Introduction: 3D Printed Miniature Engine (Bottom End)
Today we'll look at a quick Instructable on how to print and assemble your very own miniature single cylinder engine. This model bottom end is easy to print and assemble, taking about 3 hours to build from start to finish, and makes an awesome desktop ornament, educational tool, or even just an interesting knick knack. But enough about that, let's get started!
Step 1: Tools and Materials
Here's what we'll need to start building our model engine:
- 3D Printer
- Filament (I used Hatchbox 1.75mm PLA)
- 22-24 AWG Solid Strand Wire
- Hot Glue or Super Glue
- Steel Files or Sandpaper (Files Preferable)
I'll be using a MakerFarm Pegasus 8" printer. For those looking at buying a 3D printer, I have been quite happy with this model and it was one of the cheapest I could find with that size build platform. Steel files will be useful to clean up your print as some of the tolerances are rather tight in order to keep up the quality of the engine.
Step 2: Part Files
Each part was printed with a .2mm layer height, 15% infill, 2 perimeters, pillar supports, and original speed settings using Slic3r and Repetier. However, I found the cylinder benefits from having a raft due to the cooling fins trying to lift during the first 20 or so layers. All in all you'll need about 22 grams of PLA to print out the whole assembly.
Step 3: Assembly
With the parts printed, the first step will be to check for any imperfections, primarily in the bore of the cylinder, the outer face of the piston, and any of the other concentric features as any errors will prevent the engine from turning over smoothly. A set of hobby files works best here, you can pick up a cheap set from Lowe's or Home Depot. However, sandpaper or an Xacto knife will also work. The supports and raft will need to removed from the male half of the connecting rod and the cylinder. Both should be easy to remove by hand, although if they put up a fight an Xacto knife or any other sharp knife will do the job.
Next, we'll start assembling the crankshaft and connecting rod. The connecting rod should be snug on the male half of the connecting rod, but should still be able to rotate freely. From here we need to fasten the two halves of the crankshaft together. I've tried using adhesives with little luck, so try it at your own discretion. The best way I found to connect the two is to take some 22 or 24 AWG wire (I got mine from CAT 3 telephone cable), feed it through the two halves and leave enough at each end to curl into a hook to keep the wire from coming out of either end. Adding a small drop of glue to each end will give the connection better security. If so inclined, you may also apply glue to the inner faces of the crankshaft halves before adding the wire, although I have not seen a need for it thus far.
Once the two halves of the crankshaft are secured with the connecting rod attached, next we can insert the crankshaft into the body of the engine. The crankshaft should go in with the male end going through the hole in the rear of the body. Again, there should be little to no slop between the shaft and the bore of the hole. Once the crankshaft is in we can secure the flywheel to shaft protruding from the rear of the engine. This will be done using a few drops of glue applied to the shaft before sliding the flywheel onto the shaft.
Cut another length of wire the diameter of the piston. This will be used to connect the piston to the connecting rod. However, before trying to insert the wire through the two, I recommend trying the wire in the connecting rod and piston individually first. This will open up the holes in both components and make the job of inserting the wire through both much easier. If the holes are too small you may need to find a needle or similar tool to open up the holes slightly. Once you've connected the two using the wire, a small drop of glue can be added to prevent the wire from backing out of the hole.
Finally, the front cover will simply slide over the exposed end of the crankshaft and will sit in the recesses on the front of the engine. Use your glue of choice in the recesses to secure the front cover and wipe away any excess once complete.
Step 4: Finished!
Be sure to turn the engine over using the flywheel in the rear. If there is excessive resistance, check for any burrs in the cylinder bore or piston, as well as the rotating components. If the tolerances are a bit tight use some lightweight oil help the components move a little more freely.
Your engine is now complete! Display it proudly on your desk at school or work, or play with it while you're suppose to be studying or working....
Thank you for viewing my Instructable! If you liked this, please check out my others as well as my YouTube channel and Etsy page for more projects. Interested in this project but don't want to build it yourself or don't have the access to right tools? Click here to purchase your very own miniature engine!
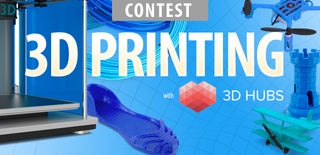
Participated in the
3D Printing Contest 2016