Introduction: 3D Printed Stained Glass Effect Suncatchers
Hello 3D printer makers! This is my first trial-and-error attempt at making stained glass effect suncatchers using 3d printing and epoxy resin. There are infinite design possibilities for these suncatchers when using 3D printing. This is also a great rainy day project or gift idea for that person who has everything.
From the beginning of the design process, to 3d printing the frame, to mixing and pouring the epoxy resin, I explore some do's and dont's as well as some #DIY suggestions for how to possibly improve this project. Thanks for taking a look and I would love to hear your opinions, suggestions and ideas in the comments.
The full process can be explained in the accompanying YouTube video. Click here to subscribe and watch the video: http://shareahack.com/link/more-videos
Supplies
These suncatchers can be made in so many different ways and the supplies you decide to use could vary depending on what you have on hand. Here's a short list of the tools and materials I used in my versions:
TOOLS & MATERIALS
- Any 3D Printer (I'm using a Creality 3D Ender-5)
- ArtResin Epoxy Resin (Starter Kit)
- ArtResin Epoxy Resin (Large Bottles - Better Value)
- Acrylic Paint Set
- Single Use Plastic Syringes
- Black 3D Printer Filament
- Plastic Shot Glasses
- Decorative Hanging Chains
- Window Hanging Suction Hooks
SOFTWARE
- Adobe Creative Cloud: I mostly use Adobe software for all of my design work. While it's not free, it's great full featured software and a joy to use. If you're a student, you can take advantage of their student/teacher promotion where you can get up to 60% off a subscription.
- Autodesk Fusion 360: Fusion 360 is my favorite program for creating 3D models. It's free for educational use.
- FREE Alternatives: There are some are FREE vector design program alternatives out there like Inkscape or Gimp but I'm not very adept in those programs yet.
Step 1: Designing & 3D Printing Your Suncatcher 3D Model
I haven't done anything like this before so I started off by googling some images to get some ideas.
After scrolling through the results, it got me thinking just how many possibilities there are. You could do someone's name, scan your kid's drawing, your favorite cartoon character - anything goes!
I decided do the first test by trying to replicate this sun and moon stained glass window photo I found.
I pasted the image into my vector illustration program. I personally like to use Adobe Flash for my vector drawing. It's now known as Adobe Animate.
Tracing Your Image
For a quick video guide showing how I traced images into vectors and converted into 3d models, you can click here for the timestamp: https://youtu.be/RgAjDr7ZAKw?t=50
In Adobe Animate, I put the photo in the first layer - then locked that layer so the photo can't be moved. I'll be doing my vector tracing in a SECOND layer on top of the photo.
I started by drawing a circle as the border of the suncatcher and then continued tracing using the line tool.
Make sure your vector line stroke weight is as thick as you want your frame to be.
I love using Animates's basic drawing tools because I find them a bit more intuitive and tactile, compared to using something like the illustrator pen tool.
For example when drawing the straight lines, all you need to do is drag their centers to create the curves.
With the snapping function on, the lines almost magnetically click together so you know when you've properly connected the line strokes.
Convert Vector Image to 3D STL File
Once the frame's design is completed, you can convert the vector line strokes into to vector fills (aka vector outlines).
If you're using illustrator, there's an option called "Outline Stroke". This turns the single pixel-wide line data into a combined flattened object that we can use to make a 3D model.
In my case, I'm going to export the final design into an FXG file, and then use a program like Adobe Illustrator to convert that FXG into a DXF file.
Once you've got your DXF to scale (i'm use millimeters), you can then import the DXF into a program like Autodesk Fusion 360 to EXTRUDE the suncatcher's frame into 3 dimensions.
Step 2: Preparing the Suncatcher Frame for Resin
For my first attempt, I glued down the 3D printed frame to some wax paper using Elmer's clear glue. This turned out to be not enough to make a good seal and I still got some resin leaks.
More clear glue might solve that, but instead recommend laying the frame down and filling each cell with a very thin layer of CLEAR resin first, letting it cure for a bit, then adding the color after.
The purpose of this is to hopefully prevent any leaks of the different colored resins into different neighboring 'cells' of the 3D printed frame. You could also possibly use multiple strips of clear packing tape along the back side of the frame, although I haven't tried that yet!
Step 3: Mixing and Pouring the 2-Part Epoxy Resin (ArtResin)
For the resin colors/pigments I'm going to use acrylic paints! Before you think I'm crazy - trust me it turned out to be a blessing in disguise. Normally this is a bad idea because acrylic paints are water-based, but for this project it made the resin easier to work with and I didn't have to buy a bunch of expensive mica pigments. You really could experiment with using anything as pigments - glow in the dark pigments, glitter, shiny pigments - heck you could even use mustard!
I'm using a couple of the single-use syringes to help me measure out the volumes of resin and hardener.
I poured out the resin and hardener into some of the plastic shot glasses for easier access with the syringes.
This resin has a 1 to 1 mixing ratio, meaning 1 part resin to an equal part hardener.
I started by mixing the blue paint and filling all of the blue colored cells.
You only need a TINY bit of paint to dye the resin because we want to keep it translucent. I actually used way too much blue in my first attempt!
I added both the resin and hardener parts to the paint in the shot glass and started mixing everything vigorously.
In the video, you can see how how I added little bit too much paint and how the the resin quickly got too opaque.
The paint mixes into the resin really well and actually makes the resin less viscous and more runny. This runniness actually made it easier to suction it up into the syringes.
I started experimenting by carefully pouring one of the resin-filled shot glasses directly into one of the larger cells. I used a popsicle stick to help control the pour.
Dabbing into the cell multiple times seemed to work pretty well with controlling the amount poured in.
In the video you can see the seal wasn't perfect and I started to get leaks. I think this may be due to the print slightly warping as it cooled down.
I place a weight on the frame to keep it as flat as possible. Luckily the resin thickens just enough in a few minutes that the leaks aren't that big a deal.
It's interesting how the resin hugs the walls of the frame and forms sort of a curved in meniscus effect.
Cue tips were really helpful with wiping up and absorbing any accidental drops.
One of the benefits of using the syringe is if you pour too much resin into a cell, you can just suction it back out.
I had some blue resin left over from the last pour and I thought it would be cool to create sort of a marbling effect using different shades. I randomly swirled around the highlights to complete the marbling effect.
Once the blues were finished, I repeated the same processes for the other colors.
As the resin drips off the popsicle stick, you can lift it up drag it toward the sharp angles to assist in filling them up.
Once you're finished adding all of the colors, it's time to sit back and let it cure for at least 24 hours.
I noticed that using paint as a pigment significantly increases the curing time (maybe by about 12 hours).
In the end it still cured hard as a rock with the only side effect being the resin seems to be a bit more flexible.
Once you're confident it's all cured, peel off the wax paper. There might be some stray resin "flashings" around the sides that you will need to snip off.
Step 4: That's It, You're Ready to Hang It Up!
Don't be afraid to experiment with different dynamic 'mobile' configurations! In a second attempt, I played around with hanging humming birds that bounce around in the wind.
Thanks for reading this far into my Instructable. If you have any interesting ideas about where to take this project, let everyone know in the comments!
If you haven't seen the accompanying video yet, you can subscribe to the channel here for more detailed context about the the above steps: http://shareahack.com/link/more-videos
Cheers
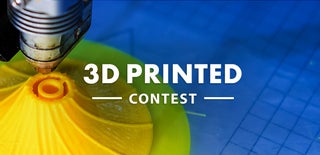
Participated in the
3D Printed Contest