Introduction: Making Light From Magnetism: Electromagnetic Induction & the Bedini Machine
Great discoveries are sometimes made by more than one person at the same time. Michael Faraday and Joseph Henry discovered the principles of electromagnetic induction at much the same time. Faraday published the results of his work in 1831, before Henry, and so gets the credit. Strange to say, many scientists of Faraday's time did not accept his findings, chiefly because he had no mathematics to back it up (Faraday's laboratory work was empirical and intuitive, and belonged to an older school of scientific research usually called Natural Philosophy). Alessandro Volta had invented the electric pile, or battery, in 1800. By 1820, Hans Christian Oersted discovered the first half of the link between electricity and magnetism when he found charged wires affected a compass needle. It remained for Faraday to close the loop when he showed how magnetism could be used to generate electricity. This was called electromagnetic induction, and it was another step on a long road of scientific and technological achievement that led to all of us sitting in front of computers, reading Instructables.com on the Internet.
Electromagnetic induction is the creation of potential difference (voltage) through a conductor when it is exposed to a varying or moving magnetic field. Faraday discovered this in the course of several famous experiments I will not detail here. This effect can be demonstrated with a simple coil of fine copper wire and a magnet, but that's not nearly as interesting as building a device that will generate electricity, charge almost any type of battery, light up a bright LED, and look cool while doing it. So for this project of Making Light from Magnetism, let me next introduce the Bedini SSG device.
Step 1: The Bedini Machine
Here's a short video of a Bedini SSG machine in operation. The early part is dark, as I left the lights off to better see the flashing LED. Some of the video is shaky, due to the use of a very small handheld digital camera.
John Bedini has had a long career in electronics and audio engineering. As the story goes, he designed a simple motor-generator for a friend's daughter to make as a school science fair project. This became know as his "School Girl" motor, later adapted as the "Simplified School Girl" (SSG) motor. Bedini has his own theories about energy which are not widely supported by scientists, but it is not my purpose to present his theories or criticize them. What the SSG device does is pretty clear, and that's what we're going to build. Though the SSG is under patent, anyone is allowed to build one for their own use. My version here is not endorsed by John Bedini, his company, or anyone but myself. I learned to build it after studying videos of working versions on the Internet, drawing on my own past experiments in building electrical projects at home.
MATERIALS LIST TO BUILD A 16 INCH BEDINI SSG MOTOR/GENERATOR
*1 16 x 1 inch aluminum bicycle wheel (no tire!). The rim can be plastic, spoked or spokeless, but it can't be steel. The rim must be non-magnetic.
*12 ceramic-ferrite magnets, preferably rated C8. (This is a rating of magnetic intensity.) I used rectangular magnets bought from a dealer on eBay, but you can get the same magnets from Radio Shack, Catalog #: 64-1895 or online. The magnets do not have to be any certain shape, but they ought to be large enough to affix to the inch-wide bicycle rim. Contrary to what you often hear and read, you do not have to use expensive neodymium magnets; in fact, in some applications they can be too strong for successful operation.
*1 1/2 inch wide, 14 or 15 inch diameter rubber bike wheel liner. These are sold to protect inner tubes from rubbing against the heads of the spokes.
*1 transistor. The common and cheap 2N3055 works fine. Other types will work as well, just make sure they can handle the voltage..
*1 potentiometer, with resistance varying between 1 Ohm to 5,000 Ohms. This will allow you to tune the device and regulate the speed of the wheel.
*2 diodes, 1 1N4001 and 1 1N4007.
*1 470 Ohm resistor.
*1 Ne-2 high voltage miniature neon bulb.
*a 3 x 6 inch piece of perforated circuit board, like this stuff. The exact dimensions are flexible, so long as you have room for all the components.
*about 300 feet each of two gauges of enamel coated magnet wire. The wire should be about 4 gauges different. I used 20 gauge and 24 gauge. Don't use too fine a gauge or the higher resistance may interfere with the proper function of the bifilar coil.
*1 coil form. I used an old plastic spindle formerly wound with speaker wire. It measures 3 inches in diameter and stands 3 inches high. The hollow center, which you will pack with iron to make an electromagnet, is 1 inch in diameter. Don't use a metal spool, or any spool with metal in it.
*Iron or steel wire, or thin rods to fill the core of the coil form. Many people building SSGs use welding rods. I used wire surveyor's flags, those whip-like orange flags you find in big box hardware stores. They're used to mark out land for surveying. They're 16 gauge, stiff, but flexible. Pull off the plastic pennant and you've got a good 1.75 feet of steel wire per flag. To fill up a 3 x 1 inch cylinder, you'll need maybe a dozen flags.
*Connecting wire. I used 22 gauge plastic coated bell wire (also called annunciator wire or hookup wire). You'll need 10-12 feet.
*9 ring connectors, sized to fit 22 gauge wire and able to slip over 8/32 bolts.
*4 brass 8/32 bolts, 2 inches long, with 1 washer and 2 nuts apiece.
*3 alligator clips, 2 inches long each.
*2 nylon zip ties, 12 inches long
*Basswood or pine sticks, squared, 1/2 inch x 1/2 inch, at least 16 inches' worth. Also 1 piece of 3/8 x 3/8 inch basswood, 6 inches long.
*Poplar rods, square, 1.5 x 1.5 inches, at least 38 inches' worth. This is for the upright wheel supports and braces, if desired.
*1 pine plank. 16 x 15 x 1 inches. This is your base. The exact measurements of this are flexible, but it ought not be much smaller than this.
*Optional: 6 2 x 2 inch L brackets, with 4 screws per bracket. Use these to brace the upright if you don't want to make wooden braces.
*4 rubber or plastic appliance 'feet' with screws.
*Super glue, and plenty of it.
*6 2 inch wood screws. I used short deck screws, but any flat-headed wood screw will do.
*2 batteries of matching output. This particular wheel works fine with 6 or 12 volt batteries, or with smaller batteries linked in series to total 6-12 volts. Alkaline or lead-acid batteries work equally well, and what's more surprising, you can charge both kinds with the SSG's output.
*For the induction coil and light I used a ready-made set made by Reelight, made in the United Kingdom but available from various retailers in the USA. All Reelight sets work much the same way, with a factory-made induction coil, connecting wire. and LED light. You can make your own coil, but the Reelight set is handy and attractive.
TOOLS: power drill, miter saw, screwdriver, wire cutters, crimp tool, soldering iron and solder, medium and fine sanding block or paper, varnish or other clear wood finish, a brush to apply it. A carpenter's square, rule, and pencil would be useful too.
Step 2: Making the Wheel
Let's make the only moving part of the Bedini machine first. Take your non-magnetic bicycle rim and make sure it is thoroughly clean and straight. I got my rim from a bike salvage yard, though I later bought a simple 26 inch rim new from an online bike parts dealer. Aside from being clean and true, the most important thing about your wheel is that it turn as freely as possible. New or used, you'll have to clean the bearings. Bike grease is too thick for our purpose, so disassemble the wheel hub and get all the heavy lube out. Spray the clean bearings and hub with a light silicone or WD40 lube. Reassemble the hub, but don't tighten the axle nuts too tight. Keep the hub from wobbling, but let it spin as freely as it can.
Next, prepare your magnets. STUDY THE PHOTOS. We're going to fit the rectangular magnets at right angles to the bike rim; that way any variation in the track of the rotating rim will not reduce the coverage of the magnet on the driving coil's core. It's vital that all the magnets face outward with the same pole--in this case, NORTH--so that the driving coil can push them along. C8 ferrite magnets are seldom marked as to polarity, so you'll have to figure this out yourself. One way to do this is to use a pocket compass. The flat faces of the magnets are the poles. Test one by pushing one face toward the North end of the compass needle. Because opposite poles attract and like poles repel, the North point of a compass is actually the South pole of the magnetized pointer. To identify the North pole of your C8 magnets, they should attract the North point of the compass needle. This is important, so take care with this process. Mark the magnets in some temporary way (a bit of tape, or post-it note). ID the North poles of all the magnets. (Alternately, if you have a bar or horseshoe magnet with poles labeled, it's easy to find the North poles of your ferrite magnets.)
Get your 1/2 inch basswood stick and cut 12 short pieces exactly as wide as the C8 magnets. Remove any burrs with sandpaper. Glue the basswood blocks in the center of the South side of each magnet. Use super glue. Let dry completely.
Depending on the shape of the bike rim, you may have to trim the basswood blocks to fit inside the wheel channel. Refer the photos to understand what I mean. You want the wood to fit snugly into the rim while the magnet sits tight across the rim. I designed the 16 inch wheel to work with 12 C8 magnets. To space them evenly, glue the first magnet in place over the hole in the rim (the hole meant for the inner tube stem). This rim has 18 spokes per side, 36 in all. That means you should have 3 spoke heads between each magnet. If you're careful, you can do this by eye. Use liberal amounts of super glue on the wood blocks and press them into place every 3 spoke heads. Let dry thoroughly. When all 12 magnets are in place, take the rubber rim protector and stretch it over the magnets. This will help keep the magnets in place and protect them as they spin.
Step 3: A Solid Base
Building a solid base for the Bedini wheel is simple carpentry, but you want things to be as square and accurate as possible. Your wheel will run much more smoothly if the base is well made.
Take your base plank (in my case, a piece of pine planking 16 x 15 x 1 inches) and affix a rubber "foot" to each underside corner. These will help dampen vibrations when running and make it easier to pick up the machine and move it.
On the top side of the plank, mark the exact center with a carpenter's square and pencil. The bifilar coil that drives the machine will be here. Mark your square poplar rods to length for the upright supports. Allowing for the driver coil, its mount, and the radius of the 16 inch bike wheel, the uprights on my machine measure 11 5/8 inches tall. Measure them out but don't cut them yet! At what will be the top end of one support, find the center of the rod. Mine measure 1 1/2 inches wide, so the center would be at 3/4 inch. Here you need to drill a 3/8 inch hole all the way through the wood. Use a drill press if you have one, to insure the hole is 90 degrees to the wood. Once drilled, cut the support in two right through the center of the hole. You're making a trough or track for the bike wheel's axle to lie in. If you've done your work carefully, you should be able to use the other piece of poplar already bored and cut as the other upright. Be very, very sure the uprights are of the same length so that the wheel axle will lie square and straight.
Using a drawing compass, draw a circle on the center of the base plank 3 inches in diameter. This is where the driver coil will go. Mark an intersecting line through the center point, dividing the base into two equal halves. Now, the axle of the bicycle rim I used to make the magnet wheel is 5 1/2 inches long. You want to site your uprights along that intersecting line you drew (with the top grooves aligned with each other) no more than 7 inches apart, measured from the outside edge of one poplar upright to the other. Center the posts on the line at the necessary width and temporarily glue them down with super glue.
The upright will need braces. The simplest thing to do is to use three L shaped steel brackets, 2 x 2 inches, centered on the three outside faces of the upright. Mark the screw hole positions in pencil, drill pilot holes, and use the screws supplied with the brackets to anchor the uprights.
Alternately, you can make braces out of the same 1 1/2 inch square poplar stock used to make the uprights. Cut two equal 6 inch pieces with 45 degree miters on each end (both cuts sloping in) Stick these in place against the base and uprights with super glue, then drill pilot holes at either end and insert 2 inch wood screws. You'll notice in the photos of my device I used both methods, brackets and braces. I was experimenting with both methods, but only one is necessary to secure the uprights.
When the upright are installed and properly braced, sand them lightly and apply a coat of varnish or polyurethane coating. Let dry and move on to the next step.
Step 4: The Bifilar Coil
"Bifilar" means made of two threads or windings over a common core. An essential feature of the Bedini machine is the use of two gauges of wire on a single coil. This allows a single coil to perform two functions at the same time; in this case, one winding pulses DC voltage to the core, creating a pulsing electromagnet, while the other winding acts as an induction coil, generating electricity that is routed to the battery being charged. The usual design specs of this kind of coil require two gauges of copper magnet wire about 4 diameters apart--in this case 20 and 24 gauge. To reproduce the coil shown, you'll need about 300 feet of both gauges and a coil form to wrap them around. I used an old speaker wire spindle, 3 inches in diameter, three inches high, with a center opening 1 inch in diameter.
Take the ends of the two wires and start them from separate points on the bottom inside of the coil form. Many spools have openings here, but you may have to drill holes of your own. Make sure the wires start 180 degrees apart. Leave a generous length of free wire to start with-- 8 inches or so. Next, tape the wires to the inside of the spindle just inside the holes. Carefully wrap them in the same direction, letting them come together like a single strand. Keeping moderate tension on the wires, wrap them smoothly along the core to the opposite end, then reverse direction. Keep repeating this until you fill the coil form or run out of wire. When you get near the last of the wire, make sure you finish winding at the same end of the coil you started. Drill a pair of holes in the spindle 180 degrees apart, aligned just like the ones you started with. Divide the two gauges of wire and route them through the holes so that you end up with a pattern like this:
[outside] > 20 gauge -- 24 gauge -- 20 gauge -- 24 gauge < [outside]
This is from one side to the other, from outside to inside back to outside again. Mark the ends of the tape with temporary tags made of masking tape, ID'ing the gauge and position (i.e., "20 outside, 24 inside," etc.)
Wrap the exterior of the coil with electrical tape. Secure the end of the tape by putting a nylon zip tie around the coil. (See photos for details).
Now it's time to make the core. The core will be magnetized and re-magnetized over and over again, so it must be made of ferrous metal. Preferably the core should be made of many small diameter pieces rather than a single solid rod. This will ease the rise and collapse of the magnetic field. Iron is best, but real iron might be hard to find. For my machine I bought a bundle of surveyor's flags and cut the steel shafts into 3 inch lengths. One by one I put these in the hollow core of the coil. When it got full, I tapped the shafts in with a hammer. Hold the core up to the light to spot gaps. When the core is as full as it can be, put a few drops of super glue on it to hold it together.
The coil should be mounted in the center of the base, squarely between uprights. Cut two short length of 3/8 inch basswood 3 inches long. Glue these to the bottom of the coil on either side of the core. Keep the ends of the wires free of the glue, then use more super glue to stick the coil to the base. Get the four wire leads running out of the same side. Let everything dry.
Using a ruler or square, draw a light pencil line about 6 inches long parallel to the uprights and 2 inches out from them. This should be on the same side where the coil wires come out. Mark the line with 4 equally spaced points Drill these all the way through the base with a 8/32 bit. Insert a 2 inch 8/32 brass bolt from underneath into each hole. Add a washer to each bolt, a nut, and snug them down.
Cut the wire leads from the coil long enough to comfortably reach the brass bolts, one wire per bolt. With sandpaper or a knife blade, clean the enamel insulation from the end of each wire. About 1/4 inch cleared is good. Put an aluminum ring post on the end of each wire and crimp in place. Slip a ring post over each brass bolt. Don't secure them yet. Let's move on to the circuit board.
Step 5: The Circuit Board
I'm not an electrician or engineer, just a hobbyist. In describing how to make the Bedini circuit board, I may use inexact or improper terminology, but I shall try to make everything clear.
Start with a 3 x 6 inch rectangle of perf board. The holes may not be large enough for the transistor's pins, so keep a drill on hand with a small bit (5/64) to enlarge any holes as necessary. Have a look at your 2N3055 transistor. There are three possible connections to a TO-3 type transistor: the Base, the Emitter, and the Case, or Collector. The case is of course the metal shell of the component. The emitter and base are the two pins protruding from the flat underside. But which is which? Looking at the pin side of the transistor, you'll notice the pins are not centered. They're sited a little more to one end than the other. Orient the 2N3055 so that the pins are closer to the bottom than the top. Then notice the pins are not evenly aligned. The left pin should be a little higher than the one on the right. The higher pin on the left is the Emitter. The lower pin on the right is the Base.
Insert the pins through holes in the perf board, centered and sited about a quarter of the way from the top of the perf board. You can tack the transistor in place with a drop of super glue. Take the 1N4001 diode and connect it between the Emitter and Base. The silver bar on the diode indicates the direction electricity will flow (toward the silver band), so the silver band must point toward the Base pin. Wind the leads closely around the Emitter and Base pins. Attach one lead from the 470 Ohm resistor to the Base pin and solder in place. Have a light touch with the solder and don't overheat the transistor. Push the free end of the resistor through any convenient hole in the perf board.
Drill a 1/4 inch hole in the perf board, a quarter of the length up from the bottom of the board. Potentiometers often have an anchor tab on one side; enlarge a hole for it and insert the pot through both holes in the board. Secure with the nut included with the pot. Refer to the photos for a clearer idea how things go together.
Solder or crimp the free end of the resistor lead (now on the rear side of the perf board) to about 2 inches of 22 gauge single strand, plastic insulated, copper wire. Strip the other end of this wire and solder it to leftmost terminal of the 1-5K potentiometer (leftmost as you are looking straight on at it). While you're there, solder on about 8 inches of the same type 22 gauge wire to the center terminal of the pot. The far right terminal of the pot will not be used.
Since we're on the back side of the circuit board, solder or crimp the lead of the 1N4007 diode to the lower end of the transistor case. THE DIODE BAND SHOULD FACE AWAY FROM THE TRANSISTOR. Solder or crimp 30 inches of 22 ga wire to the silver band end of the 1N4007 diode.
Solder or crimp on 12 inches of 22 ga wire to the upper end of the transistor case. Route this wire through the perf board and back out again to the back to take up any strain on the wire when pulled. Attach a 12 inch length of 22 ga wire to the Emitter pin. This can also be routed in and out of the board to protect it from pull strain.
The neon Ne-2 bulb acts as a safety device, protecting the transistor from high voltage spikes. The Ne-2 bulb should be attached to Emitter pin and to the Collector base. The bulb's leads are stiff enough to support the bulb by themselves.
Next mount the circuit board to the wooden base. Use two short round head wood screws or machine screws. Drill out appropriate pilot holes in the perf board and attach it to the corner of the base on the same side as the four wires emerging from the driver coil (See photos). There should be four wire leads coming off the circuit board.
The lead from the potentiometer's center terminal goes to the 24 gauge outside wire. Crimp a ring connector onto the 22 ga lead. Put a 8/32 nut over the bolt and tighten by hand.
The lead from the upper end of the Collector base goes to the 20 gauge inside wire. Crimp a ring connector onto the 22 ga lead. Put a 8/32 nut over the bolt and tighten by hand.
The lead from Emitter pin goes to the 24 gauge inside wire. Crimp a ring connector onto the 22 ga lead. Put it on the 8/32 bolt connected to the 24 gauge inside wire.
The fourth lead, from the 1N4007 diode, will be used as part of the charging system.
Measure a length of 22 gauge wire about 30 inches long. Crimp a ring connector to one end, and put it on the same bolt as the 24 gauge inside wire. Put a 8/32 nut over the bolt and tighten by hand. Crimp a ring connector to a 30 inch length of hookup wire and put it on the 20 gauge outside post. When the circuit board is complete and all the connections made, there should be three long wires coming off the machine. Attach a 2 inch alligator clip to each wire. With strips of masking tape, make a label for each of the long wires, just behind the alligator clip.
The wire from the 20 gauge outside post should be labeled "C --" meaning " Charging Battery, Negative Pole."
The wire from the 24 gauge inside post should be labeled "PS --" meaning "Power Supply, Negative Pole."
The wire from the 1N4007 diode should be labeled "C+" meaning "Charging Battery, Positive Pole."
Step 6: Power In, Power Out
The Bedini machine runs on direct current and outputs direct current. The simplest way to operate it is with two batteries of matching voltage/amperage. In the photos you see two six volt alkaline dry cells set up with the SSG. One battery provides power to the driver coil, while the other receives the high voltage impulses of the driver coil, recharging it. This machine also works well with 12 volt batteries, up to and including lead-acid car batteries. In fact, the SSG mechanism is best suited to lead-acid batteries, and is known to revitalize worn out, heavily sulphated batteries. I mostly have used it to recharge AA batteries. I have two battery clips from Radio Shack, one holding 4 AAs (6 volts) and another holding 8 AAs (12 volts). I have recharged many AA alkaline batteries, and even a high energy lithium AA. I've also ruined a few AAs too. Overcharged, the dry cells leak electrolyte and must be discarded.
To hook up batteries to the SSG, you'll need a short jumper wire with alligator clips on both ends. The power battery has its + Positive lead connected to the -- Negative lead of the battery being charged via the jumper wire. Then connect the three leads from the Bedini machine as follows: The PS-- wire connects to the --Negative pole of the Power battery; the C+ connects to the +Positive pole of the Charging battery; and the C-- wire clips to the jumper wire, preferably near the --Negative post of the Charging battery. When everything is connected, turn the Potentiometer control to the lowest setting. Give the magnet wheel a modest push. As the pulses resonate in the driver coil, the wheel should "catch" and start spinning faster on its own. If it slows and stops, recheck all your connections and settings. Low voltage contacts can be finicky sometimes. Makes sure all the contacts are clean and firmly joined and try again. If you hear a slight hum or squeal coming from the driver coil, don't be alarmed. That's feedback, electrical resonance. Adjust the potentiometer until the sound goes away, and spin the wheel again.
For steadier operation (and if you don't want to buy expensive batteries) you can use a DC power source in place of the Power battery. I've tried several kinds, from expensive DC lab supplies to rectified transformers. One of the best power sources turned out to be an old model train transformer, made by the Louis Marx Company. These variable transformers step down 110 volt AC wall current to 7 to 15 volts AC. These are not precision devices, though. Sometimes the voltage goes as low as 4 and as high as 20 V AC. You can rectify the train transformer output with a simple full-wave rectifier component. With a multimeter, check output voltages at various settings and mark the transformer case to show where 6 and 12 volt output occurs. Hookup the transformer just as you would the power battery, by connecting +Positive lead of the transformer by jumper wire to the --Negative post of the Charging battery, and PS-- clip from the SSG to the --Negative lead of the transformer.
Update 2/4/2014: I've been experimenting with other power sources for the SSG, and one of the simplest and best is an old "wall wart" plug-in adapter. I scrounged a number of these from thrift shops, all in the 4.5 -12 volts range, with power ratings from 300 mA to 2.1 amps. They all work, but they require some alteration and testing.
First, the nominal voltage rating is not accurate. A so-called 6 volt transformer actually put out 7.5 volts; a 4.5 volt one put out 6. I guess this has to do with how the wall wart works under load, but be aware the SSG doesn't impose much strain on it, so you're likely to be getting more than the indicated voltage.
Altering a wall wart is easy if the cord is the two wire kind. Cut off the plug and pull apart the insulated wires 3-4 inches. Strip the ends of the wires. You need to ID the positive and negative lines; if the wires aren't marked, test them with a digital multi-meter. (On most meters, connect the probes to the wires and plug the adapter in. If the readout on the meter shows negative, swap the leads. Mark the positive line in some way and crimp on connectors). Now use the wall wart as you would a battery, and connect it to the SSG in the same way--negative lead to the PS-- wire from the machine, and connect the positive lead to the negative post of the battery you are charging.
If the adapter line is co-axial--that is, if one polarity of wire runs inside the other--you can still use the adapter. It takes more work. Solder length of bell wire to the inner and outer wires and proceed as described above.
Interestingly, the wall warts don't seem to get hot powering the SSG. I've run them for hours and the adapter is barely warm. The charging batteries stay cool (sometimes even feel cold!) too.
Step 7: Let There Be Light! by Induction!
The accessory induction coil and light are factory-made items I purchased online. They're made by a British firm, Reelight, for use on bicycles. Traditional bike lights use batteries or friction-powered generators for power, both of which have obvious drawbacks. The Reelight system does not impose any drag on the cyclist, and has no batteries to wear out. Stick some magnets on your bike rim, mount the coil, and as long as you pedal, you have a blinking safety light.
To work efficiently, the induction coil should be mounted squarely close to the moving magnets. I made a simple mount of poplar wedge and a bit of lath at the proper angle to the wheel and mounted the Reelight coil with two nylon zip ties. Clearance between the coil and moving magnets is 1/8 inch.
The red LED light has a mounting hole on the back. I put a short piece of bamboo skewer on top of one of the wheel supports and slipped the LED onto it. Now every time a magnet passes the coil, a pulse of electricity lights the LED. The Reelight coil could be modified to do other work--charge capacitors, charge batteries, etc.
Step 8: How It Works, I Think, and Troubleshooting
If you start your SSG going and the Ne-2 bulb flashes, something's wrong. The Ne-2 bulb is there to protect the transistor by absorbing high voltage spikes that should be going into the battery being charged. Check your connections again, particularly to the charging battery. It is possible to run the SSG without a Charging battery in place. The Ne-2 will flash the whole time. You're taking a chance of blowing the transistor, but it can be done. The wheel will probably run its fastest with the 5k pot turned all the way down to the lowest resistance, but the most efficient charging may occur at a slower RPM. You'll need to monitor input and output with multimeters to find the sweet spot best for charging. I tend to run mine flat out--it's more impressive that way. Whining coming from the SSG driver coil is feedback. You can diminish it by tuning with the pot.
My wheel design has a free floating axle. I made it this way to facilitate changing the wheel for other experiments. Only once have I had a wheel come loose while turning. If you're concerned about the wheel flying off, you can anchor it by screwing an L bracket to the side of the poplar uprights, clamping the axle in place.
Here's an SSG with a pendulum instead of a wheel. Notice it's the same frame as the one described here:
Here's another video showing the SSG operating with a single permanent magnet instead of the elaborate wheel:
That's how you turn magnetism into light. Good luck, and keep building!
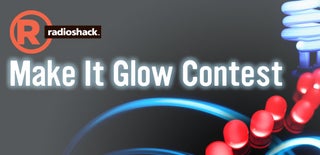
Runner Up in the
Make It Glow Contest