Introduction: Magnabiner - Build Your Own Carabiner
Hey everyone. Today we undertake a new adventure in the previously unfamiliar realm of metal. This month of January I was taught how to use a wide range of metal tools and realized the endless realm of possibilities that can be created using metal and metal tooling techniques. Here is my first, completely metal, project.
I present to you the Magnabiner, a carabiner unlike any you have ever seen before. The Magnabiner uses magnets to attract the gate (part that opens on a caribiner) to the frame. In addition to using magnets, the frame can rotate 360 degrees. No longer are you limited to a single line of freedomas found in traditional devices; now you can open it in whatever direction is easiest. Also, to ensure the gate does not become unlocked by accident, the gate features a slide on it that springs up, prevented any unwanted movement yet it i still able to be opened using one hand. On opposite, top side, there is a wire gate to attach your caribiner to belt loop or any other loop available without having to utilize the main gate. Finally, the skeleton frame allows for a lightweight, sleek design to complete this revolutionary new device.
The best part is, you can build this for yourself and impress all who see it. I hope to show you in this project how to take an idea drawn on a piece of paper in a finished, useable product that you can make yourself.
As always, my name is Christian Reed and I am currently a sophomore at MIT with a passion for building things. Here is my blog. Hope you enjoy and do not hesitate to ask any questions you have!
THIS IS NOT A ROCK CLIMBING CARABINER SO DO NOT TRY TO.
Step 1: Sketching
The first step in designing almost anything (in this case a new caribiner) is sketching. Sketching consists of creating a rough idea of what you are building and designing. Sketches do not necessarily need to include dimensions but are more or less of a method for placing certain components and creating a visual representation of whatever it is your trying to create. Pictured below is my rough sketch of what I wanted the carabiner to look like. It was just a rough layout of what I wanted to make, the various components it would contain, as well as the approximate shape. This served as the foundation for all of my future designs and definitely necessary to generate the appropriate computer files for machining in the next step.
Step 2: Designing the Files in a CAD Program
The next step after sketching your idea is to turn into something readable to a machine (CNC, water jet, laser cutter, etc) as well as provide dimensions if you plan to make any of the components by hand. There are several ways and programs to accomplish this task. For my particular project, I used SolidWorks as that just happens to be the program I have on my computer but any CAD program will work (Autocad, Rhino 3D etc). Once you have the program of your choosing ready and set up, you can begin to translate your design, one component at a time, into a computer file. Later on, you can turn the multiple parts into an assembly to see the entire design functioning as one. There are many tutorials across the Internet for learning how to your particular program ( I have included a few links below). The cylindrical shapes were not very hard to design and I recommend trying to make them if you want some practice in whichever program you feel most comfortable to use. I have, of course, included the necessary CAD files to utilize in your construction of this project.
The attached zip file has everything you need to build this project (dwg files, jpgs, pdfs, etc).
Attachments
Step 3: Prototyping
On a side note (and not really necessary for this project) is considering how to make whatever you have just designed. Originally, I was considering making this part out of some type of plastic for prototyping purposes. However, I decided on aluminum due to its relative ease of machining and is considerably stronger than most plastics. Another possibility is making the whole frame out of steel which would make it much stronger (but heavier) than if you made it out of aluminum. The purpose of the prototyping phase (at least in my case) was to demonstrate that my device actually worked. The big part of this step was to see how the magnetic gate worked and how the frame felt in my hand. As you can see in the picture below, I began be free handing the design using a Dremel and acrylic. Later on, I water jetted the frame and routed the edges. Basically, it is a time to experiment around and create a working version to prove to yourself that the device actually works.
Step 4: Materials, Tools, and Skills
Materials
-Sheet of 3/8" Aluminum
-Size depends on how many frames you plan to make
-Although I used 3/8", it came out slightly too bulky so it may make sense to use a slightly thinner sheet.
-Steel would also work and be a lot stronger (I am going to try this sometime)
-5/8" Aluminum Rod
-Spring Wire
-Metal Epoxy
-3/8" Steel Ball Bearing
-#6 Bolt
-3/8" x1" compression Spring
Tools (As always, there are alternate ways to do everything, send me a message if you need help)
-Lathe (CNC or manual)
-Mill
-Waterjet Cutter (Alternate methods are possible)
-Pliers
-Drill Press
-Wood Router (w/ 1/8" Round Edge bit)
-Digital caliber
Step 5: Water Jet the Frame
Here we will waterjet the frame which will serve as the basis for the entire caribiner. Every water jet machine and CAM program is different so I will not bother to go into details but rather give you a few pointers. (I used an OMAX)
NOTE-If you do not have access to a waterjet, there are countless places you can send away to get the frame(s) cut out for you. I have listed a few below.
-Make sure the metal you are cutting from is clamped down properly and the end of the clamps will not interfere with the tool path of the machine.
-Check to see if there is enough abrasive in the hopper.
-Ensure the water supply is on
- Zero the axes in the correct location by the edge of the piece
- I found that that using the slowest setting on the OMAX software allowed for the smoothest cut.
Once you have your desired number of frames cut, take them out of the waterjet and dry them off.
http://www.jitwaterjet.com/
http://www.jacksmachine.com/
Step 6: Routing the Frame
This is a pretty interesting step as it involves using a standard tool for a slightly unconventional purpose. We will route the edges of the frame to create a fillet along the edges (a rounded edge instead of the current square one left by the 2D water jet). This step, at first, proved to be a little changeling as 1) I had no idea how round aluminum and 2) a way to clamp such an odd shape to the table. What I wound up doing was using a standard wood router with a normal, carbide bit while placing the frame in a custom made jig.
To begin the jig construction, I found an old piece of plastic (scrap wood would work too). Using the hole pattern I have included, drill each respective hole. Screw the 1/2" screws through the holes and once completed, place a sheetrock guide (blue things in the picture) over the screw. The frame will now snuggly fit. I added four screws in each of the corners so i could attach the plastic to a larger piece of wood that I was able to clamp down to prevent the whole thing from wobbling. Once the frame is snuggly fit in, you can begin to route the edges. Use a lower than normal RPM setting on the router as you are not routing wood. Make sure the bit and the direction you are traveling are the same so that you are not climbing with the router. Once you have completed one side, flip it over and repeat the process on the other side.
Step 7: Finishing the Frame
Here we will make a slot for the rod coming out of the ball bearing to slip into along with the epoxy. This is the worst part of my design by far. If you made the entire thing out of steel or aluminum (whatever metal, just the same type) you would be able to weld it on. Since this is a prototype, I was okay with this idea (for now) of filling the hole with epoxy later on.
To begin, clamp the frame in the vice as shown. Use a 1/4" endmill and make a pass into the center of the frame as seen in the picture. Once you have a slight groove, use a drill to finish the process. Keep in mind it does not need to be deep and will be filled with epoxy to support the magnetic gate later on in the instructable. Again, if you have any other ideas for this step, please let me know as I could not seem to find a way to make it super strong (perhaps an inherent design flaw for this particular design. Again, the goal is to create a small notch in the frame for the magnetic gate to attach to the frame. If this is unclear, continue going through the steps and it should be clear what its purpose is.
Step 8: Sliding Gate I
The sliding gate is clearly the most innovative feature of this particular design. The freedom of rotating on a ball bearing and using a magnet and a sliding gate have never before been used in caribiner construction and here we will use all three in a single step.
This process relies heavily on having at least some prior experience on a lathe. However, even with a basic understanding, you can accomplish this (to provide a reference, I had only started using a lathe a few weeks ago).
Basically you just want to follow the designs I have attached. I used the knurling tool to create the knurls on the slide and then a combination of the cutting tool, end mills and drill bits for the additional steps.
Cutting tool-All of the outside faces
Drill-begin holes or complete holes that go through the whole work
End Mill-After drilling holes that do not go all the way through, I used the end mill to square off the bottom of the hole.
Use the attached PDF's to see what size bits to use, and again, if anything is unclear or if you need some advice, shoot me a message.
Step 9: Sliding Gate II
Finish turning the remaining parts found on this page. you should then have all the parts necessary to complete the assembly of the gate (minus the ball bearing at the bottom so do not put that cover on yet. Refer to the assembly diagram and attach the parts. I just dabbed a little epoxy on them to keep them together (after all, it is a prototype) but a good idea, if you want it to be much stronger, is to tap (thread) the pieces together (however, this may require some resizing of the plans).
Step 10: Ball Bearing
In this step, we will drill a hole in a ball baring to allow us to insert a rod into it and will allow the magnetic gate to rotate freely. First, take the ball bearing and clamp into place using a vise and parallels to allow a little less than half of the ball bearing to be exposed. Using a file, file down a small flat surface which is parallel to the ground. This will create a flat surface to drill into. Next, move the clamp over to the drill press and begin my using a center drill (or a center punch) to mark the centering the ball where you will drill into. Once you do, use the drill bit to drill a hole about 1/4" into the ball. Then, insert the rod (or thread the hole if you'd like ) using some force like a mallet. Once it is snuggly in, place inside the holder we created in the previous step and then place through the rod and onto the slide. Epoxy into place ensuring that the ball can still rotate freely and isn't epoxyed into place. Once this is done, epoxy the magnet into place I. The holder on top of the slide. Congratulations you have now completed the magnetic gate.
Here is a great tutorial for how to drill into a ball bearing.
http://www.stopmotionworks.com/drlballs.htm
Step 11: Wire Gate
Simply put, the wire gate is a (b@$%#) trying to get it properly without messing up the wire. Again, if you have a better idea let me know. This step, for me at least, involved a lot of trial and error. You can see what the wire gate needs to look like so bend the gate accordingly. Use pliers and whatever else you have to bend the wire into the right shape and then insert into the two repetitive holes in the frame assembly.
Step 12: Assembly
Pretty much all that is left at this point is to epoxy the gate in place. To accomplish this task, I first mixed the metal epoxy and then added some to the hole we perviously created in the frame. Once the hole had a fair amount of epoxy in it, I stuck the end of the rod in the hole. You want to try and make sure the rod is centered in both the x and y directions. Let it fully cure. Finally, epoxy the magnet to the top part of the frame as seen in the picture.
Step 13: Complete
Congratulations. I hope you enjoy your new carabiner as there is literally nothing like it. I was able to take my idea and turn it into a physical prototype and now have a great caribiner to go camping with. Again, it is definitely not rated to go rock climbing so do not bother. I also hope you enjoyed seeing the process of turning a sketch on a piece of paper into a fully functional device. As always, let me know if you have any questions, comments, or suggestions and I would be more than happy to assist in any way I could. Happy building.
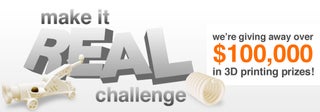
Participated in the
Make It Real Challenge