Introduction: Latex Concrete Roof
- Lightweight - the support structure does not need to be as extensive as with other materials.
- Fast Setting - you don't have to be as scared of clouds on the horizon as with concrete.
- Goes Quick - almost equals the speed of putting up metal roofing, which is a material we often avoid as it does not last as long, or look or sound (in rain) as nice as concrete options.
- Inexpensive - for its strength, durability and speed, it is cheap.
- Artistic - it allows for many different designs, though a pyramid structure seems to be the most efficient.
The shape and style of your latex concrete project depends almost entirely on your imagination. Within this article, we’ll run you through both the overall principals and the more specific details, and we hope you go on to make some wild looking creations.
For more information on concrete or other building materials, visit the shelter section of our site.
For more information about this method of building, please read "Latex Concrete Habitat" by Knott and Nez
Step 1: Materials and Tools
- Metal reinforcement (rebar or castillos)
- Cement
- Sand
- Vinyl or plastic
- Lumber, to hold the form together and in place
The Frame:
- Either metal, lumber or rebar-reinforced PVC
- Screws or wire to assemble the frame
Fabric:
- Vinyl tarp or billboard (optional)
- Loose-weave fabric, like nylon netting or shade cloth
- Either screws and washers, staples or tie-wire (to attach the fabric)
Latex Concrete:
- Acrylic Latex (100% acrylic concrete bonding agent)
- Cement
- Fine screened sand
- Paint
Step 2: Posts
We have found that fabric forming is one of the easiest and cheapest ways to form concrete. Instead of time consuming and costly wooden or metal forms, you use little more than a piece of plastic or similar fabric. The end result is not only aesthetically beautiful, it is also stronger, because it lends itself to rounded shapes, compacted pours, and consistent curing.
We have more information on how to make a fabric formed post here, so please consult that Instructable for more details. However, we wanted to give you a rough outline of the process within this article.
- Mark out the corners of your structure. To make sure it’s square (if you want it to be), measure diagonally between each corner. The two lines of the figurative X are be identical when square.
- At each corner, dig a 12” diameter hole, about 2 ft deep (and preferably wider at the bottom than at the top, so that it is “belled”).
- Stand metal reinforcement up in the hole. Make sure the bottom of the metal is up on rock or plastic instead of touching the dirt. Make sure the post is plumb/level.
- Pour concrete in the base, to just above dirt level. Wait a couple of days before continuing, so that the concrete can set.
- Cut a length of vinyl tarp or black plastic, 36 inches wide. It needs to be a little shorter than the metal reinforcement, as you will be tying the roof’s frame to the reinforcement. For ease of explanation, let’s call the post 96” tall (the reinforcement will have 2 ft extra in the ground and 4” extra on top, so will be 124”).
- Place two pieces of 8 feet 1x4s, 22 inches apart (the tarp will stretch a little, so make it a little skinnier than you want the post to end up).
- There should be about an extra 7” of tarp on both sides. Double this back on itself and staple it well to the lumber.
- Stand the form up and put it around the metal reinforcement of your post, so that the two 1x4s meet, flat against each other. Screw them together.
- Level the boards in two different plains, and then brace the form using lumber or metal.
- Pour concrete into the plastic, patting it as you go. You want the concrete a little soupy, so that it fills the form better. However, remember that the drier concrete is, the stronger it will turn out, so do not make it soupier than necessary. Patting helps to compact the concrete and release air bubbles that can make the post weaker. If you pat it too much, the post will start to bulge at that point.
- When the concrete is hard to the touch, take down the braces and then release the screws and carefully peel off the form, which you can store for reuse. We have found that concrete sets up far quicker in a plastic form – we don't really know why.
Step 3: Frame
- Metal is the strongest and most durable. It is also lighter than wood, as you would not need a very thick gauge metal. However, it is expensive and requires better tools (saw blades, drill bits and, even better, a welder). You will also have to use screws and washers to attach the fabric.
- Lumber is fairly cheap, and easy to work with (if you need an explanation for that last statement, go and cut a piece of metal and lumber by hand, and see what you think). You can also staple the fabric to the wood, which will save time. However, it’s kind of heavy and will not last as long, especially in damp conditions.
- For the roof of our water tanks, we use 3/4” PVC with 1/2” rebar inside. It worked great. It’s cheap, light and easy to work with. However, it’s not as durable and we wouldn’t want to walk on it. It’s a good choice for a small roof that you won’t need to get on, and that you want to be curved (arch or dome).
This form of construction lends itself to sweeping shapes, which are often very difficult to visualize in your head. Our strongest recommendation with latex concrete is to buy yourself a box of straws and some plastic wrap or flimsy fabric. Pick a scale for your straws and make a base frame that will fit your particular project’s dimensions. Then play with various shapes and possibilities by using the straws as your frame material and the plastic wrap as your fabric.
You can make any shape you wish, so long as it is structurally sound. While the tank roofs we do are dome-like, set on circular walls, the kids’ room roof consists of three circus tent style peaks. You can similarly use peeks, or arches or conics. You can also stick pipes up into the fabric from below to make extra dips or features. You can remove these once the latex concrete has hardened.
Step 4: Fabric
You want to use a fabric with a fairly loose weave, so that the concrete can fully penetrate it. Some people use burlap and are very happy with it. At first, we used two layers of fiberglass screen, alternating the direction of the fabric for each layer. As it turned out, this was a tighter weave than what you really want. However, it still worked just fine, just took a little more work to get the concrete to soak through properly. We’ve also used orchard netting, doubled up. 80% Shade cloth works well. The key is finding something cheap and available in your area, and then doing a couple of test runs, to make sure it will work. The thing to look out for is penetration: you want a coat from the top to penetrate all the way through the fabric without falling right on through.
Something we have started doing, which we would highly recommend, is putting a vinyl tarp on top of the frame, and then the fabric. Not only does this make less mess when applying the latex concrete, it also provides a waterproofing backup, should a hairline crack appear. It does decrease the sweeps you might achieve with a more flowing fabric, but you can always drape it a little if you wish.
Once you’ve decided on your fabric, attach it to your frame. Depending on the frame’s material, you can use screws with washers, staples or tie it on with zip-ties or wire.
The beauty of this system is that any hole and extra bit you want to cover, just attach fabric over it. It is a forgiving style of building and allows for some last minute whims.
Step 5: Latex Concrete
Once all your fabric is firmly attached and you have added any extra features by pushing out the fabric with poles from the underneath, you are ready to do the latex concrete.
So, where do you get the latex, or acrylic, from? We started off using a product called Sikalatex, but we ran out and had to move on to a 100% acrylic concrete bonding agent, which was much better. Look for anything with a high percentage acrylic. If it stinks of ammonia, you’ve got the good stuff, but most acrylic additives for concrete will work.
You want to do a minimum of three coats: a scratch, brown and finish coat. You can do more coats if you wish, but three is sufficient for most applications. To mix the concrete, we used a five gallon bucket and a drill with a paint stirrer on it. The concrete is fairly liquid, and thus easy to mix, no matter how you do it. It does dry pretty quickly, due to the latex, so don’t mix huge batches unless you have the manpower to apply it (which is also very fast).
The application is super easy. You can pour (or throw) it on and then spread it out using a paint or broom-like brush. It sets up fast, so you can usually do a couple of coats in a day. After a couple of coats it starts to gets hard. That hardness will increase over time, as it cures completely. In fact, it will continue to get harder over weeks. Even though you probably could, strength-wise, we recommend you don’t put your weight on an unsupported part of the fabric until it is fully cured.
Scratch Coat
First you do a coat on both sides of the fabric. If you have a vinyl tarp between the frame and the fabric, you won’t need to coat the underside, which is great as that’s the hardest part. Just make sure that the whole fabric gets covered (you can pick up pieces of the fabric and then let it snap back onto the tarp with concrete underneath.
The mix we used for the first layer was a 1:1 of water and acrylic, and then mix in your portland cement. It should have the consistency of heavy cream. The mix wants to be pretty liquid for this first coat, so that it penetrates (but doesn’t fall through) the fabric.
Brown Coat
The subsequent layer consists of a 1:1 acrylic and water, and then add 1:1 cement and finely screened sand. This mix can be more liquid than the first, as it will set fast.
Finish Coat
Do the final coat without sand. It will have a much smoother finish and not use as much paint. You can make this mix very liquid and paint in on thinner than the previous coat.
When we did the kids’ rooms roof (a 30 ft by 15 ft structure), we left three holes in our structure, one at the top of each peak, so that we could get up there and pour the next coats easier. We then went back and covered those holes before putting on the final coat. Latex concrete binds very well to itself, so you do not have to worry about cold joints, as with regular concrete.
You can, after the concrete has cured a couple of days, paint the roof.
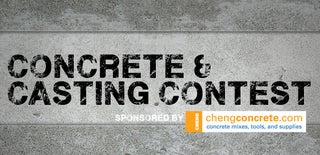
Runner Up in the
Concrete and Casting Contest