Introduction: 3D Printed CO2 Canister Rockets and Launchpad
For a long time I have been interested in getting started with model rocketry, but there seems to be a bit of a barrier to entry, with the cost of kits and rocket motors and the general danger of pyrotechnics and projectiles that fly several hundred feet in the air. So I decided to design a more compact, affordable and less dangerous way of experimenting with model rockets. I wanted to design a modular system so I could change the length of the rocket, the design of the nose cone, and the design/size of the fins. I decided to make my rocket system based off of 12g CO2 cartridges as they are cheaper, easier to replace in the field and would produce a more manageable amount of thrust for the experiments I wanted to do.
This then involved two separate builds, a safe method to puncture the CO2 canister, preferably from a distance, and a rocket system with the CO2 cartridge at its center.
Supplies
A 3D Printer
Spool of Filament
12gm Co2 Cartridges
2 9.1x34.9mm Compression Springs
1 5.6x17.5mm Compression Spring
1 2.4x14mm O Ring
(Optional) 1 2.4x20mm O Ring
1 2.6x50mm Nail
4 6x150mm Nails
Super Glue
String/ Fishing Line
Step 1: Parts
Start by printing out the attached files, some of them have a few versions depending on the design you want to create. I, like most people who are used to 3D printing avoid support material in my designs as much as possible. Therefore, all of the attached files can be printed without supports apart from the "Launch Pad Top' file. As I am still an amateur when it comes to rocket design, I don't claim to know what is most aerodynamic or how to balance center of drag and center of mass, which is part of the reason I have designed the system in this way. I have made a pointed nose cone and a slightly rounded nose cone design. There is currently only one version of the fins however, I will continue to make different fins and nose cone designs to allow mixing and matching and see which combinations work the best.
I have this set of springs, which includes both of the sizes used in this design, however you can buy the springs individually or find similar springs to use. https://www.amazon.co.uk/gp/product/B00IJYC1DI/ref...
I also own this set of O rings so have used two sizes within this set, however the same applies as the springs. https://www.amazon.co.uk/gp/product/B07ZRC4FXJ/ref...
These are the 12gm CO2 cartridges I used. https://www.amazon.co.uk/gp/product/B00345AQNY/ref...
Attachments
Step 2: Remove Support Material
The support material is fairly easy to remove as it is only on this one part. Be gentle while removing the supports to ensure you don't damage the part or the threads in the model.
Step 3: Assembling the Launch Mechanism
Start by sliding the 5.6x17.5mm spring onto the trigger part, this may require you bending the PLA of the part slightly to put the spring in place.
Compress the spring then place the trigger mechanism in the launch pad base as shown.
Once the internal components are assembled, place the launch pad top on top of the assembly and use the launch pad nuts to secure the assembly together. This will hold everything tightly in place. Be careful not to overtighten these parts as it is easy to split the layers of the threads.
Step 4: Installing the Firing Pin
In order to actually puncture the canister, place a small bit of super glue in the Launch Firing Pin piece and then slide the nail through. This may be a tight fit, so a bit of sandpaper can help, and also help to remove any excess glue that could clog the mechanism once the nail is in place.
Then, take the two larger 9.1x34.9mm springs and place them in the base. I have found one spring is not strong enough to piece the aluminium seal of the canister consistently however two works just right. then place the Launch Sled in the Launch Pad Rocket Holder then begin to thread this piece into the base, ensuring the springs slide into the hole properly.
Once these pieces have been successfully assembled, the launch pad mechanism is complete. It works by compressing the firing pin while pulling on the launch trigger. Then release the launch trigger so that it engages in the slot in the firing pin. I find that the head of a 150mm nail works great to safely compress the firing pin assembly while arming the system.This will make the launch mechanism armed, and pulling the trigger will release the spring loaded firing pin. There is a hole in the end of the launch trigger to allow a piece of string or fishing line to be attached to allow the mechanism to be triggered from a distance.
On the base part, there are three holes on the outside of the assembly that are used to securely mount the launch pad to hold it in place. I did this by placing 3 150mm nails through the holes and pressing them into the ground. However, you could also use these mounting holes to screw the piece into a sheet of plywood or other surface to keep it secured while the trigger is pulled.
Step 5: Installing the Rocket Guide
Once the launch pad is assembled, a 8mm wooden dowel can be placed in the remaining hole in the assembly. this will guide the rocket so it fires straight up as opposed to spinning out of control (hopefully).
Step 6: Installing the CO2 Canister
Once you have the rocket fins off the printer, install the smaller O ring on the base of the rocket to create a good seal on the base.
Then slide the CO2 canister into the opening of the part and if the canister is loose in the part (depending on your printer tolerances, you can place a larger O ring to secure it in place.
Step 7: Finish Assembling the Rocket
Screw the domed connector screw into the nose cone with the dome facing outwards. This domed surface will press flush against the CO2 canister and hold it in place when the nose cone and fins are screwed together.
Step 8: Your CO2 Rocket and Launch Pad Is Finished!
Now that the mechanism is finished it is time to test it.
Step 9: Blast Off!
Now i'm going to be honest, these rockets were extremely fun to make but did not fly the highest or straightest. But then again, I am still only an amateur rocket scientist.
They are a great alternative to pyrotechnic propelled rockets and the launch pad mechanism will work with any CO2 canister rocket design with the appropriate base to fit in the launch pad. I am therefore going to keep experimenting with different fin and nose cone designs, as well as playing with the weight and dimensions of the rocket as a whole.
Step 10: Design Your Own!
This kit will be a great starting point for your own amateur rocketry experiments and I will keep releasing new parts to try or you can design your own parts to use in this system.
The threads used to connect the two halves of the rockets are M22x3, you can use this to design your own fins and nose cones around my current system. I have also attached two blank files to this step. One is the fin part of the rocket without fins or connector, and the other is a model of the CO2 canister. I hope these files help you build your own unique model rockets!
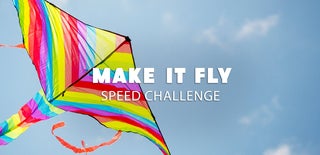
First Prize in the
Make It Fly Speed Challenge