Introduction: The Junkbots' Sound System
Hi all!
Who doesn´t love music? I consider music as a condiment for life, like salt and pepper, or mustard, or barbecue sauce, even chilli powder it's great in life... Well uh...Anyway, there also many ways to use them just as music has many ways to manifest in everyday life. Although there are many ways to listen it -like buyng a pair of cheap bluetooth speakers- I wanted since a long time ago to make something special to play music and podcasts in situations where my cellphone built-in audio was underpowered -like cooking in the kitchen or when some ambientation music is needed- also I'm an active user of apps like Spotify, Soundcloud in addition to more traditional things like listen from a CD player or an mp3 player.
So I started the last month this project that consist in a stereo amplifier with speakers inside wooden cabinet with an internal streaming device (a chromecast audio dongle, or a raspberry pi with a music oriented distro) and also an external device input port (an ''aux'' port) to play music from other devices such as your cellphone, computer, cd player, vinyl turntable or anything with a 3.5mm audio out.
To add some life and ''flashiness'' to this project I added to the amp an LED VU meter in order to show the rythm (or level) of both signals (Left and Right audio channels), this plus the amplifiers of both channels are enlosed in the body of a happy couple of Junkbots: LR-E (I call him Larry) for the left channel audio, R8-CHL (I refer to her as Rachel) for the right audio channel, too cheesy I know :).
Here is a little clip to show how the system sounds and looks:
So without further ado I'll show to you how the Junkbots Sound System was made.
Let's get started :)
Step 1: Materials and Tools Required
Materials
For the amplifier witg VU-meter circuit:
• 2-LM 386 Low Power Audio Amplifier IC (https://www.amazon.com/Texas-Instruments-LM386N-1-...)
• 2-AN6884 5-dot LED driver IC (https://www.amazon.com/AN6884-Integrated-Circuit-L...)
• 5- 0.1uF Capacitors
• 2-2.2uF Capacitors
• 4-10uF Capacitors
• 2-220uF Capacitors
• 1-1000uF Capacitor
• 2-100ohm Resistor
• 2-220ohm Resistor
• 4-10kohm Resistor
• 2-10kohm 6 pin balance potentiometer with knobs
• 6- 5-Pin Stereo 3.5mm Socket Audio Connector (like this: https://www.amazon.com/3-5mm-Headphone-Audio-Sock...)
• 4- Stereo 3.5mm Plugs used 2 in chrome, 2 in gold knurled style (like this: https://www.amazon.com/Stereo-Housing-Spring-Prot...)
• 2-8ohm Speakers
• 10- Rectangular LED 2x5mm (used 5 in green, 5 in red)
• 2- 5mm basic LED (used blue color, then changed to red)
• 1- 3-position DPDT toggle switch
• 1- 3.5mm stereo cable (since only one side is needed, you can make your own with a 3.5mm stereo plug and some cable)
• 1- Female surface mount usb connector and a mounting plate for it
• 1-Micro USB to USB cable (splited in half, the USB side used to make a USB male to male cable)
• 1-USB Male to male cable (made from a micro usb splited cable and other regular male USB cable)
• 1-USB Power supply (I used a usb power brick from an old cellphone with an ouput of 5VDC and 2A)
• 1-''Breadboard'' style PCB
• Wire (I used wire from telephone cable)
• About 4 inches of enameled copper wire
For the Junkbots (those materials are recycled parts, for more info see step ''Gathering materials''):
• 2 broken 240V 8-pin industrial relays (dimensions: height=~1.5'',width=~1.25'', thickness=~1'')
• 2- small variable coils
• 3-''can'' package or ''metallic'' style integrated circuit (TO-5 or similar to this IC design)
• 1-''can'' metallic transistor (T0-9 package)
• 2-DVD/CD burner unit focusing lens
• 1- spring from one of the 3.5mm stereo plugs
• 4- small potentiometers
• 4- ''vintage'' style resistors
• Many ball point colored sewing pins
For the amp cabinet:
• 5/16 Red Plywood, I used a wood section of 4''by 42'' to build the entire cabinet
• 1'' wood square moulding, used 4 sections 4'' long
• 40 or 45- M3x20mm screws- used 37 in total, but it's better to have some in case you lose some.
• 4- M3x40mm screws (used to secure the Junkbots' base)
• 2-M3x30mm screws (used to secure the side panel box)
• 46 or 51- M3 nuts and washers
• 2- Small 1'' hinges and countersunk mounting screws
• 1- Regular Altoids tin box (used as the Junkbots' base)
• 1-Altoids smalls tin box (used as a side enclosure for the on-off switch and the in/out connectors)
• 4-Small neodymium magnets
• A section of about 10''x6'' of speaker cloth (I used a piece of cloth from an old (and ugly) suit jacket)
• 4- Clear plastic self-adhesive bumpers
• 1- Small self-adhesive velcro dot
Audio Device:
• Chromecast Audio or Raspberry Pi with Pi MusicBox or Runeaudio for streaming, you can also use a bluetooth audio receiver if you don't want to spend on a streaming device. This instructable explains how to install a Chromecast Audio.
Others:
• Solder wire
• Rosin soldering flux
• Desoldering braid
• 1 Can of clear lacquer spray paint
• Epoxy Glue
• CA glue
• Hot glue sticks
• Painters or masking tape
• Electrical tape
• Heat-shrink tubing (used two sizes: ''small''=2.5/1.25mm, ''large''=6.4/3.2mm)
Tools
• Soldering iron
• Desoldering pump
• Digital multimeter
• A breadboard
• A dremel tool with multiple accesories (all accesories included in the dremel 4000 bundle and in the all purpose accesory kit 160pcs, most used in this project: cutting guide and cutting bit, sandpaper disks and drums, wirebrush, cutting disks)
• Cordless drill and drillbits ( 6 or 7 mm maximum drillbit diameter)
• Circular saw
• Jigsaw
• Manual stapler
• Hot glue gun
• 2- 2'' C-Clamps
• Ruler
• Square ruler
• Measuring tape
• Vernier caliper
• Wire Strippers
• Pliers
• Needlenose pliers
• Round nose pliers
• Jeweler's screwdrivers, both phillips and flathead
• Scissors
• Craft knife, utility knife or razorblade
• Cutting mat
Step 2: Gathering Materials (Looking for Some Junk)
In order to make the Junkbots, you'll need for some junk (oviously), electronic junk more precisely so I looked for some pcb boards from old CRT TVs, satellite TV receivers and a couple of broken DVD burner. You can search in junkyards or electronics repair shops in your town, they usually have huge quantities of scrap pcbs and old broken (cool looking though) components, in most cases the owners often are willing to get rid of them and you can get some components for cheap or even for free.
In order to obtain components from old pcb I desoldered them using a soldering iron, desoldering braid and a desoldering pump, it's important to say that whether you are soldering or desoldering you MUST avoid inhaling the toxic fumes from solder, I recommend the use of a fume extractor and do this activities on a well ventilated area.
Mainly I looked for old variable coils (I love these things, they have a nice boxy shape and vintage look, perfect to make heads or junkbot bodies), old resistors, old surface mounted potentiometers and old metallic ''can'' style integrated circuits and transistors (I also love these components, they are shiny and have a nice shape, perfect to make little extremities), also I looked for a big boxy component in order to make the body of each junkbot, at the end I found in a junkyard a couple of broken 8 pin 240V industrial relays, both of them had a transparent enclosure so I considered them perfect for a clear body junkbot allowing the spectator to contemplate the circuit ''guts'' of the amplifier.
From the broken DVD burners I obtained laser diodes, laser focusing lenses (great as junkbot eyes), electric motors, plastic gears and nedodymium magnets, some components are used in this project, I kepth other components to use them in further projects.
The speakers of the sound system were obtained from an old home theater that was taken apart.
Step 3: System Design
I took inspiration from many things to make this project, I wanted to make something that may resemble the look of a vintage guitar amplifier with exposed valves, also I love sci-fi and fantasy films specially where there are bulky and old fashioned robots (like the instructables robot actually! :D), I really like when is depicted how they are built like in Star Wars Episode I where there is a C3PO with exposed skeleton showing a mess of metallic parts and cables.
So I decided to make something that involves vintage audio cabinets with old school robots and I started making some conceptual drawings on how I would like the system would be. I made three similar models of the same cabinet, all with details that I have noticed on guitar amplifiers and old speakers. Finally I decided that the design that uses less parts in its structure was the best option based on the tools and resources that I had available.
The heart of the Junkbots' Sound System is (of course) the couple of Junkbots, LR-E (Larry) that contains the circuits for the left audio channel and R8-CHL (Rachel) containing the right audio circuits, each junkbot consist in a robot made of recycled components and inside of the body (that is a relay clear plastic enclosure) there is an amplifier circuit based on the LM386 integrated circuit and a VU-meter circuit based on the AN6884 ic, all the components of both circuits are soldered like the old school pre-pcb circuits so you'll need some soldering skills (not much, I'm not certainly the best in soldering, just a little patience is needed). The circuits are wired in such a form that all the terminals of the relay pins are used to communicate to the outer world by connecting the relay pins to 3.5mm stereo male connectors, those connectors would be the junkbot legs and each leg is connected to a socket in a base that is described below.
The speaker cabinet consists in a box (a rectangular prism box) made with (5/16'') plywood, it was designed in such a form that the front, back, top and bottom section panels are the same size (4''x8') in addition to the left and right section pannels (4''x4 5/8''), so all the pieces can be cutted from a 4''x40.5'' plywood section. All the panels are fixed with M3 screws and square moulding wood sections except for the back panel that is hinged to the bottom panel in order to make a back access door to have access to the wiring and the internal audio device.
At the top panel is mounted two potentiometers used to control the volume level and the VU-meter sensitivity and the Junkbots base, that consists on a Altoids tin box without the lid that is fixed to the top sections by M3 screws also there are mounted on it four 3.5mm stereo sockets in such a way that the Junkbots' legs fit on each socket, from those sockets come out the comunication cables to connect the Junkbots to the outer world.
At the side panel is mounted an Altoids Smalls tin box without the lid and on it there are mounted two 3.5mm stereo sockets (one for an external device audio in and other used as an audio out to connect headphones. Also there is mounted a 3 position toggle switch used to control on the different power modes on the system:
- Position 1 (Up): Amplifier, speakers and internal device ON
- Center: System OFF
- Position 2 (Down): Amplifier and speakers ON, Internal device OFF
This configuration was made in that form to save the power drained by the internal device when it is unused while the system is used with an external audio input. The power source of the system is a USB 5V brick whih you can connect to the system by a male to male USB cable to a USB port that is mounted on the back door of the system.
For more info about the circuits and wiring of the whole system see the ''Circuit Design'' step below.
Step 4: Circuit Design and Breadboard Test
The circuit of the Junkbots' sound system is relatively simple and cheap to build, it is based in two LM386 low power audio amplifiers (one chip for each audio channel, left and right) and two AN6884 IC which is a 5-dot LED driver that is used to transform or translate AC or DC signals such as an audio signal into logic pulses for LEDs working as a VU-meter.
A VU-meter (that means: Volume Unit Meter) is a device used to represent the signal level of an audio device, originally VU-meters are used to measure the preceived loudness of the tested environment, later on VU-meters were used as a gimmick on audio devices to display the level of loudness of the device more than a measure instrument.
More info about VU-meters: https://en.wikipedia.org/wiki/VU_meter
The LM386 IC is easy to find it is a very common chip with a pretty decent sound output quality that is often used on cheap audio devices like computer speakers, but the AN6884 IC could be more complicated to find so you can find other circuit example to build a VU-meter, even with more LEDs to show a larger sound scale. On my research of VU-meter circuits I found some good examples using programmed micrcontrollers such as the ATtiny 85 using multiplexed signals to drive multiple LEDs. I decided to use the AN6884 IC mainly for the ease of use and the shape of the circuit that I considered ideal for building a compact wired on-the-fly circuit inside a little relay enclosure.
In order to make the circuit I looked for info on both IC datasheets and basically used the suggested application circuits. In the case of the amplifier with the LM386 I built those suggested circuits first on the breadboard and tested the quality of the sound with speakers, changed between different types of capacitors and resistors until I decided for the best circuit configuration that is shown on the attached schematic diagram. For the VU-meter circuit I used exactly the suggested application circuit that I connected in the same breadboard to the amplifier out of the LM386 circuit for both audio channels.
Also I added two extra capacitors (0.1uF and a 100uF capacitor) connected between the positive and negative terminals to use them as decoupling capacitor, that is used to reduce the noise caused by frecuence interference beween all the components. In further steps another decoupling capacitor is added to the 5V power source for the internal device to reduce the annoying wifi signal noise.
More info about decoupling capacitors: https://en.wikipedia.org/wiki/Decoupling_capacitor
Altough in the schematic diagram there are shown four 10 kohm potentiomenters, in the application circuit they are used only 2 potentiometers, but with two channels each (a 6 terminal balance potentiometer) so the levels of the volume and VU-meter sensitivity on both left and right channels can be modified simultaneously.
Here is a little video of the breadboard circuit test:
You can get all the schematic diagrams of this project and IC datasheet here:
Step 5: Taking Apart Some Industrial Relays
Once I get the couple of 240V 8-pin industrial relays I took appart them by removing the coil and the terminals with help of a screwdriver and a soldering iron in the soldered joints leaving only the clear plastic casing and the terminal base.
Then I measured the enclosure to determine how big the inner circuit will be, also I trimmed some sections of enameled copper wire to lenght equal to the relay enclosure inner height, then the enamel insulating coating was removed with a knife and sandpaper in order to have full conductive surface in the wire. You can test if a surface is conductive using the continuity tester of a multimeter.
Those four copper are the positive and negative rails of the inner circuit of each junkbot, just as is in a common circuit breadboard. And each wire will be soldered at different pins of the relay base by the time the circuit would be fully assembled.
Step 6: Soldering the Amplifier Circuit: Left Channel (Larry)
The amplifier circuit of each channel is soldered on the fly without using a pcb, in order to do that it was soldered all arround two copper enameled (and then removed enameled) wires, which are the positive and negative rails, just as the power rails on a prototype breadboard.
In order to achieve good soldered joints I recomend:
- Use rosin flux paste on every connection that will be soldered in order to ease the solder to melt and sitck to the desired surface.
- Melt some solder in each lead that will be soldered before making a junction, doing this is easier than try to add solder directly from the solder wire.
- The continuity tester of the digital multimeter is your best friend in this part, always check if your soldered connections are good enough to go ahead into the next part to solder.
- Use binder clips and painters/masking/electrical tape in order to fix the components in place and make easier the soldering process, specially at the begining of the process. In case you don't have helping hands like me.
- Have patience, remain calm and take your time when soldering this way, if you fail don't worry or get frustrated i'ts just a matter of practice. It helps though as a moral support to have some spare components in case something fails (I had to use some extra capacitors when I trimmed too much one lead soldered to a wrong pin).
I started by soldering three little wire hooks (those hooks were shaped with round nose pliers and needlenose pliers) into the pins of the LM386 that needed to have direct connection with the power rails (pin 2 and 4 to groun rail, pin 6 to positive rail), then these little wire hooks were soldered into the power wire rails.
Later on a 0.1uF capacitor soldered to an output cable was connected to pin 3 and the other terminal of the capacitor into ground. Next a 220uF capacitor was soldered to pin 5 of the chip by the positive lead, to this lead it was soldered a 0.1uF capacitor with the other terminal connected to ground.
Finally a 10uF soldered to a 10kohm resistor by the positive lead of the capacitor was soldered by the resistor side into pin 7 of the LM386 and the negative lead of the capacitor was connected to ground.
The amplifier circuit is done, now let's solder the VU-meter circuit...
You can get the soldering aid diagram here:
Attachments
Step 7: Soldering the VU-Meter Circuit: Left Channel (Larry)
To make the VU-Meter circuit, first a row of LEDs was made by soldering all the positive leads to a 100 ohm resistor to make the common anode of the LED display (to make a clean, sorta-of-straight LED linear array it was used painters tape to fix all LEDs), then that row of diodes was aligned and soldered to the AN6884 pins (pin 1 to pin 4 and pin 6, please leave pin 5 alone, it isn't a LED ouput for some weird reason).
Then the array of LED plus the AN6884 was measured over the relay plastic enclosure and on it was removed a plastic section with a boxcutter to make enough room to fit the LED array.
Next the 100 ohms resistor of the common anode was soldered to the positive rail (at the tallest point of it) of the amplifier circuit. Folowed by the connection of the pin 5 to the ground rail by a soldered wire.The pin 9 of the chip was connected to the positive rail of the amp circuit with a soldered wire.
An array of a 10uF capacitor connected in parallel with a 10kohm resistor was soldered to pin 7 by the positive side of the capacitor, the other end (the negative side) of the capacitor was routed to ground. After that a cable was soldered to pin 8 in order to route it to one of the relay's enclosure base pins.
Finally, the chunk of components was tested for fit inside the relay plastic enclosure.
You can read some tips about soldering and get the soldering aid diagram on the previous step.
Step 8: Soldering the Amplifier Circuit: Right Channel (Rachel)
This is basically the same process explained on the step ''Soldering the amplifier circuit: Left channel (Larry)''
In that step you can read some tips about soldering and also you can get the soldering aid diagram pdf.
The order of the components differ a little in this step: The ground wire hooks used to connect pin 2 and 4 to ground were soldered before soldering the wire hook to pin 6.
Step 9: Soldering the VU-Meter Circuit: Right Channel (Rachel)
This step shows the same process depicted on the step ''Soldering the VU-Meter circuit: Left channel (Larry)''
It differs from the provious step in the order of the soldered components, in this step the cables that are soldered once the LED array (that contains five red LEDs) is soldered before attaching the wole thing to the amplifier circuit, this was made in that way in order to ease the acess of the soldering iron in such a reduced space.
If you want to read some tips about on-the-fly soldering and get the soldering aid diagram, please check the step ''Soldering the amplifier circuit: Left channel (Larry)''
Step 10: Junkbots' Anatomy: Trunk and Legs
After soldering all the components of the amp and VU-meter circuits, all the in/out and power rail cables were soldered into the pins located at the relay base, then the transparent casing was placed to protect the circuit from external elements. This element will be the base-trunk of a junkbot. Each Junkbot mini-trunk was tested on the breadboard to ensure that everything worked like a dream, a noisy, it was a flashy red and green dream actually :D.
The legs of each junkbot has to functions: being the legs of the junkbot (duh), and being the connection link between the inner audio circuits and the outer world. This was possible by using 3.5mm stereo plugs as ''legs'', altough the wiring is the same for both junkbots, there are minor aesthetic differences: for the left channel junkbot it was used a chrome metallic stereo plug type with green connection cables as legs, for the right channel junkbot it was used a golden metallic stereo plug type with red connection cables.
Each plug sleeve was modified with a dremel tool abrasive disk in order to make enough room for the connection cables. Then each stereo plug was fixed to the junkbot trunk using epoxy glue. Once the epoxy glue was fully cured each cable was soldered to every connection pin of the relay base.
See the attached images for more info about wiring the leg-plugs and the trunk-relay.
Step 11: Junkbots' Base
The base that holds up the coupe of junkbots it was made out of an Altoids tin box. The main reason of using a tin box as a base for the junkbots was because the threaded sleeve of the stereo sockets was too short to surface mount it in a 5/16'' thick plywood panel. Since Altoids boxes are a commmon item and since I have a lot of them, I decided to use one to make this project, I liked the look that has the base, it resembles the old exposed transformer amplifiers and are easy to machine.
First the tin box was taken apart and all the labels and paintings in the box were removed using a dremel tool with sandpaper disks and a wirebrush bit.
Then, the box was measured, the mounting holes and the stereo sockets were marked with a permanent marker to carefully drill the holes. Next, the stereo connectors were fit-tested on each hole of the box.
Once the holes were made, the box was sanded and polished to prepare it to paint to prevent rust on the tin surface. The tin box was sprayed with clear spray laquer. And while the paint was curing, I soldered and labeled with tape all the cables to the nessesary terminals of the stereo sockets and when the paint was fully cured, I installed them on the tin base.
Now the base can hold both junkbot assemblies. :D
Step 12: Junkbots' Anatomy: Arms and Heads
Each junkbot arm is an old resistor fixed with CA glue to a little potentiometer, the cool thing about using a potentiometer as shoulder is that you can move the entire arm by twisting the potentiometer. Each potentiometer-plus-resistor arm was glued with epoxy to the junkbot trunk, for this I fixed first the two left arms tilting horizontally the entire junkbot base to avoid the fresh epoxy to bleed vertically. Then when the epoxy from the left arms fully cured, the two right arms were fixed in the same way.
For the junkbot heads I used a variable coil glued to a metallic integrated circuit with trimmed pins that is the junkbot neck. The eyes (or eye) of each junkbot are a dvd burner focusing lens fitted and glued to the bottom part of the variable coil.
In order to provide some distinction and personality between LR-E and R8-CHL I added some unique features. LR-E has a ''hat'' that is a metallic big integrated circuit glued with CA glue into his head. R8-CHL has long ''hair'' consisting in a spring from one of the stereo connectors that was taken appart in the legs step glued to a metallic transistor that is fixed to her head. Also R8-CHL has a cluster of ''baloons'' fixed to her hand, this will be explained in the next step.
Step 13: Baloons and Breadboard Test (again)
To make the baloon cluster that Rachel holds with her left hand, I used many colored ballpoint sewing pins, that were glued one by one with CA glue. I started with some hole pins, then I removed the plastic balls from the metallic pin to add more volume to the balloon cluster. Once the baloon cluster was big enough I soldered a wire to the pin ends and then soldered to Rachel's left hand.
This was the final detail of the Junkbots' assembly, everything in the circuit is inside each junkbot with the exception of the control potentiometers, the in/out sockets, the on/off switch, the decouplig capacitors and two 2.2uF capacitors from the VU-meter that must be too close to the potentiometer.
Once the Junkbots' were assembled, I made another breadboard test now connecting the base wires to the remaining components in the breadboard.
Here is a little video of test:
It worked!! Let's leave as it is while the speaker cabinet is done :D
Step 14: Side Box
The side box used to hold the on/off switch, the audio in and headphone sockets was made out of an Altoids Smalls tin box, and the process is basically the same as the Junkbots' base, the lid was removed and the box was cleaned with a dremel tool, then it was drilled and painted with clear laquer.
All the side mounted components were installed, the two 3.5mm stereo sockets and the DPDT switch were soldered with wires. In order to make a visual indication of the two different swiching modes of the system two LEDs were connected into the swich terminals and a common ground resistor. At the begining those switching indicator LEDs were blue, but in advance they were too bright and at the end they were changed to traditional 5mm round red LEDs.
Step 15: Cutting and Pre-assembly of the Speaker Cabinet
The speaker cabinet was easy to make because almost all the wood sections were the same size and all of them were trimmed from a long 4x42 strip of 5/16'' thick plywood section using a circular saw.
Once I cutted all the plywood sections, each part was sanded in order correct all the defects and ease the assembly of the cabinet.
Then the front speaker pannel was marked with the circular shape of the 3'' speakers. I used a reel of painters tape that surprisingly had an almost identical diameter of each speaker. Once all the shapes were marked, I made the speaker holes using a jigsaw starting in a tangent hole previously drilled into the wood section. Each speaker hole shape was then rectified using a sandpaper drum bit of a dremel tool. The circular holes made were not perfect, but since there is a cloth in front, the shape of the holes is rarely noticed from the outside.
The frame of the speaker cabinet was made using 4 sections of 3 1/4'' long 1'' side square moulding as a structural reinforcement. Those sections were fixed from the inside of the cabinet with M3 screws nuts and bolts. All the holes for the screws were drilled 3/4'' from each edge from the outside of the cabinet.
Finally, when the cabinet frame was assembled, the front and back panels were fit-tested into their respective position. I used sandpaper to rectify any mislocation mistakes. When all the components were nicely located, the frame was taken apart in order to machine all the remaining mounting holes.
Step 16: Mounting Holes Machining and Painting
The top and side sections were modified in order to hold the Junkbots' base and the side box respectively. First the mounting holes for each box were centered and marked and drilled over each plywood panel, then bigger holes were made in order to introduce all the cables from each box. For the big holes on the top panel a 1/2'' cutting drillbit was used. For the side cable hole it was used a drill for the starting holes and then a dremel tool with a cutting flute bit and a cutting guide to enlarge the side hole.
Also the potentiometer holes were drilled and the plywood was machined in order to mount the potentiometer through the 5/16'' thick plywood, this was posible by using the dremel tool with a cutting bit and the cutting guide just like a router tool.
At the back plywood panel it was mounted a USB side mounting socket from an old computer, the mmounting plate was too long because it could hold 2 USB sockets so I cutted it with a pair of metal shears and then drilled a new mounting hole at the plate. The mounting holes for the plate were drilled into the back panel and then the USB connector shape was marked into the plywood to finally cut the marked shape with the dremel tool with the routing configuration. The plate with the usb connector was installed into the plywood with M3 screws.
After this, I installed two small hinges between the back plywood panel and the base of the cabinet. To avoid mechanical interference between the hinge's elements small countersink screws (included by factory in the hinges) were used to flush-mount the hinges at the base side. M3 screws were used to secure the back panel.
Finally I painted the cabinet frame and the back door panel with a several coats of spray clear laquer. I love how color of the plywood changed into a glossy red color after all this :'D.
Step 17: Making the Front Speaker Panel
The front speaker panel was drilled to hold the mounting screws to fix the speakers. Then a counterbore hole was machined with the dremel-router tool in order to have a flush surface finish when fixing the speaker cloth.
All the speaker and mounting screws were fixed with CA glue to stop them from falling. Be careful and wait until the CA glue fully cured, I said this because I didn't wait enough time and when the speaker cloth was placed and stapled, the fresh CA glue stained and ruined the speaker cloth. :(
The speaker cloth was made out a piece of fabric from an old suit jacket I liked the color conbined with the plywood tone. The piece of fabric was cut to lenght (the piece of cloth was about 10''x6'') and stapled into the speaker plywood panel. As I explained earlier, I ruined the first stapled speaker cloth with a CA glue stain, so I had to remove all staples and put a new piece of cloth instead.
Finally the speakers were fixed into the front panel and now you can attach it to the cabinet frame.
Step 18: Wiring Preparation
Before wiring all the elements of the system, some things were made:
- The Junkbots' base was secured into the speaker cabinet frame with M3x40mm screw, all the cables from the four stereo sockets were routed though the big holes previously drilled into the top panel.
- The 2 potentiometer shafts were trimmed with a dremel tool cutting disk in order to lower the potentiometer knob, later I discovered that the dremel cutting vibrations broke one of the internal components of one potentiometer so, I had to replace both potentiomenter to new ones :(.
- All the terminals of both potentiometers were soldered into long wires (about 15-20cm long)
- The plastic insulation from the USB socket was removed, for this project we only needed the positive and negative wires (red and black), later on I cutted the other cables (green and white cables).
- A mini USB cable was cutted in half (or less that that, the short side was the micro USB side)
- I made a long USB male to male cable out of the other end of the previously cutted micro USB cable and other cutted USB cable. This long USB cable was used to connect the system to the power source.
- A 3.5mm stereo cable was cutted and all terminals were stripped and tested with the multimeter to know which channel was each stripped cable (altough there are color codes for this, sometimes manufaturers does not respect the color, in this case the white cable was right channel and the red cable was left channel).
- All the wires were labeled with tape, this will be very usefull, because believe me, there will be a mess of cable and is easy to get confused without actual identifications.
- To wire all the components, I used a prototype pcb that was cutted in half with a knife to fit it inside the speaker cabinet.
Step 19: System Wiring
The use of labels on each cable makes a LOT easier the wiring task. You just search for the same name label, solder each end, and isolate the joint using heatshrink tubing. That's basically the wiring process, I used a smal prototype pcb to make the indirect connections.
I wired the system in this order:
- First, the usb power source positive terminal was connected into the switch common pins. The negative terminal was connected to the ground rail of the protoype pcb, the power rails of the pcb were jumpered both negative and positive rails in order to have more connecting area of the power rails.
- Next all the ground cables were soldered into the pcb negative rail, followed by connecting all the positive leads of the amplifier into the positive rail of the pcb.
- All the terminals of the 3.5mm stereo cable (left, right and ground) were soldered into different rails of the prototype pcb, to make the connections in the most intuitive way I connected all the left cables at the left side of the prototype board, and all the left channel cables into the rails of the right side (even I marked ''L'' and ''R'' on each side of the board).
- I soldered the cables from the switched audio imputs into the same left and right rails where the 3.5mm stereo cable was soldered.
- The other left and right cables from the audio IN socket were soldered into the volume potentiometer terminals.
- The other terminals from the potentiometer were soldered into the Junkbots' volume terminals.
- Both VU-meter terminals from the Junkbots were soldered into the VU-meter potentiometer.
- The Junkbots' amplifier out terminals were soldered to longer cables and soldered to diferent rails of the prototype board.
- The cables from the switched terminals of the headphones socket were soldered into the same rail of the amplifier rail.
- Then the VU-meter potentiometer cables were soldered into two rails near the amplifier out rail.
- Between the amplifier out rail and the rail of the VU-meter a 2.2uF capacitor was soldered (the negative side was soldered into the amplifier out rail) for each audio channels.
- Two decoupling capacitors (a 100uF and a 0.1uF capacitor) were soldered between positive and negative rails of the prototype board.
- The micro USB cable was soldered, the negative cable was connected to the negative rail of the board and the positive cable was connected to the internal device swithched pin cable.
- The positive terminals of each speaker were connected to the cables soldered to the headphone IN remaining terminals. The negative terminals were routed to the ground rail of the board.
- Another decoupling 1000uF capacitor was soldered between the positive and negative rails of the internal device power supply cable.
- The blue LEDs installed in previous steps were replaced with traditional red LEDs, each cathode was soldered into a 220ohm resistor and routed to ground.
- The side box was secured with M3x30mm screws.
- The finished prototype board was fixed into the speaker cabinet with hot glue.
Once the wiring was done, the front speaker panel was fixed to the cabinet with M3 nuts, I added the potentiometer knobs and the junkbots were placed into their base.
Step 20: Last Details for the Speaker Cabinet
Before installing the Chromecast audio in the system, I added some little things to the cabinet.
- I made a little ''knob'' for the cabinet back door to easily open it from the outside, I drilled a hole at the center and at 3/4'' from the edge of the back panel, then I fixed a screw with four nuts to provide enough grip to the user.
- Four neodymum magnets were glued to the back door and the contact edges of the cabinet to lock in place the cabinet door. Those neodymium magnets are recycled from an old dvd burner.
- Four plastic bumpers were sticked to the cabinet base in order to raise and lock in place by friction the device in addition to protect the holding surface.
Step 21: Chromecast Audio Installation
The Chromecast Audio was fixed at the center of back door panel using small velcro pads, then the micro usb and the audio input cables were connected.
By using the swicth at the side of the sound system you can turn on/off the device, once you have turned on you need to configure via the product's website:
- To configure the Chromecast Audio using Google Chrome please go to: https://www.google.com/intl/en/chromecast/setup/
- Select ''setup your chromecast using this computer''
- Wait until your computer detects the device
- Click ''Set me up''
- Select your Wi Fi acces point
- Click next
- Make the confirm sound test, then click yes
- Write the Chromecast device name
- Select your wireless network and write your password
- Click Next
- Now you can stream audio contents from your smartphone by selecting the ''cast to'' button in Spotify, Soundcloud and more! The Chromecast Audio device can be configured via the Google Home App
For other devices you can visit: https://support.google.com/chromecast/answer/62606...
Here's a little video of the system working with the Chromecast Audio device:
It worked, it was a little hum from the Wi-Fi interference, but it sound pretty good. :)
Step 22: Final Toughts and Follow Up
This was a very fun project to make, it was a bit challenging but it was worth it. I love how each Junkbot has it's own personality and unique style that harmonizes with all the different materials of the speaker cabinet. The VU-meter gimmick gives the project a nice visual hypnotizing effect that I could look at for hours and hours. The audio quality may be not the best, but it works just fine for listening podcasts and listen music in everyday situations.
I'm working on the raspberry pi implementation of this system, that is basically the Raspberry pi board with a software oriented to music media like PiMusicBox, RuneAudio or Volumio. I want to make a benchmark comparison between each audio apps to determine wich one is the best tor this system. I'll update those changes in the near future.
Here is a video of the system working with an external audio device:
[Reproducir video]
I want to thank my brother for helping me in different situations through this project like in the circuit design, trouble shooting, and specially for driving me too many times to the electronics store each time I needed some spare parts.
And finally I want to thank you, reader, if you get into this point, I'm sorry for the writing mistakes and the blurry photos. I hope this instructable inspires you to try to build someting alike, it is a fun and interesting project to make, do not get intimidated, just take it easy and try it worth it :).
If you have any comment, doubt or question please comment down below.
See ya next time and thanks for reading! :D
Andy_Fuentes22 - November 2016
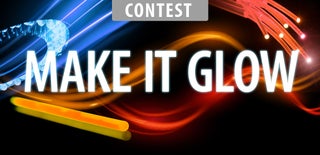
Participated in the
Make it Glow Contest 2016
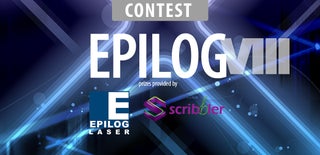
Participated in the
Epilog Contest 8
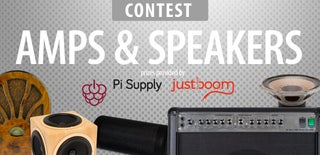
Participated in the
Amps and Speakers Contest 2016