Introduction: 3D Printed Mini Looms
Last August we did an agriculture themed week at my school. For my part, I taught the kids about fiber. One day we learned about sheep and different types of wool (I brought in samples of each type, including goat, vicuna, camel, angora rabbit, alpaca, and llama), the next we did wet felting, then we learned about yarn production and made quick spindles for spinning yarn. My thought was that the yarn the students spun could then be used for weaving---showing them all these different stages of fiber/fiber arts/production. Once I was set on this line of thinking, I needed 25-30 looms. I wanted each student to have their own, as well as a few for staff/demonstrations, and a couple backups in case one broke.
Supplies
3D Printer
Filament
Tapestry needles
Weaving materials (string, yarn, thread, embroidery thread, wool, wool locks etc.)
Tape
Fork (for pushing the rows of weaving together)
Step 1: Work Smarter, Not Harder
When I started this project I was originally making cardboard looms. I can't draw or cut a straight line to save my life so I was having the hardest time getting what should have been super simple cardboard looms made. After a couple I gave up and decided to look for a mini loom STL file (a 3D printable file).
Aside from the circular loom, I couldn't find any files that I liked or that fit my needs so I decided to make my own. That's where TinkerCAD came in.
Step 2: TinkerCAD Part 1
I started the loom with a plain box shape that I enlarged and flattened. I didn't worry too much about the size because I can always adjust it in Slic3r before printing.
I was concerned about the measurements being even, so I made sure that all sides of the box were placed evenly on the grid. Once satisfied with the size, I flatted the design so that the loom will print thin but not easily breakable and not super bulky.
I added a second box (in a different color to be easier to work with) to the work space and made it the same thickness as the loom and adjusted it into a thinner rectangle. It's about 1/2 the size of one of the work plane grids. The rectangle is what I used to add the notches to the loom (pic 4). I found it easiest to add additional notches off to the side of the main loom, just to get everything measured correctly. I cut and pasted my first notch until I had the number I was looking for and then selected all to move all the notches together (pic 5). I copied and pasted the notches from the top onto the bottom and lined them up to be even (pic 6).
Once satisfied, I grouped the original square and the notches together so that the notches would be "cut" from the box (pic 7).
Step 3: TinkerCAD Part 2
The next thing I did was add another box to the work plane to cut out the center of the loom. I had to move the view around a few times to make sure the new box was lining up with grids. When I was happy with the placement I made the green box transparent and then grouped it with the red box to cut the center out. With that, my first loom design was complete.
I made several versions (pic 4) of this loom to account for the different needs of our students. Some of the students are elementary age, so I made them slightly bigger looms with wider notches or I only left 5-6 notches. Other students I added more notches to make the loom more complex. I wanted to make sure this activity was accessible to all of our students, and it was :)
Attached is the STL file for the square loom.
Attachments
Step 4: Print
I made several size variations of the looms and tested different infills, most ranging from 10-20% infill. The infill adjustments didn't save a whole of time as all the different looms took anywhere from 25-45 minutes.
I used PLA to print all of the looms. Some of the PLA worked better than others.
Step 5: Warping the Loom
When you add the string that wraps around the notches of your loom, it's called "warp". These strings go up and down around the notches. Students either tied and taped or just taped their string ends to the loom when they warped it.
Step 6: Weaving
To weave, we used store-bought plastic tapestry needles and the kids could either use yarn, embroidery thread, string, or wool/wool locks to weave with.
Thread the needle and starting at one side, go up and over (or go under, I don't think it actually matters) the first thread and then under the next (pic 1). Repeat this pattern all the way across the loom.
When you reach the end (we had the kids tape the end to the loom) you want to "turn around" and go back across the loom, in the opposite way that you went across the first row. So if you did over/under, you're going to do under/over. You'll know if you're doing the wrong pattern if your weaving yarn lines up straight next to the previous row (pic 2).
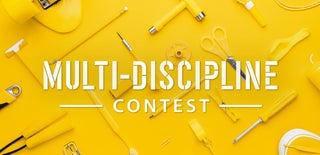
Participated in the
Multi-Discipline Contest