Introduction: 3D Printed BW Speaker Plinth (legs)
I have a pair of Bowers Wilkins speakers and I wanted to give them some base, not to stand on the floor just by themself. The original plinths with spikes were ugly, bulky, and I did not want to use the spikes on a tile floor. Without a plinth, I am not saying it is easy to tip the speakers to their sides, but I would be more relaxed if they were more stable.
Step 1: Looking for Options
There are several options to go with universal speaker plinths, I found some nice steel pieces that I liked. The first idea was to have them waterjet or laser cut. When I asked for quotations from a few companies here, they calculated with a golden price. Then I thought I would make something out of wood, some exotic hardwood, but then I just looked at my 3D printer in the corner and eureka! Why not 3D print!?
Step 2: 3D Printing - Design and Material
My first thought was if it fits into the printing bed. I had my measurements and with just minor changes here and there I managed to design a model that fits my 3D printer and serves the purpose for the speakers. I had a very nice material at home, a fiber-reinforced nylon filament from Owens Corning and that was just perfect for this project. It is a very stiff material, beautiful in color, and looks very industrial. After the first print was completed, I tested by standing on it...did not bend. I am a lot heavier than these speakers.
Step 3: Assembling
For mounting them I used the original threaded fixing points, which required 25 mm long M6 allen screws. Inside the plinths, there is enough space around the sockets for 16 mm diameter washers. It looked great as it is, but a few days later I was thinking to add some extra spiky looking legs, printed from the same material. There are holes designed in the middle of the cone shapes my intention was to tap an M6 thread for the original spikes if I want to. In this case, I just put a 5 mm diameter aluminum rod in them where I attached the cone shape legs with a yellow color ring, just for the look.
Step 4: Bowers Wilkins on 3D Printed Legs
Overall I am very pleased with the result, they are good looking and sexy. They do not stand flat on the tile anymore, have a lot more stability and some space to breathe. It took me 4 days to print them (around 10 hours per piece), using almost 60 meters of this 2.85 mm Owens Corning filament which cost almost 100 bucks. It is not the cheapest material, but these speakers deserve the best!
Step 5: Printer Settings
If someone is interested here are my Ultimaker 3 E printer settings for this Owens Corning filament.
(I use Bondtech feeders and Ultimaker CC 0.6 ruby print core on the printer to handle abrasive materials. This printer officially does not support CC print core and abrasive filaments, but you can make it work perfectly)
Bed surface: Kapton tape
Cura print profile:
- Layer height: 0.15 mm
- Line width: 0.58 mm
- Infill: 25 %
- Printing temp: 255 °C
- Build plate temp: 60 °C
- Flow 100%
- Print speed: 40 mm/s
- Infill speed: 40 mm/s
- Travel speed: 150 mm/s
- Retract at layer change: yes
- Retraction Distance: 12 mm
- Retraction speed: 25 mm/s
- Cooling: 50%
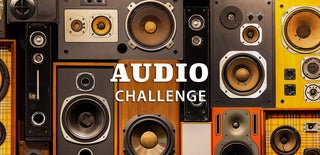
Participated in the
Audio Challenge 2020