Introduction: Timber Minions
After doing the lego men for the Easter show last year, although it didnt place, I saw the excitement from people as they saw something fun rather than just another well made truck. So it got me thinking what else would be fun. After looking a minion picture one day I realised that they are basically all round, therefore can be turned :)
There are some challenging parts but room for creativity and a good challenge making them. Here is how I made them...
Step 1: Design
These are the 3 main minions from the movie. I started by taking these 2 sets of photos to get some rough sizes. Based of the different sizes of huon pine which was my base timber I was able to set up a scale. Conveniently it was 2:1 of the picture. Start by writing down important measurements over the page to constantly reference. Check that you have all the suitable timber too. All the basic shapes are quite simple, you just need to work accurately.
Timber selection is always a key point in my work. The difference nice timbers can make in a work is huge, even if it is at a bit of an extra cost. The body is huon pine which is one of Australia's nicest timbers. I chose it for the yellow colour, even, tight grain and I had some in varying sizes. Walnut for the dark sections as its another great timber, with good turning and carving properties. For the blue sections I needed a timber with strong grain but also light in colour. Timber that I could get in solid and veneer. Oak seemed to be perfect. Fortunately oak and walnut are both timbers we use at work so easily accessible. Timber for the glasses was another timber I had to consider. I sprayed them with paint but i still wanted to see the grain. I chose Tasmanian oak as it is strong grained across the growth rings and had a bit more texture and better turning properties compared to radiata pine.
Step 2: Body and Eye Band
I already had some huon pine at 60x60, 70x70 and 90x90 however I did not have any walnut at that size and I wanted the grain to head in the same direction. I found some walnut that I had dressed one side to ensure a flat surface. I cut the pieces to the largest size and then glued them together in the vice. It makes a great clamp providing you dont need to use it for a bit. I find that it only needs to be in clamps for a bout 10 min, just enough for the glue to tack and then it wont go anywhere providing its not bumped or hit. I then glued to a waste block for cutting on the saw. I could have used a bigger piece of walnut but this saved wasting good timber.
I marked out the sizes of the huon sections, top and bottom and made a cut on the drop saw. I marked it with a line so that the grain lines up when reglued. I also used the drop saw to cut my walnut. Once again, I used my vice and other clamps to glue up the sections. Where the walnut was over sized, I cut it down on the band saw.
Mount it on the lathe using the 4 jaw chuck. To better secure it you could put it between centers and turn a tenon to get a great grip but I didnt allow the room on the top section for the point of the tail stock. You may need wider jaws too for the larger ones.
Rough it down to a round blank using a roughing gouge. The measurement of the eyeband and the base of the body is the same diameter and also your widest point so start by turning that. Using a parting tool and a set of calipers, set that dimension. Use the parting tool to then shape down the sides of the eyeband on the pine sections. This will be only about 4mm in diameter smaller. To shape the eye band, I used a point tool and a small skew chisel. Use the point tool to create a v groove in the center, approx the same diameter as the side of the eyebands. Then use the skew to round over the edges to create an even curve each side.
Now using a larger skew or a gouge, depending on your preference, you can shape the top. A detail gouge is the easier of the two options, however if you have the ability to use the heal of the skew to roll it over, you will get a cleaner cut. For the main section there is a slight straight taper. Shape this with a gouge or a skew chisel doing a planing cut (45 degree angle to the piece and toolrest).
Remove the toolrest and sand it all going though the grits. I used 120, 240 and 400 grit. After its all sanded you want a small tenon to center it to the base. I used a spanner to get my exact 12mm because a set of calipers can get minor variances, where a solid spanner will not. While parting this down, make sure it its flat or if anything slightly undercut so the base sits well. Then you can part or cut the body off the lathe.
Step 3: Glasses
I did an experiment piece before I started these. To drill the holes I used a forstner bit in the drill press. Although I though I was holding it firm, it wandered. Pics 1 and 2 show the gaps that are left when the eyes that were a tight fit go in. I had to make a jig to make sure this wouldnt happen.
The jig was fairly basic with 3 larger blocks screw to a a piece of ply. This set a stop on top and limited movement side to side. One smaller block with a screw though it on the bottom to screw into the base of the body to really lock it in place. Fortunately, it worked perfectly. To adjust it for the different shapes, just move the blocks (pic 6-7).
To mark of the positions of the hole find your center. Find this by lining up the grain of the timber. Have a line down the center of the eye band and mark the distance of the radius from the edges of the band (pic 5). This will give your centers. When drilling, the point should sit in the groove of the band. As the eye band is the same diameter as the base, you should need to pack it up for a straight hole but I decided to raise it a fraction for the big one (pic 11).
The turning for the eyes is simple but has to be done accurately to get a perfect fit. I did redo 2 to get it just right. Have a waste block with then same diameter hole to check your diameters for a good fit. You dont want it too tight but a gap will be clearly seen. Using the jacobs chuck and a forstner bit, drill out the center. Give it a light sand to 240 grit. You dont want cross sanding but you also dont want to fill the grain with dust.
For the one eyed minions, this step is irrelevant. Sanding the sides of the eyes so that they both go in because of the overlap. Mark your left and your right glasses for consistency. Put one in and mark where the points of contact are (pic 16). Mark a line that should look like a curve from the side (pic 17) but should look straight when looking directly from the front (pic 18). Use the sander to remove inside this line bit by bit. Dont to it all at once. Better to under do it and have to remove more as you go. Put a small screw in and sand them flush on the sander, marking how much you want them to be set out. When the are flush you can take them out for painting.
I just used a can of silver spray paint. This give an even and light coat. You only want one coat so that you do not fill the grain. Start by spraying the inside as it is the hardest spot to get. Should get it all from 3 angles. This will naturally get the top and some of the sides. From a low angle, spray the rest of the sides.
Step 4: Eyes
As I found for the lego men that I made. These plug cutters make excellent punches to shape circles. With a solid surface below, place the veneer on and hit the cutter with a hammer. As it is not a full circle, it will leave a tab that can be removed by realigning and repeating. This works for varying sizes. I was not able to get the bigger sizes though. Using the forstner bit I was able to get the larger shape, also a perfect fit to the glasses. As a forstner bit cuts first with the center for location, it then nexts cuts the outer of the shape for approx 0.3-0.5mm deep. This was enough to cut the shape of the eyes with out removing the entire hole providing you cut with a gentle hand. Lightly sand the edges to remove slightly frayed edges. They can then be glued together using a small amount of glue, focused in the center but lightly on the edges to prevent the need for excess clean up.
Step 5: Pants
Similar to the walnut eyebands, I needed to laminate to pieces together to get my sizes. After the glue had set, I flushed one side on the sander. Chances are it wont be perfect as the edges round a little bit but get it as best as possible. Use a straight edge of a ruler to check. Mark out a diameter approx 5mm bigger than you need and cut that out on the band saw.
I mounted this with a hot glue chuck. Yes, it is a strong enough hold for small pieces, providing you do not use a heavy cut or have a bad catch. I use a was block of a soft timber. Often I use red cedar off cuts. Chuck it and shape a flat surface. Use three to four small blobs on the piece and glue your blank on. Give it a quick spin by hand to check center. You only have a few seconds to shift it if it out. Apply pressure on it to spread the glue, ensuring it sit flush.
Using the jacobs chuck in the tail stock, drill a 12mm hole to match the tenon on the body. Using the parting tool, flush off the top or slightly undercut it if you have to. You can now reduce the diameter to be just over 1mm bigger diameter than the body, 0.5mm bigger each side. You want the step so when the veneer of the overalls goes on, that lies flush. Remember to account for sanding, depending on how clean the cut is. Test it as you go with a piece of veneer.
You can now start to shape the bottom from that set diameter using gouges and skew chisels close to the waste of the glue chuck. Try to remove as much as you can. Using a standard woodworking chisel, pry the piece of the wast block. Depending on the amount of glue, this can be easy or hard, but remember, damage the waste block if you have to.
Using a different waste block, normally something a bit harder that the cedar, like radiata pine, make a jam chuck. This is a piece with a 12mm tenon that the oak can be forced onto. (pics 15-18). It should be tight enough that the piece should hold for light cuts. You can add pressure of the tail stock with another was block to prevent markings from the centers. Finish shaping the sides, leaving a flat spot for the legs.
Step 6: Legs
The legs were another piece that could be easily shaped on the lathe. Rough it down to a round blank, set the large diameter and mark your height. Drill out the middle with a 5mm bit and then set your small diameter at the bottom. Using a detail gouge, create and even flowing half cove between your set diameters. Sand and part off.
The legs will end up fairly spread apart but you need them close together. Sand a flat spot on one edge. You may as well choose the worst edge to remove any small errors. Dont quite sand them flush because you still want only a small gap. The test to see how accurately you turned is the flat spots should be the exact same shape and when they are together there should be no step.
Step 7: Overalls
On your sheet of veneer mark out the sizes of the rectangles. Cut away from the line so that when you sand it you get your full size. With the sander, move the table as close as possible to the disc. Mine is home made so that is easy but if you need, put a timber block there. The closer it is the less chance of break out.
Step 8: Staining
This was a bit of an experiment for me as I went. I have used a few different pigment stains at work but dye stains are a little harder to use. Normally with a stain, wipe on with the rag dipped in stain and then wipe off with a clean rag. Do an entire surface at ones to avoid tide marks.
I had a bit of a problem. Although the veneer and solid were both oak, the solid was more yellow in colour as seen in pic 1. This meant that I got blue overalls and a greenish tinge to the solid. It was not a great contrast. Through experimenting I added more stain by dipping my pieces to really fill the piece with colour and not wiping it off. The difference is seen in pic 3. By a few coats of stain i was able to choke it up so I had a similar colour. There was going to be a slight difference but I got it close
Step 9: Main Glue Up
Gluing the legs to the base is as simple as putting a bit of glue to the inner section of the legs and positioning them to the base. By pushing them firmly in place, the glue spreads and I see no need for a clamp. This also saves them from being shifted from clamps.
When the legs dry, glue the body to the bottom. I did use clamps on this because of the tenon that had to close to get a clean joint.
The overalls were a bit more challenging. Using a flexible tape measure, measure the circumference of the piece and deduct the size of two overalls. This give your spacing that you also divide by two. Glue this in place accurately. The more they move, the more glue marks that you will need to clean. Position them central to the front and back. To hold them in place, masking tape is normally a good option however, you cant exactly see where the piece is and you can clean up. I used rubber bands doubled over. For more pressure add more bands or double over another loop
Step 10: Overall Straps
No going to lie. This was the hardest part. I broke a lot of pieces. I chose the grain direction to go across for strength. Too many broke along the short grain with my methods of shaping. These also broke a fair bit too but I got there with perseverance. Accurate measurements between overalls in important for a need finish. From those marks you can draw you shape on the veneer. Using the edge of a belt sander and the disc sander I sanded to the lines. After a light sand, I stained them. The reason why I shaped them before staining, compared to staining an entire sheet was to make sure i got colour on the edges.
Once again, I used rubber bands to glue these on. Only do one side at a time as the are fiddly to get in place. They look like they are held hostage at this point :P
Step 11: Shoes
This step can be done mainly on the lathe with final touches done on the sander. The toe is one of the easiest spot to reference your measurements. The other section is partially determined by the size of the bottom of the legs. You want them to be wide enough for a clearance hole and have strength but not too big to stick out from the legs. A small radius between them will blend the two sections. After turning this shape and sanding it, mark a center line as seen in pic 4. Carefully with a jap saw, cut the piece in half. If it is cut accurately, you have two shoes, however if the cut is uneven, dont be too fussed. They are small and easy to make the second.
On the sander, shape both sides to be flush with the toe and sand a flat spot on the top to give a square shape. Sand a small radius on the back corners and drill a clearance hole in the center of the top.
Step 12: Plinth
The plinth was a last minute design change. I realised that the were a bit top heavy and would easily fall over with out it. I didnt wan to risk them fall over and breaking an arm.
Back to the hot glue chucking. The cedar scrap was easy for the oak as removal would damage the was block not the desired piece. Cedar on cedar creates an equal chance of damage on the final piece. I technique that I only use for small pieces is putting some painters tape on the good piece. This allows for easy removal with out damage. However easy removal can mean flying timber. To minimize this, shape tools and gentle cuts. If you can work towards the center rather than away.
Also drill some clearance holes with the measurement based off the position of the legs on the bottom.
Step 13: Assembly
The clearance holes (4.5-5mm diameter) are already in the legs, feet and plinth. Drill a pilot hole (3mm) into the bottom through the legs. The screws will drop into the clearance holes and the pilot hole will be a starter for you to use the drill to screw them together. Its fun to place the eyes in loosely to see your progress.
Step 14: Arms
You want the arms to be central to the overalls and close to the strap to give the appearance that the arm is holding it up. For a 6mm diameter arm, I had the center 4mm down. Use a doweling bit to drill these holes. They give a cleaner cut compared to a twist bit as it cuts the edge before removing the bulk, similar to a forstner bit. Your angle will be limited by the center points contact and where the edge cuts. Always keep the center in contact for a hole that will not drift.
Turn the timber to match the holes. It gets thin so only take light cuts with the gouge. As you part them off, chamfer the ends to help guide it in the holes.
Put a small dot of glues in the holes and knock the arms in with a hammer. After determining the depth of holes in your hands, mark and cut them to length with the jap saw. With some 120 grit abrasive, sand a chamfer on that end too.
Step 15: Mouths
To design these, it need to go with the character of the minion. Loosely put the eyes on to get an idea of the expression and make a mouth to suit the minion and the timber. Pic 3 shows a small knot that I wanted to cover up with the mouth. The mouths were fairly easy shaping like the rest of the veneer. Draw them on the veneer, rough them out with a stanley knife and then sand them.
Step 16: Hands
These would be the second hardest part of the job. The turning was easy and the rest was experimenting with tools till it worked.
For the turning you want the wrist collar and the hole to be central. Thats why I started on the lathe. Fairly basic turning. Make sure you leave plenty of room for the carving, especially the open palmed hands. Dont limit yourself too much.
I then did some basic shaping on the sander, creating different flat spots. From there a made cuts with the jap saw and carved v grooves using those cuts to center. Then I rounded the fingers with a small carving chisel and sanded them to shape. The are awkward to hold and shape but somehow I got some shapes I was happy with. There were also others I threw away.
Step 17: Hair Holes
The first one was simple. Mark the hole with a pencil, then a brattle, then drill a 2.5mm hole. The other one had a bit more work. Do the same marking then drill 1mm deep straight down. This give a spot for the drill bit to sit. Then angle the drill and drill a hole so that the two will meet in the center.
Step 18: Clean Up
The blue will end up on your hands from handling. That then will easily spread to the pine. Sand the job well on any spots where there is smudging. It will show quite obviously when lacquered. I had to re-sand some parts after the first coat. Also clean up glues marks, especially around the veneers.
Step 19: Finish
A lacquer finish is ideal in comparison to oil finish due to the stain. This seals it off and prevents the spread of stain as long as you start with light coats. Thick coats will have more thinners, possible causing the stain to reactivate and run. You can use it out of a can, like I did for the eyes however I had access to a full spray booth at work. I did use the can on the veneer eyes because the force of the full spray system would blow them away. For items like the feet, use a nail board to stop them from blowing away. Apply 3-4 coats, cutting back the lacquer with a fine grit sponge just before the last coat.
Glue the glasses down with a small bit of glue and put the small screw back in. Make sure the screw is flush so the eye sits well. Then with another small bit of glue put the eye in. You get 1 shot because it wont come out due to the exact fit.
Step 20: Hair
I was going to get some black wire from bunnings however I could only find some that was too thick. So I wandered around the random isles that you would never normally check and found this. It keeps leaves out of your gutters and had perfect black lengths at 1mm diameter. I cut some off with a stanley knife. To glue these in, I put some glue on a waste block and dipped the ends in the glue. Carefully I placed them in the hole, not to spread any on the top. You only need to put glue on the first few so the hole is not over filled. For the one with the hair going to the side, I just bent the ends in the bottom 5mm. To get a nice even finish, give them a hair cut using a pair of scissors. Vary the lengths a little to make it more interesting.
Step 21: Done :D
There are only a few little things that I could improve on by working a bit more accurately. I would also try and seal the blue parts as soon as possible to prevent the amount of clean up. Apart from that I am stoked how these went.
Hopefully there is someone out there slightly crazy enough to try making these. I would love to see someone elses take on these. Good luck.
More works at: https://www.facebook.com/Simon-Beggs-Wood-Turning-...
Happy turning :)
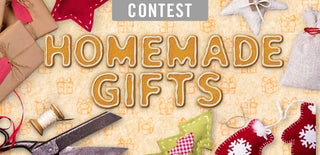
Participated in the
Homemade Gifts Contest 2015