Introduction: 2 Car All-Metal Workshop for 2 Grand
Overture: A Tale of Two Cards...
It began as a blueprint on an index card...
It began with a Lowe's credit card...
Based on a True Story,
Building Steel!
You say you'd love to have a two car garage, but you can't afford it? Or you need a workshop to build your dream airplane/car/boat/World Domination project? Here's a 400 square foot (20 X 20) all-metal shop for a little over two thousand dollars (A slap in the face to the bank!), built entirely from common parts available at any home improvement center.
This shop fits our budget because it's built without using a concrete $lab, expensive framing or siding. It's based on the old Quonset Hut design dating to World war II, although the construction method is different. The original Quonset Hut was a 20 by 48 foot hemicylinder (half cylinder); this one is slightly less than half the size of the original. Anybody that knows anything about structural design will tell you the dome is the strongest shape possible for a building - Buckminster Fuller made geodesic domes a household word. But domes are hard to build, and don't make the best use of floor space. The Quonset Hut is a "dome" in one dimension, while still maintaining a rectangular floor plan. It's much easier to build, because there is no need for tricky angles (as a geodesic dome requires) or compound curves, and it's still very sturdy.
The framing consists of half-circles of 1" thin-wall metal conduit and the skin is ordinary galvanized corrugated steel. Galvanized metal was chosen over wood because metal does not get eaten by termites, require frequent painting, or rot. Also, my husband is a sheet metal ace with 30 years of aircraft mechanic experience!
This building has stood up to the worst thunderstorms the desert southwest can throw at us, with wind gusts estimated to be in the 70 mph range. The rounded shape makes it highly wind resistant, and I think it would even survive an earthquake, because it's still just slightly flexible.
Step 1: The Problem and the Solution
My husband was a "shade-tree" mechanic, in the sense that many of his early projects were literally done under a tree. The time comes when something better is needed. This ramada was the first idea. It did a fine job of keeping the sun off of us, for a while, but it was made of wood. Even though the posts were treated and set in concrete, eventually the termites got to them. Then a nasty thunderstorm came along, picked the whole thing up about a foot, and (thankfully) set it back down. Now it's no longer structurally sound. This is a great time to build something better. We were looking for something comfortably affordable (since the bank won't loan anyone money unless they prove they don't need it!) and zero-maintenance (since we've got more interesting things to do than home repairs).
Since the Lord did not answer our prayer for a new shop by making one fall from the sky (Why should He, since He gave people talent to make things!), the next step was planning a replacement. Sadly, no blueprints exist for this building, since the only thing on paper was a sketch on an index card. Thought I was kidding about that index card, didn't you?
One thing we knew for sure was we did not want one of those "tin sheds" the home improvement stores sell. Every time there's a thunderstorm around here, there's always a tin shed or two wadded up like tissue paper and out in the road. Our thunderstorms are mean!
The design we came up with is less expensive than most pre-fab sheds, much sturdier, and reasonably easy to assemble. The total price was about $2400, including paint, but not including a door or tools. A door is planned for some time in the future. This is a labor-intensive project. It took my husband and myself (with an occasional walk-on guest star) about 2 months to complete. Some of the materials used were reclaimed, which cut down on the cost.
The New Mission: To Boldly Build better than men have built before!
(Grandiose Theme Music with scrolling prologue)
The Cast of Characters (Bill of Materials):
Quantities are approximate, but not hard to calculate with some basic math. This design made abundant use of materials we already had on hand. It can also be built in other sizes; We built a one-car version using 3/4" conduit.
- About 40-50 sheets corrugated galvanized steel, 24 inches X 12 feet
- About 50-60 ten-foot lengths of 1" thin-wall steel conduit
- About 50 1" conduit connectors
- Assorted conduit hanger straps
- 22- 3/4" X 24" steel rods for the anchors
- ABC mixture (also known as road base, a sand/gravel mix) for leveling the floor and back-filling the PSP
- 400 square feet of WWII surplus Marsden Matting (Also known as PSP- Pierced Steel Planking).
- 60 feet of PSP (see above) bent lengthwise 90 degrees (Don't ask me how to do this; we were fortunate to get it already bent)
- Around 2,500 5/32" blind ("pop") rivets
- Assorted framing connectors modified to accept conduit
- Steel drywall corners to finish the ends
- Caulking, paint, weatherstripping, etc. as needed
- Probably some blood!
Supporting Actors (Tools and Equipment):
- Site layout tools, such as level, chalk-line, stakes, long tape measure, etc.
- Various measuring and marking utensils
- Conduit bender (we made our own, but there are commercial ones available)
- Basic sheet metal tools, such as snips and Whitney punch
- Sheet metal shrinker (Not necessary, but saves time and effort), for the trim
- Drill and drill bits
- Pop (Blind) riveting tool (we used an air riveter from Harbor Freight)
- Hacksaw and other tools for cutting metal
- Basic hand tools such as screwdrivers, pliers and hammers
- Basic earthmoving tools (Pick and Shovel, wheelbarrow)
- Ladder(s)
- Scaffolding (as needed)
- A helper or two
- Band-Aids...
(Musical Montage of several trips to the home improvement store)
Step 2: Setting the Stage
A little pre-planning can go a long way in a construction project. We know the old structure has to come down, but why take it down first, then have to do everything out in the blazing sun?? So we did a considerable amount of prep work before engaging in the demolition.
The first order of business is the ribs, made of 1 inch thin-wall conduit. This stuff is dirt cheap, although you'll need a lot of it. There is no spine on this structure. The ribs provide side-to-side strength, and the corrugated skin provides end-to-end rigidity. This is known as a "semi-monocoque" construction, similar to the "unibody" in most modern cars. All this fancy verbiage means is that the skin is an integral structural component of the whole.
Since this building is half of a 20 foot diameter cylinder, the ribs must be curved to a 10 foot radius. All the conduits were marked at 6 inch intervals so the bend could be accurately controlled. The reason we made the bending tool (instead of buying one) is we only anticipated using it once, thus not justifying spending money on one, and, more importantly, we needed one that produced a larger radius bend. Ours is made just like the ones you'll find in the stores, except it's wood.
This required some amount of eyeballing. The important thing is to make sure the rib is flat after bending; all the bending has to be on the same plane. To do this, use the seam line on the conduit as a reference and make sure it's centered in the bender at all times.
The ribs are run through the bender 6 inches at a time until they match a 10 foot radius arc drawn on the floor (not shown). One "master" rib was made to conform perfectly to the radius, then all other ribs were bent to match. Don't make the mistake of using the previous rib to compare to the next one: That's a good way to make the small errors build into big errors! Make one that's perfect, then use it as the master template for all the others.
Notice that the conduit comes in 10 foot lengths, and 1/2 the diameter of a 20 foot circle is a bit over 31 feet. Several lengths of conduit will need to be coupled together to make each rib.
Step 3: Out With the Old!
Now we're almost ready to dismantle the old structure. 22 (11 each side) steel stakes were prepared as the primary anchors of the building. Each rib will be slipped onto and bolted to a pair of these stakes. Reference stakes were driven at the corners before demolition. The new shop will be up against the trailer, just as the old ramada was. This adds an additional level of strength to the completed structure.
The goal was to salvage and reuse as much of the old structure as possible; thus it's more of a disassembly than a demolition. The Marsden Matting was first removed and stacked for reuse in the new shop. This stuff has hooks and slots on the edges, allowing it to be linked together into a strong base. It was originally used as temporary runways during WWII. Each plank is ten feet long, 15 inches wide, and weighs 66 pounds, so this phase is a lot of work.
Next, the corrugated steel roof was removed and stacked for reuse. The old steel will be used for details like the ends, where the extra holes can be worked around.
Finally, the wood was removed. Some of this will be reused to build the needed scaffolding. Some was used for the evening's weenie roast. One post was left as a reference point, to be removed later.
The site is now as bare as the Marine base at Khe Sanh, Vietnam, after the Marines evacuated. Everything useful is removed, and everything else is burned.
Step 4: A Firm Foundation
(Music: Sixteen Tons)
Building your house (or your workshop) on a rock is preferable to building it on sand; desert dirt, though, after it's been packed down, is nearly as good as concrete and a lot cheaper.
The two sides, where the structure will be anchored to stakes, are critical. After laying out the floor plan and making sure it was square, we trenched down far enough to bury the bent Marsden Matting (PSP). The PSP was carefully leveled, as this will be our reference for leveling the floor later. It was also back-filled with gravel and watered down.
The prepared stakes from the last step were driven into the holes in the PSP at two foot intervals, at which point we hit our first major snag... There is no feeling quite like finding out there's a water pipe you didn't know about... Stop the flood! That cost us two days work, because a "helper" (who was subsequently fired from the project!) dug up the whole foundation on that side in an effort to "fix" the problem... and didn't fix it.
Well, we got the leak fixed, repaired the damage from the helper's bumbling efforts, frog-marched the helper off the property, and moved on. The site was roughly leveled with a layer of ABC gravel.
If you've ever tried to level a plot of ground, you know that's not as easy as it seems. We have a friend with a small yard tractor, so we called upon him for help. Problem was, he wasn't very well versed in earthmoving at the time, and he found out it wasn't as easy as it looked. We wound up doing the final leveling by hand after all.
On to the floor!
Step 5: First Floor - Seabees and Sledgehammers!
(Music: Seabees Hymn)
Lord, stand beside the men who build, And give them courage, strength, and skill...
Someone once said, "Nothing is impossible if you have vision, perseverance, and an endless supply of cheap labor!" Well, two out of three ain't bad. During World War II, Seabees (Navy Construction Battalions) built more than 100 airstrips out of Marsden Matting, often in extreme conditions of disease and climate, frequently under enemy fire, in as little as a week! These guys were good. Their emblem was an angry bee holding a Tommy Gun, a wrench, and a hammer. They could build airfields in a week because they had hundreds of men working on the project. My husband and I had only... Us. So it took a little more than a week. Of course, it wasn't a 5,000 foot runway, either.
The Marsden Matting we used, being War Surplus and all, had been used so many times already that it was pretty beat up. This made it much harder to assemble, requiring a lot of beating, swearing, stomping, jumping up and down, and swearing. Eventually, we got it all laid, and because the original method of airfield construction had worked so well, we decided to do it the same way the Seabees did it. They back-filled the matting with crushed coral (When constructing airbases on miserable tiny Pacific atolls that had no value other than their location), and then re-graded to remove the excess.
Lacking any crushed coral (Would've had to import it from Florida...), we used the next best thing: Several cubic yards of ABC gravel, also known as Road Base. This is a mixture of various sizes of sand and gravel, which tamps down into a firm base. We back-filled, raked it out, then hosed it down thoroughly and let it dry. Voila! Poor man's concrete!
We also used some of the bent matting to create a "curb" across the front, to control possible flooding.
We brought in a guest star with a welder to tack-weld the matting floor to the sides, preventing any shifting that might happen.
(Musical interlude while the ground dries... Smoke 'em if you've got 'em!)
Step 6: A Rack O' Ribs
...And we're back. Hope you enjoyed the intermission.
One more thing before we can begin erecting: We're going to need scaffolding, both to support ribs and support ladders. We used the remaining sound wood from the disassembly to build the two scaffolds. They are sized to hold the ribs in roughly the proper position, so once the ribs are draped onto the scaffolding, we can just pick them up and drop them over the stakes, then bolt them on through the previously drilled cross-holes. We cross-braced the scaffolding by tying it down to the floor with nylon straps. I knew those perforations would come in handy!
We joined 4 sections of conduit to make each rib. Using Pi (3.1416) times the radius (10 feet) gives us a length for one rib of 31.416 feet, or about 31 feet, 5 inches. We cut some of the 10 foot lengths into sections for minimal waste and made 11 ribs. All the ribs were hoisted up and draped across the scaffolding, then positioned on the prepared stakes and bolted down.
Now that we have a skeleton, the real fun begins!
Step 7: Blood, Toil, Skin, and Sweat
Never, in the history of building, have so few done so much with so little...
With apologies to Winston Churchill, the skinning of this building will be the most tedious and the most hazardous of the mission.
The corrugated steel is 12 feet long and 24 inches wide. We overlap it by roughly 2 feet horizontally (since the building is 20 feet long), and by two corrugations vertically. We made a decision to start on one side and go up, over, and down rather than starting on both sides and going toward the top. This is actually the only way to assemble this sort of building, because the steel would've gotten all dented up from leaning ladders on it. We have to do all work without putting any weight on the roof of the building. We could have started on the top and worked down both sides, but that would have been difficult because we don't have a tall stepladder, so we had to make do with two 11-foot ladders and a 6-foot stepladder. (Did I mention we're doing this on the cheap?)
The first course on each side was riveted to the Marsden Matting sides as well as the ribs.
The skin is also riveted end-to-end where the two panels of each course meet and overlap.
The second and subsequent courses must overlap the first until we get to the top, then each new course goes under the previous one. Think of shingles.
We installed temporary spars across the ribs both to help with alignment and for support while riveting the skin. Temporary fasteners, called "clekos," are used to keep everything lined up until the rivets are driven. We used blind rivets (also known as pop rivets) for the entire construction. One rivet goes in the bottom of each corrugation, on each rib. A cloth bag over the aft end of the riveter catches the rivet stubs, so they don't get scattered in the dirt to pierce tires. It's also helpful to have plenty of various clamps available to keep things organized.
About now came snag #2: Around lunchtime, that sheet metal gets hungry, and starts to bite! Sometimes, it seems bloodshed is necessary to ensure the success of a project.
(Short interlude for a trip to the first aid kit.)
Step 8: Drill. Rivet. Repeat. Repeat. Repeat.
Moving over the top, this project started to get a little dicey. Snag #3 was a shortage of ladder: The building is 10 feet tall, and the longest ladder we have is 11 feet. Don't tell the OSHA guy! Somehow we managed it with creative scaffolding. At the top, the ladders had to be leaned up against a temporary spar, with only inches to spare. Because the building is still partly skeletal at this stage, the ladders can be affixed to the ribs, making things safer.
Coming down the other side, now the next course has to be placed under the previous course, giving us even more glorious opportunities for lacerations and contusions.
Now we had to hurry - the potential of a major windstorm coming at this point was terrifying. The building is extremely vulnerable at this stage, because it's not yet structurally sound, but has lots of wind sail area. This was the time to use every daylight hour to finish the skin. It's amazing how many rivets it takes for something like this!
Forging on ahead, we finished the skin in 9 days.
(Musical Interlude while we drink a celebratory beer and rest up from all that ladder climbing and riveting.)
Step 9: This Is the End, My Friend
(Of The Building, Not the Project!) Now we can address finishing the ends of the building, which will give it side-to-side rigidity as well as a doorway and a skylight.
The openings were framed with more 1" conduit, riveted together with brackets which were then riveted to the structure. The brackets are adapted from framing connectors (Usually used to join 2X4s together). The face of the structure is framed and four diagonal braces run inside the building to the second rib from each end for extra strength. The leftover corrugated steel from the disassembly of the old ramada gets used to skin the door end. It's riveted on the same way the rest of the skin was installed.
The back opening is only what sticks up past the roof of the trailer it's attached to, and this will be a skylight, using translucent corrugated plastic. It gets framed the same as the door opening, including a horizontal member at the roof-line of the trailer. This plastic needs special treatment. Since it expands with temperature at a different rate than the steel, the mounting holes need to be oversized and washers placed under the rivets. If you ignore this important step, the plastic will crack in a short time. We also cut a hole in the center of the skylight and installed a louvered vent.
The ends were sealed with foam sealing strips made for use with corrugated material.
Step 10: Finishing Touches
Now we need to finish the edges of the building and the doorway. Again, the theme here is low-budget, zero-maintenance. We found some thin steel angle which is usually used to make corners in drywall installations. This is almost beer-can thickness, but it's good for trim, and will help make the shop weather-tight. After painting the structure, we ran the angle through a metal shrinker (which automates the process of putting a lot of little crimps in the metal) to give it the proper curve for the roof trim, punched rivet holes in it, and put it on with even more blind rivets. The door trim was done the same way without the curves.
Every single rivet on the exterior got a blob of caulking on it to keep the rain out. (I'm so sick of looking at rivets!) The seams between the corrugated panels were caulked also.
About this time the cat discovered the new building, lost his grip, and slid all the way to the ground. I guess nobody ever told him about domes!
Back to the war surplus department for some appropriate lights. Two of these warehouse lights do a good job of interior illumination. We simply hung them from the ribs with even more of those handy conduit clamps.
(We're Finished! Grand sweeping music with a bottle of champagne and high-fives all around)
But will it stand?
Step 11: The Acid Test!
We finished this project just before our Monsoon season started.
We watched with bated breath while the storms rolled in.
The rains descended. The water rose. The hail... Hailed. The wind blew and beat upon that building, and it did not fall, for it was built on steel and hardened desert soil.
This building will probably last 100 years!
(Triumphant Musical Finale)
Postscript:
No cats were harmed in the construction and use of this building.
Epilog:
One of the reasons for needing an enclosed building was to build the dream airplane, which is even now being built!
Challenge:
First person to build something similar wins a one year pro membership! Photos imperative! (Author's opinion is final.)

Second Prize in the
Metal Contest
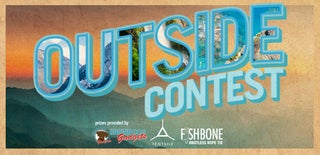
Participated in the
Outside Contest
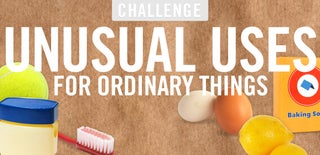
Participated in the
Unusual Uses Challenge