Introduction: 3D Printed RC Tank
Hey guys! I am a senior at Mount Mansfield Union High School.
The urge to drive an RC Tank was strong with me one day, but because the ones online don't seem very capable, I made one myself using a 3D printer and Fusion360, and decided to share the process with you.
In this Instructables guide I will show you the resources and materials needed to build the tank, the process for building the tank itself, and the code used to control it.
P.S - The video below is a video of the tank driving through the frame
Attachments
Supplies
Tools:
- 2.5mm Allen Wrench
- 3D printer with 188mm in one direction
- Drill (With 2.5mm and 1mm bits)
- Metal File
- Craft Knife
- Lighter
- Soldering Iron with Solder
- Hot Glue Gun with Hot Glue
- Hacksaw
Materials:
- 2Kg PLA
- 40mm x 66cm Rubber Tracks - Here
- M3 Hex Socket Head Screws with Nuts - I bought this kit
- Deans T-Plug Connectors - Here
- Extruded Aluminum Shaft: 5mm x 250mm
- Male to Male, Female to Male, Female to Female Jumper Wires
- Velcro Strip (Optional)
- Heat Shrink (Optional)
- 5mm Toggle Switch - Like this
Components:
- (2) 12v Geared Motors - I used these
- (2) Brushed Esc - I used these
- Rc Reciever and Transmitter - I used this
- (12) 5mm inner x 8mm outer ball bearings - I used these
- (2) 8mm inner x 22mm outer skate style ball bearings - Like these
- 3s Li-Po battery - Like this - You will also need to buy a safe charging regulator for Li-Po batteries
- Arduino - I used this Nano
Step 1: 3D Printing the Tank Frame
The first step to creating this 3D printed tank is to print the pieces! I kept the ease of assembly and printability of these parts in mind as I designed them, so they are easy to both print and put together!
Here is a link to a google drive folder which holds the 3MF files for the tank, and here is a link to another folder which has the slices of these files I made for my Creality CR-10 v2 with a .8mm nozzle on it.
Here is a list of which parts you will need to print, and how many of them to print:
- (1) Chassis
- (2) Track Frame Motor Side
- (2) Track Frame Bearing Side
Remember that some parts will need to be mirrored in your slicer of choice. There will need to be a right and left version of each track frame component, so for example, one track frame component will be sliced as is, and another will have to be mirrored so that they will fit on opposite sides of the chassis.
- (4) Track Frame Spacer
- (6) Free Spin Wheel
- (2) Drive Wheel - You may want to print an extra because the support material is hard to get off the part
- (12) Basic Axle Cap
- (1) Battery Holder
- (1) Esc Switch
- (1) Motor Joiner
- (1) Switch Stand - Make sure to print with long edge on bed so that support is not required
- (4) Axle Holders
Now you're ready to start building!
Step 2: Attaching the Inside Track Frame to Chassis
The Track Frame is the 3D printed "Sub-Chassis" which will hold the motor, guide wheels, drive wheel, track, and bearings. This is essentially the area which powers the tracks, and ensure that they maintain a straight drive line.
My first step was to Hot Glue some Velcro to the bottom of the main Chassis so that it would be easier to organize and secure components to the tank. I expected to to get a little shaky in operation, and the Velcro was a "cushioned" way to secure those components.
The next step is to locate the inside track frame parts. These are differentiable to the outside track frame components because they have a smaller hole in them at the larger end, which is where the motor will be housed. The rear of the chassis is the area where there are through holes in the bottom of the chassis, and the larger end of the inside track frame is in front.
The inner track frames can be attached to the chassis with three M3 bolts and nuts per side. They should be tightened so that the outside of the main chassis and outside of the inner track frame are firmly held together. You can do this for both sides of the chassis.
Step 3: Attaching the Motor and Drive Wheel
In this step we will install the motors into the motor side of the Track Frame and mount the drive wheels on their shafts.
The shafts of the motors fit into the shafts of the inside track frame component, and they can be screwed into the track frame with screws. My screws were included with the motors. To improve the rigidity of the chassis the motor joiner can also be placed between the motors, and the wires routed through the slots in the joiner. If this is confusing, the pictures above show what the completion of this step should look like.
When wiring the motors, I soldered wires to the terminals, and also heated heat shrink over the exposed metal so that the motors wouldn't short against each other. I also added some bullet connectors to the motors for easy removal in the future, but that would be an optional step.
To fit the drive wheels onto the motor shaft, align the flat edge of the drive wheel to the flattened section of the shaft, and slide the drive wheel onto the motor shaft. This may require some effort depending on the dimensional accuracy of your printer, so a lighter may help to heat up the motor shaft so that the drive wheel slides onto it easier.
Step 4: Attaching the Bearing Side Track Frame
Here we will attach the other Track Frame part using the track frame spacer.
First we must insert the 8mm x 22mm bearing into the hole of the outside Track Frame. This bearing is not load bearing, but it helps to align the drive wheel, and will ensure a straight track line.
Fit the printed track spacers first onto the two square extrusions from the inner track frame side. Again, these parts may require some effort to fit depending on the accuracy of your printer, so it is okay to sand or shave away at the sides a bit to get them to fit snugly.
Then you can fit the identical square extrusions on the outside track frame into the track spacers on the open end, while also inserting the extension of the drive wheel into the bearing.
(Optional) - You can insert some extruded aluminum rod into the holes which go through both track frames and underneath the chassis to improve the rigidity of the tank. You can trim the aluminum rod so that ~7mm extend beyond each side, and clip them into place with 4 axle holders.
Step 5: Securing the Free Spin Guide Wheels
In this step we will install the free wheels into the Track Frame.
The first step is to cut 6 sections of 45mm aluminum extrusion. I did this with a hacksaw, and then filed down the sharp edges with a file. Then you will have to drill a hole on the ends of the aluminum shaft, facing inwards, for ~6mm with a 1mm pilot drill bit. These drill bits are extremely fragile, so you should use some lubricant like WD-40 to cool down your bit when you are drilling.
After the holes are drilled with the 1mm bit, they need to be enlarged by using a ~2.7mm drill bit. These holes are going to be threaded directly by screws which will cap the shafts, so they have to be large enough to let the screw thread them, and small enough so that the screw doesn't strip the inside of the hole. The second photo at the top of the step has the six shafts I cut and drilled, so they serve as an example.
The free spin guide wheels will need to have the 5mm to 8mm ball bearings pushed into the recesses on the larger faces. These bearings reduce friction and reduce the horizontal movement of the free spin wheels along the aluminum shaft. The bearings can be aligned on the free spin wheel, and pushed in by laying the two components on a flat surface, which should press the bearings into the recesses.
Then, on one end of the aluminum shaft, a axle cap can be secured to the shaft with a ~4-6mm screw. The cap and shaft can be inserted into the hole through the inside of the track frame, then the bearing and free wheel can be slid onto the shaft, and finally the other cap can be screwed to the shaft when the shaft goes through the hole on the outer track frame, as detailed in the picture above.
I've included some additional pictures in this folder in case they would help with the step.
Step 6: The Track, Battery Holder, and Switch Standoff
In this step, the printed Battery Holder, Switch Standoff, and Track are put on the main body we have built up.
The Battery holder has a hole which should be aligned in the center of the chassis. The switch standoff aligns with the hole off center. They both can be screwed through the chassis, with a nut securing them on the bottom of the chassis.
The track can be placed on the track frame but first putting it on the drive wheel, then over the front most free wheel, and then stretched to fit over the rear most free wheel.
Step 7: Setting Up and Coding the Arduino
In this step we will flash the included code to the Arduino and attach jumper cables to it.
First, we will upload the included code linked at the bottom of this step, or it can be found here, to the arduino of your choice. I choose the arduino nano because it was small and inexpensive. If you don't know how to upload files to an arduino, here is an included guide.
Then solder jumper wires to it's GND, Vin, D3, D5, D6, D9, D10, and D11 Pins. If you want to make the wiring easier to follow along with, you can follow my color scheme.
P.S - I also coded my arduino to receive input from channels 2 and 4 on my receiver, so the pins which correlate to those channels on my receiver may need to be switched on your Arduino/Radio.
Attachments
Step 8: Laying Components in the Chassis
In this step we will lie the components in the chassis.
I used velcro hot glued to the chassis and the bottom of the components to make it easier to outline and manage, but this is not a necessary step. The critical part of this step is to ensure every component has a place on the chassis where the wires won't short out, and can be easily managed.
Step 9: Dividing Power, and Installing Main and ESC Switches
In this step we will divide the power for both ESCs, and secure the switches for the battery and ESCs in an easily accessible and anchored spot.
The power from the battery needs to be equally divided among the ESCs, so the input from the male T-Plug, which will plug into the battery, needs to be attached in parallel to two female T-Plug connectors. The red sides of the female connectors will both be soldered to the single male T-Plug, and the same is said for the black wires. Make sure that lots of solder is used for these joints, and that they are secured and protected by electrical wire so no exposed metal is showing.
The small switch can be attached to the switch standoff with the threaded head and nut which comes with the switch. The terminals of the switch can be soldered to wires, which will go in between the male T-Plug and female T-Plugs on the ground (black) wire.
The ESC switches can be hot glued to the ESC switch holder, (so that on for both switches is facing the same direction), and I secured my switch holder to the chassis with velcro.
Step 10: Connecting the Radio to the Arduino, Arduino to ESC, and Radio to ESC
Here we will connect the Radio receiver to the arduino, and the arduino to the ESCs.
To connect the receiver to the arduino, connect the D3 pin on the arduino to the first signal pin on the receiver (top left pin on receiver), D5 to the second signal pin, D6 to the third signal pin, and D9 to the fourth signal pin. I switched the second and fourth signal channels in my case because of how my receiver is set up, but the configuration above is what should be used for a standard receiver. Then connect three red female to male jumper wires, female end towards the receiver, to any middle pins on the receiver. These will carry 5V power from the receiver to the VIN pin on the arduino, and the red wires in the ribbon cables coming from the ESCs. 3 Black female to male jumper wires will need to similarly be connected to the arduino and ESCs. One black cable will need to connect to the GND pin of the arduino, and the two others will connect to the black wires on the ribbon cables coming from the ESCs.
The D10 and D11 pins on the arduino will connect to the ESCs to control them. The D10 wire will connect to the white wire coming off of the ESC on the right, and the D11 pin will connect to the ESC which will control the left motor through the white wire coming off of its ribbon cable.
When the electronics are finished and you find the steering on the tank in reverse, switch which ESC the D10 and D11 pins are controlling.
Step 11: Connecting the Motors to the ESCs
In this step we will finalize the electronics by connecting the motors to their respective ESCs!
Connect the thicker wires from your ESC, mine are blue and yellow, to your motors. I recommend that this connection be made with bullet connectors made in the middle so that the wires from the motor can be switched in case the drive of the motors needs to be reversed. If you do not have bullet connectors, then do not solder these wires and make sure they don't touch each other.
When you start to drive you tank and realize that a motor goes forwards instead of backwards, reverse the polarity of the wires coming off of the ESCs and the motor should spin in the right direction.
Step 12: Starting to Drive!
Now that your tank is done, time to take it for a test drive!
Ensure that your battery is charged, receiver and transmitter are charged, and that all your components turn on when you flip the switch!
I hope you enjoy the tank, and if you would like you can send me videos and pictures of the tank you made @projectmax2021 on instagram.
If you would like to see more pictures, videos, and general resources for the tank, they can be found in this google drive folder.
Thanks for viewing!
Attachments
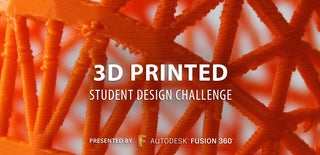
Second Prize in the
3D Printed Student Design Challenge