Introduction: Mobile Coal Forge Build
Hello and a warm welcome to all Instructables community. In this instructable, I am going to show you a simple blacksmith coal forge. After being inspired from forged in the fire my interest begins in knife making as well. That's why I build this coal forge. Although I wanted to build propane forge but the fuel cost is more than the coal. So that's why I stick to coal forge. Although I didn't know how much time taken by propane forge to heat 7 mm thick and 2" wide spring steel but my forge heats that piece under two minutes. If anyone here working on propane forge than definitely tells me about that weather my coal forge taking much time or not. The overall expenditure to build this forge is around $82.
If you like this instructable then definitely tells your opinion, because they are more valuable. If you didn’t get anything then toss me a message in the comment section. I always feel happy to help you guys.
Step 1: Material and Tools Used.
Material used:-
here is the list of material which I used in this build. I highly recommend using Proper fitting for your blower and the fire pit. You can also use the flexible metal pipe. Also If you don't want to lined your forge with refractory cement then I highly recommend to use a thick metal plate, I think 1/2" thick plate for the fire pit should be more than enough but even then I suggest you to cover the area around the pit to avoid any miss happening. After lining of cement in my forge the walls of the pit didn't hot. I think If I do a long run that may be some effect would take place. But still, everything works fine for me because I am not lightening up my forge every day.
Always use proper fittings for your blower. I wrote what I use for my build because it wasn't available to me.
- 1.5" X 1.5" square pipe
- 1" X 1" square pipe
- 4 mm thick mild steel plate(I buy it little big for my future builds)
- 3" long door hinge
- 2" wide mild steel flat bar
- Refractory cement for casting.
- 2" dia stainless steel pipe
- 2" dia 2 stainless steel bends
- Blower
- PVC reducer
- Scrap plywood to make bushings.
- M6 hex bolts with washer and dom nut.
- M5 Allen screws 20 mm long.
Tools used:-
Following are the tools which I used in this build. These are the basic metal working tools. I think if you do metalworking then you definitely have these tools in your workshop.
- ARC welding set
- welding rod Mild steel and Stainless steel
- Angle grinder
- Grinding wheels
- Cutting discs
- Drill machine
- Drill bits
- Tap
- clamps
- Welding magnets
Step 2: Draw the Layout of the Forge Top
So, starting of the forge I cut down the 4mm thick mild steel plate. I lay out my design on this piece of mild steel plate. First, I marked out total area required to build the forge which is 26” X 36”. This is because I include the height of the forge walls as well which is 3” high. Then by marking 3” wall dimension I draw out the inside lay out of my forge Which is approximately 20” X 30”. Once I bend those walls this is the dimension I got. Once I finished the layout of forge I draw the lay out of my fire pit. Since I am going to place it in the centre of the top that’s why I first marked out the centre of the top and then by doing half of my pit size length I marked the dimensions on either side of the top. To draw the Straight line, I used these long set square. These works really well.
Step 3: Cutting Out the Forge Top and Deburring
After doing the layout I start cutting out the forge top. For my first cutting of the top, I Cut it with the help of jigsaw by clamping a piece of straight piece of 1” X 2”. This is the first time I tried jigsaw to cut this heavy metal. And I must say this works really fantastic. By using plenty of oil to make the blade cool and easy to slide during cutting you can easily cut these chunks of metals. But don’t run your jigsaw at high speed otherwise you are going to break the blade. By doing this I got very clean cut which is going to be one of my forge walls. Since I am going to bend these walls to formed my box shape that’s why I have to cut those squares. Once I cut down these squares I cut the centre of my fire pit. The centre part and the squares I am going to use for the further builds in this project.
Once I cut out everything on the top I deburr everything with the help of this flexible grinding wheel. This grinding wheel is generally made to use on stainless steel but they worked brilliantly well on mild steel.
Step 4: Creating the Walls for the Forge
Once I completed deburring I worked on the walls of my forge.i scored the lines over the drawn lines with the help of angle grinder and then bend them inward this is because I don’t want to weld the outside portion of the walls. To scores the lines I also used a thick grinding wheel and with the help of It I am able to bend that sheet and formed the wall for my forge. But this process took a lot more time than I expected. You can use this method if your material thickness is less suppose If you have 16 gauge sheet than you can easily bend that inward to make your desire shape but as the thickness of the sheet increases the difficulty also increases. With this process, I am able to square only one wall out three walls that’s why I decided to tear down rest of the two walls and then weld them at some distance. Here I didn't touch the fourth wall because I think that I can use that portion as a tool holder. Since I didn't have any tool yet for the forging purpose that's why I leave this portion, so that I can modify it according to that tool.
Step 5: Cutting Pieces for the Fire Pit.
Then I draw the layout on a piece of 4 mm thick mild steel plate. I highly recommend using a thick plate to construct the fire pit for yourself. I draw the trapezium shape on the plate.Here I have two types of trapezium one for longer side and other for shorter side.First I draw a straight line on the sheet. Then I marked 15" length which is the longer side of the pit. Then I marked the centre of it and draw perpendicular that. Then on the opposite end of that perpendicular, I marked the distance from the centre to either side of that which is 9" and this is the bottom of my pit.The dimensions of second portions are 8" and 3". The dimension of the bottom of the pit is 9" X 3". Later on, I slightly update the lengths because it seems little longer to me. Then with the help of jigsaw, I cut down the pieces free hand. I must say it very easy to cut complex shapes with jigsaw very easily. Once I cut the pieces I deburr them and then prepare them for the next process.
Step 6: Create the Fire Pit
This is the main part of the coal forge. I first lay the cut-out pieces on to my workbench then I draw L shape with the help of set square onto the ply. Although pit has a pyramid shape and if you draw a line horizontally from the same level they will always meet and are perpendicular to each other. With help of this line, I am able to form the basic shape of my fire pit. Once I weld two individual pieces I draw a complete rectangle onto the ply and then place those pieces over them. The size of the rectangle I have drawn is 3” X 9”. Then I first tack weld and then after satisfying with the shape I complete the weld.
Step 7: Welding the Pit and Creating the Forge Boundaries.
Once I completed making the fire pit I laid it over the forge top and centralize it from all four sides. After double check everything I tack weld the pit to its place so that it will not deform during long weld operation. Even after tacking I didn’t perform long weld. I weld half portion of the one side and then weld the alternate half portion of the other side and completed this task. I also welded the inside portion of the top as well. Once I completed all welds I turned It upside down and weld the walls with the top. For welding these walls I used these welding magnets to hold the plate 90 deg so that I can tack weld and creates the wall. Here I didn’t make the complete weld because it wasn’t really necessary to do that. The gap which is created by scoring the lines onto the plate has been filled with the help of body filler.
Step 8: Creating the Base for the Forge.
Once I created the top for the forge I cut the material for the base. For that, I chose 1 ½” square pipe. Then I cut 4 30” long piece for the legs and 2 Sets of 20” and 30” for the top frame. I also cut down 2 sets of 17” and 27” long piece of 1” square tube which I am going to use as a bottom brace for the main structure. Then I cut out the portion equal to the thickness of the pipe. I do this for only two of them. This is an alternate for the mitre joint. I saw Jimmy Diresta to use these kinds of joints in his build. Then I first tack weld and then recheck everything and then complete my welds. I do the same thing with the legs as well. Then to join the bottom braces I marked 4” above the bottom and then marked the location where I need to weld the brace. Then by holding it with welding magnets I first tack weld and then complete the weld.
Step 9: Making the Air Chamber for the Forge
Then I made the air chamber for my forge I cut out these two pieces but unfortunately, I cut them little big what I actually needed. The main dimension I actually needed is 9” long but I cut down 15” long pieces with is the dimension for the top of the fire pit. I made these pieces slightly tapered so that air come from one end and slightly raise on upward. Then I resize them and weld to the pit. Then I worked on the flange which I am going to connect the pipe to the air chamber. These are the leftover from the top out of which I am going to create flange for my fire pit. For that I first tech weld these two pieces and trace the circle over it with the help of this bend, then centre punch them and drill holes to remove inside material. Then I clean up the hole with files until I get my bend fitted into that hole. Then I drill holes for the joinery and tap them so that I can connect them. After that I grind those Welds so that they can be separated from each other then I marked one side so that I can remember how they are connected to each other. Then I weld the peace with the air chamber. I also close the other end as well with third leftover piece by slightly trimming it down. Then I complete the weld because now it's not going to deflect anywhere. Then I used the fourth leftover piece as door for the chamber. I temporarily weld it with the chamber and then measure the dimension of remaining chamber which is 6” X 3”. Then I deburr the edges and tack weld and then perform the complete welds.
Step 10: Making the Air Delivery System for the Forge.
Once I completed the air chamber I need something with the help of with I can connect the fire pit with the blower but there is a big problem in that. I didn’t find the correct size of bend for my system because steel bends are not available in the size greater than 2”. The size of the blower I am using is 2.5” Dia. First, I slightly chamfer the edges of the pipe. Then I weld the bend with the steel pipe. After that, I place the blower on the braces and roughly measure the distance from the centre of the fire pit to the centre of the blower. Then I draw a line over the pieces of ply and placed my pipe and fitting over there. Then I marked the length which I actually needed. Then I cut that length deburr it and then weld it with the second bend. After that, I grind off the excess weld so that It will lay flat on my workbench and then weld the remaining pipe with that bend. I also weld another flange with the pipe also so that I can connect the delivery system with the fire pit.
Step 11: Wheel Mounting Plate:
For the wheel plate, I draw the layout onto the piece of metal (this is the leftover from the fire pit portion) and cut it with the help of angle grinder. Then I hold all the pieces into the vies and then grind its one side and tack weld that. The same process repeats with other sides as well. Then I lay the caster over this piece and draw the hole location. Then I centre punch the holes and first drill pilot hole and then drill 10 mm dia holes in it so that I can fasten it with the casters. Once I finished this task I welded them with the frame legs.
Step 12: Filling the Gaps With Body Filler
Once I Completed all welds Some of my welds are not good at all that’s why I decided to fill them with the help of this filler so that it looks pleasant to eyes. Once I apply it at every corner I remove the excess material with the help of grinder and scotch wheel to make it smooth for the paint job.
Step 13: Making Ash Dump Door for the Pit.
To make it like a door I used this 3” door hinge and attach it to the door. Make sure that hinge is welded in position when it's completely opened. Then I weld a little space over the hinge so that the counterweight handle has the same level and easy to weld on. Then I took this 2” wide piece of mild steel bar and draw a handle shape over it. Then cut the shape with the help of angle grinder. Then to increase the weight on the far end to keep the door closed I cut the remaining bar in half and then weld it on either side of the handle. I fill it with the thick layer of welding. Then I grind off the excess weld and round off the corners. Then I weld this handle to the door of the pit.
Step 14: Customize the Pvc Fitting for the Blower.
Since I didn’t find the exact fitting for my blower and pipe. What I got is slightly oversize. Then I decided to make these two bushing one for the pipe and other for the blower. I made them out of 3/4" thick plywood by drilling holes with the help of hole saw and for each set, I glued 2 bushings to give it a socket type look. Then I inserted them in the PVC reducer with the help of a hammer and slightly inserted them deeper so that if air leakage occurs i can fill these lips. But luckily this doesn't happen. Here I also counter the inside edge of the smaller bushing to minimize the resistance.
Step 15: Mounting Arrangement for the Blower
Then I worked on the mounting arrangement for the blower. Since I roughly calculate the distance from pit to the blower that’s why the blower is slightly lower than the pipe position then I cut these 1” square pipe and use them as a spacer for my blower. I cut them according to the blower mounting. With the help of these square pieces, I closed both the ends of the spacer pipe as well. Here I also cut a longer piece for the second mounting of the blower. I made I out of 1" X 1" square pipe, then weld it on my stand. Then I placed those spacers on this stand and place my blower onto it. Then I measure the distance I needed to cut the pipe to join it with the blower. Once I cut it, I installed it in the blower and thenHere I also measure the length of air delivery pipe and cut it too so that it can be fitted to the blower.
Step 16: Priming and Painting:
Then I apply a second coat of primer over all area and then apply two coats of orange colour on the frame and black colour on the forge.
Step 17: Assembling
Then I assemble everything. First I installed the caster with the M6 bolt and dom nut. Then I place the blower in its position and marked the hole location, dill and tap them as well. Then I place the forge over the frame. Since I didn’t want to fix it permanently with the frame I fasten it with these self-tapping screws. Then I connect the air assembly with the forge. Then I connect the blower to the pipe.
Here I also made a plate above which the coals are resting. This plate is made by cutting plate slightly greater than the fire pit bottom which is 9" X 3" and drills couple of holes so that sufficient air enters into the pit and keep the forge lighten.
Step 18: First Test Tun:-
After finishes, everything I performed my first test run and the forge heats up the metal very quickly but there is one major flaw and that is the thickness of fire pit. During my first test the two walls of the pit turned into a yellow colour within a couple of minutes and if I didn't pay attention towards that then possibly I will damage my fire pit. That’s why I decided to lined it with refractory cement.
Step 19: Laying Refractory Cement and Finalizing:-
For that, I made a fire pit out of cardboard whose sides are 1 inch less from all directions than the original fire pit I made. I highly recommend that if you are using cardboard for casting purpose then always use thick cardboard only and make sure to tape all around to make it waterproof. Then I place the mould into the fire pit and mix the refractory cement then I pour the cement around that mould. I also tap the metal surface at regular intervals to remove the air trapped inside that. Then I cover all the screws with the help of PVC Pipe and half inch thick refractory cement layer laid over the entire surface. Then I allow it to cure for almost 2 days.After curing the cement remove the mould. Since I am using very thin cardboard that's why my casting slightly deformed but grinding it with the help of diamond wheel I reshape the pit. But always make sure to use thick cardboard for casting purpose. To prevent the end from Breaking Down I add this half-inch thick mild steel bar so that cement will not break during the making.
After Lining the refractory cement I slightly resized my plate also so that it fits perfectly into the pit.
Step 20: Finally After Retouching
If you Like this build then don't forget to share your opinion.
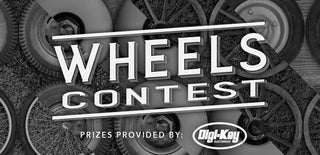
Participated in the
Wheels Contest 2017
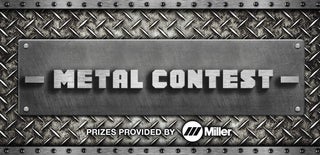
Participated in the
Metal Contest 2017
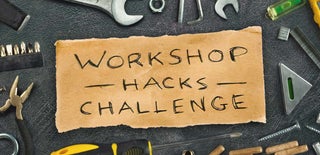
Participated in the
Workshop Hacks Challenge 2017