Introduction: Toughening a RFID Door Opener
I guess I should sit down and record the process of my references, parts, and code for the actual device sometime, but mostly this Instructable will focus on my refitting of a RFID door opener to protect the wiring.
History: About three and a half years ago, I got pretty tired of getting flack from the local security when I would lock my keys in my office. Yes, sure, I am turning into a caricature, but my mind is on other things. So I decided to grab a few off the shelf components and make a door opener or the office. I used RFID and a stepper motor and it did pretty well.
During the next 24 months I 'discovered' design flaws I wanted to correct.
Step 1: It Kept Getting Broken
During the first couple of years, I noticed some things that I wanted to address. I had done a quick and rough prototype so I could start using it right away. Although, I like the raw aesthetic, there are more times than I wished that I would discover a wire dislodged, a bent header pins, pulled wire, etc.
I can only guess that facilities and housekeeping staff kept running into it. I know that I didn't. So I repaired it many times and then I went a long period without it because I was just too busy to work on it. (Yes... I had to deal with the agony of getting my door unlocked during this time.)
I needed to develop some sort of shield to provide at least casual protection to the wiring/parts.
Step 2: Parts
The stuff I used for this redesign:
- Clear acrylic.
- Machine screws and nuts
- Nylon standoffs
- wood screws
- Zip ties
- some scrap wire
- And of course the origninal RFID door opener project
I also used a vector drawing program and a CNC to cut the acrylic sheet.
To match my desire to see the guts, I decided to go with clear acrylic. My desire is to just create a shield to minimize accidents; otherwise, I could have just bought a project box and jammed it in there. My design came down to two flat planes (one to attach the components and one for the front protection plate) and one piece to make a stepper motor mount.
Step 3: Record the Working Model!
I took a couple of photos to be able to quickly be able to put it all back together without having to recreate my schematic from three years ago.
Then I disassembled the old mount and disconnected all the wires. I took the parts off the old mounting plate.
Step 4: Making a Motor Mount
I used a propane torch to soften the small tongue of plastic into a "L" bracket as a motor mount. Be careful! The propane torch softens the material quickly! After heating the plastic I draped it over the motor and pushed it into an L shape.
Step 5: Layout
I put all the component on the mounting plate to figure out attachment points. I used tape to make a surface that I could trace out where I would need to drill the base and the shield piece. Using a pencil, I traced the outlines. The tap also made sure that holes for connectors were perfectly aligned on the base and front face.
I also drilled the attachments slots for the motor mount.
I attached a spool that I modeled in Sketchup and 3D printed to the shaft of the stepper motor.
Step 6: Assembly and Some Wiring Optimization
Then it was merely a matter of attaching components. First, the Stepper Motor. Next Arduino and so forth. I decided that the motor shield on the project attached fine from friction. It also will make things easier to pull the shield for reprogramming the Arduino (the serial connection goes haywire when trying to upload new code if the shield is attached).
The original setup had a lot of wire on the stepper motor. This was an obvious snag point and in my design I wanted to shorten these to minimze this risk. I setup the parts measured how much plus a little allowance for the length and cut them. I used the motor shield as clamp running these wires underneath to hold them snug.
I retrofitted the 12volt power connection for the steeper motor by using the Vin port and Ground off the motor shield. This corrected a messy splice on the power cable that increased the problems with snagging the wires. I used a couple of those popular prototyping jumpers with female ends and cut them to length for the connections to the screw terminals.
Step 7: Attach Front Plate
I decided to setup the RFID module temporarily using painters tape. I need to make a bracket for the module.
I tried a series of different screw lengths and standoffs until I was happy with the distance. The front plat hovers just a few millimeters off the top of the stepper motor.
I used some scrap wire for my pulley and the original hacked together handle extender made up of pipe clamps and some spare brazing rod.
Step 8: Here It Is...
It works pretty well and I am pretty confident that the wires will be a lot less prone to being snagged. All of the header pins are now well protected. I took a little extra time and secure the power cable to the door with enough length so the door can be opened all the way up without pulling on the power plug. I believe I'll get a lot more use out of this and less repairs needed with just the simple shielding.
On the outside of the door, I put a small yellow sticker proximately on the opposite side of the RFID receiver. This helps me lineup my RFID token.
Still to do:
- Replace the handle extender
- Change the wire to some ball chain
- And make/install a bracket to hold the RFID module in place
Attachments
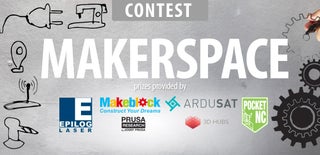
Participated in the
Makerspace Contest