Introduction: 3D Moon Lamp (Concrete&Resin)
Hi Makers!
In this Instructable we are going to make a 3D moon lamp to celebrate Apollo 50. The plan is to have a lightbulb inside a casted moon, which will have surface detail. Albeit I’m a little late to the moon party, I still wanted to go through with this project, as I wanted to make matching decoration for my table. Indeed, I’m talking about my most recent project, the floating bedside table. Originally, I was only making a decoration, but then I imagined how cool it would be if it was glowing. I wanted to stick with concrete as the theme for this one as well, however we both know that light can’t shine through concrete. That’s a bummer. Well, I guess I won’t join the party at all. Or will I?
Upon further research I discovered light-transmitting concrete. Even more interesting, I found that the maker nepheron had already made such a material and made a great tutorial…. a whole 9 years ago! He uses optical fibers as his light conductor, but I wanted the actual material to be translucent, so this left me with one option; to come up with the material myself.
Now, before we get any further, I know I could’ve just 3D printed the moon, but then, what fun would there be in the process of making? Besides, not everyone has a 3D printer.
I thought of and tested a few different mixtures like concrete and silicone, concrete and epoxy and even concrete with fibreglass. I knew that in order to preserve the translucency, only a small ratio of concrete could be added to a transparent material. In the end, I settled on 95% epoxy and 5% concrete by weight.
Supplies
- A lamp stand (I used this from Ikea)
- Cement or concrete of fine grain
- 160 mm transparent plastic globe, which can be taken apart ("small globe")
- 180 mm globe of the same type ("large globe")
- Epoxy or Polyester resin
- Oil-based modelling clay
- Black and white paints
- A lightbulb (which must fit through the hole of the lamp shade ring!)
- Some fishing line
- Strong glue (I made the mistake of using a weak one)
- And some tools!
Step 1: The Design
With the material chosen, the next step is the mould. As the inner mold piece cannot be removed afterwards, it will need to be transparent. I chose two separable plastic balls, one with a 16 and another with an 18 centimeter diameter. While designing the mold, I had to account for the light bulb. It will need to be removable, so I won’t need to destroy the moon each time I change a light bulb. The idea is that the screw on ring for the lamp shade holder will be firmly glued to the inside of the smaller globe, and a hole is made in the plastic, at the center of the ring. This way, the moon can just be screwed on to its stand.
When securing the threaded ring, choose a strong glue; I made the mistake of applying a weak one. The problem presented itself later in the process. I poked a couple of small holes around the top ring and on the bottom center of the globe with a hot needle (heated up above a tealight). Lengths of fishing line were threaded through the holes, and knots were made on the inside. Silicone was applied to prevent any leaking later on. On the top, I marked one centimeter up and made another knot on each line. Then, I took the halves of the larger globe and made some small holes which matched the ones of the smaller globe. The fishing lines were threaded through these. As for the bottom string, I did not make any knot, as this will be done later, although that too was threaded through the large globe. The small globe’s two halves were glued together with super glue.
I test fitted everything, and suspended the globes. It looks nice!
I also made a hole of significant size, which the mixture will be poured through.
Note: the smaller globe cannot touch any of the larger globe's walls, it has to be centered on all three axes, if it's not, try adjusting or re-measuring the knots, before moving on to the next step
Step 2: Creating the Topography
Now, the hard part – making a moon isn’t just about the material – it also has to look like a moon. This can be achieved by engraving details afterwards, but a much simpler and faster method is to incorporate a negative topography into the mold. An oil based modelling clay was my choice for the task. I sandwiched the clay between two sheets of baking paper, so it wouldn't stick to anything, and then applied the thin layers to the inside. As a modelling reference, I downloaded moon data from NASA in the form of a bump map and mirrored the picture side-to-side (notice the flipped NASA logo, 6th picture). This point in time, don’t worry about the color, just the texture. I used everything from paintbrushes and skewers to things like needles and straws to sculpt the correct texture. The time it took me to make the mold was around two hours, and it was actually quite therapeutic. After the completion of the two halves, they were joined. The string on the bottom was knotted, but to be sure everything stays in place, they were taped together with aluminum tape.
Step 3: Pouring the Polyester and Concrete
For the casting of the moon, I hung the mold above a plate, in case any material would drip down. I mixed the polyester resin according to the instructions and then combined 5% concrete with 95% mixed resin by weight, as mentioned earlier. The mixture was added in several small batches, and I waited 15 minutes between each pour. The mold was lightly tapped to eliminate some bubbles, although they may add to the texture and character of the lamp. I filled up the mold all the way to the top.
Step 4: Touching Up and Painting
After 30 hours or so, I removed the tape, pulled the two globe halves apart and removed the clay, which revealed a real beauty. THE MOOOOOON! However, now is the time to worry about the finish. I removed the leftover clay with a toothbrush - no chance I will use that again! I used a rotary tool and sandpaper to remove any rough edges, especially the seam line. While I was at it, I also removed the resin above the screw-on ring, and cleaned up the rough edges with a file. Here, I was extra careful not to drill through and damage the black ring. I then covered the surface with a matte lacquer.
I was eager to find out how it looked, problem was, that my light source's color was a bit too warm for my taste. This was easily fixed with a blue marker, MacGyver style! However, there are things left to do until it's finished!
The painting was done with white and black paints, mixed in different ratios. The different shades of gray were highly diluted, to still let the light out. For the painting, I followed a color map of the moon, which is abundant on the Internet (aka picture ;D).
When the paint had dried, I hit it with the lacquer again to seal the paint.
Step 5: Epilogue
So what is the moral of this story?
Always choose a stronger glue!
Well, joking aside there were other issues with this project, than just the ring not sticking well. First and foremost, there was a problem with the mixture itself. You see, even if I mixed the concrete and polyester rigorously, the larger chunks of rock sank to the bottom, thus creating a "dark spot" on the top, when the lamp is lit.
There are however a number of solutions for the issue, from what I beleive is the best to the least good fix, respectively;
- Use a faster curing resin (this way, the concrete doesn't have time to sink)
- Or instead of mixing concrete and resin, try a fine cement instead, with no rocks inside
- Wait longer between pouring the different layers, but risk them separating later.
That said, use the strongest lamp available, so that it'll actually look like a lamp. Additionally, it's best if you use transparent/translucent paints, that way it will glow even more.
Although some problems did emerge, I still consider the project a success. Not only was the process of making the mold and painting it satisfying, the result also looks good. The color looks realistic enough, and the surface detail is a nice addition. I'm considering making a video out of this if there is any interest in that, as that would make things easier to understand!
I hope you enjoyed this Instructable! If you did, consider voting for me in the Concrete contest! :)
If you've made something similar, I would love if you could share your experience (you can DM me on Instagram, @pew.tech), and if you have any questions, please post them in the comment section, I'll try to answer quickly!
I will see you another weekend!
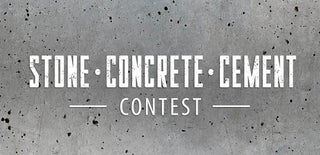
Second Prize in the
Stone Concrete and Cement Contest