Introduction: 2.5D Divine Mercy Edge Lit Acrylic Lamp
The Divine Mercy image shown to Saint Faustina had two rays of light emitting from Jesus Christ. However, all the realistic Divine Mercy images that I have come across are flat pictures - mostly paintings. Some artists do create 3D figures, but usually the rays of light are depicted as solid blocks of structure, which I find rather odd, as they don't look like rays of light.
With my CNC machine, I can now carve 2.5D Divine Mercy images on transparent acrylic sheets and use these as edge lit lamps. This results in a more realistic image of Jesus Christ floating within the piece of acrylic. Red and blue LED's are placed under the rays, while white LED's are place to illuminate the body of Jesus Christ at the center.
I use LinuxCNC to control my 3-axes CNC machine. Within LinuxCNC, there is a function called Image-to-Gcode which I can use to convert any image to g-code. I then run the g-code at my cnc machine to cut the acrylic surface of my work piece using ball nose end mill tool bits for both roughing and finishing runs.
Before I can proceed with generating the g-code, I have to convert a flat Divine Mercy image of Jesus Christ into a greyscale heightmap image using GIMP photo editing software. This step requires some artistic skill on my part - determining which portions of the image to make darker and so to cut deeper by the CNC machine and which areas are to be lighter and so be cut shallower.
I make the base for the acrylic lamp out of wood, and install cylindrical shaped LED's in it. The base consists of the wooden block, LED's, resistors, barrel socket, and wiring. Therefore, I machine the wood into a pattern of grooves so that I can install the LED's, resistors, barrel socket, and wiring in place and solder them together securely. In this way, the electrical connections do not touch one another if they are not required, the wood being the insulator. After that, I turn the base over and machine out the slot for placing the acrylic sheet.
The electrical wiring is glued in place and then covered up with a piece of cardboard to prevent them from moving. The wooden base is finally given a coat of varnish for finishing.
Supplies
- Transparent cast acrylic sheet 2 mm thick
- Ball nose 3.175 mm dia. milling tool for roughing the acrylic sheet
- Ball nose 2 mm dia. milling tool for finishing the acrylic sheet
- 60 degree conical mill bit for cutting the wordings and rays on the acrylic sheet
- Twist drill 3 mm dia. for peck drilling of the base for placing the round LED's
- Straight end mill 3.175 mm dia. for cutting the grooves in the base
- Straight end mill 2 mm dia. for cutting the base slot for the acrylic
- Soldering iron and solder
- LED's - 3 pcs red, 3 pcs blue, 3 pcs white cylindrical type
- Resistors 3 pcs 330 ohm 1/4W
- Barrel socket 1 pc 5.5 mm x 2.1 mm
- Bare copper wires
- CNC machine
- Wood strip 40 mm x 19 mm x 150 mm for the base
- Power adapter smps 12 VDC 1A for powering the LED's
- Portable power drill with 10 mm dia drill bit
- Sandpaper, varnish
- Jig saw or hand saw
Step 1: Cutting the Height Map on Acrylic Sheet
Cutting the height map of the image of the Jesus Christ is key to the whole project. In order to create the height map image, I use the free open source software called GIMP. By manipulating the dark and light areas, I am able to differentiate those areas that I want to cut deeper or shallower using my CNC machine later.
Once I have a satisfactory height map image, I open it with LinuxCNC which my CNC machine operates on. LinuxCNC has a special g-code generating feature called Image-to-Gcode. By entering the required figures, I can generate a g-code file that will enable the CNC machine to scan repeatedly over the acrylic work piece in either the x or y direction as I wish. At the same time, the cutting tool will move up and down in the z direction according to the height or depth interpreted by the software.
I save a g-code called rough cut and then another g-code called fine cut. First, I run the rough cut g-code with the larger sized ball nose milling tool. When this is completed, I run the fine cut g-code using the smaller sized ball nose milling tool. That completes the height map cutting.
After this, I change the tool to a 60 degree conical milling bit for engraving the text below the height map image of Jesus Christ. Text paths can be created with Inkscape, a vector open source software. The text paths is converted to g-codes with the use of another software called dxf2gcode. This g-code can be opened at my CNC machine to cut the wordings below the 2.5D image of Jesus so the tool paths of the text cutting g-code must be positioned correctly so that the engraving can be done below the image of Jesus Christ.
The last step for engraving the Divine Mercy image is to add in the rays. For this step, I flip over the acrylic sheet and engrave on the front side. The previous steps are all engraved on the back side of the acrylic, with the image and wordings flipped. The rays are quite straightforward. They just consists of straight lines. Their g-codes can be generated by dxf2gcode software. The tool used is the same 60 degree conical milling bit.
Step 2: Machining the Base for the Edge Lit Lamp
Wood is an excellent work piece medium for my CNC machine. I chose wood as the base for my Edge Lit Lamp.
For the Edge Lit Lamp of the Divine Mercy to work, the base have to:
- Be able to install LED's, resistor, sockets, wiring
- Be able to position an acrylic sheet vertically
- Be stable at rest
- Be pleasant in appearance
- Be machinable by my CNC machine
- Be easily available
I designed the base such that the LED's are spaced evenly apart. I also choose to work with 3 mm diameter cylindrical shaped LED's because they can be inserted into drilled holes and fit snugly in wood. The spacing of the LED's is also changeable, unlike ready-made LED strips. The Divine Mercy image has also a requirement for red and blue colored LED's. All the LED's are soldered manually. In order for me to do this easily, I fabricated a jig so that I can position the 3 LED's and the resistor according to the final destination at the base.
Why 3 LED's and a resistor?
Well, I have 12 VDC adapters available so using 3 LED's just suits me. Connecting a resistor to the LED's is to avoid overheating due to over current. If needed, the circuitry can be modified to suit. The reader needs to read up further on connecting LED's if they are not familiar with this.
I work out the connections that I need for the LED's, resistor, socket according to their placements. Then I work out how I am going to place the components in position, taking into consideration their measurements, shapes and sizes. Then I draw the layout, convert them to g-code and let the CNC machine cut out all the grooves and pockets that is required.
The grooves for the electrical components are cut with a 3.175 mm diameter end mill using my CNC machine. After the grooves and pockets have been cut, I replace the end mill with a 3 mm diameter twist drill and run another g-code for peck drilling. The peck drilling g-code moves the tool to the specified position at the wooden base, drills it to the required depth, moves the drill bit up again and then moves it to the next position and repeats the process until the holes for inserting the LED's have all been drilled.
I then overturn the base, change to a 2 mm diameter end mill tool and then run another g-code to cut the slot for inserting the acrylic sheet.
I then temporarily place the barrel socket into the cut out pocket of the wooden base, determine its axial center position, remove the barrel socket again and then manually drill a 10 mm hole at that location. This is the hole for pushing in the barrel plug of the 12 VDC power supply.
Step 3: Installing the LED's, Resistors, Socket and Wiring
In order to solder the leads of the 3 LED's, I use a jig to position them so that their distances apart will be exactly the same as the holes drilled in the wooden base. The LED's have to be connected with a certain polarity, so I make sure that I bend only the longer leads of the LED's while leaving the shorter leads straight. The heads of the LED's are positioned inside the holes of the jig for soldering.
Once the soldering is done, the leads are snipped off, leaving only the soldered joints. The assembled 3 LED's and a resistor are then placed into the holes already drilled in the base. I have to be careful to place the correct colored LED's in their proper positions in order for the final edge lit lamp to show red rays on the left, white in the center and blue on the right.
The barrel socket is also soldered and placed in position. All the connections are done with bare copper wire and soldered.
During the course of assembly, I often test that the LED's are working correctly by connecting a 12 VDC supply to their leads. The 3 LED assemblies are connected in parallel.
Step 4: Finishing the Base
The base are cut off with a jig-saw, sandpapered and varnished. The electrical components are glued in place with epoxy glue or hot-melt glue so that they will not move. The bottom of the base with the grooves and electrical components are then covered up with a layer of cardboard or felt so that they are no longer visible.
That completes the making of the 2.5D Divine Mercy Edge Lit Acrylic Lamp.
For those interested, they can check out my other interests:
My Website: https://divinemercylamp.com
My Blog: https://divinemercylamp.com/yoon/
My Facebook Page: https://www.facebook.com/artengrave
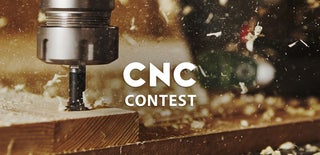
Participated in the
CNC Contest 2020