Introduction: Prosthetic/Robotic Hand Printable As an Assembled Unit Without Supports
You might have heard about the 3D-printed prosthetic hands created by Richard Van As and Ivan Owen for about 100 children thus far. That's a great thing they've been doing. There's also a "Snap-Together Robohand" version, http://www.thingiverse.com/thing:92937, which is intended to be easier to build. I'm sure it is... but it still takes half a day to print the parts and assemble them. Unfortunately, I had less than 3 hours total on Saturday, September 28, 2013, to give an overview of making technologies and have YMCA Black Achievers students actually build something. So, I designed a new prosthetic/robotic hand for which all the printed parts print assembled without supports in less than an hour. You still have to thread some fishing line and rubber bands through it, but from print start to working hand is easily done in less than 90 minutes!
The hand is roughly sized to match that of a 18 month old girl. It embodies a variety of compromises, any of which might make it unusable as a prosthetic in practice... but it certainly is functional enough to get the idea across -- which was my goal. I know very little about prosthetics, but I do know that fitting them is a very personal thing, so the primary design doesn't have a mount attached. It is possible to add a simple mount and still have the complete structure print assembled as either a prosthetic hand or a hand for a robot.
Step 1: It Prints Assembled (but You Still Need to Add Some Stuff)
- A 3D printer and printing supplies. I used a MakerGear M2, which is an excellent printer, but as I write this costs close to $1,800... there are many cheaper alternatives, and at least some of them can make prints as good as those made by our M2. This hand should be printable on just about any FDM/FFF printer with a large enough bed. Printing one hand uses less than $1 worth of PLA filament. We recommend PLA, rather than ABS, because PLA is more dimensionally stable and there are various spots where a little warping could cause a lot of problems.
- Five rubber bands. We need the fingers to be able to return to and stay in the open hand position, and these wide rubber bands do that pretty well. You can buy a bag of "firm stretch" ones for a $1 if you haven't got them already.
- A few feet of monofilament fishing line. The channels for the fishing line form paths accepting wires or line up to about 0.7mm diameter; I used a 20-pound-test line with a 0.0185" diameter, which is a little less than 0.5mm. One could use string, etc., but different plastics tend to move past each other more smoothly without needing lubrication. A 250-yard spool costs less than $3 and will make a couple of hundred hands.
- A pair of scissors. This is used to cut the rubber bands and the fishing line.
- A pair of tweezers with a very fine point. This is used to guide the rubber bands through the slots. The end of a partly-unbent paper clip is actually a good alternative.
Step 2: Two Hands Are Better Than One?
Grab the design files I've posted on Thingiverse: http://www.thingiverse.com/thing:158843
Initially, I'm posting just the STL file for a pair of hands roughly sized to an 18-month-old girl. Yes, you can actually print both a left and a right hand on the bed of our M2 simultaneously -- and there's still space to spare, although we recommend rotating them at a 45-degree angle. This is what you see in the photo. However, I'll post more design files as I get things cleaned up and/or I hear more about how people would like to use this.
The hand was designed using openscad, and is fully parametric in terms of both overall size and tolerancing. The tolerance issue comes from the fact that this hand has a lot of print-assembled hinges in it. The hinges use a special design that should be printable using most FDM/FFF printers, but how close to each other two threads can be printed depends a lot on what printer you have, the material you're printing with, and how well you've tuned everything.
Although there is a lot of complexity in the fingers and lots of plain solid in the palm, the hand prints in PLA as quite a strong part even with relatively low fill percentages. Something between 20% and 40% should be fine -- most we've printed have been 25% fill. We used 0.25mm extrusion of PLA at a head temperature around 195 degrees C. That's a little hot, but there are no significant spans here, and we need good binding to get the strength desired for a prosthetic. The borosilicate glass bed was kept around 70 degrees C during printing; the hand sticks to the bed very well at this temperature, but literally pops off when the bed has cooled back to room temperature.
Step 3: The Not-At-All-Speckled Band
- Cut a rubber band to make a straight elastic band.
- Tie one end in a simple knot, as shown in the photo.
- Trim the other end of the band to be somewhat pointed. This will make it easier to feed under the bridges.
- Start at the base of a finger and work the pointed end of the band under the first bridge. This is where a fine-tipped tweezer or a paperclip can help by nudging the band's pointed tip through.
- Pull the excess band through until the knot has hit the first bridge and tension it accordingly.
- Repeat the fishing and tensioning process for the next three bridges.
- Tie a simple knot as close as you can to the tip of the finger then push the knot down to complete the tensioning. The finger might bend backwards somewhat under tension; that might look funny, but is essentially harmless.
You can trim the excess band ends any time, but I'd suggest delaying a bit because it is easier to slide the knot down to adjust tension when there is a longer end to grasp.
Step 4: No Strings Attached
- Feed the fishing line into the slot at the bottom of the back side of the hand (under the UK logo). It will come out on the inside of the palm.
- Feed the line through the holes in the segments of the finger.
- Once the line is through the finger tip, knot it as shown in the photo.
- Trim the line just after the knot you just made.
- Cut the line from the spool so that the line extends at least 6 inches back before the wrist.
Once all the lines have been run, grab them behind the wrist and try pulling on them to close the hand. Work it a number of times to remove any minor burrs or imperfections that may have made operation rough. Once operation is smooth, carefully align the lines and twist them together with the fingers all even. Tie a simple knot at least 4 inches behind the wrist to keep all the lines together.
Now you can make final adjustments to the rubber band tensioning. If any of the fingers do not return smoothly, increase the tension on those fingers by nudging the rubber band knot closer to the finger with the rubber band stretched a bit. Don't worry if you break a rubber band -- you can easily replace it.
Step 5: Give Yourself a Hand
Ok, you're sort-of done now.
Recall that we said you could have modified the design so that the printed hand would include a mount... but you didn't do that, did you? So, how do you hold it? I find it easiest to hold it like I did in the intro photo -- from the left and right sides of the palm, using my other hand to pull the fishing line. It works surprisingly well... as a demonstration.
If you really want to try to use this as a prosthetic device, you'll need to figure-out how to scale it and mount it on the user. Scaling isn't hard, but mounting it depends strongly on the anatomical structure of the individual who will be using the hand. For example, if one is only missing some fingers, the design needs to be adjusted to fit around the remaining fingers. A potential user with an intact wrist easily could be fitted so that downward motion of the wrist closes the hand, but routing control up to the shoulder is also possible. Replacing human muscles pulling fishing line with motors or "muscle wire" also could be viable, and this could make a nice, simple, hand for a robot.
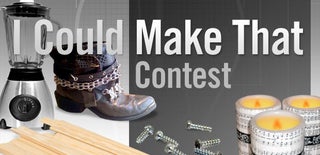
Participated in the
I Could Make That Contest