Introduction: π¦ House Sparrow π¦ Bird Box Terrace π¦
Based on a number of comments I've had from my USA readers please read this note before embarking on this project...
The House Sparrow is an invasive species to the Americas, as such should NOT be encouraged. You could use this instructable as a starting point for a box that encourages your native species.
Please take into consideration your local wildlife recommendations for house styles.
I'm lucky enough to be in the UK and have a tree and bushes outside our front window, for years now I've been feeding the house sparrows that congregate there. Sometimes there are 40-50 birds chirping away.
A couple of years ago I put up a cheap bird house that was immediately occupied and saw two broods.
I decided this year they would get a house upgrade to a terrace of four houses they could share with their friends.
Supplies
The supplies for this one is fairly simple, about 4 metres (4.4') of rough sawn timber and some outdoor screws. If you decide to go over the top (as I did) 5β6 metres (5.5β6.5') of 7 mm (0.28") western red cedar.
I also used an air staple gun to attach the shingles.
Step 1: Bird Terrace Design
The design of the terrace was based around the original single bird house. This was obviously the right size and shape, so was a good starting point.
I've attached the original SketchUp file so you can edit it if you choose. I've also put all the individual images into a single PDF file for those who don't have SketchUp.
Step 2: Preparing the Planks
Unfortunately the length of the planks I got were too big to be safely cut on my table saw.
I use my chop saw very infrequently, so it is packed away. I had to cut them down to length with the circular saw. To make sure this was straight I clamped a framing square and cut to that.
Once I had cut the pieces to length I used the planer to square them up, then a few passes through the thicknesser to get them all to the same thickness.
Getting the pieces square and the same thickness is very important for the next step.
Step 3: Making the Front and Back
The planks I had were only 150 mm (5.9") wide, so I had to join two lengthwise to get the width needed.
Having got the boards straight and flat I joined them using Kreg pocket screws, waterproof wood glue was also used.
I used dog hole clamps to make sure the faces were flat while the pocket screws were screwed in.
Checking on the angle of the top edge in the SketchUp design, I needed 72.6ΒΊ. Having zeroed the angle finder the closest I could get it was 72.7ΒΊ, I was happy that a 0.1ΒΊ error wouldn't be noticed by the sparrows.
This angle was cut to the top edge of both the front and back pieces.
While the angle was set on the saw I also ran the cut along the back of the lid. I left the front of the lid so there was a rain overhang.
Step 4: Making the Separators
The SketchUp image here shows the sizes required for the separators, the two larger ones are for the ends and three shorter ones are required for the internal separators.
One of the dangers of cutting lengths of wood on a table saw is trapping the wood between the blade and fence. To stop this I have a piece of 20 mm (7.87") wide wood that bolts through the fence, the wood to be cut is butted to the fake fence then cut, it makes sure there is enough space so the cut piece doesn't get trapped.
With the 5 lengths cut I then added the angled cut to the top. The angle is 72.6ΒΊ the same as the top edges. I used the mitre guide sliding table on the saw. My saw has a really handy 'yellow dot' on the saw bed, marked on this is the kerf of the blade, it makes it super easy to line up the corner to cut to.
Step 5: Entrance Holes
The entrance holes for bird houses have very specific dimensions depending on the bird they are intended for. For the house sparrow it needs to be 32 mm (1.26").
The SketchUp image shows the layout of the entrance holes.
The holes were marked out, then drilled using a 32 mm (1.26") Forstner bit in a pillar drill. Always make sure you clamp down the wood you're drilling as the Forstner bit can grab and spin the wood, this can be very dangerous and hurt a lot when a spinning piece of wood smacks your knuckles.
This is where I'm going to introduce one of my favourite workshop hacks, it's a magnet stuck to the pillar drill, an easy place for the chuck key to live.
Step 6: Assembly
Now you have all the pieces cut and shaped it's time for assembly.
I start by screwing the sides and dividers to the back, to do this I laid the back down and stood the dividers spaced out with the tops flush, with a sharp pencil mark onto the back where the dividers are. With a drill big enough for a clearance hole, drill three holes in the centre of your divider marking.
To make sure you don't split them you'll want to drill pilot holes in the divider.
Once you have the dividers screwed to the back piece you can now attach the base, this is done the same as the back... Position, mark, drill clearance holes, drill pilot holes and screw.
Now it's time for the front, this is pretty much the same as the back and base with one exception. To get a neater finish I opened up the front of the clearance holes to 10 mm (0.39"), this allowed me to glue in some dowels, once the glue had dried these were trimmed flush with a Stanley FatMax mini flush cut pull saw.
Step 7: Adding the Roof
To enable me to clean out the box in winter time I decided to add the roof with a couple of hinges.
Having already added the angled cut to the rear edge make sure you have it the correct way round.
I didn't bother to inlay the hinges as they will never be seen.
Hold the top in place, lay on the hinges and mark the holes, drill out the pilot holes and screw the hinges in place.
Step 8: Setting Up the Table Saw
This is when I had a brainwave, 'I know what I'll do, I'll put cedar shingles on the roof'... This wasn't clever, it probably doubled the time of the build.
I had some strips of western red cedar left over from when I made a strip stand-up paddle board. I tried these on the roof, but they were too thick. I needed to thin these down. To do this I ran them through the table saw set at 5ΒΊ.
The resulting strip was going to be very thin, so I needed to make a 5ΒΊ zero clearance plate.
I traced around the original plate and cut out a blank on the bandsaw. 9 mm (0.35") plywood is pretty much the perfect thickness to be level with the saw bed.
To cut the slot for the blade I clamped a piece of wood across the plate and raised the running blade through it.
Once I had the plate, I moved the fence to 2 mm (0.08") and run the strips through, this was done with a couple of feather boards, it's important for two reasons, first is for safety, the feather boards hold the strip against the fence while holding it down against the bed. The second reason is to make sure that the strips are cut to the same size.
Step 9: Cutting the Shingles
Again, to make sure of shingle size consistency I made a little jig for the bandsaw. This jig also had the great advantage of allowing me to keep my fingers away from the blade.
Step 10: Attaching the Shingles
Once I had finally cut the 180 ish required shingles I used an air powered staple gun to secure the shingle in place.
Having put the first row of shingles in place, I wasn't happy with how straight the row was, so I snapped off all of those shingles and with a pair of nail pliers removed the staples.
This time I held a single shingle in place and marked the top, I then transferred this mark to the other side and marked a line, this allowed me to put a perfect row of shingles in place.
The next row of shingles were attached in the same way also with a location line marked in place.
Each row of shingles overlaps the previous row by about 5 mm (0.2"), these are offset by half a shingle to allow the rain to run off the rows.
The final row of shingles were tacked into place with a single 12 mm (0.47") pin nail.
Step 11: Mounting the Box
I had some 3 mm (0.12") thick stainless steel left over from a previous project, as the box was quite heavy these 4 steel strips would be perfect.
I secured the strips to the box with some stainless screws, making sure that the tips didn't protrude into the box.
The box was then finally attached to the wall with Rawlplugs and #8 65 mm (2.56") stainless screws.
Here's hoping we get some nesting this year.
π¦
π¦ π¦’ π¦ π§ π¦ 𦩠No emoji for house sparrow I'm afraid π
I hope this has inspired you to give your local birds a home.
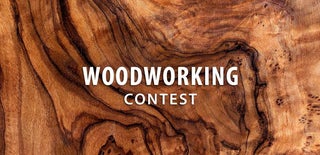
Participated in the
Woodworking Contest