black iron pipe nipple, at a slightly downward angle.
Step 3: Fasten L Brackets to Wood Block
Measure out your brackets against the length of your can and where you drilled your bracket holes in the can.
Step 4: Affix Can to Brackets
Use metal screws with a washer and nut and fasten securely.
Step 5: Attach the Pipe Fitting
Just screw it in. It should all look like this.
badideasrus added useful tips in the comments, shared here:
"i like this. it's simple and easy. a note though! most of what i read indicates that the angle the pipe enters the forge is important. you want to aim the flow so that it lines up with the circular cross section, so that you get a spinning flow of fire. (bleh, so much harder to say with words what a picture would explain in seconds...)
"make the pipe tangent with the inner chamber, so that it flows round and round, instead of straight into. this keeps fuel inside longer, and supposedly makes the forge burn hotter (i think it keeps heat in too) http://www.habairon.org/images/propaneforge.jpg (this shows basically what i'm trying to say XP)"
Thank you badideasrus!
Step 6: Make & Pack Your Fireproof Lining
Mix equal part sand and plaster of Paris in a gallon Ziplock bag, with enough water to make a moist clay consistency. It's a little too crumbly in this photo, and not quite enough. This was actually the hardest part for us.
We used a 12 oz plastic cup for measuring and based on that would recommend 3 cups each of sand and plaster, and about 1- 1.5 cups of water.
You have to work pretty quickly because the stuff starts to set up fairly fast, and starts getting crumbly.
Pack the mixture in firmly, until the can is about 3/4 full, then dig out a 1.5 inch diameter cavity (we used a plastic spoon), leaving about 3/4" plaster/sand lining the can.* Carve a wider hollow towards the back (bottom) of the can, to create a better heat retention area.
Run a tool, or the back of your plastic spoon through the iron pipe nipple to clear out the plaster there. Wipe the outside of the whole thing clean with a wet paper towel, and then let it sit for a half hour.
*Alternatively (it occurred to us later), you can probably stuff the nipple with paper, and insert a toilet paper tube into the center of the can, or something similar, and pack the plaster in around that, then either remove it or let it burn when you turn on the torch.
Step 7: Fire It Up and Dry 'er Out!
Insert the propane torch nozzle into the pipe nipple and light 'er up! If the air holes on the nozzle are near the tip of the nozzle, make sure they're not covered. Your itty bitty forge will burn cold for about 10 min. or so, until the last of the moisture in the fireproof lining is burned off, and then you'll start seeing the classic red glow of a nice hot forge.
Step 8: Forge Away!
Now you can start doing some small scale metalsmithing and glass forging.
And those are whole new how-tos! We have some ideas and hope to share some of those back here soon.
Have fun! And thank you NightHawkinLight for getting us started!
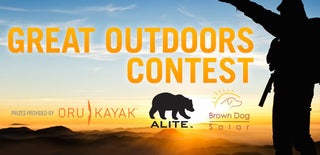
Participated in the
Great Outdoors Contest
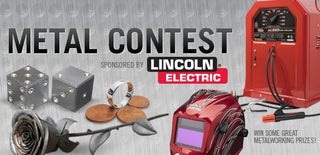
Participated in the
Metal Contest