Introduction: 3D Geometric Optimization of Plant Production in Micro-gravity and Growing Automation System Concepts
Human exploration of deep space, Mars, outer planets, and even other solar systems depends heavily on our ability to survive and adapt to adverse conditions. This challenge includes growing sustainable food that we can take with us into the great unknown.
For this contest entry, I decided to focus on how this design would fit the cubic volume of the EXPRESS rack, but also be applicable and scale-able beyond that rack as well. This is a professional level contest entry.
Supplies
Fusion 360 CAD
Step 1: The Problem and Design Approach
My design approach here was to focus on a few key concepts:
- Modularity. The swap-ability and pattern-ability are key points.
- Access.
- Automation
- Scale-abilty
The design is still in the early stages, however the potential to automate this harvesting, watering, PH and moisture level monitoring, and light dosing, are all built into this design. The creators of Farm-bot have developed many of the tools uniquely suited for adaptation to this application.
Shapes to consider
I considered several shapes, including rectangular, rhombic dodecohedron, pentagonal dodecohedron, octagonal, cylindrical, and other shapes. The challenge with dodecahedrons is the ability to wire in the water supply, automated harvesting tools, and sensors to insert into the soil for continual monitoring.
Something prismatic seems to allow the access to 'rows' of plant beds, which is how much of the traditional farming has been done on land for generations.
Hexagonal prisms were one of the early design concepts. These can be patterned on a flat wall or even around a sphere with no dead space between them.
However, adding the additional sides to a shape such as an octagon seems to be able to include more plant mass within a cubic volume and the Octagonal - square pattern allows the squares or in the case of the portions of the pattern that interface walls or an end boundary of the patter, triangular shapes; allows storage of water, electrical wiring, extra seeds, or other equipment in removable drawers in between the stages. This is similar to a concept for a soccer ball.
Given the nature of launch vehicles, the cylindrical profile of certain ISS modules is a function of what can optimally be fit into a cylindrical rocket payload. Hence, a likely shape for a Greenhouse module would also be cylindrical in nature.
Step 2: The Conceptual Design
The main features of the design include:
- Octagonal shape to optimize plant mass within the given volume
- Modular light panels that are removable to repair/maintenance the pod
- Central windows and control panel for monitoring the growth of the crop and PH levels, Moisture levels, etc.
- Pattern-able design within a cylindrical volume of a greenhouse module.
The plants here are placed on a central hub while the lights remain a spoke design. This may be suitable for plants which have a wider angle of growth from the point in the ground substrate which they germinate from. Plants which are shorter and wider in nature may be more suitable to be grown on the outer surfaces of the hexagon and have the internal hub become the light source.
Some of the detailed sections have yet to be fully modeled in CAD, but the seeds would be contained within an irrigated packet of soil. The outside of this packet would be either a mesh material similar to how this is done in current ISS experiments or some other bio-degradable recycled paper based material to recycle items in long term spaceflight.
A two pronged probe would plug into the bottom of the seed pouch from the central hub base and would contain two sharp electrodes which would be measured by a micro-controller to determine the resistance and capacitance of the soil to calculate moisture content and PH. This monitoring would be integrated with an irrigation system which could pump water to an embedded plastic ring within the inner body of the seed pouch to add moisture on a schedule and or when levels are detected to be too low, or by manual input from a touch screen from the front panel by the astronauts.
Step 3: Additional Design Features
An automated harvest system can be added to this build. Similar mechanisms to the hedge trimmers and hair clippers with a stationary set of blades and a reciprocating set of blades. This can ride along the longitudinal axis of the system and have a fan and a net in order to propel the harvested plant matter into a mesh bag for collection after severing it from the stem.
For lettuce, this application works, but for other items such as fruit bearing plants, this approach could be adapted to create a shaking/agitating attachment to shake loose tomatoes, peppers, etc. those may also be severed and the plant matter collected for human sorting and use in compost at the end of the plant's fruit bearing life.
Another design feature is a modified seed pillow comprising a hybrid of 3D printed and recycled paper material. In an ideal long term spaceflight, plastic tools or other items can be ground down, processed, and made into new filament for a printer similar to the printer on board the ISS presently.
The paper would be pulped with water and pressed into a 3D printed mold similarly to how XYZ Adrian explains in this youtube video https://www.youtube.com/watch?v=0ItPfhx3ulw
a 3D printed Irrigation Ring would be embedded into a cardboard form with soil and fertilized also included, and then the top half of the mold would be molded or a mesh would be used to cover it and prevent excursion of the soil into the spacecraft.
There are many ideas to augment this system, however the first phase of this challenge is to primarily discuss high level concepts and use of 3D space.
Step 4: Conclusions
This is not the only way to achieve plant growth in 3D as there are many other challenges to long term spaceflight.
Do tomatoes grow in space? are they perfect spheres of itallian delight? or does gravity adversely affect fruit bearing plants? or do cherry tomatoes grow to the size of softballs with no gravity to wear them down?
What about harvesting these fruits with a vision system and picking robot arm? such technology exists and with the Farmbot API and other items, these things can be integrated into a full robust system.
https://farm.bot/pages/open-source
Alternative iterations of this concept may exist, including cylindrical designs such as those pictured on The Expanse
The harvesting arm could be fixed stationary and the plant drum could rotate to harvest the plants in this configuration, although when growing from the outside in, the plants must be wider at the base than the top, and many plants grow wider at the top than at the interface with the ground (think lettuce heads) and thus the configuration of my design i flipped this even though it makes the design mechanically more complex.
I am certain both configurations could be employed with different crops and could co-exist in a growing ecosystem.
Thanks! for any questions, please leave a comment.
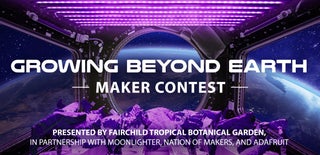
Participated in the
Growing Beyond Earth Maker Contest