Introduction: Wall (mains) Power for an Olympus E-510
Learn how to build an AC/DC interface for an Olympus E-510.
Unfortunately, Olympus didn't bother to make an AC/DC adapter for the Olympus E-510 camera. This typically isn't a problem as you can just tool around with a bag full of fresh batteries. It does become an issue if you decide to use your camera for time-lapse photos and don't want to replace batteries constantly during a long time-lapse sequence. Not only is replacing batteries a hassle, but it also shifts the position of the camera and makes the finished product not as smooth.
This project assumes you have a better-than basic understanding of DC electricity and some basic wood-working skill. If you have successfully built a circuit from a kit, know how to solder and are confident that you can cut wood without amputating your or your friends fingers, you should be OK.
If you have access to a laser cutter, you can have your plywood prototype in no time! If you don't, get your hobby knife and sand paper ready! This project also shows a great way to make 3d plywood prototypes.
You will need an AC/DC converter that can supply at least .5 amps (1 amp if you plan on shooting more than a picture/second) at at least 10 volts. Most variable voltage regulators need a supply voltage at least 2 volts over the set voltage to function properly. Check the spec sheet for your regulator.
To keep your camera safe, run your DC supply through a voltage regulator to ensure that your camera only gets between 6.8 and 7.2 volts. I suggest building the one shown below and dropping it into a box as it is handy to have an adjustable voltage regulator hanging around your bench.
http://www.ladyada.net/library/equipt/diypsupp.html
If you can find an LBH-1 for a reasonable price ($60 here in Norway), you can skip this instructable and simply wire up the LBH-1 as shown on the page below. I strongly encourage you to use a voltage regulator between the AC/DC wall-wart and camera. The wall-wart adapter shown in the page below will *NOT* provide a stable voltage. The selector switch simply sets an approximate range.
http://www.pinetreecomputing.com/camctl_eseries_power.asp
For more information on creating an intervalometer for shooting time lapse with an Olympus E series camera, check out this blag entry:
http://www.txoof.com/2011/04/time-lapse-intervalometers-and-555.html
You may also want to look into this instructable for making a remote cable interface for your Olympus E series.
https://www.instructables.com/id/Olympus-Evolt-E510-Remote-Cable-Release-Version-2/
Some things to think about before you start:
This project involves hacking your potentially expensive camera. With care and attention to detail, you should be able to create a nice AC/DC adapter without damaging anything. But as all hacking goes, you could wreck your camera and release it's magic blue smoke, start a fire, fall off the side of a bottomless cliff, or make your dog implode. This worked great for me, but your mileage may vary.
Step 1: Materials
Tools you will need
* Google Sketchup
* Google Sketchup Slicer Plugin
* A decent Vernier Caliper - Make sure you know how to read your caliper
* Metal straight edge or ruler
* A printer
* Sharp hobby knife
* Small clamp
* Tin snips
* Soldering Iron
Materials you will need
* Thin bass or pine wood sheets (approx. 2.5mm thick works well)
* Printer Paper
* Craft glue stick
* Sand paper
* Two part epoxy
* Wax paper
* Disposable mixing cup (I like to use the dimpled end of a soda can with a bit of aluminum foil)
* Disposable mixing sticks
* Thin brass or steel plate (a steel soda can or bean tin works great)
* 2.5 mm female DC power adapter (links to Mouser.com)
* Solder
Other handy items
* Eye protection - you'd be amazed how far and fast the tips of hobby knives can fly when you bust them.
* Coping saw
* Chisel
* Multimeter
Step 2: Create Templates for Cutting
As I couldn't lay my hands on an LBH-1 for a reasonable price, I made my own out of home-made plywood.
I measured out my battery using my calipers and Sketchup, sliced it up in sketchup and made templates to create the individual layers.
Attached to this step are two models of the E510 LBM-1 battery. This is the same battery that many Olympus cameras use. One file is a 1/10 mm accurate model of the LBM-1. The other is a model that will fit inside the E510 leaving a nice handle to pull it out with.
* Download the models, install Sketchup and the Slicer plugin - make sure you read the directions for installation and usage
* Measure the thickness of your wood stock material. My stock was 2.6mm; this will be my "Slice Spacing" value
* Load the model with the handle into sketchup
* Use the arrow tool to draw a box around the entire model. There should be a blue box showing that it has been selected.
* Choose Plugins > Slicer
* In the Slicer Parameters use the following:
Slice Spacing: >your stock material thickness< mm
Slice Thickness: 0mm
Slice Orientation: X
* Click OK; "No" to Equalize Spacing; "Yes" to Add Numbers; "Yes" to Hide the Original; "Yes" to make a flattened copy; "0.5mm" to minimum gap;
* Use the arrow tool to select the sliced model (not the flattened pieces); right click and choose "Hide"
* Choose File > Save As to save your work so far. Sketchup tends to crash in the next steps.
You should now have a bunch of rectangles that can be used as templates to cut out each element of the plywood battery. You now need to print out the templates. Sketchup *can* do scale printing, but it is very buggy, at leas under OS X. Follow these steps to make a printable template. If you have access to a laser cutter, this is a great time to feed this data into it and save your self a few hours of cutting and sanding. If only I had say, an Epilog Laser Cutter...
* Choose Camera > Standard Views > Top
* Choose Camera > Parallel Projection
* Dimension each piece in the X and Y dimensions using the Dimension Tool (Tools > Dimension)
This will give you a reference when cutting each piece to the right size. It is very difficult to cut exactly on the lines.
* SAVE YOUR WORK! The next steps are prone to all kinds of weird bugs.
* Resize the window to minimize the amount of gray space around the templates without cutting off any dimensions or model parts. This will save you from sketchup trying to print empty pages.
* Click File > Document Setup; uncheck "Fit View to Page"
* Set Print Scale to 1mm in drawing; 1 mm in model
* Click OK
* Click File > Print - DO NOT attempt to adjust *any* settings. Some annoying bug in Sketchup will cause your print out to become unstable. If you find that your model will fall over more than one page, consider create several different documents that will contain only a few slices. Attempting to preview or adjust any settings will just corrupt the printout.
* Collect your printouts and carry on to the next step.
Step 3: Cut and Sand Each Ply
Now that you have your slice templates you can begin laying out your plywood slices. Plywood is strongest if the grain of each layer is laid down opposite of the one before it. That is to say, all even layers should have the grain running in the long dimension and all of the odd layers should have the grain running in the short dimension.
* Label the odd slices with a "V" and all of the even slices with an "H" to help you remember which way to orient each template.
* Use your hobby knife and straight edge to slice out your template pieces.
* Apply a small amount of glue-stick glue to the back of the template; lightly glue it to your stock in the proper orientation (H layers should have the grain running along the long dimension.
* Use your hobby knife and straight edge to cut out each slice. Cut along the *outside* of the lines. This will allow you to sand down each piece if it is too large. It's hard to put cut wood BACK.
* Use your calipers to measure each slice for length and width, making measurements in at least two different places. Use fine sand paper on a block, or taped to a table top to remove a small amount of wood. Sand two or three strokes and measure again. It is easy to remove too much material. The battery is designed to fit into the camera with very little lose space. If the slices are not cut carefully, good contact may not be made.
* Once each slice is done label it with its part number to make assembly easier.
Step 4: Glue Layers Together
The layers now need to be glued, squared and left to dry. It is best to glue no more than four layers together at a time. This makes it easier to square each layer. Also, in the event of a catastrophically bad glue job, it limits the number of replacement parts that need to be remade.
* Read the directions for your 2 part epoxy. I like the 1 hour stuff. You have about 10 minutes to work with it and it dries to near full strength in around three hours.
* Line up all your segments and double check you have them in the proper order.
* Lay out enough wax paper to cover your work surface and wrap entirely around the pieces to be glued.
* Mix up a small batch of glue and apply it to several layers.
* Push the layers together and place them on the wax paper. Use a known square to line up the edges. Square the bottom and the top, checking at least twice for good alignment.
* Wrap the wax paper around the layers and gently clamp them to your work surface. Do not be tempted to over tighten the clamp. This will cause the layers to slip and no longer be square.
* Allow parts to cure according to your epoxy instructions.
* Repeat this with each batch of slices.
* You should have three or four units now. Use the same techniques to glue the groups of slices together.
Step 5: Test for Fit
Once your plywood battery is cured, jently try to slide it into the camera body. It probably wil not fit on the first try. Look carefully for where it may be binding and use sand paper to remove any edges that are catching. Work slowly checking after a few strokes and sand AWAY from your camera body. Do not force the wooden battery into the camera. It should slide in and out easily just like the authentic plastic version.
* The stock battery has a small grove in on the side opposite from the contacts. Use a hobby knife to make the grove. Your plywood battery must have the same groove in order to fit in to the camera. Check the model from step 2 or your original for the exact dimensions and location of the grove.
* Remove a small amount of material at a time and test for fit each time. The grove does not need to be perfect in dimension, but the location is critical.
Step 6: Create Electric Connections
It is now time to make the electrical connections. Refer to the battery model in step 2 for measurements for the location of the battery contacts.
NB! The image shown below is an early prototype that does not include the extra handle at the jack end. Other than the extra few millimeters of wood on the bottom of the battery, everything else is the same
* Use your calipers to measure the location of each contact and mark out the location. The contacts inside the camera are rather large, so this doesn't need to be precise.
* Check the diagram or your original battery for dimensions. The most important dimension is the size of the contact on the top of the battery (4mm x 4mm). Measure out and cut the brass stock to make a battery contact. Bend the contact appropriately so it will fit.
* Use a hobby knife to remove enough material to allow the contact to sit about 1mm deep at the top of the battery. See the model from step 2.
* Use the coping saw, chisel and hobby knife to make an opening flush with the bottom of the battery that is slightly larger than the outside dimensions of your 2.5 mm DC adapter plug. The plug should sit completely flush within the wooden battery.
* Use a hobby knife to cut out channels for wires that will go from the DC plug up to the contacts on the top.
It's time now to start making the electrical connections.
* Clean and buff the brass contact. Dirt, grime and oil will prevent the solder from making a good connection.
* Cut two lengths of hookup wire that are at least 1.5 times as long as you will need. This allows a good amount of "fudge factor" for mistakes. I used a red (+) and black (-) wire to help keep negative and positive straight.
* Strip and solder each wire to the back of one contact. If you have an adjustable temperature soldering iron, set it to a setting around 700C. The entire contact needs to heat up in order for the solder to make a good connection. If you are struggling to make a good connection, buff the area to be soldered with sand paper to make it rough, then clean the piece with steel wool and alcohol.
* Trim the wire to the appropriate length and solder the wires to the DC adapter plug. This is a VERY good time to think about how your power supply is set up. Make sure that you match the polarity of the power supply. The contact closest to the outside should be positive and the contact closest to the middle should be negative. Make sure you hook these up to match the plug coming out of your power supply. Hooking them up backwards coulddefinitely fry something in your camera.
* Check your connections using a multi meter. If you are using a regulated supply, set it for 7 volts. Plug your DC female jack into your power supply and measure the voltage across the two contacts you have made. Identify the positive and negative contacts and label them.
* Test fit everything again making sure that with the solder everything still fits in its place.
* Mix up a bit more epoxy and epoxy the clips, wire and DC connector into place. The negative contact should be closest to the center and the positive terminal should be closest to the edge. If in doubt, check your original battery.
* Clamp the project in wax paper on a smooth surface and allow the epoxy to cure fully.
Final testing:
* Test the electrical connections again by plugging your battery into your power supply. If the voltage across the terminals is lower than expected, you may have a thin coating of epoxy on the terminals. Use sand paper or steel wool to clean them and check the voltage again.
* Double check negative and positive orientation of your contacts. If the contacts are swapped, you could do some serious damage to your camera.
* Double check the voltage is within 6.8-7.2 volts. Voltage over 7.2 volts can potentially damage the camera.
* Unplug the battery and test for fit again using sand paper to remove any extra material.
* Once you are satisfied with the fit and electrical properties of your setup, plug it in and take a test shot.
Step 7: Closing Thoughts
After building this gadget, I realized that the camera draws quite a bit of current and the voltage can drop out if more than one shot per second is shot. Adding some larger capacitors to the voltage regulator shown in step one can help, and using a DC power supply that can offer up 1 amp at 10 volts will help greatly.
Step 8: Some Time Lapse Shot With the Adapter
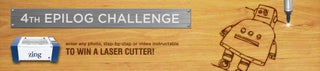
Participated in the
4th Epilog Challenge