Introduction: Make a Broken Screw Extractor
If you've ever used small screws in hardwood then you've probably experienced the joy of broken screws! Most likely you were installing a hinge and need to place another screw in the exact location of the broken screw. What do you do now? Having faced this dilemma multiple times I came up with this a simple extractor which works quickly to remove the screw while allowing you to plug the hole and try again. Similar extractor are available for purchase however they break easily and commonly only add to your frustration. This tool is robust, cuts cleanly and will last for a long time. Let me show you how to make it.
Step 1: Supplies & Materials
I got this idea when I found a 4mm deep socket on sale at Home Depot for $2. It's the perfect size. The outside diameter is just slightly bigger than 1/4" which means a 1/4" wooden dowel can be used to plug the hole it makes. The inside diameter is just big enough to accept the broken screw end as you're drilling it out (depending on the size screw used). This size works well with #4 and #6 screws like you would use on a piano hinge. This concept could be used with any size screw using an appropriately sized socket.
Here's what you need to make and use this extractor:
4mm deep socket
Dremel tool with cutting disk and grinding stone wheel
Drill
17/64" drill bit
Socket adaptor tip for your drill
1/4" wood dowel
Wood glue and sandpaper
Step 2: Making the Extractor
Essentially what you are going to make is a 2 tooth hole saw on the end of the socket. To do this simply use a Dremel cutting disk and make a slot in the socket tip roughly 3/16" deep. Create each tooth by grinding off the extra metal on a diagonal line from the end of the socket to the bottom of the cut groove on both sides. When you hold the socket with the end upright the point of the tooth should be on the right.
When I initially tried out the extractor I had made I was quite disappointed as it didn't cut at all. I finally realized when I ground the tips I made it backwards. If you look closely at the pictures you can see the point of the each tooth is on the left and can only cut when the drill is spinning backwards. When I reversed the direction on my drill it cut like a champ! It works so well I've never bothered to make another and how to use it is a tightly held shop secret. Keeps it from walking off!
Step 3: Extracting a Broken Screw.
To extract the screw simply drill with your mini hole saw around the screw end. To do this you need a 1/4" socket adaptor chucked up in your drill to accept the socket. I have found that a shallow 17/64" hole drilled over the broken screw really helps to keep the extractor from wandering (not pictured). As you can see in the 3rd picture this little tool drills a very clean hole. Continue drilling until you feel the screw loosen and remove it.
Step 4: Starting Over
Now that your broken screw is removed you can simply plug the hole with a 1/4" hardwood dowel and try again. I primarily have used this little extractor when installing piano hinges. The beauty is the piano hinge covers the dowel completely so this quick repair is not visible on your finished project.
To avoid using this extractor my best tip is to drill a pilot hole and use a good quality steel screw to thread each hole before installing the brass screws. Small steel screws are much harder to break and this avoids messing around with repairs.
I hope you will make this little extractor and keep it handy in your shop. You still won't enjoy breaking screws but at least you can avoid freaking out about it. I hope this instructable was helpful. Thanks for reading it.
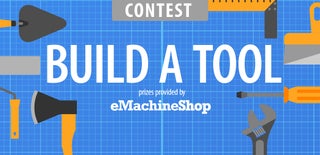
Participated in the
Build a Tool Contest 2017