Introduction: Make a Pinhole Box Camera That Uses Standard Spool Film
Make a working wooden film camera to take creative and unusual photographs. This design is for a medium format pinhole camera that takes any 120 format roll of film.
This project comes from a love of Kodak box brownies, the camera design that introduced the world to the idea of a snapshot. Before these readily available cheap mass produced sheet metal box cameras photography was expensive and inaccessible. I shoot with a few models and they're still great cameras. I also make pinholes, there's just something special about making images with a camera you've made yourself.
Both types of camera reduce the process of taking pictures to the fundamentals of photography. The only variables are composition and exposure, no focusing, no aperture selection. Just load the camera with film, point it at something interesting and take the lens cap off. Removing the complexity is a great way for beginners to learn about exposure and light levels. Knowing you've only got 8 exposures makes you think a lot more about composition too..
For my first laser cutter project I wanted to see if I could make a working pinhole camera based on the Brownie. After a few prototypes, and then a few more, I've learned how the cutter works, and settled on this design. Using a separate film cassette makes it is easy to reload film while you are out taking pictures. Like the Box brownie's this camera takes eight 6x9 cm negatives to each roll of film.
The files are open source so feel free to take them and have some fun. It'd be great to see the results!
It was designed and cut at DoES Liverpool Maker nights.
NB This instructable is to show how to build this camera. If you are new to pinhole photography and need some more information about taking pinhole photographs there is more information in this instructable https://www.instructables.com/id/Design-and-Build-y...
There are also lots of useful resources on the World Pinhole day website.
Attachments
Step 1: Materials and Tools
The files needed for this project can all be found in this repository.
https://github.com/huffeec/huffeeCamera
The pieces are grouped into two files, the camera case and the film holder. When complete the film holder slides inside the camera body and is made light tight with the back panel. The advantage of a separate film holder is being able to change rolls of film just by unclipping two rubber bands.
For the plain camera design you will need;
For the decorated case replace the front piece in PinholeCase.svg with this version PinholeCaseFrontEtched.svg
To cut the parts yourself you will need two 300mm x 300mm sheets of 3mm material. I use Birch Ply but any material that can make a light tight box would work, but remember there is a lot of gluing so pick something you are able to stick together.
The designs are colour coded as follows
Black - Designs and construction marks, just mark the surface of the material. Mark these first.
Yellow - Decorated case only. Use the etch setting on the laser cutter.
Blue, Red, Green, Pink - Cut the full thickness of the material. The colours are intended to be cut in this order so that if any parts drop slightly while they are being cut it won't matter.
To make this camera you will also need;
- 3d printed winder key
- 2x 80mm lengths of 3mm diameter metal tubing
- A bamboo skewer
- 2x 1/4 20 UNC Nuts for the tripod mounts. There is no metric equivalent for the standard tripod mount thread.
- A 24mm M4 bolt and nut.
- A compression spring, the kind you find if you break open a ball point pen is fine.
- A pinhole, or make your own with a thin square of metal and a pin
- 2x Strong elastic bands
- A 2cm square of red cellophane, think toffee wrapper or lighting gel.
- An empty 120 film spool. Anyone who uses 120 film, or any lab that develops it should have plenty of spares.
- Matt black paint, ideally spray paint
- PVA or other wood glue
- Fine sandpaper
Step 2: Cutting and Painting
Now you have all your parts the next step is to paint the internal pieces with matt black paint.
Pinhole cameras need long exposures so it is important to stop stray light bouncing around inside your camera as this will reduce the contrast of your photographs. Painting the internal parts helps absorb stray photons. You might also want to experiment with the same black 'flocking fabric' astronomers use if they're making telescopes, but paint will work fine. Spray paint works best but if you are planning to brush your paint aim for a thin smooth finish.
- The parts shown in the first image don't need painting. These include two of the three pieces that make the back cover, and most of the small pieces for the winding knob and lens cap.
- The next two images show the parts that need painting on one side only. NB It matters which side! The first of these shows the film holder, and the other two bits for the winding knob/lens cap. The other has the five pieces needed to make the camera case, and the final back panel piece. Especially check the location of the holes in the side of the film holder and in the back panel piece.
- The last picture shows the five parts that need painting on both sides. These are the rest of the pieces to make the film holder.
If you want to finish the wood on your complete camera with Danish oil or varnish it is worth lightly sanding the external faces of the camera now. It's harder to get a smooth finish if you leave all the sanding until the small pieces are fixed in place. Light sanding with 600 grid paper along the grain is all that is needed,
Step 3: Make the Small Parts
Now you are ready to assemble the four small parts. The image shows all the pieces you need (on the left) and the completed part (on the right) Starting from the top these parts are;
- The winding knob
- The winding key housing
- The lens cap
- The lens hood
The two largest rings and the disk with the Huffee design make the lens cap. Carefully glue all three parts together making sure to align them as closely as possible.
The two medium sized rings are the lens hood, again carefully glue them together.
The smallest rings make the housing for the winding key. Glue one of the two small circles and the disk with the hole in together. Keep the other small ring separate for now.
Next make the winding knob by gluing the five wavy edged pieces together in the order shown.
When they are all dry check that they fit together. The lens hood should be a snug fit inside the lens cap, if it feels loose add another coat of paint to the inside of the lens cap.
The winding knob should turn freely on the housing for the winding key. You will probably need to lightly sand the winding key housing to get smooth movement. You should also sand the spare small ring to match too.
Step 4: Make the Small Parts II
Now is a good time to make the back cover for the camera. This is made from the three large rectangles with holes in them, the outer one also has two clips to hold the rubber bands. Together with the red cellophane, these holes will form a window that shows the frame numbers printed on the film backing paper.
Glue the two unpainted pieces together using the etched rectangle as a guide. Make sure the two holes are lined up or you wont be able to see how much film you have used.
Then glue the square of red cellophane over the hole on the smaller (inside) piece.
Finally glue the painted back piece over the top of the inside piece to complete the back cover.
The next job in this section is the most fiddly, it's worth fitting the winding key onto the bolt to cut a thread before you finally assemble the winding knob. You will need the winding key housing, the 3d printed part, the M4 nut and bolt and the spring.
First put the nut into the hexagonal cut out on the inside of the winding knob, a little dab of glue helps.
Then thread the bolt through the winding knob, from the outside, and tighten it against the nut.
Thread the winding key housing onto the bolt, to fit in the space inside the winding knob, next thread the spring on top.
Finally push the 3d printed winding key onto the end of the bolt and tighten it onto the bolt. A vice and a spanner are very handy to help get this piece tightened and square. Again a little dab of glue isn't a bad idea, but be careful not to glue the moving parts together.
Step 5: Build the Film Holder
Cut two 90mm lengths of bamboo skewer. These are the axles for the film rollers, they fit in the holes at the back of the film holder. Depending on the size of your skewer you might need to sand the ends to a slight taper, they should be a tight fit. You will also need the two lengths of metal tubing.
The laser cut pieces for the film holder are;
- Four brackets
- Two baffles
- Two side pieces
- Front piece
- Two film guides
It's worth putting all the bits together without glue first to see how it fits. It's important to make sure you get the hole for the winding key in the right place and on the right side. This part slides inside the camera case, it's designed to be a snug fit. So take time to make sure you fit all the pieces tightly together with no gaps.
First glue the brackets to the baffles, there are two of these parts to make. Make sure the unpainted sides of the brackets are all facing outwards.
Making sure the winding key hole is in the right place, glue the brackets to the side of the film holder.
Glue the skewers into the holes on this side.
Slide the metal tubes over the skewers, these are rollers to hold the film.
Glue the other side to the two baffles, making sure the skewers are in place in the two holes.
Glue on the front panel and fit the two film guides into the slots inside the film holder
.
Step 6: Make a Pinhole
Now to make the most important part of the camera, the pinhole. This can be any tiny hole in any material. The thinner the material and the rounder the hole the sharper your photographs will be. Drink cans are a good source of thin material to get started. I generally use sheet pewter I found in a craft suppliers, it's softer so easier to get a round hole. You only need a small square of material, enough to cover the hole in the front piece of the case.
For this camera the optimal diameter of the hole is 0.42mm (somewhere close is fine!). There is a useful calculator at http://www.mrpinhole.com/calcpinh.php if you want to make a different sized camera.
One way to make the hole is to carefully mount a pin on the rubber on the end of a pencil. Use this tool to push a hole into the material. (try to be straighter than I was in this picture, it's easier if you are not holding a camera!) Do this gradually, pushing the pin a little way in to make a dimple and then turning the material over and sanding it. Repeat this process until you are happy you've got a good sized hole and sanded off any jagged edges.
Another option is to use wire gauge drill bits, you can be a lot more accurate with the size of the pinhole. Again it's a good idea to sand both sides of the material to remove jagged edges.
There is more information on these processes at http://www.kodak.com/ek/US/en/Pinhole_Camera.htm
You can buy ready cut pinholes if you want to be really accurate, but why build your own camera and not make the most important bit? It's not hard to do and it doesn't have to be accurate, just use shorter exposure times for bigger holes.
Pinhole photography is about experimenting, trying different pinholes is all part of the process.
So that you can change your 'lens' use masking tape to fix the pinhole over the centre of the hole in the camera case. I normally colour these in with black marker pen, but have left them white here so you can see that the tape covers all the edges of the pinhole material.
Step 7: Build the Camera Body
Nearly done, at the end of this step your camera will be ready to use.
The first step is to glue the five main camera case pieces together, in the order shown in the first image. Just like with the film holder it's important to take your time and get a good tight fit. Start by fitting the two side pieces into the bottom piece, then add the top and finally the front panel.
Gaps in the camera case as big or bigger than your pinhole will mean it won't work properly, so accuracy is really important here. If you've got them use clamps to hold the box together while the glue dries. This is especially useful if any of your pieces are slightly bowed.
When the glue has dried hold the camera case up to a bright light source and check every join from the inside. If you can see any light getting through little gaps repaint the joints on the inside of the camera until it is completely light tight.
The last job is to fix the smaller parts to the camera case.
Glue the lens hood in place, using the etched circles on the front panel as a guide.
Fix the single ring left from making the winding key housing around the hole in the side panel of the camera case. When this has dried carefully glue the rest of the winding key housing to this ring. Make sure the winding knob can turn freely, be careful not to glue the winding knob to the winding housing.
This camera has two tripod mounts, one for portrait and one for landscape. Both are made of two pieces and one of the 1/4 -20 UNC nuts. Glue them in place using the etched guide marks. The bottom tripod mount is also a clip to hold the elastic bands in place, hook one under each side.
Pull the winding key out and then slide the film holder into the camera case. Let go of the winding knob and the spring will push the key into the film holder. Push the back piece in place and hold it closed with the elastic bands.
That's it! You've made a camera.
Step 8: Take Photographs!
Just add film and you are ready to start taking photographs.
You can load film anywhere, but it's best to be out of direct light if you can. The full spool of film slots in the holder without the hole for the winding key. Wrap the film around the two rollers, only let out as much backing paper as you need. Slot the backing paper through the empty (take up) spool and wind a few turns to lock the paper. Put the take up spool into the other holder.
When you have put film into the holder, pull out the winding knob and slide it into the camera. Make sure the hole in the film holder for the winding key is on the right side. Wind the knob anticlockwise (see arrow on winding knob) until you can see a '1' in the red window.
There is a more detailed explanation of this here
http://www.huffee.com/using/loading-film/
To take a picture remove the lens cap for as long as you want to expose the film and then replace it. Depending on the size of your pinhole exposure times for 100 iso film will be approximately;
- Bright Sunlight - 8-12 seconds
- Overcast - 12-16 seconds
- Shadow - 16 - 30 seconds
- Indoors - Anywhere between ten minutes and half an hour. (The picture above of DoES Tower was taken indoors at Liverpool Make Fest and took 15 minutes.)
Black and white film is very forgiving so just get out and experiment, it won't take long to learn what a good exposure time is for your particular camera.
After each exposure wind the knob anti clockwise, watching through the red window for the next frame number.
You might decide to cover the window with a piece of tape you only remove when you're winding the film on. Otherwise there is a danger of burning the frame number onto the film, you can see a faint 8 in the top right of the DoES Tower picture.
You can use the diagonal marks on the top and side of the camera as a rough view finder. Imagine the lines projecting into the scene you are photographing, showing the middle and edges of your final image.
There is more information about the camera and how to use it here.
(I'm working on the blog..)
If you have a go at making one it'd be great to see how you get on, and what pictures you take!
I'll post updates at @huffeecamera and my next instructable here. Imagine what I could come up with if I had my own Epilog Zing to experiment with... ;)
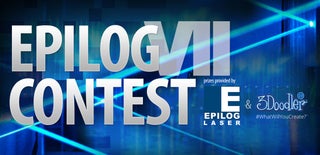
First Prize in the
Epilog Contest VII