Introduction: Making Biodiesel From Waste Vegetable Oil
Maybe if Walt and Jesse had taken to making biodiesel rather than methamphetamine they would have had less trouble with the Mexican cartels, less murders and violence and an altogether easier life? Also a lot more environmentally friendly! There have however been some moments of excitement in my biodiesel career - on one occasion I was raided and interrogated by the Feds on suspicion of processing 'red' diesel into 'white', but fortunately they went away happy that I was innocent.
When I watched Breaking Bad there were quite a few actual similarities like, for example, always being wanting to perfect the product and taking a great pride in it. Some of the machinery in their industrial production plant looked a bit weird and unfortunately there was not enough pipework for it to actually work. It does however give some insight into what it is like to work with chemicals and in many ways making diesel (biodiesel) is a mysterious business and more akin to alchemy than science.
Biodiesel made from waste vegetable oil is possibly one of the most environmentally friendly fuels available for road vehicles. Yes, the methanol used is derived from petroleum but once it is reclaimed from the glycerol bi-product it's use is only at 14% by volume. It's not 100% carbon neutral, but goes a long way to help prevent climate change. A big bonus is that it is made from a waste product, which gives it a lot of extra points on the eco-friendly scale. Using new vegetable oil sometimes can have some negative consequences such as the destruction of natural environments by planting palm oil trees or competition with local food crops in countries such as Mexico, pushing up food prices. Please check the source when processing new vegetable oil!
Essentially, biodiesel is vegetable oil that has been broken down with chemicals to reduce it's viscosity thus making it spray out of a diesel injector nozzle with finer particles, making it easier and cleaner to combust. The main reaction takes place with methanol, which is a type of alcohol, in the presence of a strong hydroxide catalyst such as sodium hydroxide. Although the reaction itself is fairly simple, there are many steps in the process that involve heating, mixing, neutralisation, washing, drying and filtration. Waste oil presents it's own challenges - it's more tricky to process than new oil, but with good techniques devised over a ten year period we have 'cracked' it!
This instructable is a video based step by step of a training course but can not be thought of as a substitute for proper hands on training. Please do not attempt to make biodiesel without such training.
Difficulty: | .......... | Training required |
Cost: | .......... | Starts at £2500 |
Satisfaction: | .......... | |
Hazards: | .......... | See next step |
Step 1: Health and Safety
There are considerable health and safety implications when making biodiesel. Some of the chemicals are extremely hazardous, explosive and inflammable. Never make biodiesel in your house or even in the garage unless it is separated from the house by at least 30 metres. If something goes wrong in your garage you may have a small fire which escalates to a large fire as other things in the garage start to burn and if your garage is connected to your house it could well burn your house down and harm those within it. Here's a run down of the individual hazards:
- Methanol is flammable, burns with an invisible flame, it's vapor is explosive and it has a cumulative poisoning effect on the central nervous system.
- Sodium hydroxide is caustic and will dissolve flesh when mixed with water. Wear gloves and goggles at all times when handling.
- Sulphuric acid is extremely corrosive and will dissolve flesh and metal. It will also cause an explosion if water is added to it's concentrated form. Always add acid to water, never the other way round. Never use containers greater than 2 litres as they are too difficult to decant. Always wash jugs and measuring cylinders in water immediately after use as it's easy to forget.
- Sodium methoxide is the chemical formed when sodium hydroxide is added to methanol. It has all the characteristics of methanol and sodium hydroxide so gloves and goggles are essential.
- Vegetable oil is a slip hazard on the floor. Use sawdust to keep the floor slip free. Waste vegetable may be a bio-hazard if vermin such as rats have been near it. Rats carry many serious diseases which may be transmitted by their urine.
- Chemicals need to be stored in locked cabinets according to local laws. Sulphuric acid must be stored separately from sodium hydroxide.
- No smoking signs, no mobile phones signs etc need to be in place.
- Fire extinguishers and eye wash kits are required.
- Ensure that there is good ventilation in the building. Low roofed buildings are not suitable.
Step 2: Legal
The main legal implications are listed below but will be dependant on which country/state you live in so check your local laws.
- Storage of methanol - consult your local fire department
- Other fire regulations when processing oil and methanol - as above.
- Employment of personnel - consult your local health and safety unit regarding using hazardous substances.
- Tax - consult your local government tax office for taxes payable.
- Delivery of chemicals - sometimes chemicals may not be transported in your own vehicle or delivered to a residential address.
- Other laws particular to your country/state.
- Environment protection authority
Step 3: Equipment and Chemicals Required
Equipment:
- Biodiesel processor eg. TT700A. For safe operation the mixer tank should be separate from the heating tank and the heating tank must have level switch cut outs and thermostats installed.
- Methoxide mixer
- IBC's x 10 of
- 14 cfm compressor
- Electricity supply
- Water supply
- Drain to the sewerage system
- Titration kit (see next step)
- Large funnel
- 10kg weighing machine
- Personal health and safety equipment (goggles, gloves masks etc.)
- Fire extinguishers
- Eye wash kit
- Sawdust for spillages
- Pipe work
- 100 ml plastic measuring cylinder
- 500 ml ml plastic measuring cylinder
- 1 litre plastic measuring jugs x 3
- Mason / kilner jars x 5 of
- Kettle for heating oil
- Work bench for testing oils and samples
- Plate and frame filter machine
- Methanol storage facility
- Chemical storage cabinets
- Extraction fan and hood over the heating tank
Chemicals:
- 2 litre bottles of concentrated sulphuric acid x1
- Industrial grade methanol 200 litres
- Industrial grade sodium hydroxide 25 kg
- Waste vegetable oil 1000 litres
Step 4: Titrating the Vegetable Oil
Waste vegetable oil is commonly used for producing biodiesel and becomes degraded during the cooking process into it's constituent fatty acids. This can also happen with new oil if the raw seeds have not been stored properly. The acidity can not be measured with a pH meter or litmus paper as it is not an aqueous solution and so the titration method must be used.
Equipment required:
- 50mm conical flask
- 10mm pipette
- Rubber pipette filler
- 10mm disposable syringes
- 1mm disposable syringes
- 10ml pH bromothymol indicator solution
- 500ml 0.025M sodium hydroxide solution (1g/L)
- 500ml Isopropanol
Instructions:
Add 1ml of oil to the flask and then 10ml of Isopropanol using the syringes and then 3 drops of the indicator solution. Whilst stirring the solution add the sodium hydroxide one drop at a time using the pipette until the indicator solution changes from yellow to green. Keep adding the drops until the green colour is maintained for at least 15 seconds. The amount of hydroxide used will be the final reading minus the initial reading, in ml.
If your amount of hydroxide used = x (ml) and the quantity of oil to process is y (litres), then the amount of solid sodium hydroxide required should be:
z = (x + 3.5) * y grams per litre.
For example, if the titration reading was 3.0 ml, then z will be 6.5 grams of sodium hydroxide per litre of oil.
Step 5: Mixing the Methoxide
We are planning to make a 700 litre batch and so need to make a quick calculation to get the quantities of sodium hydroxide and methanol. From the previous step we arrived at z = 6.5g grams per litre. Now the amount of sodium hydroxide will be z x 700:
s = 6.5 x 700 = 4550 grams = 4.5 kg of sodium hydroxide
The methanol required is normally 20% by volume of the oil although, with experience, this can be reduced slightly to save cost. Here is the methanol calculation:
m = 700 x 0.2 = 140 litres of methanol
So we now add 140 litres of methanol to the methoxide mixer and then pour in 4.5 kg of sodium hydroxide and stir for 5 to 10 minutes or until the granules can not be heard whizzing around inside.
Step 6: Making a Mini Batch
Equipment required:
- 1 litre mason / kilner jars
- 100 ml plastic measuring cylinder
- 500 ml plastic measuring cylinder
- Kettle
- Stirring rod
- Plastic 1 litre measuring jugs
The titration that we did in step 1 is a really good indication of how much chemicals to use to get a good biodiesel reaction, but it is not fool proof. Sometimes, with waste oil, there can be all kinds of weird contaminants that the titration test wont pick up on, so just to be on the safe side we test the oil once more by making a mini batch in a mason jar watching very carefully how quickly the black coloured glycerol separates out.
The process involves taking a 100ml sample from the methoxide mixer and a 500ml sample from the hot oil tank and mixing them together in a 1 litre mason jar. If the solution gets cold then it can be quickly heated in a kettle for about 5 seconds and poured back into the jar. If anything unusual is noticed in the next few minutes then the oil in the heating tank can be discarded before being pumped into the mixing tank, thus saving time and chemicals.
Step 7: Drain the Water / Gunge From the Heating Tank
The filling and heating of the vegetable oil is NOT shown in these instructions so we are starting from the point where the left hand tank, the heating tank, has about 750 litres of hot oil in it. After it reaches about 70 degrees C, the level in the tank needs to be brought down to 700 litres and the water and 'rubbish' that falls to the bottom of the cone is flushed out. This is particularly important when processing waste vegetable oil as there is often a certain amount of water etc. in the oil. It is of crucial importance that water is not accidentally pumped across to the mixing tank on the right hand side in the mixing / reaction stage as water will spoil the reaction and reduce the overall yield.
The level of fluid in the tanks is indicated by a sight tube running down the inner sides. This system is NOT fool proof as sometimes the tubes can become blocked or give false readings due to a difference in density of the fluid in the sight tube and the fluid in the tank itself. Believe me this happens, so watch out! The efficiency of the sight tubes can be improved by only opening the sight tube valve at the bottom when necessary, so preventing unwanted contamination entering the tube. A marker made by wrapping a cable tie around the tube is located at the 700 litre level point.
Step 8: Check for Contamination in the Mixer Tank
It's really easy to get water left over from the previous batch lurking in the bottom of the right hand mixer tank, so drain off any water by opening the bottom valve with a pipe connected to remove the residue. Never short cut this step as water will seriously affect the main biodiesel reaction.
Step 9: The Primary Biodiesel Reaction
The methoxide is now pumped out of the methoxide mixer into the right hand mixer tank with the sight tube valve remaining closed to prevent contamination. Then the hot oil is pumped onto the methoxide and simultaneously mixed. Never pump the hot oil in first as methanol can boil off the top of the oil if the oil is hotter than 64 degrees C. Another advantage of this technique is that the mixing is much more efficient than trying to mix a whole tank load of reactants and normally only needs 10 minutes of actual mixing time.
As the hot oil is pumped into the mixer tank, the temperature can be seen to slowly rise. If it gets to 64 degrees C then the pump needs to be switched off until the temperature has dropped down a few degrees, after which it can be turned on again. With practise it is possible to get the final temperature of the batch to exactly 64 degrees at the end of one continuous pumping procedure.
Now we take another sample of the contents of the mixer tank whilst it is still mixing to check that we are getting a good reaction. Very quickly we see glycerol separating out in our mason jar and can turn off the mixer system after 10 minutes of mixing the full tank load.
Step 10: The Secondary Biodiesel Reaction
The contents of the mixer tank are left to settle for exactly one hour and the crude glycerol is pumped out from the bottom of the cone until the golden biodiesel can be seen in the pipe work. At this stage the biodiesel is only about 80% pure and needs to be sent through another reaction phase to 'push' the reaction forwards.
The crude biodiesel is processed with 10% by volume of methanol and 1.4g of sodium hydroxide per litre of biodiesel. So for 700 litres of crude biodiesel the chemicals required are:
m = 0.1 x 700 = 70 litres of methanol
s = 1.4 x 700 = 1000 grams of sodium hydroxide
These ingredients are mixed in the methoxide mixer in exactly the same way as before but this time they are pumped INTO the mixer on top of the crude biodiesel. The reactants are now mixed for 10 seconds and allowed to settle for about ten minutes before draining off any glycerol that has settled to the bottom. Sometimes there is none at all!
An alternative method is not to perform the secondary reaction, but to allow the reactants from the primary reaction to stand for 3 days, during which time the reaction proceeds at a very slow rate as glycerol continues to settle out. (This method is not used so much these days).
Step 11: Acid Washing the Crude Biodiesel
In this stage dilute sulphuric acid is used to neutralise the residual sodium hydroxide in the mixer tank making it easier to wash the biodiesel in the next stage. If the catalyst is not neutralised it will tend to form soapy emulsions with some of the co-products when water is added. The amount of concentrated sulphuric acid required for 700 litres of crude biodiesel is calculated as follows:
a = 700 / 2.3 = 300 ml of concentrated suphuric acid
This is then carefully poured into a drum of 25 litres of water. Full personal protection equipment is required at this stage as the concentrated acid is extremely corrosive. Never try to use acid in large containers as they are too difficult to handle - a 2 litre container is the maximum.
The diluted acid is now slowly pumped through the spray nozzle in the mixer tank until the drum is empty. Much of the acid will fall straight to the bottom of the cone so it's a good idea to recycle it back through the spray nozzle to get more efficiency from the acid. This is done for about 5 minutes, watching carefully what the fluids look like as they exit the cone pipe work. If biodiesel starts to come through, the air operated diaphragm pump needs to be slowed down.
Step 12: Water Washing the Biodiesel
Water is now used to wash out all the residual chemicals and glycerol in the crude biodiesel. Great care needs to be taken to prevent emulsions of water with the diesel, particularly if the original feed stock had a high fatty acid (FFA) value in the titration stage.
The valve on the sight tube is now opened and water is sprayed in through the spray nozzle in the mixer tank using mains pressure - about 2 bar. The dirty water is simultaneously drained off from the bottom of the cone, taking care not to drain off too much and get into the biodiesel layer. In any case, the water is always drained into an IBC so as to catch any biodiesel that gets through by mistake. (IBC = intermediate bulk container).
Normally about 400 litres of water is required for a 700 litre batch, but this could be more if the vegetable oil was of high FFA. The trick is to keep looking at the colour and consistency of the waste water coming out. The flow of water going in is regulated using the ball lever at the top of the main in such a way that it balances the flow of waste water coming out. This is a bit of an art and is aided by looking at the sight tube, checking that the level is not too high or too low and checking the waste water coming out. The whole process normally takes about 1 hour.
Step 13: Draining Off Residual Water
Now the contents of the mixer are allowed to stand for about 60 minutes to allow any residual water to settle out to the bottom of the cone. The more time given to this stage of the drying process, the less time required in the heating tank so it is a bit of a balancing act here.
The residual water is now drained off and the wet biodiesel is pumped back over to the heating tank for the final drying stage. It's a really good idea to allow the wet biodiesel to flow by gravity as much as possible and only use the pump when the levels in the two tanks have equalised - this will prevent any droplets of water hanging about on the mixer tank walls from emulsifying in the diaphragm pump due to it's aggressive action. Once the mixer tank is empty, the heating tank elements can be turned on and left to heat to about 70 degrees C. At this temperature most of the dissolved water will separate out and fall to the bottom of the cone. However, there is still a very small amount of water dissolved in the biodiesel and this needs to be removed by spray drying. At this stage, residual water in the cone must be removed as otherwise it will be picked up by the circulating pump and ruin the effectiveness of the drying stage.
Step 14: Drying the Biodiesel
The hot biodiesel is now sprayed back on top of itself using the electric centrifugal pump at the bottom and spray nozzle in the top of the tank. An overhead hood type extractor fan removes any fumes from the work area. This part of the process normally takes about 15 minutes and the effectiveness of the drying can be observed by watching the temperature of the tank contents. If the temperature is falling it means that the biodiesel is still wet, if it starts to rise then it is dry. Now samples from the heating tank can be taken and the process is finished when the sample stays bright and clear at room temperature.
If the electric circulating pump is turned on and the flow seems to be restricted, there is probably a blockage in the brass filter unit located upstream of the pump. It has a gauze that protects the pump from damage and can be removed, cleaned and replaced.
Step 15: Filtering the Biodiesel
Finally, the biodiesel needs to be filtered before using in a vehicle. The best type of filter machines are the frame and plate type which have a very low running cost and massive capacity for removing particles. Cartridge filters can also be used but they will be expensive to use in the long run as they will block up fairly quickly. The cartridges themselves would need to be rigid enough to sustain high pressures and normal water cartridges are not suitable. ProBond filters are the ones to go for. The biodiesel is left to stand for about 3 days, by which time any wax that wants to form will appear as a wispy haze in the sample jar. If a diaphragm pump is used, this waxy biodiesel can be pumped through a frame and plate filter without breaking up the wax too much.
Now that you have a quantity of finished biodiesel you will need to blend it with diesel according to the ambient temperatures and your vehicle warranty. Some people just go ahead and use it 100% with no problems but there are definitely issues with vehicles with a DPF (diesel particulate filter) fitted. Biodiesel is not compatible with the DPF as it does not ignite in the unit as it is supposed to and the unit then becomes broken, at considerable expense to the owner. Even filtered biodiesel will go waxy at low temperatures, depending on the nature of the vegetable oil originally used. Typically, it will start to wax at about 5 degrees C so will need to be blended with diesel to prevent the vehicle fuel filter from becoming blocked.
Step 16: Play All the Videos in Order
If you've got 77 minutes to kill, you can watch the whole training session here in one go.
If you enjoyed this Instructable, please vote generously. Thank you.
PS. An oscilloscope would be really useful for my electronic projects.
Please Vote Generously! | ![]() | Voting will help save the planet |
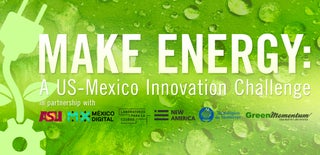
Third Prize in the
MAKE ENERGY: A US-Mexico Innovation Challenge