Introduction: Making Kukri Style Bowie Knife
In this Instructables, I am going to show you how to make a kukri style bowie knife. From past couple of months, I am watching forge in fire and that show motivate me in knife making. I am also a huge fan of kukri knives that's why I give bowie knife a little bit touch of a kukri. I don't know why I always fail in my first attempt. In my last Instructables I fail in my first attempt then I slightly modified my design same thing happened to me in this build also but the problem is that I am not able to correct my fault and the complete project ruins and my 5 days of effort gone in vain. There are a couple of reasons why my knife broke and the major reason is choosing water for quenching process that was my one of the biggest mistake. Because of that there so much cracks formed in my knife. The second reason is the edge of the blade since I don't have belt grinder that's why I am worried about the sharpening process in the beginning of the build and made the edge shape before quenching and leads to warp edge. Even if it survived the quenching process than because of edge warping of the knife my project also went in vain. Because of that warping when I am going to correct my mistake by holding it into the vice the blade cracks from multiple places. The vine work which I made on my knife might be a case of those cracks. The Sharp edge of the vine pattern also might be the reason for cracks. But that build taught me a lot and in spite of demotivating it motivate me to build another knife with no mistake and I think I definitely learn a big lesson with those mistakes. The end result is in front of you. I am very much pleased how this knife turned out. If you like my success story than don't go away without leaving your valuable feedback and suggestions. I always felt motivated to read your valuable feedback.
Step 1: Material and Tools Required
Material required:-
Form what I learn from other knifemakers that steel of 1075 to 1095 are good to produce the knives, tool steels are also the good choice and spring steel are also an option for you because of higher carbon content. This is also an ideal material for making knives. That's why I go for this material because I am not able to get the 1095 or 75 steel for my build. Following is the list of material which I used in this build for making my beautiful knife. You can definitely replace the material with any material you want.
1. Spring steel
2. Brass for handle
3. Cooper for handle
4. Brazilian Ipe wood
5. Glow in dark casting.
6. Micarta
7. Mosaic pins( you can replace them with rivets if you don't have because they come quite expensive)
(Make your OWN Custom Mosaic pins for Knife Handle)
8. Two part epoxy
9. Sandpaper from size 60, 80, 120, 150, 220, 320, 400, 600 and then with 1000 grit.
10. Buffing compound.
Tools required
Following are the list of tools which I used for the knife
making although three is an alternate of every tool so choose tools wisely according to your need. I list all tools which I used.
1. Angle grinder
2. Bench drill
2. Flap wheel
3. Cutting wheel
4. Grinding wheel
5. Buffing wheel
6. Forge (How to build your own coal Forge )
7. Sledgehammer
8. Vise ( it's good to have rotating vice like I have)
9. Anvil( the hammer and anvil required only in that case if you are using not too wide material and going to make a curved knife like I did. Since I didn't get right material that's why I use hammer and anvil to get my desired shape)
10. Needle files
11. Knife filling jig
12. Flat and half round file
13. Flexible scale
Step 2: Forging
Starting of this build by forging a material for my knife design. Since I am not a professional knife maker and even don't have the right place to forge but I start my process by place the metal into my homemade coal forge. This is definitely a learning process for me. I didn't do too much of forging work just a little bending work is done by me in this build and it definitely not that easy which I am thinking of before starting this project but with my effort, I am able to bend the handle side first and then proceed to bend the centre portion. Since my material width is 2” and by bending the metal from the center I am able to get appropriate width for my knife. There is not too much for me to talk about this bending just heat up the material and then strike with the hammer at its far end to produce the bend in it. If warping occurs then place it on the flat area of the anvil and flatten it with the help of the hammer. By repeating this process I am able to get my desired shape.
Step 3: Grinding and Flattening
Once I bend the material to the necessary width I clamped it on my workbench and then with the help of angle grinder remove the scales from the knife. For flattening process, I used the flexible grinding wheel to remove excess of material. I also used flap wheel and this disk wheel to flattening my stock. Since I don't have the belt sander that's why I am using these tools for this operation. The more the size of the wheel the better will be the grinding operation and always use the aggressive grinding wheel for this operation to work faster. After getting the appropriate flatness I move to the design process.
Step 4: Designing the Knife
Since I was thinking of a hybrid of kukri and bowie knife I came with this design. I place the metal on to the piece of paper and then draw its outer boundaries then I design the shape of my knife. Although at that time I am not confident about the design of my handle. The blade design came out is very nice. Then I cut off the template and place it on to the metal and trace the outlines of my knife. The result was in front of you.
Step 5: Cutting the Knife Shape
To cut the knife shape I clamped the piece on to the table and then cut it apart with the help of the cutoff wheel. It's not that difficult. Someplace I also used scouring method in which I scour line repeatedly on the same place and remove the material. At the handle area, I make straight cut repeatedly and made the handle shape. At some place, it's difficult to cut with the grinder that's why I leave that area for the file work. Then I hold the knife in the vice and with the help of grinding wheel carefully grind off the excess material. Then I filled the area where the finger is inserted with the help of round file. Once I get the basic profile of my knife I straight my lines with the help of files. I hold my knife in the knife and continuously filed it with the help of flat file and get a smooth profile of the blade. Then I hold the blade horizontally into the vies and flatten it with the help of files. During that process, I keep checking the knife with the help of straight edge to know that whether I am doing correctly or not. Once I am completely satisfied with the work I proceeded to the next step.
Step 6: Marking the Edge
After flattening the knife I coloured the areas where I am going to mark. First I start marking on the edge of the blade. To leave 1 mm thick edge I choose 5 mm dia drill bit and then place the knife onto the flat surface and marked the area onto the edge. Then I marked the bevel area of the knife and for that, I measure the distance on to my drawing lock my calliper at that position and then scour the bevel onto the knife. By doing this I got marks on each side of the knife. With the help of circle guide, I also draw area at back side of the knife as well.
Step 7: Profiling the Blade
Although there are the bunch of different methods to profile the blade and one of the easiest method is to use the belt grinder. You can also use angle grinder also but you have to be careful while using that. Because it makes the surface uneven and if you made your surface than its quite difficult to reshape your design. The hard method is to use human effort and file down the blade until you get the exact profile of your blade. For that, I made a filling jig to make this work easier. I didn’t invent this jig, there is a person named Gough on youtube who invented this filling jig, by watching that person I made a temporary jig for my own with the help of scraps. For that, you need a T shape wood. The smaller side is the place where you are going to mount the knife and the longer side is that where you insert the eye bolt to guide your file during filling. By tightening or loosening the bolt you are able to adjust your grinding angle. In the image, you can clearly see how this jig is made. Then clamp your file with a pipe which will easily fit into the hole of that eye bolt and start filing your knife. To prevent the knife from any movement I drive a couple of screws to hold it onto its position further going forward I fasten a harden screw so that file will not move further and ruined the shape of my knife. I think if you watch that person you can easily make the jig for your own. Then with the help of that jig, I am able to get a nice profile for my blade. The back side of the knife is quite different for that I filled down that area free hand and achieved the nice-looking edge. By doing this I left with 1 mm thick edge which is good. As you decrease the thickness of the blade the chances of blade warping increases. Then I hold the knife horizontally into the vies and filed the knife in linear motion so that all the scratches diminished and I have cleaned even surface. By doing this it's quite easy to finish your knife without leaving any scratch marks.
Step 8: Spine Work
Once I cleaned up the profile of my blade I proceed to the vine work. Since I am new to knife making and tries it one time on my previous knife which completely destroyed I downloaded an image from the google and use that as a reference. For the reference, I marked quarter inch distance onto the spine of my knife. The distance completely depends upon the thickness of your files. Always make sure to check the thickness of your files before proceeding to the vine work. Once I marked the points I draw a centre line on to the spine I also draw reference mark on either side of the knife so that I do not file down below that line. As starting of the pattern I start with the triangular file to mark the deep grooved into the spine by leaving every other mark untouched and repeat this process for other side as well as shown in the reference image. I am filing this slightly at an angle and then by following the guide in the image I able to get vine type pattern on the spine of my knife.
Step 9: Making the Composite Handle
Once I completed making vine pattern on my knife spine I proceeded to make the handle for my knife. I am doing this in early stage because the handle I am going to make for my knife is slightly complex and I am going to install the mosaic pins in each section of that handle. For the handle, I choose a bunch of different types of material like brass copper Brazilian ipe wood and glow in dark castings. I also use homemade micarta to provide strength to the individual pieces. The glow in dark castings made by me already for my previous knife. For that, I make some mould out of ply and then mix 2 part polyurethane resin and edit some glow in dark resin and filled the blanks with the resin. Once the resin cures I remove it out of the mould and then send it everything up to 120 grit.
The same thing has been done with the micarta as well. For that I choose cotton cloth cut them into required size and then stack them together by pouring resin on to each layer and then press them with the help of clamps so that it will form a compact shape material. Unfortunately, I didn't record this process but it's quiet and easy process to make. There are a bunch of videos with the help of which you may know how to make micarta easily. Then I draw the layout of my handle onto a piece of paper and then design the handle on to that. In my handle design, the parts are going to attach with each other at an angle of 15 degrees which I marked onto the paper and lay the brass over that template and mark the portion which I needed to cut to form the handle for my knife. I also cut down some pieces of copper as well.
Then I start cutting the piece of Brazilian wood on to the mitre saw. There are two angles in the design and it's quite difficult to achieve those angel free hand. First I taper one side at an angle of 15 degrees then I set both angles horizontal and vertical of the mitre saw at 15 degrees and made the second cut. During the working on the mitre saw always make sure to clamp securely your material. I repeat the process multiple times and cut 4 pieces. During the cutting process when my stock size decreases I glued it onto a Scrap piece of ply with the help of hot glue and then made the cut on my mitre saw. Then I cut 5 pieces of glow in dark casting for one side. Once I have all material cut out I mix two-part epoxy, glue everything with that and clamped it securely. Once the glue dries I sand off everything up to 60 grit Sandpaper. Then I sand both angles of my mitre saw at an angle of 15 degrees. I also clamped those casting blanks on to scrap piece of ply because it's quite difficult to make a cut on to mitre saw with those small pieces. Before making my final cut I made a cut on the test piece and fit it into the drawing I made. Once I satisfied with the cut I perform it on the main material. Here you can clearly see both the angles onto the casting blanks. Then I glued both pieces with the casting blank with two-part epoxy resin and clamped it on to the table. Always make sure that you have flat surface while clamping this kind of stuff. Once the black has been the cure I remove it and sanded off everything up to 60 grit Sandpaper.
Step 10: Making the Handle Shape
Once I completed making the handle for my knife I stick them together with the help of double-sided tape and trace the handle shape onto the handle material. Once I got the required shape I hold the material into the vice and start shaping it with the help of die grinder. Once I got the exact shape of the handle a drill 4 mm holes into each section of that handle and then with the help of centre punch transfer those holes onto my knife. I drilled 4 mm holes in the handle because the diameter of the centre punch Is also 4 mm. Once I marked the exact location of the holes I move onto my drill press and start drilling holes with the help of carbide drill bit. It's always easy to drill holes before quenching process because once the material Harden you are not able to drill holes in your knife. Then I enlarge the holes with 10 mm drill bit because the pins I am using to hold the knife having the same diameter. To decrease the weight of my knife I also drill a couple of holes into the handle portion. And this process really works great in reducing the weight of your knife. Once I drilled all the holes I counter all of them to avoid any stress formation during the quenching process.
Step 11: Quenching and Tempering the Knife.
For quenching the knife I lighten up my Forge and insert my knife into the fire pit to heat it up. Once it becomes red hot I check it with the help of magnet stick whether it's ready for the quenching or not. Always make sure that when your blade becomes demagnetize that is the right temperature to quench your blade with the oil. One thing I definitely want to suggest you that always prefer to use bigger magnet which tells you better about the magnetized state of the material. Then I dip The Blade into the quenching oil. To minimise the walking in the Blade I entered the knife into the oil from Spine because when you dip the knife into the oil the thinner portion gets cool down earlier than the thicker one. And because of that the chances of warping The Blade increases. Hair you can see there is no warping occur into my blade. And to know the quenching I use the file to file down the knife. And at that time I am not able to file my knife which means that my knife gets harden with this process without any interruption.
Once the knife has been changed I prepare it for the tempering process. For that, I placed it onto my forge slightly higher so that less amount of heat reaches to the blade. Then I kept changing the position of The Blade and temper my blade for about 45 minutes. Off camera, I also check the tempering by hitting the knife on to the mild steel pipe and it makes a dent in the surface and blade didn't crack which is a good sign.
Step 12: Finishing the Knife
After quenching and tempering process I hold the knife in the vice and start cleaning of those scales by sending it with the help of 60 grit Sandpaper. If anybody knows how to minimise the scale formation then definitely post the comment in the comment section below. Once I clean up the knife with 60 grit I proceeded dry sanding up to 120 grit. Then up to 1000 grit, I do the wet sanding and bring the knife to the finished state. I also cleaned the handle portion of the knife as well but don't go with too much finish. I kept it lightly rough so that epoxy will make a better Bond with the handle. With the help of drill machine, I also cleaned up the vine pattern of the knife as well up to 1000 grit.
Step 13: Attaching Handle to the Knife
After cleaning up all the mass produced during the quenching process I proceed on to the handle work. For that, I first reducing the weight of the handle by drilling partial holes into the brass pieces. It slightly works for me by reducing the weight to some extent. Then to increase the stability of those pieces I glued the handle to the micarta which I made. Then with the help of coping saw I separate them apart and remove the extra material with the help of files and some other tools. After glueing that fibre material to the knife handle the overall build of the handle looks quite study. Then I drill the holes by placing knife onto the handle and drill 10 mm holes into the handle blanks. To keep the handle at its position I use the mosaic pins so that they hold up the handle to the exact position during the drilling process. Where's the hole has been drilled out? Then I reshape the handle blanks. Then I shape the front portion of the handle because once it attached to the knife is quite difficult to reshape that portion of the handle. This makes the design look more beautiful as well. You can choose any type of design for your knife handle. Also by shaping this portion, I reduce the weight of the knife handle to some extent. Then I cut the mosaic pins with the help of hacksaw. Then with the help of two-part epoxy, I glued the handle with the knife and also inserted the mosaic pins into the knife handle as well. Then I clamped it securely and wipe off the excess glue squeeze out in the front portion of the handle with the help of acetone.
Step 14: Shaping the Handle
Then I hold the knife in the vice and sand off all the excess glue with the help of angle grinder. once the handle has been finished I mark the point Onto a piece of paper which is equal to the thickness of the knife handle. Then I cut that strip and fold it from the centre and then draw a shape onto it. Then I cut the template out of that strip. Once I got the template I laid it on the knife handle and start tracing the outline. Make sure to centralise your template on to the handle. I repeat the same process on the bottom side of the handle as well. Then I start reshaping the handle according to the marking and made the comfortable design. For the reshaping of my knife, I used a die grinder and needle files for this process. Once I got the desired shape of the handle I start finishing the handle by removing the scratch marks. I sand off everything up to 1000 grit to remove all the deep scratches.
Step 15: Buffing and Finishing the Knife.
Then with the help of angle grinder buffing wheel and buffing compound I clean up define marks and bring the knife to a mirror like finish. Here I am using this Potentiometer To vary the speed of my angle grinder. Because it's not safe to use grinder with its full speed onto knife. Although there are a bunch of options you can proceed any of your choice. I go with angle grinder because I don't have any other option to do this process.
Step 16: Sharpening the Blade Edge.
Once I finish The Blade I cover the surface with the help of masking tape so that no scratch produce during the sharpening process. To sharpen the edge I choose 800 grit wet sending stone. Then I drag the edge on to the stone to profile the edge. For one side I do this process 10 times then repeat this process with the other side. By doing this I get equal amount of edging on each side of my knife. This is one cycle of the sharpening process. Then I repeat this cycle about 12 to 15 times. Then I get sharp edge on my knife. To increase more sharpness of the blade I use backside of my Leather belt and charge it with the buffing compound. Then I do 30 cycles for each side and by doing this my life start cutting the paper quite easily. It seems to look a quite difficult process for sharpening The Blade but I think by practicing you get master in this technique. The only disadvantage of this process is that you get slightly uneven edge on your knife.
Step 17: Finally
If you like this build than don't forget to leave your valuable feedback in the comment section.
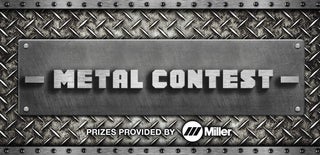
Second Prize in the
Metal Contest 2017
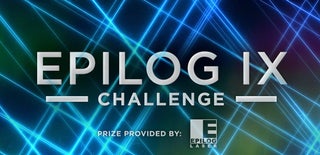
Participated in the
Epilog Challenge 9
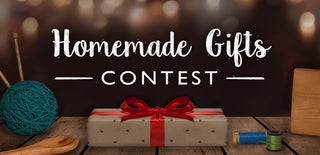
Participated in the
Homemade Gifts Contest 2017