Introduction: Wooden, Cyclone Seperator Shop Vac
tired of changing your shop vac bag right when you are in the middle of needing great suction.
A cyclone separator is what you need.
made from scrap timber and a few shop fitting.
I've put up with only cleaning the most essential parts of my shop as I did not want to fill my shop vac bag, Now I find I'm looking for things to suck up. I'm enjoying a dust free shop for the first time in years, my lungs are thanking me and so is my hip pocket.
Step 1: Tools Needed.
tools needed: cumpas
pencil
tape measure
square
straight edge
angle finder
filler
sandpaper 60 -300
glue
torch
rasp
masking tape
jig saw
elastic of some description
circular saw
tapering jig
level
240 ltr garbage bin
2 feet of 2" pvc pipe.
4 rubber flanges
masking tape
Step 2: Cutting List
45, 12mm x 12mm x 600 long, tapered to 6mm with 4 degree edges
1, 12" diameter 3/4" thick mdf
1, 10" diameter 3/4" thick mdf
1, 6" diameter 3/4" thick mdf
1, 1" dowel 40" long hard wood
1, 180mm x 90mm x 240mm block (pvc cover)
Step 3: Disks
cut 3 disks from 3/4" mdf scrap
1 x 12" diameter 3/4" thick mdf
1 x 10" diameter 3/4" thick mdf
1 x 6"diameter 3/4" thick mdf
using a 1" dowel, 40" long, drill a 1"hole in the center of the 12" & 6" disks keep the holes slightly under size ensuring a very very firm fit.
the dowel and the 6" disk will we permanently removed at a later stage.
cut a 6.5" hole in the center of the 10" disk. ensuring you angle your cut to match the cylinder angle
Step 4: Cutting Wall Sides
wall sides 20" long x 1/2" tapered to 1/4" with edges sanded 4 degrees on both side edges to make them sit in the cylinder closer together.
use a straight edge tapering jig cut approx.. 45 lengths.
using a belt sander, sand your 4 degrees on each side. no need to be perfect here just a rough guide, putty will fill in any small gaps later.
Step 5: Assemble Cylinder
sounds simple lol
without an additional top and bottom support this becomes impossible with 2 hands. if your were born in this galaxy you will need the extra supports.
for the base, I used hair ties joined together, great elasticity. top, used a stretchy rope.
GLUING
firstly apply masking tape around the 6" disk to prevent the glue sticking to it.
I used about 600 mills of glue. poured the glue on to a board and lay each tapered edge in the long pile of glue.
with the 10" disk facing down on the bench, I placed the thin edge of each side piece under the rope and pushed up, then slid it down and under the hair ties. fastest and simplest way I found without all the side pieces falling to the table. lol
I would strongly recommend cutting the 6.5" angled circle in the 12" disk before proceeding much further
after all sides are in place drop the 12" circle over the dowel and push firmly down.
tap the disk until its perfectly level, use a level!
Step 6: Elbow Grease
when dry, remove the small disk and the dowel from the cyclone and disregard.
if you have not done so by now, insert the 12" disk back on. do not glue.
mark and cut the ends of the sides flush to the 12" disk.
sand the inside and outside smooth, if your have any odd shaped sides that stick out, using a rasp, file them down then sand smooth.
I used aprox 1/2 kg wet mix filler and sanded 90% off when dry.
repeat for outside. then glue the 12" disk in place.
I would strongly recommend taking more time here and remove more filler before the sanding starts.
it is a messy job when you add water to cylinder but will be worth your efforts ten fold.
Step 7: Pvc Attachment Shaping
cut 2, 2" pvc piping to 7" long
one will be placed through the enlarged dowel hole on the 10" disk & the other needs one end to be flush on the inside of the cylinder.
attach 60 grade sand paper to the widest section of the cylinder, at approx. 1 1/2 " before the top end of the cylinder.
we are aiming to make the end of the pvp pipe look, some what similar to the mask used in the scream movie.
once you can place the edge of the pvc on the sand paper without much light getting under then you have finally reached the right shape.
when you have reached your shape needed its time for a hot cup of coffee.
trace outline the pvc tube aprox 1 1/2" below the end of the 10" disk, make sure its clear and accurate.
make a small hole for your jig saw to fit, keeping away from the edge of the line just incase you made a mistake in your outlining.
carefully sand the remainder of the timber up to the line checking with your pvc regularly, remove small amounts at a time to get the perfect fit.
with your 60 grit sand paper rub the pvc tube until the pvc is deeply scratched, giving your glue something to bond to.
DO NOT GLUE AT THIS STAGE we are just prepping.
Step 8: Sealing the Cylinder
once your happy with the smoothness of the outside of the cylinder and have bogged any divots, dints or misshaped pieced, cover the entire outside of the cylinder with glue, yes I said glue.
I used a cloth the spread the glue evenly and finished with a damp cloth to finish off.
when dry sand out any small bubbles with 400 sand paper and your job on the outside is done.
CYLINDER INTERIOR
Seal with paint, you will need to find a better way to cover the outside to protect it from the paint than I did.
this method I used ( glad wrap) allowed the paint to escape from the pvp hole and travel where ever it liked.
I've used materials around the house to make this project so instead of buying varnish or a polyurethane sealer I've used oil based enamel paint. the type of paint your architraves around your doors are painted in.
first give the inside a coat of oil based sealer.
when dry apply a thin layer paint and let dry.
continue painting thin coats of oil based enamel until your happy with the thickness.
ensure you follow manufactures drying times.
Step 9: Wooden Pvc Side Cover.
The shapes pvc tube will take some great abuse over its life so we need to secure it firmly to the cylinder.
ive used a old red gum fence post.
using the 10" disk as a template, trace the disk edge on to the side of the slab of red gum.
using the table saw cut slots until it looks like a very large comb.
knock the fine teeth out, and clean up until nice and smooth
when your shape is close to the desired shape repeat steps used to make the pvc tubing. elbow grease and sand paper.
move to the drill press
stand the slab on its end grain.
locate the center and drill a 2" hole, I used several smaller holes in a circle, a chisel, rasp and sandpaper to make the perfect fit.
I found the hole drilled square was not quite right as I wanted to keep the pvc pipe on a specific angle. I was being a little pedantic.
glue the pvc to the red gum, I used hot glue.
Step 10: PVC Support Gluing.
supporting a flat edge to a curved and angled edge, what a challenge.
I needed to keep a very specific angle to keep the pvc level on the inside of the tube so depending where you locate the red gum support will make a difference to how the pvc aligns internally.
place your hand inside the cyclone and move the red gum support back and forth until you are happy that the pvc aligns perfectly on the inside.
once aligned trace lightly around the red gum support and remove your hand from the cylinder.
cover the area outside the outline with masking tape to protect the surface from the coming glue.
I used liquid nails as I also needed to make a air tight seal.
- entire tube of glue, over kill but that's just me.
using rope and 1 g clamp, secure it in the right place, again insert your hand in the cyclone for best positioning.
remove any excess glue from the inside before it dries.
Step 11: Hose Attachments
using rubber pipes with adjustable rings, attach one end to the pvc and the other the vacuum hoses.
top hose: goes to the suction inlet on your vacuum.
side hose: goes to your hand or chosen machine
Step 12: Secure to Sawdust Storage Bin
using melamine 3/4" board, cut a size equal to your storage bin top.
attach side supports to prevent the cyclone moving while switched on.
cut hole in center to match cyclone base hole.
glue the 12" disk to the melamine ensuring the holes line up.
remove the top pvc and use a torch to look down.
add screws for support .
when dry turn over, reattach your top pvc pipe and sit the project on the bin.
if done correctly the bin will be air tight once the shop vac is turned on.
if you have any leaks use a rubber based double sided tape along the area of the lid to make a seal.
Step 13: Suction Test OMG!
here is a view of the power of the cyclone in action.
I had to use bolts to secure the lid to the bin as the suction was so great it almost completely collapsed the bin.
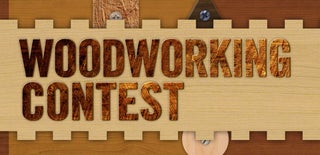
Participated in the
Woodworking Contest
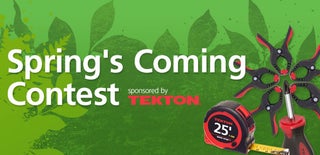
Participated in the
Spring's Coming Contest