Introduction: 3D Printed LED Plexiglass Sign (Color Changing)
For a Christmas gift, I decided to make someone a 3D printed LED sign that uses interchangeable plexiglass pieces for different effects. I want to share this awesome project with you guys and I hope you will learn something from it to include in other projects.
Most of the materials could be salvaged from spare parts such as the switch, button, LEDs, and wires. But for those who want to purchase new, I have the links down in the supplies. If you don't have a 3D printer, this can still be made from wood, cardboard, or any other sturdy material.
If you want a rundown of the project, feel free to watch the video. Otherwise, let's get right into it :)
Supplies
Step 1: Print the Materials
Understanding the materials:
To start off, we have the 3D printed parts starting with the motherboard enclosure. This holds the programmable ATTiny85 and any extra wires. At the back, there are two holes for the positive and negative wires coming from the batteries to power the components. The next gap near the front will allow the three wires from the ATTiny to power and control the LED’s that will sit on top of the enclosure.
Next, we have the battery pack. There is a switch at the front that allows around 2 amp of current to flow through to give the components 4.5 volts to operate. The batteries are in series to boost the voltage from a standard 1.5v double A battery to 4.5v. There are two holes exiting the enclosure for the positive and the negative wires. There are four screw holes that allow a lid to screwed on flush with the battery pack to secure the batteries.
Now we have a plate that sits on top of the battery pack and the wired base. AS well as helping secure the glued parts together, this thin piece also acts as a guide and center the 12 WS2812B LEDs in the middle for the plexiglass to sit on.
Finally, the top of the project holds the Plexiglass in place directly in the middle of the LED strip for maximum brightness. It also has a hole for the button to change the color.
Step 2: Upload Sketch to ATTiny85
The code cycles through 7 solid colors as well as 6 different animations. Feel free to add your own colors or animations, but be careful on the memory limitations the ATTiny85 has. This project may also be able to fit an arduino nano as well. The cargo space which carries the ATTiny85 can be expanded.
I will also link a video on how to upload to the ATTiny85, since it can be a long process.
Here is the youtube link to upload to an ATTiny
https://www.youtube.com/watch?v=i9WOwDrpRKs&list=PLdiX14C9BpYT0S-i7akw6hZH-6iOqR3xc
Attachments
Step 3: Solder, Glue, and Test
Soldering the wires took a while because of pre tinning each component, stripping all of the wires, and fitting the wires between the small gaps. Makes sure to have proper ventilation and not breathe in the fumes. I had a fan blowing so the fumes would dissipate. Having two pairs of metal helping hands helped improve the solder joints instead of my shaky hands holding them.
In the battery pack, I glued the metal plates to the enclosure using hot glue. Throughout the project, I also hot glued wires and solder joints down to secure them.
I had to solder the ATTiny85 according to this layout. The ground wire was soldered on the left of the ATTiny on pin 4. From pin 4, there were two other wires. One went to the ground of the LED strip and the other went to one side of the momentary push button. Then from the other side of the push button, a wire went to pin 5 which is the bottom right side. Pin 6 was used to control the LED signal and the top-right pin had 5v to power the controller as well as a wire leading to the LEDs again to power the strip.
The button was used as an input pullup in the code so it can receive and pass through a ground signal when pressed.
I make sure to test my components after each step when they receive the power and ground wire. This helps figure out what may have caused a problem if one occurs and I can easily backtrack.
When gluing the 3D printed parts together, I used a glue called e6000 which drys pretty fast and I have had great luck using this glue for other projects. I used many different types of clamps to guarantee a strong bond between the parts. It’s important to not clamp the project too hard or that the pieces don’t move out of place. When I had the clamps set up, I made sure the project was still running.
Step 4: Etch the Plexiglass
Now for my favorite part, carving the plexiglass. I photoshopped an image then printed the image out. I wanted to make sure the picture was a good size for the frame and that the image was proportional to the plexiglass I cut out. Afterward, I taped the image on the back to sketch out.
When carving out the picture, the best tool to use is a Dremmle or any small rotary tool. For the tip, I used a small, thin tip to follow the precise lines. It was hard to follow the lines in general so I improvised and did the best as I could. This happens because of the thickness of the plexiglass being a distance away from the actual picture. Depending on the rotation of the tip, the tip is hard to control and skips around the glass. I found that going with the rotation of the device is the best way to avoid slipping.
In the middle of the flower, I shaded the middle and dug holes to represent the flower seeds of the anemone flower. I like to add different styles of shading because it shows up differently under the light and adds more of a 3D effect. For shading, I used a larger diameter tip to cover a larger area. I also used this larger tip when creating and shading letters and creating the stems.
This can be a tedious process and could quite some time depending on the picture detail. I placed down an LED lamp which allowed me to see the project much better and to follow the lines more accurately. This project is universal, The Plexiglass can easily be swapped out so you can create multiple sketches with different pieces of plexiglass for the one 3D printed stand.
Step 5: Add Plexiglass to Project and Enjoy!
I hope you enjoyed this project! Let me know if you created this project or what your thoughts were on this project. Also if you have any comments, questions, or other ideas, let me know in the comments below. Thank you for your time and I hope you learned valuable key points you can implement in this project and many others.
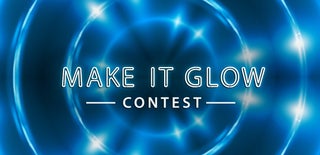
Participated in the
Make it Glow Contest