Introduction: Spiral Vessel- Turned and Carved
How to turn and carve a spiral vessel
This is one of my main entries for the Sydney Royal Easter Show. I though that I would share the process of drying timber and the steps to turning and carving a piece like this.
Inspiration- One of the guys from my turning group did a similar piece a few years but recently i have seen a page on facebook that has a similar style. https://www.facebook.com/TheWoodenPotter/?fref=ts
Hope you can get something out of this. More of my works at: https://www.facebook.com/Simon-Beggs-Wood-Turning-...
Step 1: Rough Turning
Finding the center on a round piece: To do this I used a compass. This is an accurate way of finding the center. Set the compass to approx half the diameter. Put the point on edge and mark lines to the center from different points. Where all the lines intersect or leave a small space is the center. It doesnt matter if your gauge measurement is slightly over or under, you swill still get a shape.
Chucking: I could use a faceplate but I rather just drill a 50mm hole using a forstner bit. I means that your chuck stays on the lathe so there is 1 set up of the lather, rather than 2
Shaping: I have covered some turning technique in other instructables. Simply, use a bowl gouge riding the bevel. It does not have to be accurate in shape and finish in this case as it was wet timber and i had to dry it. My gouge wasnt exactly sharp but i didnt need a clean finish at this point.
To set up the shape I wanted the bulge towards the top. The ratio 5:8 is apparently an aesthetic ratio and i have to agree. Tends to look good every time i use it. To set up the carving you will want an ogee shape (radius top and bottom) to blend the carving in so it is not an abrupt start.
Step 2: Turning With Semi Green Timber
I had been saving this piece of camphor laurel for a project like this. I bought it a year ago but it was still a bit too wet. There are a few options I had. All of these quicker after rough turning it too approx. 25mm wall thickness.
- wait for it to dry
- bag with sawdust
- microwave it.
- plenty of other techniques that turners use
Microwave are fun. Also I had some experimenting in the past and its the quickest so that was my pick.
It is a bit of an art to get right. I know because of some nice pieces of timber that I have over done and burnt, warped too much or cracked.
What you need:
- old microwave
- scales
- plastic bag
Step 1: Rough turn your timber to approx 25mm wall thickness. Ill cover some turning techniques later
Step 2. Weight the timber.
Step 3: Place timber into plastic bag and then into the microwave. I think the plastic bag helps the timber sweat, allowing more of the water to come out
Step 4: Zap it. Timing is the crucial element of getting this right. This time I did it a bit differently and seemed to work better. 10 seconds on, 5 min off (or the length of a song. Easy to keep track). That doesnt seem much but after a few rotations it starts to sweat the water out of the timber. In the past I have done 2 min on 50% but have overdone a few.
Step 5: After a few rotations with the 10 seconds on/5 min off, take the timber out of the bag and weigh it. It can be hot and it does create steam. It will begin to loose weight as the water goes. You can loose about 50g or more off water on a wet piece in each weigh in. I have seen pieces almost halve their weight by the end
Step 6: Repeat. Keep going until the weight starts to only decrease by small amounts. Then its almost at the 12% moisture content that you are aiming for
Step 7: I then like to put it aside for a few weeks just to equalise with the surrounding conditions. This piece I left inside under the aircon, in a dryer room. This step I guess is not essential
Step 3: Final Turning
I used the cole jaws to mount it. I think this is the easiest way of remounting rough turned timber other than an expensive vacuum chuck. Please share if you have an easier way.
To start you want to true it up. start with the chucking point. The point of the skew chisel does this job well. I then used a scraper, which is a tool i dont use often, and the skew using it in a scraping motion to clean up the outside. Pic 5 shows a step in the timber. In the drying process the loss of moisture will change the shape of the bowl, often to an oval shape. This happens as the long grain becomes close where the moisture was. The end grain wont really move, hence the oval shape.
Keep reducing the shape to your desired thickness using your fingers as a gauge or use a set of calipers. Turn the lathe of before doing this.
When you are done sand. You only really need to sand the bottom, top and inside as the main section of the outside will be carved
Step 4: Marking Out
I marked out increments of 50mm on the outside of the of the vessel. Rest the pencil on the rest as the lathe is running. This give you your lines on the circumference.
My lathe has an indexing holes in the headstock. I locked the pin in and ran the pencil along the rest at all of the positions of the holes. I wanted more lines so I just marked the mid point on the rest.
Roughly marking corner to to corner I got my spiral shape. Do mark accurately because this will determine accuracy in carving.
Step 5: Carving
I only really used 2 tools for the most of this. My 12/8 v tool and 5/5 shallow carving gouge.
Warning. This is time consuming. It is rewarding but a test of patience as it gets repetitious of 24 spirals.
Ill use the pics to reference the steps
(1) Start with the v tool to follow your lines. Control is important at this stage. Keep the depth consistent. Also make sure that your cut is in the middle of the line.
(2-3) Increase your depth. The v tool should be cutting from both sides
(4) End grain can be harder. If you like a dremel with a burr can make it a bit easier
(5) But not as neat. Get your v groves going across your entire line. I did this in 3 steps (top, bottom, mid)
(6) A file can also be used to straighten up any misaligned sections
(7) Mark your center line between all these groves. Using the 5/5 or similar chisel, start to remove all corners of your spirals, give a round shape from the angular one.
(8) Shows the difference in form
(9-10) I wanted a steeper angle in the bottom of the grove. I used the edge of the 5/5 to cut deeper, alternately cutting left and right sides, keeping the center. If It was off centered, I focused cuts to one side
(11-12) Keep your tools sharp. I use a leather strop with tormek honing compound as I carve. Makes a big difference.
Step 6: Clean Up and Finish
(1-2) Sand. Then sand some more. I set up infront of the tv and sanded for quite a few hours but dont let that discourage you. Start with 120 grit and then work your way to your desired grit. I just used the 240 and 400 after the first stage. Pinch the paper to get a point and start by sanding the bottom of the grove. Then sand the top, moving the paper side to side to prevent flat spots. Also mark with pencil a starting spot. Makes it easy to keep track of what you have done.
(3) That sand paper is all 240 and 400 grit. I used a bit
(4) Remount on the lathe just to do 2 min sand to remove sanding marks at the top and bottom
(5-6) Oil. I use Kunos oil. Using a rag, apply a thick coat. it will soak it up. I would get drips to run down the grove and then spread it over the top. For the 2nd and 3rd coat apply a thinner coat. It brings out the colour beautifully. I then go over it lightly with cabinetmakers wax (bee and carnauba wax mix) with steel wool. Buff off with a clean cloth and you are done :)
Hopefully I have inspired you or helped with turning, carving or drying timber for turnings. Check out my page for other works :) https://www.facebook.com/Simon-Beggs-Wood-Turning-...
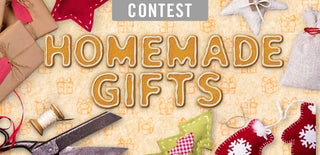
Runner Up in the
Homemade Gifts Contest 2015