Introduction: Wind Lantern: LEDs Powered by a Vertical Axis Wind Turbine
In this project, we’ll build a small, vertical-axis wind turbine, or VAWT for short. These are not as efficient as their horizontal-axis cousins, but they are better suited to urban environments where wind can come from all different directions.
Normally, when you give electricity to a motor, it spins. The same is true in reverse: If you give a motor a spin, it acts as a generator and creates electricity. The wind lantern will use energy from the wind to turn a motor and the resulting energy to light up some light emitting diodes (LEDs) within the base. The wind lantern will use this electricity to create a flickering, glowing indicator of the wind.
LEDs, like any other diodes, allow current to flow through them in only one direction. Bipolar stepper motors have two wire coils. The challenge here is to design a circuit that directs energy generated in each coil through an LED in the correct direction, no matter which way the wind lantern spins. Because even the best intentioned design is no match for NYC wind -it has a mind of its own. To do this, we’ll build a rectifier circuit for a bipolar stepper motor.
This project was recently featured in an episode of Make: Live - thanks Matt and Becky!
Step 1: Shopping List
Here are all the parts you'll need, down to the last washer.
Electronics
• Stepper motor (SparkFun ROB-09238)
• Male header pins (SparkFun PRT-00116)
• Breadboard (like All Electronics PB-400)
• Jumper wires (like SparkFun PRT-00124) or hook-up wire to make your own
• Eight diodes (SparkFun COM-08589)
• One or more LEDs (yellow SparkFun COM-09594 used here, but choose any color)
• One or more 1,000 μF capacitors (SparkFun COM-08982)
Hardware
• 1/4 in acrylic plastic sheet about 15 × 30 in or equivalent (size based on Ponoko P3 template) for gears, disks, and sail holder pieces. You can download the FREE template here on Thingiverse, or go ahead and buy them from my Ponoko showroom.
• 10 in wide aluminum flashing (usually sold in rolls; you need about 2 ft length for this project)
• 5mm bore shaft collar with set screw (McMaster 57485K65)
• 7 1/2 in bore shaft collars with set screws (McMaster 6166K25)
• 18 in length of 1/2 in outer diameter aluminum tube (McMaster 1658T45 is 8 ft long but a good value if you have the means to cut it down to 18 in—any hacksaw will work (like McMaster 4077A1))
• Two flanged sleeve bearings for 1/2 in shaft diameter (McMaster 2938T12)
• Thrust bearing cage assembly for 1/2 in shaft diameter (McMaster 5909K31) with two matching washers (McMaster 5909K44)
• Three female threaded standoffs, 4 in length, 1/4 in -20 screw size (McMaster 92230A350)
• Six socket head cap screws, 1/4 in -20 thread, 3/4 in length (McMaster 92196A540)
• Six lock washers for 1/4 in screw size (McMaster 92146A029)
• Six flat washers for 1/4 in screw size (McMaster 92141A029)
• Four M3 screws 40mm long (McMaster 91292A024)
• Four M3 lock washers (McMaster 92148A150)
• Four M3 washers (McMaster 91116A120)
• Set of inch and metric hex keys (like McMaster 7324A18)
• Deburring tool (like McMaster 4289A35) and/or rounded file
Step 2: Prepare Aluminum Rod
Put on your safety glasses and cut an 18 in length of the aluminum rod with a hacksaw. Use a deburring tool or file on the inside and outside of the end of the rod to smooth it and avoid cutting yourself.
Make sure your aluminum rod fits through the flanged sleeve bearings, thrust bearing and washers, and the shaft collars. Look at the tolerances of all the parts on McMaster:
• The aluminum rod has a ±.025 in outer diameter tolerance, which means it can range from 0.475 to 0.525 in.
• The shaft collars don’t give a tolerance for their inner diameters.
• The flanged sleeve bearings say +.001 to +.002 in for the inner diameter. This means they will be between 0.501 to 0.502 in.
• The thrust bearing says 1/2 in +0.002 to +0.007, which means the inner diameter can range from 0.502 to 0.507 in.
• The thrust washers don’t give any tolerance for the inner diameter.
This means that the outer diameter of the aluminum rod needs to be smaller than the smallest possible part it needs to fit into, which is the 0.501 in sleeve bearing. As you can see here, we have a good possibility for overlap in an inconvenient direction.
If your aluminum rod is too big for the sleeve bearing, put on your safety glasses, dust mask, and gloves (aluminum dust is not good for you). Grab the aluminum rod with the sandpaper and rotate it while you’re squeezing until you see aluminum dust coming off. Continue this until the rod fits through all the components. If you’re lucky enough to have access to a lathe, it could be a time-saver if you have a lot of aluminum to shave off. A bench grinder will work faster than sanding by hand, but it will be harder to maintain the round shape of the rod.
Step 3: Start Assembling Base
Assemble the base (refer to the full picture in step 2 as you go through the steps). Start with the two disks, the hex standoffs, and the 1/4-20 screws, lock washers, and washers. Install the standoffs by sandwiching the acrylic disk, a washer, and a lock washer on each end with a 1/4-20 screw.
Step 4: Part Assembly in Base
Install one of the flanged sleeve bearings in the center hole of the base disk. The base is the one without the four holes to mount the motor.
Rest a thrust washer, thrust bearing, and then the other thrust washer on top of the flange.
Slide the aluminum rod in from the top. Before it hits the sleeve bearing on the bottom, it should slide through the other sleeve bearing, a 1/2 in shaft collar, a laser-cut gear, two more 1/2 in shaft collars, and finally the thrust washer, bearing, washer stack.
Pull up slightly on the aluminum rod so it’s not hitting your work surface. Use your Allen key set to tighten the set screw in the lowest shaft collar. At this point, the shaft collar is resting on the thrust bearing and attached to the aluminum rod, so you should be able to spin the rod.
Lift the next shaft collar from the bottom up with the gear to about the halfway point inside the base. Tighten the set screw. This shaft collar will be attached to the gear with epoxy putty later, but DO NOT do this yet.
Step 5: Finish Base Assembly
Secure the top sleeve bearing with the top shaft collar.
Step 6: Solder Wires and Mount Motor
Before you continue up the rod, this is a good time to mount your motor. First, cut the wires to about 8 in long and solder a set of four male headers to the wires. Red and green should be next to each other on one side, and blue and yellow on the other.
Remove the screws that hold the motor together. Use the longer M3 screws from the shopping list to mount the motor from the back, on the underside of the top disk. Sandwich an M3 washer and lock washer with each screw.
Slide the other gear onto the motor shaft and use the 5mm shaft collar to secure it temporarily. Adjust the height of both shaft collars until the gears are at the same height and mesh well. Now you can break out the epoxy putty and secure the gears to their respective shaft collars.
Step 7: Continue Adding Parts Up the Rod
Continue up the aluminum rod. Slide on a 1/2 in shaft collar, one of the plastic sail holders, and then another 1/2 in shaft collar. Pull the lower shaft collar up so it’s not resting on the top of the base and secure it to the rod with its set screw. Then pinch the plastic sail holder with the shaft collar on top of it, and secure the assembly with a set screw. When you rotate the whole assembly by the shaft, it should rotate smoothly, and the sail holders should rotate with the shaft.
Cut out three sails for your wind turbine to catch the wind. There’s no right answer here, and you have a few different slots in the sail holders, so just use scissors to cut the aluminum flashing in a length you think will work. Then cut 1/2 in tabs into each corner to slide into the slots. Bend over the tabs to secure the sails.
Do the same shaft collar, sail holder, shaft collar assembly on the top of the sail to finish this section of the build. It should spin with very little friction when you turn it by hand with the aluminum rod.
Step 8: Now, the Electronics
We need to create a circuit like the one shown here. Use the eight diodes and jumper wires to create this circuit on your breadboard as shown. It will tell any electricity generated in each coil of the motor to go to the same place: the power column on the bottom of the breadboard. Make sure all your diodes are facing the right direction, and don’t forget to jump the ground columns across the board. Here's a schematic too if that's easier.
Notice the LED in the center and the two capacitors at the sides of the board. Plug the long leg of your LED into the power column and the short one into ground. Before you add the capacitors, give the wind lantern a spin and watch the LED flicker!
Try adding at least one capacitor as shown. The negative marked side should go to ground, the other to power. The capacitor will store energy while the wind lantern is creating it, and release it when it is not. The resulting effect here is a smoother flicker on the LED. Try adding more LEDs and more capacitors until you get a smooth glow when you spin the aluminum rod. You can also place diffuser paper over the side of the lantern to create a pleasing glow.
Step 9: Put It to Work
Now take it outside! See if it works with real wind. We had success on a street corner in Manhattan and on the roof of Eyebeam Art + Technology Center’s two-story building as you can see in this video - thanks to awesome intern Sam Galison for helping with the project!
Attachments
Step 10: When I Win the Laser Cutter...
I first got addicted to using the laser cutter at Eyebeam Art + Technology Center when I was a resident there last spring. I was able to use if for lots of the projects in the book I wrote called Making Things Move: DIY Mechanisms for Inventors, Hobbyists, and Artists. When I win this one, I will be able to continue working on projects at the edge of art and technology and using them to teach others about making both for "real" projects and for art and fun.
I'm now part of a new lab at NYU-Poly where I work as a research assistant while pursuing my PhD in Mechanical Engineering, and we don't yet have our own fabrication tools. I'm working on some fun projects, like creating a low-cost robotic hand to test space suit gloves, and having a laser cutter will help take me through several iterations of a design with less cost and time than would be possible any other way. We're also getting a DARwIn-OP humanoid robot in the lab, which is all open hardware, and I'll be modifying it and outfitting it with sensors to measure energy consumption (and of course post about the progress!). Having a laser cutter will also help immensely here.
On top of that, I've introduced my fiance to laser cutting and now we have a lot of projects for our wedding that need one! From laser cut fabric flowers to engraved favors for our guests, we have less than two months to pull everything together. And we'll continue making and spreading the DIY bug long after that - we already have a list of projects for our new apartment!
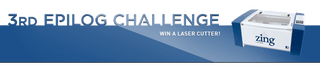
Finalist in the
3rd Epilog Challenge
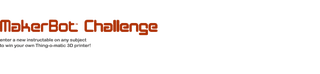
Participated in the
MakerBot Challenge