Introduction: Scrap Adirondack Chair
Summer's over and the weather is crisping up, but it's not too late to spend some time lazing on the deck in the sun. These chairs are a modern take on the rustic Adirondack chair, stripped down to a simple wooden wedge with angled back and cantilevered arms. Low to the ground and laid-back, it's perfect for cabin deck or poolside patio. The wedge base is old-growth Douglas Fir, oiled to bring out the grain and then coated with outdoor-grade polyurethane. All of the slats are various shop scraps of flooring and other off-cuts, bought in bulk bundles from the ReBuilding Exchange here in Chicago.
The chairs were made to break down flat, though I screwed them together for final assembly. You could easily use through-bolts instead of screws to make them permanently de-mountable for storage or moving. This could be built with just a circular saw and a drill, but a table saw and chop saw make things a lot easier.
You will need these materials:
1 8' 2" x 12" (per chair)
1 8' 2" x 4"
Approx. 40 linear feet of assorted 3/4" material
8 2" x 3/8" hex-head bolts or a handful of galvanized 1-1/2" screws
Galvanized (or, better, stainless steel) 1" and 2" screws
Wood glue
Outdoor-grade finish of your choice
You will need these tools:
Chop saw
Table saw
Circular saw
Orbital sander
Drill/driver
Clamps
Chisel
Hand plane
Tape measure
Square
Pencil
Paintbrush
Rags
Step 1: Base Assembly
I made my base by laminating together a pair of 2" x 8"s; you can eliminate this problem by using a regular 2" x 12". That said, lamination is a great way to make use of smaller pieces of scrap.
Rip a straight edge on either side of your boards on the table saw. Go ahead and glue up the whole 8' lengths of wood; you'll cut them to length later. Generously coat with glue (I use a mixture of wood glue and polyurethane glue like Gorilla for maximum strength) and clamp together, cleaning up squeeze-out with a damp rag and putty knife. Once the glue has cured, run through a thickness planer or use a hand planer to clean up the seam.
Run a rabbet on one of the long edges of your newly laminated piece (or 2" x 12", as the cse may be) that is 3/4" x 3/4". You can use a table saw for this, or set your circular saw shallow and use an edge guide to make a straight cut.
While you have your saw settings, go ahead and run the same rabbet on your 2" x 4", for the back supports.
Cut the rabbeted 2" x 12" down into two 36" pieces on a chop saw.
To make the wedge shape, clamp the 36" blank to the edge of a table. Strike a line on the non-rabbeted edge that tapers from a full 11"-12" on the one end to 4-1/2" on the other. Cut that line witha circular saw. Your rabbets eventually have to face one another, so make sure your tapered cuts are mirror images of one another across the two pieces.
To increase the long-term durability of the bases, which are made of soft wood, I put hardwood runners made from old oak flooring on the bottoms. Cut strips of hardwood (oak, walnut, maple, etc.) to 1-1/2" wide, then glue and screw them to the bottom of the wedges, planing the seams smooth.
Step 2: Dados and Half-Laps
The base of the chair has a dado, or groove, to accept the two uprights that support the back. A dado ensures that the chair is super-strong, and take a lot of weight in reclining. It also means that the pieces can break down flat, into a back and a base piece.
First lay out the groove by putting your 2" x 4" on the base and scribing some lines. I'm not sure what angle it is exactly; I just eyeballed it. Make the base as long as you want -- 48" if you want to kick your legs out flat, like a chaise, or about 20" if you want it to act more like a conventional chair.
Cut the 2" x 4"'s first, mitering one end so it will be flush with the ground. The length should be around 30" from the top of the eventual seat surface to top of the 2" x 4".
Next, cut out the dado in the base. Set the table saw or circular saw to a 3/4" depth, then run the piece over the blade, using a miter gauge to prevent kick-back. Knock out the chips with a hammer and chisel. Do the same for the back pieces, creating a half-lap that matches the dado. Remember to make your notches mirror images of one another, on the same side of the wood that the rabbets are in.
Step 3: Slattin'
For the cross-slats, I made a simple jig to help place the screw holes. This saves time and makes sure all the fasteners are lined up.
First, use the table saw to cut all your slats to a uniform width. Or don't. Random slat widths could be handsome as well.
Next, use a stop set up on the chop saw to cut all the slats to 20".
The jig is super-simple: take a scrap, the same width as your slats, and cut two v-shaped notches or drill two holes, evenly spaced apart and 3/8" in from the end, for your two screw holes. Screw on another scrap, perpendicular to the first, so that you can register the jig against the side of the slat. Use this to pre-drill 1/8" pilot holes in the ends of all the slats.
You can run a chamfer on the edges with a router, table saw, or hand plane so there are no sharp edges in contact with the body.
Step 4: Assembly and Finishing
Once everything is notched, rabbeted, cut, planed, and ready, assembly is quick.
I cut a spacer block so that my slats are evenly distributed, but again, random widths could be a nice move. Pre-drill, glue, and screw the slats into base and back, tying the parallel pieces together. Use outdoor-grade screws -- galvanized or coated at least, stainless at best.
At the top of the back and the front of the base, put a second slat perpendicular to the seat/back plane, which will serve to brace the structure side-to-side.
You can just screw the base and back together, like I did, or use through-bolts so that it can be broken down.
As for arms, they are optional, but great for propping up a beer. I used some leftover slats to make an "L"-shaped cross-sectional piece, then screwed it into the uprights.
Sand the whole thing down thoroughly, then apply many coats of your favorite finish. I used a base coat of Good Stuff, which is a beautiful hand-rubbed, oil-base finish. That brought out the grain and warmed up the wood while providing a nourishing foundation of protection. I followed with several coats of water-based polyurethane, which is nice and thick and non-yellowing.
Sit down and enjoy!
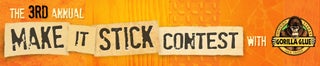
Participated in the
3rd Annual Make It Stick Contest