Introduction: Steel Washer/Dryer Stand With Adjustable Legs
First a little background:
When I bought my washer and dryer a couple years ago, I couldn't justify the extra $400 for the stands to raise them up to a comfortable height for loading and unloading. I decided to build my own stand out of wood and was able to put together a real sturdy setup. The only problem was that my washer and dryer were located in a part of the basement that had a sloping concrete floor. I shimmed my heart out trying to get the platform level, but it still walks all over the place and I have had the dryer slide off the edge a couple times.
Time for an upgrade. I decided to build a new stand out of steel. I haven't found any information online on how to build your own out of steel, nor with adjustable feet, so I will be designing and building the project. Ever since I got my new wire-feed welder I have been looking for projects and this one fits the bill properly.
Step 1: Design
I wanted the new washer dryer stand to be stout, but easily moved so I decided to make 1 stand for each machine so I could adjust them independent of each other and I would be able to get them into the basement easier than one large stand. The only measurements I really needed were the distances between the feet front to back and side to side. The stand doesn't need to be any bigger than the footprint of the machines, so I designed mine that the feet set directly on the corners of each stand, above the stand's legs (it will make more sense as the project progresses). I also designed the top of the stand with an 8" overhang so when the stand is all the way against the wall, there is still room for the dryer hose and water hoses to make their bends without kinking or folding over.
Step 2: Procure Materials
I was lucky to find myself cleaning out a well-lived in home and I came across this scrap angle. Actually, half of that material is a bed frame which is perfect for this project. I pulled out what I could find before the truck left for the scrapyard.
For the legs, I bought a 10-foot length of galvanized unistrut (not pictured). The unistrut measures 1-5/8" x 1-5/8"
For the adjustable feet, I bought 3/4" bolts, nuts and washers. I wanted to use 7/8" because the nuts fit perfectly inside the unistrut legs, but the 7/8" bolts cost over 10x as much as the 3/4" bolts, so I decided to work around the smaller hardware (which will be explained later).
Step 3: Tools Needed
I'm sure I am forgetting some of the tools I have used. I will try to list everything here:
- Flux core wire feed welder. Mine is the cheapest available at Harbor Freight and yes, it is a little messy, but it works like a dream.
- Wire brush
- Vise grips
- Magnet square clamps
- Squares of all sizes
- Welding pliers
- Grinders, the more the merrier
- An assortment of grinding, cutting, wire, and sanding wheels for the grinders
- Tape measure
Let's not forget safety!
- Safety glasses
- Welding mask (another cheap Harbor Freight purchase that continues to work great)
- Long-sleeved cotton shirt and long denim or duck pants
- Leather shoes
- Work gloves
- Welding gloves
Step 4: Preparing and Cutting the Steel
I start by salvaging the most usable angle off the bed frame as I possibly can. I had to cut off rivets and hooks, but was able to get probably 10 feet of good steel out of it.
I use my workhorse as a clamp and I measure and cut, measure and cut. It is a lot quicker and safer to use a cut-off saw, but alas, I do not have one. I get to do it the hard way with a cutting wheel on a grinder. I mark the length, use the square to make my cut line, cut the side first and then the top. Do not bind the wheel! It will blow apart into tiny bits of shrapnel that can easily find their way inside your body.
I cut all the pieces of the frame and the legs at once. Then I used a sanding wheel on the bed frame parts to strip the paint off of the area to be welded. It is possible to weld through the paint, but the bead will be inconsistent and therefore weak. If you take a little extra time to prepare the material your finished product should last forever.
Step 5: Welding the Frame
I find these magnetic squares to be indispensable. I always double-check with a big ol' rafter square to make sure the corners are dead-on. This won't be a guide on how to weld. There are tons out there. Just check out the pictures and try not to make fun of my rudimentary welding skills. I did both top frames first, making sure everything is square by using my rafter square and measuring corner to corner as well.
Step 6: Making the Adjustable Legs
I used a bench grinder to take the zinc plating off the surface of the washers as well as the bottom edge of the nuts. I will come to find later that, with the right amount of current, you can actually weld through the zinc plating to the steel underneath.
I started by welding the nut to the washer, trying to keep it as centered as possible. The vise grips are very useful here. I just put one spot weld on each side of the nut, so 6 spot welds per nut/washer combo.
Next I cleaned up the outer perimeter of the washer to prepare it for welding.
The nut/washer assembly is inserted into the end of the unistrut leg, nut side up. Weld the base of the leg to the washer.
Thread another nut all the way down on the 7/8" bolt. This nut will serve as the locknut. Therad the bolt/nut assembly into the nut/washer assembly (clear as mud, right?) and that completes the adjustable foot mechanism! Be sure to check the pictures if this step isn't very clear.
Step 7: Final Assembly
Time to weld the legs to the upper frame. With the help of the magnet clamps, I was able to square everything up and hold the leg in place long enough to get a couple tack welds on it. Then I would come back finish the weld on the leg. I probably overkilled it a bit, but I welded every seam a had access to.
The cross braces are next. I just cut them all the same length and used my handy magnetic clamp to hold the piece at a 45-degree angle while I applied the vise grips. Tack, weld, and move on to the next one. For two stands, I had 16 of these braces to weld. I'm not even sure they were necessary! When in doubt, I always overkill it a bit.
Step 8: Retainer Cleats
At this point I knew I wanted to add something to work as a last resort in case the washer/dryer still tried to vibrate or walk off of the stand. What I ended up doing is cutting small pieces of angle to wrap around the front corners of the stands. For the back of the stand, I had to fabricate the pieces shown in the pictures in order to accommodate the way the top frame extended past the back legs. Cut, prep, and weld them on. I don't expect I will need them, but I feel it is better to have and not need than need and not have, right?
Step 9: Cleaning Up and Painting
Time to clean up the welds, prep for paint, and paint the stands. Use the wire cup wheel on the grinder to knock off any welding spatter left on the stands. I really only focused on the outside of the stand since no one will see the inside of the stand once it is in place.
Use the sanding wheel to clean up and sloppy welds or high spots on the stands.
Paint selection is really up to you. I went cheap and bought the 98-cent paint and primer at Wal-Mart. The primer was great. It went on smooth and was very consistent between cans. The paint on the other hand, was terrible. It was very inconsistent and runny. I had one can that was literally like white paint thinner, so use at your own risk. Remember, this will have a washer and dryer sitting on it tucked away in a basement or a closet. The paint job shouldn't matter that much.
When the painting is done, you can insert the adjustable feet. Start by threading the locknut all the way down on the bolt. Next screw the bolt all the way into the end of the leg.
Since my stands are going onto a concrete floor, I decided to add some rubber feet to increase the friction a little. Just a little insurance to make sure the stands have no reason at all to scoot across the floor.
Step 10: Completed Project
Time to install the stands. Place them where you want them. Level them front to back and side to side. Lock down the adjustable feet with the locknuts before you place your appliances on top. I would suggest placing the washer first. Make sure it is level on the stand. Next the dryer. Hook everything back up and you should be good to go. I ran an unbalanced load on purpose to get the maximum vibration out of my washing machine and it just sat there solid as a rock. I am excited to share my experience with all of you. Please leave any comments or suggestions below and happy building!
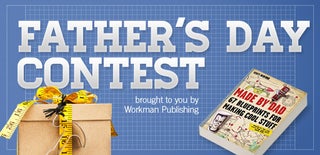
Participated in the
Father's Day Contest
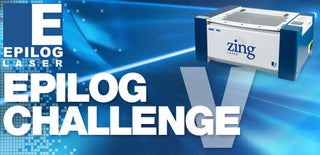
Participated in the
Epilog Challenge V