Introduction: Power Your Home and Workshop With Steam
First Thank you for reading my instructable. This is a work in progress, I will be adding more and more to this instructable on how to build a steam driven turbine and power plant for your home. As always if you find any typo's or any mistakes please let me know there is a lot of information I am going to throw your way. So lets get started.
I am going to show you how I build this 45 Kilowatt Genset, or steam turbine to power my home and business. This unit was a major effort to get off the ground. I will attempt to show you how to build this beauty. Perhaps you can build one on a smaller scale. This unit is not for the amature. This build is very difficult and dangerous. There are a few things you need to be aware of when working with high power.
1. Respect the power. It will kill you in a heartbeat.
2. DO NOT ATTEMPT THE PROJECT IF YOU DON'T KNOW HOW TO WORK WITH HIGH VOLTAGE AND HIGH PRESSURE STEAM.
3. BE REALISTIC. If you don't have the equipment to build this device then send the parts out to be made.
4. What you don't know, ask. I will be happy to help anyone in any I can.
Always wear safety glasses and proper protection when working with electronics and steam.
Ok this is the turbine and generator attached together on the test stand. This is a turbine of my own design the generator portion or Technically the Alternator to be more precise is as mentioned above 45 kw 3 phase AC power output. The turbine in order to produce that level of power it required to run at an astounding 100000 rpm, thats right 100000. Now that will ruin your day if you have a major malfunction this runs at ballistic levels so if you have a destructive or catastrophic event the shrapnel will kill you. It would literally explode. This will turn you into a red mist. That said I have maintained my rpm to more respectable and safe level of around 50000 rpm my power output drops, as should be expected. Though I feel safer at that rpm. My power levels at 50k are about half of my top end of 100k so around 22 kw output 3 phase.
This is more that enough for my purposes. So here is the layout and break down of the genset. From right to left. The large cylinders are far right the alternator left of that larger alum housing is the turbine chamber, the input to the turbine is via the silver high pressure line you see entering the turbine. This LIne is rated for 10000 psi at over 800 degrees. My steam unit runs at a max of 500 degrees F so i have plenty of worry room from a potential runaway. The steam unit will be discussed later right now turbine. so after we see the input line to the left of that you will see the oil pump system I have to use turbine oil rated for aircraft turbines. 150.00 per 5 gallon drum. This is great for the protection of the bearings. I am running hydrostatic bearing at the front of the turbine and a ceramic at the rear. both rated for very high rpm. The pump is a standard 110v ac motor driving a screw pump to maintain pressure at 55 psi for the hydrostatic bearing. the oil is also use to cool the alternator during runs. the oil is returned to the bath via a radiator or heat exchanger.
just below the alternator portion on the right you can see the pressure sensor and oil filter setup, I use a standard automotive sending unit to give me my oil pressure more on that later. In the following steps I will show you more detail for the components of the system.
the top drawer housed the control panel. This is the basic layout of the genset.
Step 1: DA Build
In this drawing you see the new design of my labyrinth seal. This device is used to allow steam to flow in only one direction inside the rotor. these two pieces stack one on top of the other with the geometry facing each other.
Steam enters at the center and flows to the outside into the jets. the pressure builds and only allows the steam to flow to the od of the part and out the venturies.
This is my design I was inspired by an a similar invention by Tesla. His however had issues. I made some changes and improvements and what you see here is the first layout of my design.
Step 2: Da Real Thing
Here is the part completed and ready for assembly. All I need to do now is buff and clean the surfaces to help with adhesion and viscosity of the steam to facilitate the choking effect. I will explain in more detail later.
Step 3: Rotor Time
This is a rotor of my own design. This is new. This is a leap forward in turbine design. This is the bottom piece of a two piece rotor. the rotor is completely enclosed unlike standard turbine rotors. This unit has no veins exposed. the are inside the rotor the steam is injected via the valvular disk conduit on the previous step. The conduit rides inside this rotor and the jets of steam expel and hit the geometry of this rotor assembly. the steam is kept in contact with the surfaces longer transferring more of the kinetic energy to the rotor than in standard types of turbines. I have found an increase in efficiency in the power out of this unit to over 95%. this is not a typo. This is a leap forward in steam turbine tech.
The next drawing shows all the pieces together.
Step 4: Commin Togeather
In this picture you can see the major parts of the alternator and housing on the workbench the large steel drum is the housing for the alternator. Behind this with the blue tape is the alternator assembly, shaft, and cartridge with seals . this simply slides into the housing and is fit with friction the bearings are in the front of this housing you can see the dome on top of the drum this is where the hydrostatic bearing is inserted from the inside. there are drilled holes in the housing that allow for oil to enter the bearing system.
The rear bearing is a ceramic bearing and is held in the rear plate you can see this plate further in other pics and steps.
You can see the bearing in the second picture. the third picture shows the bearing housing welded into the main assembly. Now it is ready for assembly.
Step 5:
In this picture you see the turbine lower half attached to the axle and all the major parts assembled. The other half of the rotor will be attached with the valvular conduit held inside the rotor. the outer housing of the rotor is needed to hold the conduit centered and the rotor will be free to rotate around it.
In the second picture you can just see the other half of the rotor, you can also see the breaking tool i used to run the turbine during breaking in phase. I had to run the turbine with an electric motor to breaking the bearings. That small round piece fit into the assembled rotor and the motor shaft fit into the end. I was then able to run the rotor and alternator for long periods at low speeds to break the system in.
Step 6: Covered
Here you see the rotor housing attached and the valular conduit inserted into the rotor and the steam input attached and ready to run.
Step 7: High Life
Here in this picture you can see a closeup of my high preasure line. This is stainless steel construction, braided with a quick disconnect at the turbine input. this line is about 10 feet long and is run from my steam generator. The burst rating of this line is over 10,000 Psi. high temp over 700 degrees. Very strong and durable stuff. I don't want to have deadly steam excape and cut me in half while admiring my work. So I overbuilt this system.
Step 8: Kewl
In this photo you can see my oil cooling radiator. this was used to cool oil. It came from an old trucks automatic transmission the fan is located at the rear. I will add a picture of that once I retake them.
Step 9: One Panel to Control Them All.
Here you can see the control panel located inside the drawer of the test stand. I have added several gauges most of the gauges are from my local auto parts store. As you can see there is one for Air Fuel Mix, one for oil preasure, one for oil temp, and one for control voltage. I had to add a 12 volt power supply to run the gauges and sending units.
The center digital gauge was handmade by myself. It is the rpm gauge and as you can see it is rated to display 6 digits. The top center is the hours of operation display showing total time machine has run.
The three switches are from the right. Oil pump #1, Oil pump #2, And main power on switch for the Steam plant. As you can see I cut this panel with my cnc mill, I also cut the lettering with the mill as well.
Step 10: Spagetti
Here in these two photo's you can see my wiring harness, entering into my control cabinet via the drawer. Neat and clean, until you get inside the panel.
Once inside the panel you can see the mess of wires I have to hook up to my new set of gauges. I will add this pic later today. There is a lot of wiring to be done.
You can see the circuit board I made that is the rpm gauge. Also visible are the control relays for the system.
The last picture you see the controls hooked up and running. kewl baby
Step 11: Oil Treatment.
Here is this picture you can see the Main pump motor and oil tank for the turbine. Oil is used to lubricate the front hydrostatic bearing and also to keep the alternator cool. There is a mass of hoses and supply and return lines that go into and out of this tank. The second picture shows some of the lines running back and forth from tank to the turbine and the radiator or heat exchanger which you can just make out in this picture.
Step 12: Pump It Up
In this picture you see the pump hookup. This is a 100 psi pump set to output around 55 psi. the black rod sticking out of the brass fitting at the bottom of the pic is the adjustment for pressure output. If you look at the right of the pump are valves I use the valves to control the flow from this main pump to the system and the return, I had an issue when I built this system with my oil not being pulled from the system quick enough and as a result the oil would overflow and leak everywhere. In response I added what is known as a scavenger pump to help pull the collecting oil out of the system to avoid the backup or buildup of excess oil.
The second picture shows the white secondary scavenger pump that removes excess oil from the system. The last picture is of both pumps working together within the system.
Step 13: Feedback I Need Feedback
Here you can see the oil filter system and the pressure feedback sending unit. This is a 12 volt automotive sending unit I converted to work for this system. you can see the control wires and oil line running to the sensor.
The second pic is the oil input line this is the main input for the turbine to keep the bearing lubed and under pressure if the pressure falls below 45 psi the hydrostatic bearing will fail to keep the shaft from the bearing surface and the system will overheat and self destruct. That is why I must monitor the temperature of the oil to avoid a catastrophic failure of the lube cooling system. The other line held on with the hose clamp is the overflow return line. I should never see any oil here, if I do then I need to adjust my scavenger pump settings.
You can also see my mounting saddles and bracket on the right of the alternator This is really all that I need to hold the unit down. keep in mind that you must have a balanced rotor on you turbine if your rotor is not properly balanced the system will self destruct.
I had my rotor professionally balanced by an aircraft engine maintenance facility that works on jet engines. My cost was 1300.00 for the service This was essential to have it balanced right. Don't think that you can get away with just trying to balance the rotor like you would an airplane prop. or a model aircraft propeller. It won't work. The rpm you might run a Propeller at are not even anywhere near the rpm this turbine runs at. It must be balanced at or near operational rpms.
Step 14: High Speed Low Drag
Here is the rear of the alternator. You can see the interface ring, plate and sensor used to measure the rpms. The wires you see connect to the hall effect pickups the read the magnets attached to the rear of the shaft there are 4 magnets so I get 4 pulses per rev. This is sent to the display board and shown on the control panel. There is a cover plate that goes over this I removed it to show you the board.
The blue and white wires are the power output wires. There are three white, three blue, and three red, and one green. One set for each phase.
Once the system is running I do what I call scrub the power. I take each of the phase outputs and run through high power rectifiers this helps to level out the signal. I also use a bank of large capacitors for filtering. Then I rectify the three phase power and translate via circuitry. The three phased power is combined into one ac output. I then use a massive transformer to bump the voltage down and increase the amps. I have a net of 220 out and a very nice clean ac sine stable and ready to run any device. I will show my control circuitry to you via a new instructables. It is very involved and would make this one way to big. It requires a detailed explanation. I will also be adding to this instructable as i finish this system.
Step 15: Hot Stuff.
Ok basic turbine genset done. Now how do I produce the steam to drive this massive monster. Well I looked at many many ways to produce steam. All were costly or not enough volume. I wanted to run tests and when the testing was done convert the steam plant to multi fuel so I could get off the grid. That is what I am going to show you next. This system is my own design again. It is somewhat unique, and as usual very dangerous. I use ac power to produce my steam. Basically it is the same overall simple design as an HHO system just that it runs on ac not dc, and I have built it like a brick shit house. The boiler for lack of a better word is made from schedule 80 316 stainless. 3 feet long, 12 inches in diameter 1/2 inch thick walls. I had a Flange and a dome welded my a boiler maker. This is critical If the welds are not done right the system WILL Explode and kill you. if you get a leak you will if standing close be cut in half. Literally, Steam is not something to be messed with. Use caution when working with it.
You can see the top of the boiler 1/2 inch thick plate with 32 holes drilled and tapped to hold the cap to the boiler. The seam between the cap and the flange has a gasket made from 1/8 inch thick brass plate that fits the flange perfectly. I took great care in the design of this beast. all of the connections are rated for high temp high pressure all 316 stainless except for the fitting for the temp thermocouple. and the pop valve.
You can see the body of the boiler in the last two pics. The control for the entire turbine is by opening and adjusting the yellow handle valve. This valve like the other parts are rated for over 10000 psi. and 800 degrees F. You can see the output high pressure line coming out from the control valve.
You can see the electrodes entering into the top of the endplate. This is where the 220 volts ac enters the system. There are two insulated high power connectors that allow my power to pass the end plate and connect to the heating elements inside the boiler.
There is also an input fill hose on the top left, and a pressure gauge center all are built to withstand the heat and pressure of this system. the brass colored rod next to the pressure gauge is the pop valve this will open and release all build up pressure in the event that my control circuit fails. Almost like a standard water heater except this one is rated to pop at 150 psi. Which is my operating just above my operating pressure,
Step 16: Top Down
In this picture you can see a birds eye view of my controls and feedback. You can see the solar panel for the temp display this will work with just standard in house lighting to power the temperature sensor.
You can also see a better layout of the output piping for the pop valve on the left. You can just make out the two power input lines connections one black one white.
At the bottom left corner of the box you see my control mosfet power switch. This switch is attached to my safety pressure switch which is what drives the system. The bus bar at the bottom shows the connections. if the pressure arrives at 120 psi, the power will be cut off. if it falls below 90 it will turn on. This is a solid state switch, I didn't want to rely on a mechanical switching system.
You can see on the control bottom left the large alum heat sink for the power switch. I had to add this because my first one burned up in testing, due to the high power consumption of the system.
The bottom right of the pic is the main disconnect for the system. to shut off power from the entire unit.
The heating elements are simple for this, what i did is cut large diameter stainless steel discs with two holes in them the disks were about 1/2 inch smaller in diameter then the boiler. One of the holes was 1 inch in diameter and the other was 1/4 inch in diam. I then would stack the disks alternating the holes large over small and tied them together with 1/4 inch tread stock made of again you guessed it stainless steel. the larger hole would allow the nut to pass through the one plate and not make contact to the plate above or below. This insulated the rods and bolts from each other and powered each plate separately I then added a spacer around the rod stock to keep that end of the plate from dropping and closing the gap. I need the gap of the plates to be 1/2 inch apart.
I used purified water or distilled water in the boiler. this greatly increased the resistance to electricity or the dielectric properties of the water to keep my amp draw down in relation to my disk spacing. This is an important part of the design. If you put tap water or contaminated water in the system you will blow fuse after fuse.
I also made sure the plates did not and could not touch the side of the boiler. This will help keep me alive if I for some dumbass reason decided to touch the powered up steam generator.
Step 17: Finaly
And my last picture is a closer look at the control switch and my pressure gauge. Here is a link to my website with a video of the steam system running click on the link, the steam video is at the bottom right of the page.
More to come keep watching for updates to this.

Runner Up in the
SciStarter Citizen Science Contest
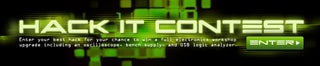
Participated in the
Hack It! Contest
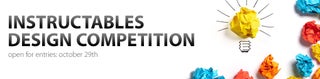
Participated in the
Instructables Design Competition