Introduction: Under Shelf LED Light
I had a problem. Okay maybe not a problem, but an annoyance.
When I sat at my desk, my head blocked most of the light from the overhead fixture. This was fine when using the computer, but for other tasks I needed more light. The room with my desk is fairly small, so repositioning the desk wasn’t a good option. The obvious solution was to add another light source.
First I tried a floor lap. It worked, but for it to be effective, I had to position it close to my chair. This resulted in me constantly bumping into it. Next I tried a small desk lamp. This also worked, but my desk is rather crowded with stuff, so it was always in the way of something. What I needed was a light source that came from in front of and above me.
I already had a floating shelf on the wall in front of me so it seemed like a perfect place to mount a light. The shelf was a custom build of mine and I didn’t what to detract from its appearance by slapping some cheap light fixture under it, so I decided to build a custom fixture which would blend into the design of the shelf.
Step 1: Gather Your Materials
Parts and Supplies needed:
1 x 2 wood planks. Use whatever type of wood you like. The length needed will be dependent on the size of your light.
Thin sheet of plywood (1/8 inch is fine) (size determined by your frame size.)
1 light panel (diffuser lens) Cut to needed size.
http://www.homedepot.com/p/OPTIX-23-75-in-x-47-75-...
(4) L-brackets (also called corner braces)
(15+) Wood screws. Size (thickness) is determined by the hole size on your L-brackets. Length should be slightly shorter than the thickness of your shelf or frame (whichever is thinnest.) You will need 8 for the L-brackets, 4 to mount the light source, and 3 or more for your magnets.
(1) LED strip lights. These typically come in 16 foot rolls. Make sure you get one with the power adapter and controller. They come is single color or multi-color (RGB) rolls.
(?) LED strip light connectors. There are two main types: Two wire (single color LED strips) and four wire (RGB LED strips). Get the right connector for your lights. The number of connectors needed depends on how many strips you have cut your roll into. You need 1 fewer connector than the number of strips. (6 strips? You need 5 connectors)
(3+) Rare earth magnets (disk shaped.) Longer and heavier frames may need more magnets but three is a good starting place.
Wood Glue
Epoxy resin
Optional:
Hot Glue –Highly recommended for attaching the LED strips to the backer board.
Paint or Wood stain – Your choice.
Recommended Tools
Table saw or Miter saw
Tape measure
Combination Square
Brad-nailer
Bar clamps
Band Saw or jigsaw
Drill Press or hand drill
Drill bits
Screwdriver
Cost: I had all the parts laying around with the exception of the diffuser panel and the 1 x 2’s so my out of pocket cost was less than $15.
Step 2: Build - the Light Source
The design consists of two main parts: The light source, and the decorative frame with a diffuser panel.
We will build the light source first.
The light source us made using LED strip lights attached to a thin backer board which is then attached to the underside of the shelf with some screws. The backer board needs to be small enough to fit completely inside the frame with a gap between the edge of the board and the edge of the shelf on all sides. The exact size of the gap isn’t important, but you just need to leave enough room to mount the frame with L brackets.
The LED strips have designated spots where you can cut it into smaller segments. Cut the LED strip into segments about 1 inch less than the length of the backer board and join them together using the clamp connectors. Once all the strips are cut and connected, plug them in and make sure they all turn on. (If they don’t, recheck your connections.) Next, position them where you want them on the board. (Make sure the end with the power plug is near the back.) Pay attention to how far the connectors extend beyond the edge of the board. If the connector wires are going be pressing against the inside of the farm, you may want to shorten your LED strips. (The connectors are fairly weak and the LED strip can shift and lose contact if there is any pressure placed on them.) Remove the backing from their underside and stick them to the backer board. If the adhesive feels weak, use hot glue to make sure they stay in place.
The light source is done. You can mount it now (just screw it to the underside of the shelf) or wait until the frame is in place. (Recommended)
Step 3: Build - Cutting the Frame Pieces
The frame consists of 1 X 2 boards with the ends cut at 45 degree angles so they can be connected with Miter joints.
You can use a table saw or a miter saw to make the cuts. (Exact 45 degree cuts make the cleanest joints, so you may want to test you saw’s settings on some scrap wood first.) I’m not providing the length of the boards since it would only work if your shelf was the same dimensions as mine. To have a clean fit, the “long” sides of the boards need to be the same length as the sides of your shelf.
Next we need to cut a dado along the Short (inside) length of each piece. (A dado is just a fancy word for a groove.)
In each board, cut a ¼” deep dado along the entire length of the inner side. The dado should sit about ¼” from the bottom edge. The width of the dado needs to be slightly larger than the thickness of your diffuser panel. You can use a table saw or a router to do this. If you ae using a table saw, you don't need any special blade to make this since the width is not critical. To make my dado, I just made two passes with a standard table saw blade, moving my rip fence over 1/8 inch between passes. If you use this method, make the first pass on all four boards, then adjust the fence and make the second pass, this will ensure the grooves line up on each piece.
When you assemble the frame, you will have a ¼” deep grove forming a ring around the inside of the frame. The groove will hold the diffuser panel in place.
A quick safety note: The small size of the boards means you will be working close to the blade/router bit. Be safe. Use of push blocks is mandatory here to keep your fingers safe.
Step 4: Build - Assemble the Frame
Dry fit the four sides together to make sure you have a nice square frame. If everything fits together nicely, decide which side will be the front and which will be the back. (If it doesn't, check the tips section at the end for some advice.) Glue or nail (or both) the back corners, but leave the front corners unattached. Miter joints have a tendency to slip, so it can be helpful to use some clamps to to keep the corners square.
Once the glue has dried, drill a hole into the back on the side closest to where the power adapter plug will be.
If you are planning on painting or staining your frame, now is a good time to do it.
Once your paint/stain is dry, attach the L-brackets to the inside of the frame. Exact positioning doesn’t matter, but try to keep them fairly even on each side. The tops of the brackets should be flush with the top edge of the frame.
Step 5: Hang the Frame and Light Source
You can now attach the (currently 3 sided) frame to the underside of the shelf using the L-brackets.
Because the frame only has three sides, there is still some flex in it. Use clamps to keep the sides parallel while you screw it in place.
If you haven’t done so already, mount the light source. Just run some screws through the backer board into the underside of the shelf. Make sure the screws aren’t too long, you don’t want them poking through the shelf.
Step 6: Attach the Front of the Frame
The front if the frame is removable to allow access inside the light fixture. It is held in place by magnets.
Drill the holes for the magnets into the top of the frame piece. (A forstner bit will give you flat bottomed, holes) The holes should be the same diameter as the magnets. The depth should be slightly deeper than the magnets. Put the magnets in the holes to check for fit. The magnets should sit slightly below the wood surface. Remove the magnets, place a small amount of epoxy in each hole, and insert the magnets. They should be nearly flush. Let the epoxy cure.
On the underside of the front edge of the shelf, mark where the magnets will be. Insert a screw or nail in each spot and be sure it sits flush. If everything is lined up right, you can stick the front panel in place and the magnets will hold it secure.
Full disclosure: In the end, I couldn’t use this magnetic mount. I believe the idea is sound, but the design of my existing shelf prevented it. My shelf has sliding doors which ride in recessed grooves. Unfortunately, the place where the screws needed to go were directly under the door grooves. The screws would have poked through the groove and prevented the doors from sliding. Right now I just have the front panel held in place with clear tape. For a more permanent solution I am going to screw the joints together. (So much for my clean look…)
Step 7: Cut and Install the Lens
Cut the light panel to size. If you made your dadoes ¼” deep, cut it so it is 3/8” longer in each dimension than the interior of your frame. (If the inside of your frame measures 30” X 10”, your panel would need to be 30 3/8” X 10 3/8”) This will allow the panel to float in the slot but still be secure.
Note: cutting the light panel turned out to be the most troublesome part of this project. See my notes at the end for some tips to help with this part.
I used a band saw with a zero clearance insert to make the cuts.
Once your panel is cut, remove the front of the frame and slide the light panel into the grooves. Once it is fully in place, replace the front of the frame.
Congratulations. You are done!
I've put some additional build tips together which you may find useful. Click ahead to see them.
Step 8: Tips and Some Preemptive Q&A:
Tips:
The LED strips I had were encased in a rubbery water-resistant coating. From previous experience, this coating can get in the way when making connections. Since I wasn’t installing them in a wet area, I decided to remove the coating completely. It made them much easier to work with.
If your LED strips come with adhesive (aka double sided tape) on the back side, scrape it off the contacts where you will be joining LED segments using clip connectors. This will help ensure the connectors make good electrical contact. It is also not a bad idea to lightly sand the contact pads before attaching the connectors. On a previous project, I found there was a clear coating over all the contact pads which acted as an insulator and prevented the connectors from working.
The clip connectors for the LED strips can be very finicky. The slightest tap on the side can cause them to lose partial contact. If I had to do it again, I might consider just soldering the strips together using short lengths of wire.
If you are gluing your miter joints, don’t get sloppy. If you put too much glue in the joint it will squeeze out of the joints and get onto visible parts of the frame. Keep a damp rag handy to wipe up excess glue immediately. You will need to scrape off any dried glue before painting on staining the frame.
Miter joints are not particularly strong, especially when they are only joined by glue. Using a combination of brad nails and glue will give you a stronger joint. However, once installed the joints will not be under any stress. If you don’t want to put nail holes in your frame, glue alone will be fine.
The diffuser panel is quite brittle and can be difficult to cut cleanly. I initially started scoring it with a utility knife but found if I used too much pressure it would crack the plastic along unpredictable paths, resulting in a jagged edge. I found a band saw worked better, but even that resulted in some large chunks being knocked out. I got the cleanest cut when I placed a scrap piece of wood under the panel and then ran it through the band saw. The scrap wood functioned as a zero-clearance insert and completely eliminated chipping. You could probably do the same with a table saw and zero-clearance insert. If you don’t have access to a band saw, you could do the same with a jigsaw while laying the panel on a scrap wood panel to provide support.
Q&A:
Q: I don’t have the tools needed to cut a dado, can I still make this?
A: Yes, but you will need to use an alternative method of mounting the diffusion panel. The simplest would be to purchase some ¼” x ¼” wood (usually sold next to the dowels at home or hobby centers) and glue it on the inside of the frame, along the bottom edge. This will form a lip your panel can rest on. The panel will need to be cut slightly smaller than the inside of the frame (but larger than the lip.) Alternatively, you could just tap a few small nails along the bottom edge of the frame and let the panel rest on that. It won’t look as nice, but will get the job done.
Q: My miter joints have gaps! What did I do wrong?
A: Either your angles are not true 45 degrees, or your opposite side are not the same length. To compare length, lay the boards on a flat surface, long side down. If they don’t look identical, that’s your problem. If the lengths are good, then your angles must be off.
Q: My Angle/length is wrong. How do I fix it?
A: If the problem is length, you can recut or sand one end to make it match. If it is off by just a little bit, put a piece of sandpaper on a flat surface and rub the face of the miter on it a few times. (Hold it flat so you don’t change the angle.) If your problem is your angles, you can either start over, or you can try to fix them with sanding and/or trimming. It can be difficult to get the angles perfect so you are going to want a protractor or combination square to help you. To further complicate things, by fixing the angle you are naturally going to change the length. If you are planning to paint the frame, there is an easier way. Just assemble the frame, gaps and all. Fill the gaps with wood putty and then paint!
Q: I don’t have a miter saw or a table saw. How can I make the 45 degree cuts?
A: You can use a miter box and a hand miter saw. I’ve never had great luck with them, but maybe you will. Or you could just use butt joints and skip the miter joints. If you skip the miter joints, I recommend using the alternate panel mounting method above.
Q: Miter Joints suck! What were you thinking?
A: I used miter joints for two reasons. First, they look nice and clean. A good miter joint looks like a single piece of wood bent at 90 degrees. When you want a clean look, and the joint will not be under any stress, a miter joint is perfect.
Clean looks aside, I used miter joints is because they simplified cutting the dado. If I used a joint where the end grain was exposed, there would be a gap visible where the dado is. I would either need to cut a plug to fill in the gap, or stop the dado just short of the end of the board. (That can be tricky.) By using a miter joint, I could just cut the dado the full length of the board, (without needed to stop short of the end,) and it would remain completely hidden.
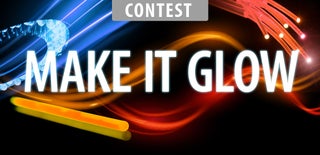
Participated in the
Make it Glow Contest 2016
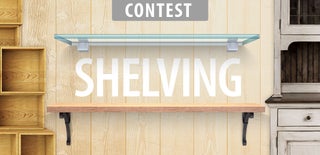
Participated in the
Shelving Contest 2016