Introduction: 3D Printed Blast Gates for Dust Collection
On several occasions, I have caught myself cleaning the dust from my workbench instead of focusing on making the project. This inspired me to build a hobbyist version of a dust collection system that helps to maintain the work-space dust free. To direct and control the flow of suction to the various machines I designed and made custom blast-gates.
Blast-gates are a clever contraption in a dust collection system to either let air flow or block it. Although one can easily make them out of wood, I chose to 3D print them because of the precision that can be achieved to reduce gaps between the moving parts. This increases the efficiency of the suction due to a better seal.
If you liked this project do drop a vote in the "Spring Cleaning Contest".
Step 1: Using Fusion 360 to Model the Parts
After having searched the web for 3d printed blast-gates and not finding simple designs to print, I decided to design my own using Autodesk Fusion 360. I made two versions that fit into my 1 1/2 inch dust collection ducting, a singular gate and a dual gate. A dual gate can be connected to any machine that requires suction in two areas. In my setup it is meant for a belt sander, that has a disc and a belt attachment. All the stl files are provided in the following step for one to be able to modify it or scale the model to their own needs.
Step 2: Materials Needed
The parts can then be 3d printed. As the blastgates itself were a 2d geometry I decided to lasercut them out of 4 mm clear acrylic, although one can 3d print them too. The parts required to make this project can be found in the following list:
Single Gate Parts
- Singular Guide Piece x 1 - 3D Printed, 30% infill
- Endstop x 4 - 3D Printed, 30% infill
- Singular Gate x 1 - Lasercut, 4mm
- M4 Bolt x 4 - 1 inch in length
Double Gate Parts
- Dual Guide Piece x 1 - 3D Printed, 30% infill
- Endstop x 4 - 3D Printed, 30% infill
- Dual Gate x 1 - Lasercut, 4mm
- M4 Bolt x 4 - 1 inch in length
For my workplace I printed out 4 Single Gates, and one Double Gate on the Creality Ender 3 printer which took around 30 hours of printing time.
Step 3: Post Processing and Light Sanding
Few of the parts are printed using supports which one can easily break with the help of a pair of cutters.The inlet and outlet holes might require a bit of sanding to remove the residue material. Finally due to slight variations in the laser cutter's tolerances I had to sand the gates a bit, before they slid into the Guide smoothly.
Step 4: Assembling the Blast Gates
Assembling the blast gates is straightforward. To make things clearer while using the blast-gates in the future I decided to assemble them all in the same way. I slid in the acrylic gate such that when the gate is pushed to the left it is 'open' and when pushed to the right it is 'closed'. To keep the gate in place secure the printed end-stops on either side with M4 bolts. Again, the orientation is important as the bolt should be screwed from the front for ease of access and removal in the future. The same process can be repeated to assemble a dual blast gate if used.
Step 5: Adding the Fittings
Now to make the blast-gate easily connectable to a machine or even to some flexible hose pipe one needs to attach some fitting to the front end. To do so cut around 8cm of the same pipe as the ducting and with a few drop of CA glue adhere it to the front end of the Guide piece. This way one has the versatility to connect any accessory they wish to the overlapping pipe.
Step 6: Mounting to the Work Surface
I have provided two mounting holes at the back of each Guide piece. Using small wood-screws, I simply mounted the devices to the wooden work surface. Now that the blast-gates are secured in position one can test if the suction works fine and if they slide around smoothly.
Important : make sure to leave at least one outlet open before powering on the vacuum, if all outlets remain close it could damage your vacuum.
Step 7: Dust Free Work Process
It has been only a week since I have been using this setup but I can already feel the convenience of having these blast-gates. Finally one can concentrate on the project while easily switching the blast-gates of various tools and machinery being used, to maintain a dust free work-space.
I hope this quick project could be useful to a few other hobbyist. Feel free to modify the design and share your experience in trying to make your very own dust collection system.
Happy Making!
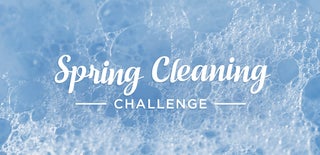
First Prize in the
Spring Cleaning Challenge