Introduction: 12'x16' Mini-Barn/Shed With Gambrel Roof
Hello again everyone! In this instructable, I will be showing you how to build a 12' by 16' shed modeled after an old-style barn, complete with double barn doors, a partial loft, a barn-style roof, and a classic red and white paint job (although really, you can paint it whatever color you want). I built this shed for the farm program at my old high school, where I used to volunteer, and I now have a part time job there. The administrator there was going to buy a kit shed because the first shed was too small and falling apart, but I convinced him that I could build him a better shed from scratch, for less money, while at the same time teaching some of the students a bit about construction. It also helped that he really wanted a Gambrel roof, which is a bit hard to find in a prefab shed.
Let's get started!
NOTES:
This is not a 1 person project. A minimum of 3 people are required on some steps to build this without it being a huge pain.
Also, this instructable is written with the assumption that you already have basic carpentry experience and the ability to figure out small details yourself. For example, I will tell you to cut a board to a specific length and angle, but I will not specify the correct saw to use (hint: it's a miter saw) or how to line up the cut.
Also, I forgot to take pictures of some of the steps, but I have tried to cover those areas with computer-generated images.
Step 1: Check Your Local Building Codes
Before you begin construction, it's a good idea to check your local building codes to see if your shed will require a permit. Where I live, anything over 200 square feet requires a permit, which is part of the reason I chose to build a 12'x16' shed, at 192 square feet, it's just about as big as I can make it without having to worry about the hassle of getting a permit. Sometimes there will also be requirements such as a minimum distance from a property line, or a maximum height of the structure. If you are doing this on your own property and plan to simply ignore getting the required permits, it is still a good idea to follow the building code, that way if you have a nasty neighbor who likes to stick their nose where it doesn't belong (you know who you are...) who calls the county on you, the county will probably just make you get a permit, whereas if you built it too close to a property line or something like that, they might make you demo it. Better safe than sorry!
Step 2: Tools and Materials List
Before you begin, it's a good idea to make sure you have (or can borrow) all the required tools for the project. It's also a good idea to order your materials before you start building, or you won't get very far.
Tools List:
- Miter saw (unlike many projects, you can't really get away with substituting a handheld circular saw, in my opinion it isn't accurate enough)
- Table saw
- Circular saw
- Reciprocating saw
- Drill
- Impact Driver
- Air Compressor
- Roofing Nailer
- Drywall Square
- Rafter Square
- Level
- Calking Gun
- At least 2 ladders, one at least 14' tall
- Misc common hand tools
- Paint Brushes and Rollers
Materials List:
- 16 - simpson strong tie 18g 4x4 hurricane tie (4x4 version of the H1Z)
- 10 - simpson strong tie H1Z 18g hurricane tie
- 25 lbs - #9x3" star drive deck screws
- 25 lbs - #8x1 5/8" star drive deck screws
- 5 packs (500) - simpson strong tie #9x1 1/2" external hex flange hex head structural connector screw
- 1 box (7200) - 1 1/4" galvanized coil roofing nails
- 2 lbs - #12x1" electro galvanized steel roofing nails with plastic cap
- 1 roll (1000 sqft) - GAF feltbuster synthetic roofing underlayment
- 18 bags - architectural shingles (I used estate gray)
- 6 rolls - 7"x33' starter shingle roll
- 1 bag - hip and ridge shingles
- 1 roll - 7"x50' roll aluminum flashing
- 9 - 4"x10' galvanized steel drip edge flashing
- 1 tube - flashmate roofing sealant
- 2 rolls - 6"x75' roll grace vycor flex flashing
- 6 yards - gravel
- 3 - 4x4x8'
- 30 - 1x3x8'
- 1 - 2x2x8'
- 8 - 2x3x8'
- 9 - 2x6x12'
- 92 - 2x4x8'
- 30 - 2x4x10'
- 5 - 2x4x12'
- 6 - 2x4x16'
- 13 - 2x6x12' PTGC (pressure treated ground contact)
- 4 - 4x4x16' PTGC
- 2 - 2x6x16' PTGC
- 9 - 23/32x4'x8' pine plywood
- 20 - 19/32x4'x8'sheathing plywood
- 22 - T1-11 siding panel 4'x8'
- 16 - heavy duty hinges
- 1 - heavy duty double door latch
- 4 - window slide latch
- 5 gallons - barn red exterior paint
- 1 gallon - white exterior paint
- Little stuff I forgot
Materials cost is around $4,000.
Step 3: Site Prep
Before we start building, we will want to prepare the spot where the shed will sit. First, remove any vegetation underneath where the shed will go and do the same for 1-2 feet on every side. I screwed some scrap wood together into a crude 16'x20' rectangle so I could easily see where to dig. Once you've removed all the vegetation, lay down burlap or landscaping fabric to keep weeds from growing. Lastly, put several inches of gravel on top. For a 16'x20' pad, 6-8 yards is about what you'll need. After you've dumped all the gravel, level it out as best you can. It doesn't have to be perfect, as we can level the base of the shed with blocking later, but it should be within an inch or two. You may instead pour a concrete pad if you wish, although it isn't really necessary because the shed will be raised off the ground on skids.
Step 4: Lay Out Skids and Build the Subfloor
Now lay out 4 16' 4x4s on the ground as shown in the first image. There should be 3' 6" of space between the 4x4s. Next, build the subfloor using 13 11'9" 2x6s for the joists and 2 16' 2x6s for the sides. The subfloor is upside down in my pictures because I had a lot of people to help me, so I was lazy and just built it upside down with the skids already attached and then had everyone help flip it over. You will need to assemble the subfloor on top of the skids and then screw them together with 3 1/2" screws. The 2x6s all have 14 1/2" of space between them, except for the first and last spaces, which are 13 3/4". This is so that we can screw in the floor with minimal cutting or waste. When assembling the subfloor, regularly measure the diagonals to see if it is square. If the diagonals are the same length, you know the floor is square.
Step 5: Level the Subfloor
Before we build the rest of the shed, we need to level the subfloor. To do this, place blocks of pressure treated wood scrap under the 4x4 skids in at least 4 places along each skid. Use a long, straight board to extend your level to ensure accurate measurements.
Step 6: Build the Floor
Next up is to build the floor, which is made of sheets of 3/4" plywood. The pattern is fairly simple, just a row of 2 full 4'x8' sheets, followed by a row of a 4'x4', then a 4'x8', then another 4'x4', and finally another row of 2 4'x8' sheets. Use 1 5/8" screws spaced 8" apart into every joist to attach the floor. In order to avoid missing the joists when you are putting in the screws, use a drywall square as a guide by putting it against the edge of the sheet of plywood, directly over the joist. The drywall square will then parallel the joist on top of the plywood, and you can slide it over an inch and put the screws in next to it, and they will hit the joist.
Step 7: Side Walls' Framing
Before we assemble the side walls, it will save time to pre-cut all of the pieces. Both side walls are the same. Be sure to be accurate with your cuts, otherwise the walls will not fit together properly.
I assembled the side walls slightly differently than in the first image by making them in 2 pieces each. The goal was to make them easier to carry them out to the building site (I pre-assembled a lot of pieces in the school gym/shop). Unfortunately, it didn't work very well, so I would recommend sticking to the original plan when building yours and build them as just one piece each.
In the first image, in addition to all of the dimensions, you will see 2 "H" shaped areas which have been colored darker. You need to pre-assemble these before you fit them into the wall, otherwise there will be no room for the screws. The top is a double board, with the top board 3 1/2" shorter on either side than the other board. Once again, check squareness by measuring the diagonals. Assemble the double top board last. Use 3" deck screws for everything. All double boards should be screwed together every 8" in a zigzag pattern.
Cut List:
- 26 - 7'6" 2x4
- 8 - 6'8" 2x4
- 4 - 4'3" 2x4
- 12 - 6 1/2" 2x4
- 4 - 2'3 1/2" 2x4
- 2 - 15'5" 2x4
- 4 - 16' 2x4
- 4 - 2'6 1/2" 4x4
- 1/2" plywood scraps
Step 8: Back Wall Framing
Assembling the back wall is pretty straightforward. Unlike the side walls, the double top plate is longer on the top.
Cut List:
- 10 - 7'6" 2x4
- 2 - 11'5" 2x4
- 1 - 12' 2x4
Step 9: Front Wall Framing
The front wall is quite different from the back wall, as it includes a double door frame. Make sure it is square by measuring diagonals. Cut the small spacers above the door frame to each be a tight fit. Add the top of the double top plate last, etc. I don’t think I need to repeat myself anymore, you should be starting to know what you’re doing by now.
Step 10: Wall Framing Assembly
To attach the walls, simply line them up with the sides of the floor and attach the base plates to the floor using 3 1/2” screws every 6” in a staggered pattern. Screw the walls to each other at the corners using 3 1/2” screws every 8” in a staggered pattern. At the top corners of the walls, where the top boards overlap, screw each corner together with a pair of 3” screws. It is easier to start with the side walls, and then add the front and back. Make sure to hold the walls vertical as you screw them in.
Step 11: Add the Siding
Attach the siding to the framing using 1 5/8" screws every 8" into every stud, as well as the top and bottom plates. Draw lines on the siding using a large drywall square to help line up the screws with the studs. You will need to drill pilot holes through the siding, as it is very tough to start screws in it without them. You want to line up the top of the siding 1 1/2" below the top of the walls to allow room for the roof to go on properly. The interlocking panels will leave ugly seams on the corners, but we will cover these with trim later.
As you add some of the pieces of siding, you will cover the door and window holes. To remedy this, use a reciprocating saw with a long blade to trace the window and door frames from the inside and cut them out. You can also pre-cut the holes with a circular saw before you put the siding in place, which will result in a neater finish, but it is also easier to make a mistake this way. I chose to pre-cut my holes because I know what I'm doing.
Save the scraps of siding to use for the windows.
Step 12: Make Gussets for the Roof Arches
Next we need to make gussets for the roof arches. We will make them out of sheets of 3/4" plywood. To lay out this pattern on a 4'x8' sheet of plywood, first mark every 11 1/4" on the short sides of the sheet, and every few feet in the middle, then use a straightedge to draw parallel lines between the marks. I find that a 48" drywall square works very well for this. Next, mark every 9 1/4" along all of the lines you just made, and along the long edges of the sheet. Now, starting with the first mark on one edge of the sheet, draw lines perpendicular to the first set of lines, which extend 3 3/4" out from each side of the line. Skip to the third mark, then the fifth, and so on. Repeat this with every other line. Now do the same thing on the remaining lines, except start at the edge of the sheet, and skip to the second mark, then the fourth, and so on. Now all that's left is to draw zigzag lines between the tips of the second set of lines. When you're done, the pattern should match the second image. To cut them out, cut along the lines with a circular saw in the same order you drew them; cut the longest lines first, then the short perpendiculars, then the zigzags. As you finish cutting each zigzag line, the gusset will fall off, exposing the next line. Resist the urge to over-cut with the circular saw to save time, as it will weaken the gussets. Instead, use a jigsaw or handsaw to finish each cut. You will need 84 gussets.
Step 13: Cut the Beams for the Roof Arches
Next we need to cut the rafter beams which the gussets will join together. To do this, use a miter saw to cut one end of a 2x4 at a 67.5 degree angle (set the saw to 22.5 degrees). Then, measure 55 inches from the tip of the cut end, and cut the other end at 67.5 degrees in the opposite direction. Cut 60 beams this way. Use 10' 2x4s to get 2 pieces out of each board.
Step 14: Build a Jig to Assemble the Roof Arches
Next, we need to build a jig to ensure that our angles are accurate when we assemble the roof arches. To build the jig, first get a piece of scrap plywood, a few feet wide should be enough, and screw one of the rafter beams into it. Then, get another rafter beam and screw it into the plywood next to the first one to make an isosceles triangle with a base of 101 5/8". That's it.
Step 15: Use the Jig to Assemble the Roof Arches
Now it's time to assemble the roof arches. Take 2 of the rafter beams and place them in the jig, use a gusset and 1 5/8" screws to join them together. Repeat this to join sets of 4 rafter beams together with 3 gussets, then flip each one over and add 3 more gussets on the other side, except for 2 arches which only have gussets on one side. Use 6 screws per gusset, 3 into each beam. Save 8 rafter beams for later; these will be used to make the roof ends.
Step 16: Make the Roof Ends
Now we make the roof ends. To do this, first cut 8 more rafter beams, but this time make them 61" long. Then cut 28 pieces of 2x4 blocking, each 9" long. Now assemble 4 more roof arches using the 8 longer pieces you just cut for the ends of the arches, and 8 normal pieces for the peaks in the centers of the arches. Then screw the 2x4 blocking into 2 of the arches as shown in the pictures, using 2 3" screws per piece. Drill pilot holes to prevent the blocking from splitting. There should be 4 pieces of blocking on each of the long sections and 3 pieces on each of the short sections. Once you have all the blocking screwed into 2 arches, flip them over, set the other 2 arches on top, and screw the blocking to the second arches to finish the roof ends.
Step 17: Add Loft Beams to 9 of the Roof Arches
Now we need to add the beams that will support the floor of the loft. The loft will span across the first 8 roof arches, and we will need one extra with a beam for the other end of the roof, totaling 9 beams. To start, cut the ends of 9 12' 2x6s at 67.5 degree angles (set miter saw to 22.5 degrees). Cut off as little of each end as possible to make the angles. The angled ends should make them look like big rafter beams. Now take 9 roof arches and screw the 2x6s to them so that they span across the bottoms of the arches. Use 2 3" screws through the end of each 2x6. 2 of the arches which need loft beams are the arches with gussets on only one side. The beams go on the same side as the gussets.
Step 18: Reinforce the First and Last Roof Arches
The first and last roof arches have both loft beams and 5 vertical 2x4s to reinforce them and provide something to attach the siding to. Space them evenly along the base of the roof arches, otherwise the siding will have nothing to attach to at the seams, and cut to fit. Attach them with 3" screws. Use a square to make sure they are perpendicular to the base. The arches you want to use are the ones that have gussets on only one side.
Step 19: Raise the Roof Arches
Once you have assembled all the arches, it's time to raise the roof. This requires at least 2 ladders and 3 people. Start at the back end of the shed, and place both ladders against one of the side walls about 10' apart. Take one of the reinforced end roof arches and have 2 people carry it up the ladders, while the third stands on top of the walls, or on a third ladder. The people on the ladders hand the arch to the person on the walls, who then positions the arch at one end of the roof, gussets facing in. Then have the people on the ladders move the ladders to the ends of the roof arch and screw the arch in place while the third person holds it vertical. Repeat for the remaining arches, using the arches with loft beams first, then the ones without, then the other end arch, working back to front. Use hurricane ties to secure the arches more firmly to the walls after you screw each one in. After you install the second arch, and for every arch after it, cut blocking to fit between the arches in 3 places per set of arches (see images for pattern, it's hard to explain). The arches should be evenly spaced, 1'3" on center.
Step 20: Add More Siding
Now, it’s time to put the rest of the siding on. Instead of measuring each piece and cutting it, just hold it up against the arch and trace the outline of the arch onto it, then cut along the lines, and you will get a very good fit. Attach the siding the same way you did before.
Step 21: Paint the Walls
In hindsight, now would have been the best time to paint the walls, before the roof went on. Good thing I made the mistake, now you don't have to! So yea, paint the walls barn red or whatever color suits you. Also paint the remaining pieces of siding so they're ready for later when we make the doors and windows.
Step 22: Add the Roof Ends
Attach the roof ends to the shed with 3" screws. You will need 2 ladders and 3 people again.
Step 23: Add the Roof Sheathing
Now take your panels of 15/32" sheathing plywood, haul them up to the roof, and screw them in with 1 5/8" screws or nail them in with sheathing nails. You want all the vertical seams to be centered on roof arches, so cut them accordingly. I find it is easiest to just screw the panels in with some overhang, then set the depth of the blade on a circular saw to just barely deeper than the plywood, and just cut them to fit in place after marking my center line with a drywall square
Step 24: Build the Loft
Make the loft floor out of scraps and extra from the roof sheathing. Use 1 5/8" screws.
Step 25: Install Drip Edge, Flex Flashing, Underlayment, and Starter Course
Now it's time to start actually putting the roof on. The order that you do things is very important here. Start by nailing drip edge on the bottom edges of the roof. You should nail every foot or so. Second, roll out flex flashing to cover the nail heads and seal the drip edge to the roof. You may need to use some 3M spray adhesive to help the flex flashing stick to the wood. Third, roll out rows of feltbuster synthetic underlayment (you can also use tar paper, but the synthetic stuff is much more durable), covering both sections of both sides of the roof, working from the bottom up, and securing the underlayment with cap nails or cap staples. Fourth, add drip edge to the sides. You want to start from the bottom up, and overlap pieces of drip edge by about 6". Also, instead of cutting new pieces for where the roof changes angles, simply snip the part of the drip edge that sticks down and bend it to the correct angle. Fifth, roll out flex flashing on the sides, on top of the drip edge and the underlayment. Sixth, roll out starter course, nailing every 6 inches, and about 2 inches back from the outer edge. Roll out the bottom edges first, then the sides. You will want to snap chalk lines before you roll out the underlayment to ensure that it is straight.
Step 26: Install Shingles on Steep Roof Faces
First, snap chalk lines, starting 13" above the bottom edge, and then every 5 5/8" after that. Now, starting on the left side, get a full shingle, line it up with the first chalk line, and nail it in place using the 6 nail pattern shown in the third image. It is important to nail at the indicated height so that the nails will not show between the rows of shingles. Next, get a full shingle and cut 6 1/2" off the left side of it. Line this shingle up with the second chalk line, and nail it in place. Think about where you are nailing so that the nail heads do not line up with the cracks between shingles. Continue cutting more and more off each shingle as you move up, 6 1/2", 13", 19 1/2", 26", 32 1/2", and then move to the bottom row again and add a second full shingle. Add full shingles to the first 6 rows and then repeat adding the cut shingles for the next set of 6. Once you reach the top of the steep section, cut the tops of the shingles off to be level with where the roof angle changes. Be careful not to accidentally cut the underlayment. Continue across the rows with full shingles till you reach the other side, then measure and cut shingles to fit to finish the steep sections.
Step 27: Install Transition Flashing and Starter Course on Top Sections
Now, nail a roll of aluminum flashing to cover the exposed tops of the shingles on the steep section of the roof, and fold it over and nail it to the top section of the roof. Seal all the nail heads with flashmate roofing sealant, then cover it with flex flashing, and lay down starter course the same way you did before, bottom first, then sides.
Step 28: Install Shingles on Top Sections
Now install shingles the same way you did before, except now you only need to use 4 nails per shingle, unless you live in a high wind area (check your local building codes). When you reach the top of the first half, trim the shingles down, but when you reach the top of the second section, just fold the shingles over the ridge and nail them down.
Step 29: Add Ridge Cap Shingles
To finish the roof, add ridge cap shingles by starting from either end and working towards the middle. Use 4 nails per cap shingle, and when they meet in the middle, cut a small rectangle to cover the seam and secure it with 8 nails. Use some roofing sealant on the exposed nail heads, and you're finished with the roof.
Step 30: Build the Doors and Windows
Cut the doors out of 2 pieces of T1-11 siding. Frame the backs of the doors with 2x4s as shown in the first image. Cut the doors to fit the door frame. Then cut the 4 windows out of scrap T1-11 siding and frame with 2x3s as shown in the second image. The windows should theoretically be 27" squares, but either cut them to fit the window frames, or be prepared to trim a bit off the edges.
Step 31: Attach the Doors and Windows
Have someone help you hold the doors in place while you screw in the hinges. Use 3 hinges per door. I replaced the little screws that came with the hinges with 1 5/8" deck screws to make it a bit stronger. Then attach the 4 windows in the same fashion, except that you only need 2 hinges per window.
Step 32: Paint the Trim
Now it's time to paint the trim. I found it was easier to paint the trim before attaching it to the barn. Paint all 4 sides of all the 1x3s with 2 coats of white paint (or whatever color you want).
Step 33: Build the Corner Trim
Now put together the corner trim. Start by ripping 3/4" off of 4 pieces of trim with a table saw. Then assemble sets of 1 full size piece and 1 ripped down piece into L shapes as shown in the images. Use 1 5/8" screws. You will need 4 pieces.
Step 34: Attach the Corner Trim
First, hold a piece of corner trim up against the corner of the shed, and mark and cut off the extra. Then, attach the corner trim to the corners of the shed. Use 1 5/8" screws.
Step 35: Attach the Window Trim
For the window trim, cut pieces to fit around the outside edges of the windows. On the 3 sides without hinges, you want to have the trim extend slightly outside the border of the window, such that it covers up the gaps between the window and the wall.
Step 36: Add Window Latches
Now add latches to the windows. Instead of using the little piece that the latch usually slots into, just drill a hole in the window frame. Just as with the hinges, I used larger screws than the ones that came with the latches.
Step 37: Add Door Latch and Trim
Add a heavy duty double door latch to the center of the doors, then frame it with trim as shown in the images. As with the windows, overhang the trim to hide the unsightly gaps around the edges and between the doors.
Step 38: Finished!
You're done! Enjoy your new shed!
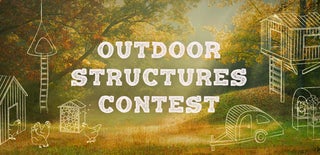
Second Prize in the
Outdoor Structures