Introduction: 2 Ways to Make Custom Electric Guitar Knobs
"You see, most blokes, you know, will be playing at ten. You're on ten here, all the way up, all the way up, all the way up, you're on ten on your guitar. Where can you go from there? Where?" ~ Spinal Tap
Of course, the only solution is to replace your volume knob with one that goes to eleven.
In this Instructable, we machine a potentiometer knob from solid brass for the volume on an electric guitar. For those of you who want to make but don't have access to machine tools, we've included a link to the STL, STEP and SolidWorks files for 3D printing.
Supplies
The following supplies are used to machine a brass knob. For a 3D-printed one, all you need is a printer and your preferred filament.
Materials
- Brass stock (1-inch round bar)
- Wax
- Cutting oil
- Boric acid
- Superglue
Tools
- Lathe
- Milling machine
- 90° cutter
- Dividing head
- Small file
- Sandpaper
- Grinder
- Blowtorch
- Arbor press
Step 1: Measure the Potentiometer
There are 3 "standard" electric guitar knob types, so the first step in making a custom knob is determining which type your guitar uses and other key dimensions:
- Remove the old knob
- Check for a set screw first and loosen this with a screwdriver or Allen key if needed.
- Gently pry up the knob using something thin and flat like an old credit card or ruler.
- Count the splines on the potentiometer
- The most common type is Metric/Coarse, with 16 splines on a split shaft, or 18 total inside the knob.
- Imperial/Fine potentiometers have 20 splines on a split shaft, or 24 total inside the knob.
- Lastly, solid shafts are smooth with no splines and instead, normally use a set screw to clamp the knob to the potentiometer.
- Measure the shaft diameter
- Metric shafts are usually 6 mm.
- Imperial shafts are typically 5.95 mm.
- Solid shafts are normally 6.35 mm.
- Measure the distance from the face of the guitar to the top of the potentiometer - this will determine how deep the spline groove is cut later.
In this tutorial, we are working with a metric potentiometer but the same techniques could be applied to imperial pots too. Similarly, the same steps can be followed to make a knob for a solid shaft, replacing the spline punching with the inclusion of a set screw instead.
Step 2: Making a Spline Punch
The next few steps will cover the machining operations for making a metal volume knob. If you're planning to 3D print your knob instead, skip ahead to Step 7.
The first challenge is making the female version of the potentiometer spline. Machining this internal geometry can be tricky, so here we opt to make a punch, which matches the geometry of the spline.
I make the punch from 6 mm silver steel and start by facing off the end.
To machine the splines on the punch we need a cutting tool with an included angle of 90°. The one shown here is homemade but any similar 90° cutter should do the job. I used a milling machine with a dividing head to set up the cutter and punch. The spline we are copying has 18 grooves, so the workpiece needs to move 20 degrees at a time.
I roughly align the dividing head to the mill axis and mount the faced-off silver steel in a collet. I then put the cutter in the mill spindle. I tilt the dividing head slightly off-axis to provide relief for the punch and engage the worm drive on the dividing head.
Of course, we need to know how deep to cut each grove, so I gently move the y-axis on the mill until the cutter just begins to scrape the surface of the workpiece, providing me with a zero reference. I can then move the mill axis by the required amount.
Once all 18 grooves are cut, that’s the cross-section of the punch shaped. The surface finish isn’t great, so I clean it up with a file. In its current state, the punch is too soft, so it needs to be heat-treated before we can put it to use. For this, I heat the punch with a blow torch, dip the end in some boric acid to protect it from oxidizing, heat it again until it glows red, and quench it in water. I then clean the shaft with some sandpaper, reheat the punch to a straw colour, and quench it again to temper it.
The punch benefits from concavity ground into the end, to provide some rake, so we added this using a grinder.
Step 3: Punching the Spline Hole
The body of the brass knob is made from 1-inch round brass stock. I begin by machining the inside, which is a hole in which the spline will be punched, and a large chamfer to clear the potentiometer nut.
To use the punch, I mount the brass workpiece onto a press. Punching operations require a lot of force, so a liberal application of cutting oil helps reduce this. The resulting spline should now fit nicely onto the potentiometer.
Step 4: Machining the Knob Body
I mount the knob to a super glue arbour for machining. This variation includes an extending spigot in the centre to help with aligning the component. (The arbour shown here is unnecessarily large because it was made for a different project.)
One of the reasons the superglue arbour is so useful is that it can be machined in situ, which makes it very accurate. I can also machine the spigot in situ for perfect concentricity and a nice fit in the spline for concentric location.
The blank is slightly too long so, although unnecessary, I also use a centre to support the workpiece as I rough it to size, reducing the risk of the superglue bond failing.
I use a protractor to roughly measure the angle of the numbered face and machine the brass knob to the same shape.
Step 5: Adding the Taper & Knurling
Now it’s time to machine the grippy part of the knob. Normally, machinists would use a knurling tool but instead, I’m going to demonstrate a shaping technique. I begin by swapping the topside with a modified alternative. I then mount a lever and fulcrum to the bed, which is then coupled to the modified topslide.
This part of the knob is slightly tapered too, so I machine the taper using the lever feed, and then I apply a chamfer before setting up to form the knurling. This method ensures that I cut the knurling at the same angle as the taper.
To remove the knob from the superglue arbour, I remove the spigot and tap a bar of aluminium located at the bottom of the spline. The bottom face of the knob has leftover dried superglue which I remove with emery paper.
Step 6: Engraving the Label & Dial
For an easy way to mount the knob onto the engraving machine, I reinsert the punch we made earlier.
To mark the divisions for engraving, I simply use a pencil mounted in the lathe tool post. This leaves clear markings which can be easily removed once the engraving is finished.
The engraver is a pantograph machine that works by copying the path of a stylus onto the spindle. I define the path of the stylus by following the lettering. To engrave the numbering, I tilt the knob over at 45 degrees and align the pencil divisions with a mark on a special holder made to fit in the engraver.
Just for fun, after the engraving was finished, I mounted the knob in the grinder and used it to generate a lovely pattern on the top face of the knob. To finish, I melted some black wax into the engraving to help the lettering and numbering stand out.
Step 7: 3D-printing a Custom Knob
The STL, STEP and SolidWorks files for a volume knob can be downloaded here: https://grabcad.com/library/electric-guitar-volume-knob-1
We used the Bambu Lab X1 Carbon 3D printer and associated slicing software and PLA basic filament to print the knob. (See image 2 for additional settings.)
Thanks for reading this article and don't forget to check out the accompanying YouTube video!
Disclaimer: Note that the volume knob does not actually make your guitar any louder.
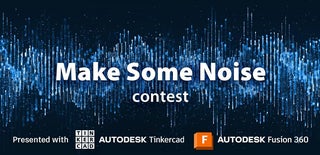
Participated in the
Make Some Noise Contest