Introduction: 3D-Printed Electric Hand Mixer
So this all started with the lock-down due to Covid-19 pandemic situation and the rise of "Dalgona Coffee". My wife got fond of the creamed coffee and i had to mix the coffee. On first day it was fun, but after that it was pain only. Recently I completed my Home made 3D-printer and I thought of making something which can help me out.
I looked in my junkyard box and found an old motor used in Cassette Players and few more supplies. Good, lets make it.!
Found a Pinion and Spur gear(I used to collect these gear from old toys) for gear reduction.Found some chrome plated shaft (3mm dia.) collected from old CD Drive.
I looked for the design on the internet but didn't find anything useful. Also, I didn't like the design of the commercially available Hand mixers. I looked for few designs ideas for inspiration and stared to make the design.
By profession I am a Hardware Design engineer working in medical domain. As a hobby I learned Fusion 360 few years back. And I thank myself that I started with Fusion 360 only and Autodesk team for making such an interactive tool that hobbyist and students can also use.
Supplies
Hardware Supplies:
1. 6V DC motor (use in cassette Players)
2. Pinion gear (8 teeth 0.05 module) and spur gear (50 teeth 0.05 module)
3. Stainless Steel shaft 3mm diameter.
4. DC barrel Jack (PN: CUI_PJ-102A ) and 12V power Adaptor.
5. 4 x 623ZZ Ball bearing or Bronze bushing 3 mm ID
6. 2 x screw(2mm dia x 10mm length)
7. 2 x M2 Screws for Motor (length 5mm)
8. 1 x push button
9. Some wires
10. 3D printer
11. PLA or PETG Filament
Caution: Using PLA filament with the Brass Nozzle leads to small amount of traces of Lead which is hazardous to health. Although it may be very minuscule amount. Therefore, a stainless steel nozzle is suggested with PETG Filament for the parts (whiskers in this design) which are used in direct contact with liquids.
Step 1: Design
The inspiration behind this is to make a design which hides the inner complexity of the product. I wanted the design to be very simple and minimalist, yet very modern and eye-catching. The key ideas on which I designed the product are
1. Compact, Minimalist and Modern
I am fond of the design which are very simple like a box or a cylinder yet very functional.Therefore I decide to use primitive shapes only for the body.
Also I need to think from the 3D-printing perspective view. Parts should be easily printable with minimum or no supports. In the whole design only the Handle needs support for printing and that is also very less (2-3 gm extra). I have experienced that it is better to split a part, print them separately and then join them using super glue rather than using the support. But i didn't want any seams or line on the Handle. So i printed it with support.
I tried many iterations with the gears and motor position to make it as compact as possible.The shafts are parallel aligned with the handle rather than forming a T- design which is present in the commercially available mixers. Due to the parallel alignment the width of gear and motor assembly reduced significantly.
Initially I designed the body with the T- design. It would look like a hammer only! No matter how much modern I make it.
I used two colors for the printing, Gray and Orange, they really go well with each other. And the result turned out to be very good I must say.
3. Screw-less snap fit design
Since i want the design to be Minimalist and futuristic, using screw holes on the body was a big no for me. Therefore i made it as a snap fit design by adding protruding and gaps on the top and bottom arch of the Handle and the joining arch. (refer images for better explanation)
In that way all the parts are in little tension holding on to each other firmly without any screw. Designing this was the most challenging part because of the tolerances. Since 3d printed items always have some 0.2 to 0.5 mm of tolerance on my printer
4. Mechanics
I designed the gears using a helical gear add-in for Fusion 360. I choose helical gears because they make low noise as compared to straight teeth gears. I didn't use the 3d printed gears for the motor as its not possible to print small pitch gears with the 0.4mm nozzle. And achieving the gear ratio of 50:8 with the bigger modulus makes the gear diameter big, which then increases the overall size of the product. So i saved some time and used what i already have.
For me the most beautiful looking part of the design is the orange button. It turned-out really well. The button is fixed with super glue on its tail. There is a small cut to avoid the contact with the excess glue as the glue has tendency to spread into the slits. Also, this provides enough flexibility for the button movement.
Step 2: Printing the 3d Models
Download the Stl. Files and print them. If you want to change anything in the design as per your need checkout the Step files.
STL Files
Attachments
Step 3: Assembling
Once all the parts are printed lets start with the assembling of the Gear Box.
1. Rub the surface on the shaft with a sand paper in the direction of the shaft. And then put the superglue using a needle on both sides of the gear to get a good hold. Do the same for the other pair.
2. Push the bearings on the motor plate and the base.
3. Assemble the motor and the Shaft-Gear pairs on the Base and Motor Plate.
4. Now, assemble the OrangeRing on the Center Plate and fix it with the Outer Case using Super Glue.
5. Fix the Orange arch on the Outer Case with the help of Super Glue.
6. Solder the wire to the motor, push button and the DC power jack as shown in the image.
7. Time to assemble the Handle. Put a drop of epoxy on the red marked area only and stick it inside the button cutout. Also insert the DC barrel jack from the inside only and fix it with glue.
8. Now paste the push button and on the tiny support and fix them inside the Handle.
9. Slide the Gear Box inside the Outer case and then insert both of them into the Handle. Apply some little force. It is a snap fit design and doesn't need screw.
Step 4: Final Result and Testing
We are using this to blend the coffee regularly past one week and had no problem so far.
Please check the small video clip for light, frothy and creamy coffee! :)
Video Link
There is a scope for more improvement in the design. The first thing is that the motor i used is not so common. So for the next version I am thinking of using a 775 DC motor which is easily available. Since this motor will be more powerful I can use a lower gear ratio for reduction. Which allows for all 3D printed gears in the design.
But 775-DC motor is bigger in size. so I have to find some clever design to fit the motor in the same body size.
Thank you for reading! Wish you all the best for your own 3D Printed Mini Hand Mixer.
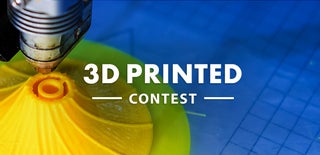
Runner Up in the
3D Printed Contest