Introduction: 3D Printed Moulds for Slab Built Ceramic Art!
The realm of creating complex shapes in clay has historically been dominated by slip casting (shapes created by pouring liquid clay into plaster moulds and pouring out the excess to leave behind a clay shell), and this well established method has been thoroughly explored by other artists to include all means of exciting additions (like 3D printing and CNC machining), but watch out! There's a new player in town now and their name is 3D Printed Slab Moulds!
Slab building is a technique that's positively ancient as it involves little more than taking flattened slabs of clay and attaching them to one another by scratching up the surface of the clay and using some of the afore mentioned slip to glue the pieces together. Typically one is restrained by the laws of physics and gravity when it comes to making forms, but technology steps in to make new things possible!
I have spent many months developing, testing, iterating and perfecting this technique to be able to quickly design, create, and recreate awesome clay art WITHOUT the need for plaster or liquid clay. Check out the video for a fun explanation of the technique, or read on to learn how you can make your own!
Supplies
This Instructable assumes at least a basic understanding of 3D design software, 3D printing, and working with clay.
3D Printing Tools & Supplies:
- CAD software of your choice (I use Fusion 360 in this tutorial, but you can use anything you're comfortable in)
- FDM 3D Printer
- 3D Printing filament of your choice
Ceramics Tools and Supplies:
- Clay body of your choice (stoneware recommended, but any will work)
- Cornflower/Corn starch
- Rolling pin and guide rails, or slab roller
- Clay knife
- Scoring tool
- Smoothing sponge
- Soft silicone rib (optional but useful!)
- Clay slip & brush
- Plastic wrapping to cover clay
- Hair dryer or heat gun
- Kiln to fire the clay in
- Glaze for finishing
This technique absolutely SHOULD also work with other materials like air drying clay, polymer clay, or even fondant! However, I have not personally tested the technique with these materials, so adjustments may be necessary to make it work. Experimentation is encouraged though, and please do share your results if you do!
Step 1: Planning Your Design
When it comes to designing a mould for slab pressing, there are some important aspects to keep in mind that will make or break whether or not you're able to pull off the final piece in clay! Some of these things are common among all mould based techniques, and others are specific to creating a form for slab pressed clay pieces. I will try and cover some of the most important things, but encourage looking into more in depth mould making resources if this is your first time ever making a mould!
Undercuts
As displayed in the image above, undercuts are parts of your final clay piece that prevent the mould from being able to pull away cleanly, resulting in damage when you try to remove it. The above mould design would not work as the top of the clay vase would break off when demoulding. Fortunately, undercuts can often be designed around by choosing smart seam placement at high points in the design, and creating the mould in such a way to move away from the highest points in the design, like below.
Other ways to avoid this issue is to use designs with little to no undercuts, that can use a single part mould.
Slab Placement
Often moulds only require a small hole or opening for the material to enter (slip casting and injection moulding both work this way) but with slab press moulds you need to be able to get your hands fully inside the mould to place the slabs! This can be accomplished either with a wide mouth mould design, or a multi part mould that you can press slabs into one piece at a time before assembling.
Demoulding
Unlike slip casting or other techniques that use plaster moulds, 3D printed plastic does not absorb water from the clay, ultimately speeding up the drying process. Because of that, air being able to reach the clay is essential for this technique to work. Even so, the clay is likely to be a bit softer when it's time to demould than it would be with a plaster mould, and being able to do so without damaging the clay is worth taking into consideration when making the design.
Like with the other considerations, breaking a mould design into more pieces can often alleviate this concern.
There's obviously a lot more to mould making than this, and if you are completely new to mould making then I highly recommend reading up a bit more about mould making and mould design basics!
Step 2: Designing Your Mould
Something like this absolutely can be approached in a myriad of ways and using a huge range of software. There's no one way to approach it! Feel free to experiment and find what works best for you. I will walk you through how I approach it though, and you can tailor it as you see fit!
I like to start by creating the 'positive' in my CAD software, to give me a good idea of what the final piece will look like. Being able to visualise it right at the very beginning is extremely useful throughout the process for reference, but also makes creating the moulds a bit easier as you have something to design around.
To create the Hex Cup mould I created three sets of sketches that followed the curve of the edges and lofted the body between them, allowing me to line up the mould seams with the edges of the cup.
I cut away at the outer edge of the mould to create flat faces that would make it easier to rest the form on it's back whilst placing the clay inside it. In this instance, I simply doubled the number of sides on the cup and used that number to dictate how many facets would be on the outer edge. I found this one addition greatly improved the user experience!
I used cylindrical primitives with a filleted edge to create keys, or alignment points, for the mould. Each side is identical and fits into the other, so there's no real order to the sides for this design. Make sure to remember to add in tolerance gaps between the pieces so they fit together nicely!
I created cutter shapes for both the bottom of the cup and the side pieces that would (hopefully) fit perfectly with each individual side of the mould. Getting the side cutter piece just right took a bit of experimentation as you are effectively flattening a three dimensional shape, which is easier said than done! For something like this, it's a bit better to overshoot (go bigger) than undershoot, as you can always trim away the excess. The slightly lower centre rib in the side cutter was to create a score line along the middle of the clay to make bending it easier, as seen below.
The steps for the Wavy Vase were similar, but with some adjustments made to make the mould seams fit the shape. I still applied the same faceting to the outer edge (but with 8 sides instead of 12) and created a cutter to create the base for the vase. I only created keys along the top instead of the top and bottom as I wanted a looser fit.
Once you've designed all the pieces you need, it's time to print!
Step 3: Printing Your Mould Pieces
This is probably the easiest step of the process, as there isn't really a right or wrong way do it! Clay is extremely forgiving in this regard, and you can get away with not having the best or cleanest print by simply cleaning up bodges in the clay later.
That said, I find that a balance between fast and clean is ideal. I tend to use a 0.6mm nozzle and 0.3mm layers, with as little infill as I can reasonably get away with. This makes the prints fast and light, using less material. You can do smaller layers to make clean up easier, but I found little difference between 0.2mm and 0.3mm layers.
You can use pretty much any material you feel comfortable printing in. I use PLA in a colour that makes it easy to see material build up on the plastic (so not a white or grey), but again, this doesn't really affect the final quality of the clay piece, so feel free to use what you have to hand.
Make sure to scale up your print by 10-15%, depending on your clay body, to accommodate for shrinkage!!
Your final clay firing with shrink your piece down by an amount dictated by the clay you use (find your clay's data sheet to learn the exact amount), so you need to scale up your mould before you print it or you'll have a much smaller ceramic piece at the end!
Step 4: Preparing Your Clay
It's finally time to bust out the clay! Most clays should work with this method, including air drying clays, polymer clays, even edible things like fondant or modelling chocolate! That said, I have only personally used two different clays with it, Draycott White Stoneware and Audrey Blackman Porcelain. If you're less familiar with ceramics and working with kiln fired clay, I recommend using a stoneware as they tend to be the most forgiving.
I will, of course, be running through this tutorial using kiln fired clay, so the steps may be slightly different if using something else. Adjust as needed!
Once you've got your clay out, cut off a reasonably sized piece to wedge up. If you've never wedged clay before, I recommend looking up some how to videos on YouTube, as there are multiple methods for it, and your mileage may vary! Regardless of how you wedge, it's important to do it thoroughly as it removes the air bubbles from the clay and helps to make it homogenous.
Once your clay is wedged up, it's time to make some slabs! This can either be done with a rolling pin and some guide rails (can literally be two pieces of wood, long as they are the same height to ensure consistent thickness) or with a slab roller if you have access to one. The slab roller makes an easy job of it, but rolling pin works just fine!
As far as slab thickness goes, this is somewhat dependant on the piece you're making and personal taste. I find somewhere between 1cm and 0.5cm to be a good thickness for most things, but feel free to go thicker if the piece is larger or you feel safer with more clay to work with.
Step 5: Preparing the Moulds
Before you can put clay in your 3D printed moulds, you need to prepare them with a release agent, lest you find yourself with a hard to remove mess later! Just to be extra clear:
This step is not optional! Please do not skip it!
Cornflower or corn starch (same thing, different name) is ideal for this as it is generally harmless to ingest, wipes off well and burns off cleanly in the kiln. You can use talc, but as talc can be harmful to inhale, it recommend against it (unless you are masking up for the process). Either way, I recommend doing this part outside or over a sink!
Generously apply the cornflower to the inner surfaces of the mould and rub it around until the entire surface is thoroughly coated without gobs of excess. It can help to give it a tap to knock extra powder off. You want a good coating to prevent the clay from sticking too much, and some will get knocked or brushed off before you finish, so I found it helpful to be a bit extra here! Apply to all sides of the mould.
Step 6: Laying Your Slabs
Once you've got your powdered moulds and rolled out slabs, it's time to get laying! If you created cutters for the sides, then now is the time to get them out and start cutting out pieces. Otherwise, grab your clay knife and freehand cut your pieces one at a time.
Drape your piece gently inside your mould, making sure it's large enough to cover the complete surface area of the piece before pressing it more firmly in place. Be careful not to press too hard and thin the clay out unevenly in places, only press hard enough to make sure it's seated fully against the form. (Side note: for the Wavy Vase I pre-assembled the pieces into halves as I found this faster and easier for me, but approach how you feel most comfortable)
Once the clay is secure and flush with the mould, take your clay knife and run it along the edges of the mould, trimming off the excess clay from the sides, top, and bottom. Don't worry about this being too clean, you will end out doing it a couple more times to get rid of uneven bits before you're done!
After the edges are trimmed, it's time to go in and smooth down your slabs and make sure they're fully pressed into any nooks and crannies in your design. If your form is smooth, this can be done easily with your silicone rib in steady, even movements. You want to avoid putting too much pressure in one place if you can, but if you accidentally press too hard in one place, you can always press the excess clay back into the thinner spot.
If dealing with a more complex mould like the Wavy Vase, you will need to be extra careful to not make any spots too thin. If in the process of pressing the clay into the grooves you find spots getting a bit too thin, take a bit of extra clay and press it into the thinner spots until it fills back out.
It's worth taking your time with this step if your mould is extra complicated, as you can't really make it up later after the clay has hardened!
Trim up your sides once more if they need it. It's time to attach them to each other!
Step 7: Assembling the Mould Pieces
Once all of your mould sides are prepared with slabs, it's time to assemble the pieces into one solid piece. This is where the ceramics technique known as 'slipping and scoring' comes in. In spite of the commonly used name, the scoring bit actually comes before the slip bit!
To prepare for this part you'll need to prepare a small brush (I find one with rough bristles works best here) and your slip. I keep some excess slip from throwing on the wheel in a jar for times like this, but you can always make some by adding some clay and water to a jar and mixing them up until you get a thick sludge like consistency. Lumps are fine in your slip, long as it's loose enough to be brushed on!
You'll start by taking your scoring tool (this can be a dedicated scoring tool, your clay knife, a fork, or even a needle tool; it just needs to be able to leave fine scratches) and creating a criss-cross pattern over the edge of the clay that's going meet the other side. Feel free to be messy with this; you're just creating more surface area for the slip to cling to when you apply it. Score all of your edges before applying slip.
Lay your pieces out for easy access because once you start applying slip, you'll want to work a bit quickly to prevent the slip from drying before you can press the sides together. Liberally dab slip onto the scored edges (it's okay to be a bit messy, it's better to over than under apply!) and press the mould and clay pieces together.
Smooth and reinforce your joins with your finger or a smoothing tool (this can be a bit of wood or a silicone sculpting tool). If the join looks a bit thin or weak, you can add a bit of extra slip to fill in gaps, or roll out a thin coil of clay to press in the join. You can use your silicone rib at this point to smooth and clean up the interior and edges.
If your mould needs a bit of help staying together, you can use ratchet straps or giant rubber bands to hold the mould together! Depending on how tight the tolerance were in your 3D print this might not be necessary, but there's nothing wrong with a little bit of extra hold if it needs it!
Once your moulds are secure, put them somewhere dry and warm for a while for the clay to firm up.
Step 8: Preparing Your Base/Handles
Before you can go off and do something else while your clay hardens, you'll need to prepare the base for your piece, along with any handles or other pieces you want to add on at the end. Use any slabs remaining to cut out your base, as well as any handle pieces you may need. If making a handle, form it into the shape you plan to use. Cover them with plastic wrapping loosely to keep them from drying out too much and set these aside for later.
Step 9: Take a Break!
It's time to step away for a while and let your clay harden and dry a bit before you attempt to demould it. If you're able to put it somewhere really dry and warm it'll go faster, but feel free to forget about it for an hour or two at least. Which, if you are like me, can be a bit frustrating! Go do something else for a bit, you'll thank me.
Step 10: Demoulding Your Piece
After an hour or so, check on your clay in the mould! Gently touch the edges and the inside where you can to see how hard the clay is. If the clay is pulling away from the walls and feels quite firm to the touch, it's time to get demoulding! If it's still quite soft and sticky, or still seems to be holding fast to the walls of the mould, it's not quite ready to come out yet. If the edges seem like they're doing pretty well but the inside is still too soft, then now is a good time to pull out a hair dryer or heat gun.
Aiming your hot tool of choice toward the inside of the piece, gently warm up the interior while being careful to not concentrate the heat too long in one place. If using an actual heat gun, be sure to keep the temperature on the lower side so as to not over dry the clay, which can lead to cracking. Keep checking the clay with your fingers every so often and keep at it until things have firmed up a bit more.
Once everything is feeling pretty firm without being too hard or dry, it's time to take that mould apart and reveal the sweet inner clay shell! Gripping the rest of the mould firmly, gently work away a single piece of the mould at a time until it pulls away cleanly. If it's not coming away at all, then you need to let it dry some more. Keep an eye out for cracks in the clay while you're pulling! Keep at it until the clay is completely free.
Give your piece a once over after it's free! This part is optional, but highly recommended. Look at how cool this thing you made is! You should be proud.
Step 11: Attaching the Base (and Handles)
Before you call it a day and let your piece dry out for firing, there's still a bit more to go while the clay is still workable. It's time to add the base and handles!
Just like with attaching your individual mould pieces, you'll use the same slip and scoring technique to apply the base. Your base piece should be a bit softer than the clay in the main body of your piece, but not drastically different, or you may encounter cracking when it dries out. If the main body is significantly harder, spritz your piece down with a little bit of water (not too much!), or if the base is way too soft, leave it to harden a bit. You want the individual pieces to be somewhat close in firmness.
As with the inner joins of the main body, if you can access the inner join of the base, it's a good idea to reinforce and smooth it out. I like to go in with a brush and some smooth slip and paint it into the joins before using my finger or a silicone sculpting tool to smooth it.
Attaching handles works more or less the same way, with the main difference being that you may need to trim back a bit of the handle to make it sit flush with the side of your piece. Otherwise though, it's the same slipping and scoring, with a bit more of extra smoothing and clean up of it's edges to blend it into the main body of clay.
Once your base is secure, the edges can be trimmed down and smoothed out to make the bottom blend seamlessly into the main body. I use my clay knife to cut off the excess, and a combination of my finger and a sponge to smooth and blend the seam.
Step 12: Final Clean Up and Smoothing
Now, you might be wondering, what about those layer lines??
Rest assured, you're about to show those layer lines who's boss.
Now is the time to take your fine pore sponge (I like my white Mudtools sponge for this), a bit of water, and go to work on those seams and layer lines. Take the wet sponge and apply it with a bit of gentle pressure to the surface of the clay and make little circles until the layer lines start to vanish and the outer layer of the clay gets wet and a bit soft again. Once the lines start to disappear, you can sponge down along the body lines of the piece, making the clay uniform once more. Stubborn spots and more pronounced seams may require a little more elbow grease, but it shouldn't take a great deal of time and effort to remove most of the layer lines and imperfections.
If you want to get the surface even more smooth, you can use your soft silicone rib here and drag it over the surface of the clay, burnishing it slightly. This can also help bury any stray bits of grog that can surface in rougher clay bodies and leave you with a really smooth and shiny piece.
Now is also the time to put any finishing touches on your piece. For things like cups, mugs, or bowls, I like to burnish the rim with my silicone rib and give it a final smoothing with my fingers to make sure it's not too sharp or unpleasant to eat and drink from. Handles should have a similar treatment applied to make them nice to hold and not sharp against the skin.
If you have a maker's mark, make sure you add it to the bottom of your piece now! It's complete!
Step 13: Firing and Finishing Your Clay Creation
Congratulations! You have successfully turned a digital design idea into a physical clay creation!
This is technically the end of the tutorial, though not exactly the end of the process. If you created a piece in kiln fired clay, then this is the point where you let it dry completely before bisque firing it, and then glaze it prior to it's final firing. If this is your first time glazing a piece, I recommend looking up other tutorials or guides on that part, because unfortunately I don't cover it in detail here! The good news though, is that if you find you weren't able to completely eliminate layer lines or surface flaws, many of them will vanish under the surface of the fired glaze when it turns into something skin to smooth glass.
From here, the sky's the limit! Not everything is guaranteed to work with this technique, but there is MUCH to be explored around what can be created with it that would be challenging to impossible to make by hand, or even just what can be made simpler and more accessible.
If you're made it all the way to the end, you're a champ! Please do share any pieces you make as well as any new experiences had in the process! If you want to learn more about the projects created during my recent art grant study, you can read all about it here on my website, as well as finding links to my social media and 3D printing models. Lastly if you aren't already, please consider subscribing to my YouTube channel to stay up to date with my latest projects and experiments.
Thank you again for coming on this adventure with me!
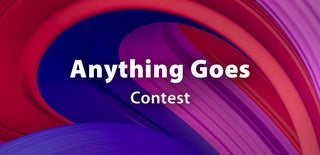
Grand Prize in the
Anything Goes Contest