Introduction: 100 Watt LED Grow Light
There are a lot of "plug and play" LED grow lights on the market, many of which can screw into regular light bulb sockets. However, the performance and life-span of higher watt LEDs is highly dependent on the temperature they run at. I wanted to make an Air-cooled grow light with a small physical footprint.
Step 1: Gather Supplies
For this build, most of the parts were sourced cheap from Ebay and Amazon. The important elements are the 100W LED Driver (AC input), a grow light spectrum LED chip, a cheap CPU heatsink with fan, and a small power supply for the heatsink fan. Other tools used were a set of calipers to get the dimensions of the off the shelf parts, a 3D printer to make the enclosure, along with some miscellaneous wiring and an AC cord cut off a broken vacuum cleaner. All 3d modeling was done using Autodesk Inventor, and the parts 3d printed on a Rostock Max v2.
Step 2: Bottom Section, and Lens Mounting
First I attached the LED chip to the heatsink after drilling and tapping a matching hole pattern into the aluminum heat sink. Make sure to use some heat-sink thermal compound and don't over torque the screws. I tapped the 4 corner holes on the heatsink and affixed it to the 3d printed piece using 4x 10-32 socket head cap screws. the lens clicks into the chip , and is mounted on the exterior of the plastic piece. I had to use a soldering iron to melt out little pockets for the lens holder to fit just right... be careful if doing this with ABS or other plastics with voc's. I used self tapping screws to tap into 3d printed pilot holes for the metal lens holder. After backing them out carefully put the lens into the hole. it should click into place, and then tighten down the screws.
Step 3: Body and Electrical Components
First I mocked up the components (driver, heatsink, fan power supply) using Autodesk Inventor, and designed an enclosure around them which ensured good porting of the exhaust heat out of the enclosure. the power supply and driver board were both secured to the bottom 3d printed section using a little bit of epoxy putty. The bottom section was also secured to the body of the enclosure using a general two part epoxy. The bottom piece has a small ring to locate the middle section that sits over it.
Step 4: Top Section and Hanging
The top section provides an air intake for the heatsink, a hole for a cord grip (strain relief), and eyelets hooked to standard keychain rings to hang the light. The eyelets were printed slowly with 100% infill to make sure they are strong. the top section is again epoxied to the body of the enclosure, indexed by a small ring around the interior of the joint. It will actually join as a snap fit to mock everything up before putting the epoxy on for a permanent bond. For the final epoxy setup I made sure to clamp everything because the lid joint is holding the entire weight of the light.
Step 5: Hang the Light and Start Growing Plants
Installation is pretty straight forward. Use two different strings, cords, cables, or whatever you have on hand to hang the light above your plants. I used an old pair of boot shoe strings. The light runs very cool, and the fan is basically silent. the added benefit of an air cooled setup it doubles as airflow circulation to the plants. Next on the list is building a small grow tent.
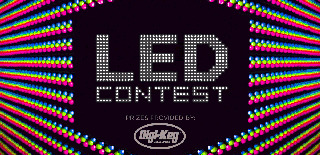
Participated in the
LED Contest 2017