Introduction: 10 Degree Kitchen Drawer Fix
Sometimes the smallest home improvement or fix it project can mean the most to a homeowner.
We recently replaced the original laminate counter tops in our house with granite counter tops. When we did this we decided to install drawer handles and door knobs. One thing we discovered at the corner in out kitchen is that one of the drawers would not open if the adjacent drawer had a handle installed. Luckily I did not install the handle on that drawer before I discovered the problem.
We didn't install the handle that would block the other drawer, but to open the drawer to full depth then we had to open the door to the oven. Not cool.
It was a really bad cabinet design by the people who designed the kitchen, but it was something we didn't notice when we bought the house when it was a month away from being completed as a spec home.
As I looked at the drawer that wouldn't open all the way I thought to myself that it would be great if the drawer could slide out of the opening at an angle. Then I thought "Why Not?" There was enough room in the corner cabinet for it and I thought I would most likely be able to re-use the original drawer slide hardware.
The drawers were made as a box with the drawer face screwed to the front of the box. A box with a little angle to it shouldn't be too difficult.
Step 1: Materials and Tools
Materials
- Poplar board for drawer sides
- Various screws
- 1/4" plywood for drawer bottom
- Re-used the drawer slides and drawer face from the original drawer
Tools
The tools I used on the project were as follows:
- Table saw
- Band saw
- Miter saw
- Cordless drill
- Drill press
- Screwdrivers
- Pliers
- Clamps of various types
- Belt sander
- Sanding paper
- Clamp light
- Kreg Pockethole Jig - https://www.kregtool.com/store/c13/kreg-jigsreg/
Not all of the tools in this list are required. You may be able to substitute other tools depending on your situation.
NOTE: If you plan on using any tool for a project please make sure you are familiar with the tool and all of the dangers associated with it. If you are not familiar with a tool then you should ask someone who is to show you the proper way to use it. A lot of communities have classes at local colleges on the proper use of tools and machinery. There are also local woodworking clubs that offer classes at very reasonable rates for beginners. I highly recommend using these resources for your safety and for the most efficient use of the tool.
SAFETY FIRST
Always wear eye and hearing protection.
Always work safe with the proper safety equipment and guards on your tools.
Step 2: Measure Existing Drawer
I started measuring the existing drawer and realized since I was going to angle the replacement drawer out of the existing opening that the width of the drawer would be limited by the width of the drawer opening. I then took some measurements from the existing drawer to find out how much width the drawer slide hardware added to the width of the drawer.
I was going to make the new drawer a parallelogram, but decided against this so using the existing drawer hardware would be easier.
Step 3: Planning for the Angled Drawer
I was going to make the drawer at a more extreme angle such as 20 or 30 degrees, but decided it would look better to just go with something that would just clear the handle on the adjacent drawer and the stove. I settled on 10 degrees for the angle. It actually worked out really well since my miter saw has a locking position at the 10 degree angle.
I decided it would work to re-use the existing drawer slides. To do this and make use of the auto close feature that kicks in when the drawer is almost closed I needed to keep the slides parallel and even with each other. Since the front of the drawer face was going to be at 10 degrees I had to put a 10 degree wedge under the front of the new drawer. More on that later.
Step 4: Cutting the Pieces / Sample Drawer Box
I started layout out the piece doing the math with a 10 degree angle, but decided to fall back on my computer to lay out the drawer using the width constraints I determined from the earlier step.
I have a 10 degree locking point on my miter saw so it worked out great to cut the pieces accurately.
Since I only had one piece of poplar that I had milled down to a 5/8" thickness to match the other kitchen drawers I decided to make a trial run drawer box out of some scrap plywood. This worked out well and also allowed me to set my pocket hole depth so it would not let the pocket hole screws go all the through the side piece of the drawers.
I cut all of the pieces I could at the same time to minimize any differences in angles.
I put all of the pieces together to make sure the pieces had a good fit and then held it in the cabinet to make sure the box was roughly the correct size.
Step 5: Assemble the Drawer
I used a Kreg pocket hole jig to assemble the drawer pieces. Before I did this I used some of cutoff pieces from the drawer sides to assemble a mock piece to make sure the pocket hole screw depth was sep appropriately. I didn't want the pocket screws going through the side of the drawer where the corner angle was 60 degrees.
I added glue to the corners before I
Step 6: Drawer Bottom
The drawer bottom includes the bottom piece of wood and the slots that need to be cut in the front, back, and side pieces of the drawer box.
I used an existing piece of 1/4 inch baltic birch plywood for the drawer bottom. I set the drawer on the piece of plywood and marked a 1/4" line on the two sides of the piece of plywood. I lined this up with the inside of the drawer box and drew line on the plywood for the other two sides. Then I draw a 1/4" offset line to get the full outline of the drawer bottom.
I cut out the drawer bottom using a band saw and then smoothed the edged with a belt sander.
I cut the slots for the 1/4 inch plywood on the table saw. The 1/4 inch thick plywood is actually a little thinner. I used a sample piece to get the slots cut the correct width.
One of the nice things about using the pocket screws to put the drawer box together is that you can cut the slots for the drawer bottom all the way across all of the pieces. When the box goes together the slots are hidden in the front of the drawer with the drawer face.
Step 7: Attaching the Slides
Using the old slides I had to make sure they were parallel and also extended the same amount. They have a quick release piece that attached to the front of the drawer. Since the drawer front is at 10 degrees I had to cut a piece of wood to put across the front of the underside of the drawer so these quick release pieces would be besides each other.
I then attached a couple think pieces of wood on the bottom of the slides to keep them spaced correctly while installing the guides. These made it possible to hold the drawer assembly in place while positioning it in the cabinet.
Step 8: Make the Drawer Supports
The existing drawer slides I was using had molded plastic supports that attached to the back of the cabinet. Since I couldn't re-use these with the 10 degree angle I decided to support the slides with added pieces of wood screwed to the sides of the slide mechanism. This worked well since they already had screw holes in them.
I rough cut the wood supports to a length that I though would almost touch the back of the cabinet. This would allow a little side to side movement for aligning the drawer face and let me support the guides with another piece of wood screwed to the back of the cabinet under the guides.
The first time I cut and attached these I ended up with one piece that was about a quarter inch too long. I couldn't get the drawer box face to align with the cabinet face so I remove the assembly and cut a quarter inch off of the support.
Step 9: Support for the Supports
I installed a horizontal piece of 3/4" thick wood under each of the drawer supports. The top of these supports were set by measuring from the top of the cabinet down to match the distance at the front of the cabinet from the top down to the drawer supports.
Since I had to put the whole drawer and slide assembly into the cabinet through the door opening and then lift and rotate it into place I was able to lift it a little higher and swing it into position on these rests in the back of the cabinet.
There really wasn't anything too exact with these support pieces as no one will see these inside the cabinet and behind the drawer.
Step 10: Align the Drawer Face
The next step is to align the drawer face with the front of the cabinet so the drawer face is flat against the cabinet when you attach it. With the front left drawer guide attached to the face frame of the cabinet you can slide the back end of the guides (near the back of the cabinet) left or right to align the drawer face. One you have everything where you want it make the supports at the rear of the cabinet with a pencil mark so you know where things need to be for proper alignment. This is critical since things move easily until you get them screwed in place.
Now put a screw through the right drawer support to get the that locked into position. I added a thin wood shim between the guide support and the side of the cabinet.
In the back of the cabinet I added a strip of wood over the top of the drawer guide piece to keep the drawer from tipping down once it was extended. I just screwed this in place in case I ever needed to remove it.
Step 11: Attach the Old Drawer Face
Add two strips of double sided tape to the front of the drawer box. Now take the old drawer face and slowly push it into position on the tape. This should hold it enough for you to securely attach the face to the drawer box. Since the drawer face already had a handle installed I used the holes from the handle and extended those holes through the front of the drawer box. Once I had those holes drilled I removed the double sided tape and then attached the drawer front with the drawer handle screws.
If the drawer box is sitting slightly behind the front of the face frame of the cabinet then you will need to hold the drawer face in position with one hand and use your other hand to reach through the door opening and pull the drawer box forward until the double sided tape sticks.
Step 12: Success
After installing the new drawer I realized I could have made the drawer a little deeper, but didn't want to take the chance of things not fitting when trying to put it all together.
It wasn't a really fast project, but the result is very satisfying. It is great to finally have the drawer handle on the last drawer so everything looks the same.
It will be nice to be able to get access the full depth of the drawer and not have to open the oven door in order to do that.
I think the Kreg pocket hole jig performed fantastic for building the drawer box. The two joints at the front of the drawer that are at 80 and 100 degrees look extremely tight and clean. I have only used the pocket holes on 90 degree joints before, but a little patience goes a long way in making things look great.
I would highly recommend this type of solution if you have a similar situation. The only money I spent on the project was actually for the wood for the drawer box as I had everything else left over from other projects.

Grand Prize in the
Home Improvement Contest 2017
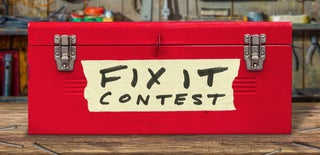
First Prize in the
Fix It Contest