Introduction: 2000 Watts Induction Heater
Induction heaters are a great piece of tool for heating metal objects that can come in handy in a DIYers workspace when you need to get things red hot without messing up the whole space.
So today we are going to create an extremly powerful induction heater totally from scratch and the good thing is that this unit is built using customized Printed Circuit Boards which makes the whole building process for you guys a piece of cake and neat aswell.
Step 1: Tools and Material Required
- List of material required for this project :
- Customised printed circuit board
- 12 AWG & 16 AWG enamel copper wire
- Ferrite cores
- 12v DC fan
- Heat sink
- Resistors
- Capacitors
- Diodes
List of tools used in this projects :
- Soldering Iron
- Soldering wire
- Cutters
- Pliers
Step 2: Designing the Schematic
The unit works as an LC oscillator and thus inducing the current into metal objects with a continiously changing magnetic field.
The input is a DC voltage ranging from 12v to 36v. At the initial stage we have the DC fuses just to make sure that thing wont blow up in case of any fault. From there the supply is split into two parts, one of which is the LM7812 12v voltage regulator that is used to drive the cooling fan to keep the mosfets cool.
The other part of the supply is then fed to the four N-Channel mosfets, a pair of which is driving the two channels that are working alternately and thus changing the DC voltage into a continiously changing electric field.
Now there are two possible configuration, we can either go with only one onboard inductor and have the output coil split into two parts which makes the design of the output coil a bit more complicated thus we decided to go with the tanks circuit configuration which offers two on board inductors and has a single output coil inducing the electromagnetic field into the object being heated.
With this design in mind we have designed the customized PCBs on easyEDA, an extremly useful platform for PCB designing
Step 3: Designing the Printed Circuit Board
As I finished the schematic I have decided to go with designing a dedicated PCB for the induction heater as it will not only help us to keep everything neat but I intended to design this unit so thats its capable of further modifications for my other DIY projects.
The idea of designing a PCB might seems to take a whole lot of efforts but believe me it worth that all when you get your hands on customized boards. So with that in mind I designed the PCB for the induction heater unit.Then i also made customised packages for inductors on the boards.
I have also added four mounting holes which will be helpful to mount the controller and also hold the cooling fan along with the heat sink above the MOSFETs.
Schematic, Gerber Files and BOM(Bill Of Material):
Step 4: Ordering the PCBs
Unlike any other customised part for your DIY Project, PCBs are surely the easiest one to get. Yes Now once we generated gerber files of our finilized PCB layout we are just a few clicks away from ordering our customized PCBs.
What all I did is to head upto JLCPCB and after going through a bunch of options there I uploaded my gerber files. Once the deisgn is checked for any errors by their techinical team your design is forwarded to the manufacturing line. The whole process will take two days to complet and hopefully you will get your PCBs within just a week. JLCPCBhave made this project possible by their support so take your time and have a look at their website. They are offering Standard PCB, Quick-turn PCB, SMD etc so for discounts of upto 30% on your PCBs visit this link. Gerber files,schematic and the BOM (Bill Of Material) for the PCB is avaliable here.
Step 5: Assembling the PCB
As expected the PCBs arrived within a week and the finish is just too good. The quality of the PCBs is absolutely flawless. Now time to gather all the components as mentioned in the BOM(Bill of Material) and drop them in place.
To keep things flowing we need to start with the smallest component on the PCB which is some resistors, diodes and some connectors. After soldering these components we have to move towards larger components. And then we have bend the Mosfets legs and soldered it on the board.
Step 6: Attaching Capacitors and Cooling Fan
After that we have placed the capacitor on the boards. In order to cool down the MOSFETs we have placed the 12v dc fan with the heat sink sandwich in between.
But after that we have realized that this fan is not enough powerful so we have replaced it by some bigger one.
Step 7: Making the Inductors
For tank circuit we have use 24mm ferrite core and 16 AWG enamel copper wire. We have wind 22 turns on the each ferrite core in order to get suitable frequency. And then soldered it on the boards.
Step 8: Induction Coil
After placing the inductors its time to make the induction coil and for that we have used 12 AWG enamel copper wire. First we have straitened the wire and then wind it on the PVC pipe in order to get the perfect shape. And screwed it on the terminals.
Step 9: Final Results
This induction heater performed like a champ. From a metal ruller to a half inch thick rod, it took not more than a couple of seconds to heat it red hot.
The heater can work inbetween 12v to 36vDC and can handle surges of upto 2000 watts which is a suffient amount of energy to handle large objects.
Drop down your thoughts in the comments section below.
Regards,
DIY King
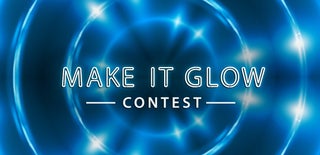
Runner Up in the
Make it Glow Contest