Introduction: Wooden Axle
If books, TVshows, and movies are any indication, it seems that civilization is headed for certain collapse. Once the fall happens, wheeled transportation is going to be at a premium. We may be fleeing zombies, or farming with horses, or trying to get a car running on moonshine and tree sap -- whatever the case, wheels, and the skills to make them, will be valuable to have.
This post-apocalyptic wheel assembly uses a wooden axle and spare tires (donuts) to provide the basis for a handcart, simple wagon, or trailer. Short of metal, and tools, this is also a perfect repair for a broken trailer. After I made it, I realized a solid axle has some trouble turning, so I would recommend actually cutting the axle in half and mounting each wheel independently so that a two-wheel arrangement can pivot.
The parts for this are all recycled, and very cheap, if not free. Sustainability starts with re-use, especially when the factories collapse and no new ones are being made!
If you enjoy this Instructable, check out my new website at Object Guerilla for more projects and musings on the end of the world.
You will need these materials:
2 compact car wheel hubs
2 compact car spare tires (donuts)
Several pieces of scrap plywood, appox. 4 sq. ft. in total
Hefty chunk of douglas fir, spruce, oak, walnut, hickory, pecan, or similar
Wood glue
Handful of 1/4"-3/8" through-bolts, nuts, and washers
Handful of 1/4" x 5" lag bolts
1-1/2" hole saw
Wood glue
Wax
You will need these tools:
Table saw
Jig or Bandsaw
Block plane
Drill/driver
Step 1: Blankin'
Finding a suitable wood for the axle is the most important step in this process. You will need something extremely strong, kind of heavy, but also possessing a little bit of flex. Hickory, used in axe handles and drum sticks, would be ideal. It is hard yet resilient. Oak, maple, and walnut, three common hardwoods, are often used as pallet stringers and flooring. Poplar can be found in door casings, some cabinet work, and cheaper furniture. The Douglas Fir that I used was from an structural beam torn out of an old house. While technically a softwood, old-growth Douglas Fir is strong, tight-grained, and dense. If you can't find a thick chunk, laminate a number of thinner strips together -- like pieces of hardwood flooring -- to create a larger blank.
Start by cutting the piece down to about 2" square. This axle is about 28" long, and I would hesitate to go above 36" wide because the axle would start to bow at that span.
Set the blade of the table saw to 45 degrees, set the fence at about 1-1/2" from the base of the blade, then bevel all four corners of the blank. This should create an octagon with approximately equal sides.
Step 2: Planin'
To fully round off the axle, use a block plane. Begin by taking one pas off of each corner, creating a 16-sided form. Then take one pass off of each remaining corner, and so on, gradually rounding off the whole piece. As you get close to round, roll it back and forth on the workbench or the floor to determine where any flat spots are. Aim for a finished diameter of 1-1/2". Finish off with a healthy hand sanding and several coats of wax to help it roll smoothly in the bearings.
Step 3: Wheels
Buy two spare wheels and donuts from a junkyard, pull-your-own yard, or tire place. These cost about $12 each.
Cut four 3/4" plywood disks, about 10" in diameter. Drill out the center of two of them with the 1-1/2" hole saw. Glue and screw one "donut" disc to one solid disc, resulting in two hubs, each 1-1/2" thick.
Hold the hub to the wheel and scribe the bolt holes onto the plywood. Drill them out and through-bolt the plywood to the wheel, with the drilled-out portion of the hub facing in.
Step 4: Assembly
Cut out four "U"-shaped pieces of plywood, about 12" x 6" wide. It's probably easiest to cut rectangles of that size, then round off the bottoms with a jigsaw. Drill out 1-1/2" hole, nestled down in the curved part of the "U", in each. Glue and screw them together in pairs, wax the inside of the holes, and thread onto the axles.
Glue the axle into the socket on the hub, then attach through the other side with a 1/4" lag bolt, pre-drilling to prevent splitting. The end-grain connection will not be the strongest, so pop in some toe screws or triangular braces as well.
Once both wheels are on, and the mounts are sliding freely in the center, jack up your cart or trailer and screw the mounts on. As I said in the intro, it won't track right unless each wheel turns independently, so you should probably cut the axle in half and double the number of mounting point.
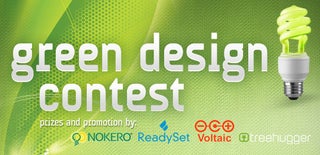
Participated in the
Instructables Green Design Contest